Chemical and Process Engineering Resources
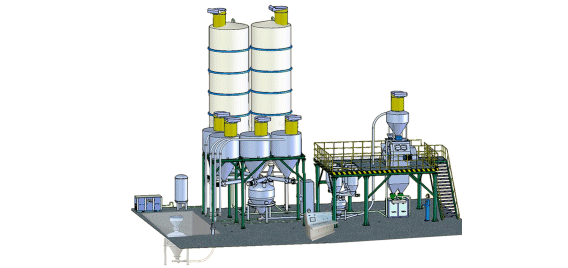
The Base Equation is the basis for the following equations used in the pressure loss calculations. The pressure loss is expressed in psi or lbs/in2 in the following equations.
![]() | Eq. (1) |
![]() | Eq. (2) |
![]() | Eq. (3) |
![]() | Eq. (4) |
![]() | Eq. (5) |
![]() | Eq. (6) |
The Fanning Friction Factor
In order to determine the fanning friction factor, f, the Reynolds Number must first be calculated:
where ?g is the gas viscosity in lbs/ft s.
Then, the friction factor is calculated from the following equation derived from pages A-23 and A-24 of Crane's Technical Paper No. 410:
Where ? is the pipe roughness factor which can be estimated as 0.00015 for smooth pipes or 0.0005 for shot-peened pipes.
Pipe Equivalent Length
For straight pipe runs (either horizontal or vertical) use the actual length of the pipe. For bends and other devices, use the table below as a guide:
Component | Equivalent Length |
Bends, 90° bend, long radius (10 to 1 radius to diameter ratio) | 40 x diameter or 20 ft (whichever is larger) |
Diverter Valves | |
45° divert angle | 20 x diameter |
30° divert angle | 10 x diameter |
Flexible Hoses | |
Stainless steel w/ lined interior | 3 x pipe length |
Rubber or vinyl hose | 5 x pipe length |
For bends that are less than 90°, use the following equivalent lengths: L =40 x (Degree of bend / 90) |
Solids Velocity
Solids also move at a velocity lower than the gas velocity due to drag forces. The difference between these velocities is called the slip factor. For most course or hard solids, the slip factor is around 0.80.Â
For fine powders, the solids velocity can be closer to the gas velocity and a factor of 0.90 may be more appropriate. Depending on the size of the particles, the slip factor can range from 0.70 to 0.95.
Solids Velocity in Long Radius Bend
For a 90° radius bend, the solids velocity at the exit of the bend (Vp2) is around 0.80 times the solids velocity at the inlet of the bend (Vp1). This factor can range from 0.60 to 0.90 depending of the properties of the solids. For bends that are less than 90°, the exit velocity may be expressed as:
After leaving a 90° bend, use a nominal value of 20 pipe diameters for the length of pipe needed for the particles to accelerate back to their original velocity at the inlet of the bend.
Solids to Air Ratio
The solids to air ratio is calculated as:
In the above, m is the the solids mass flow in lb/s and A is the pipe cross sectional area in ft2. Remember that the gas density (and therefore velocity) will change throughout the system (we'll discuss this in more detail later).
When calculating the gas velocity, reduce the gas mass flow rate by 5% for pressure systems to account for gas leakage through a rotary valve if such a valve is used to feed the solids.
Gas Density and Pressure Loss
As the carrier gas moves through the system and losses or gains pressure (depending on whether the system is a pressure or vacuum system), it's density will increases or decrease accordingly thereby changing the velocity of the gas.  The gas pressure loss equation is shown in Equation 2 above. The ideal gas law may be employed to calculate the density of the gas throughout the system.
Setting Up the Calculation
The method presented here can easily be set up in a spreadsheet to show the performance of your system. It is recommend the divide the entire system into 5 to 10 ft sections for such a calculation. The exit conditions of from section become the inlet conditions for the next and so on. Also, be sure to account for any gas losses that are known and for any extra gas inlet points in the system. For pressure systems, start from the end of the conveying line and return to the solids inlet point. For vacuum systems, start from the solids inlet point and end at the blower inlet.
References
- Zenz and Othmer, "Fluidized and Fluid Particle Systems", Chapters 10 and 11, published by Reinhold Publishing Corp, 1960
- Agarwal, A.T., "Theory and Design of Dilute Phase Pneumatic Conveying Systems", Powder Handling & Processing, Vol. 17, No. 1, January/February 2005
- Kimbel, Kirk W., "Troublefree Pneumatic Conveying", Chemical Engineering Magazine, April 1998, page 78
0 Comments