Chemical and Process Engineering Resources
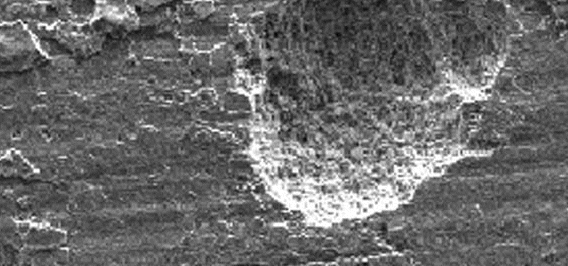
Intergranular Corrosion
Occuring along grain boundaries for some alloys, intergranular corrosion can be a real danger in the right environment. On the left, a piece of stainless steel (especially suspectible to intergranular corrosion) has seen severe corrosion just an inch from a weld. The heating of some materials causes chromium carbide to form from the chromium and the carbon in the metals.
![]() |
Figure 5: Intergranular Corrosion |
Selective Leaching
When one element or constituent of a metal is selectively corroded out of a material it is referred to as selective leaching. The most common example is the dezincification of brass. On the right, nickel has be corroded out of a copper-nickel alloy exposed to stagnant seawater. After leaching has occurred, the mechanical properties of the metal are obviously impaired and some metal will begin to crack.
![]() |
Figure 6: Example of Selective Leaching |
Erosion-Corrosion
Erosion-corrosion arises from a combination of chemical attack and the physical abrasion as a consequence of the fluid motion. Virtually all alloy or metals are susceptible to some type of erosion-corrosion as this type of corrosion is very dependent on the fluid. Materials that rely on a passive layer are especially sensitive to erosion-corrosion. Once the passive layer has been removed, the bare metal surface is exposed to the corrosive material. If the passive layer cannot be regenerated quickly enough, significant damage can be seen. Fluids that contain suspended solids are often times responsible for erosion-corrosion. The best way to limit erosion-corrosion is to design systems that will maintain a low fluid velocity and to minimize sudden line size changes and elbows. The photo above shows erosion-corrosion of a copper-nickel tube in a seawater surface. An imperfection on the tube surface probably cause an eddy current which provided a perfect location for erosion-corrosion.
![]() |
Figure 7: Example of Erosion-Corrosion |
Stress Corrosion
Stess corrosion can result from the combination of an applied tensile stress and a corrosive environment. In fact, some materials only become susceptible to corrosion in a given environment once a tensile stress is applied. Once the stress cracks begin, they easily propagate throughout the material, which in turn allows additional corrosion and cracking to take place. The tensile stress is usually the result of expansions and contractions that are caused by violent temperature changes or thermal cycles. The best defense against stress corrosion is to limit the magnitude and/or frequency of the tensile stress.
![]() |
Figure 8: Stress Corrosion Cracking |
References
- Callister, William D., Materials Science and Engineering, 3rd Ed., Wiley, New York, 1985
- InterCorr.com website
- NASA website
2 Comments
Thank you for good basic summary. Easily understood.
such an informative article.