Chemical and Process Engineering Resources
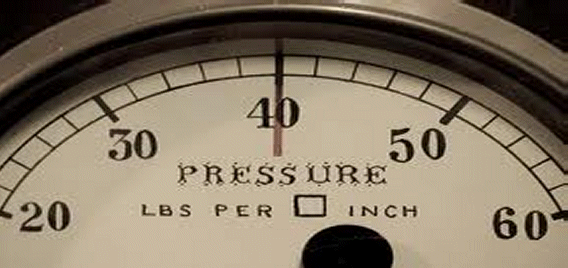
So, Why the Confusion?
The confusion faced by the reader who wrote the "Letters to the Editor", and probably many others, is due to a number of reasons. First and I think foremost, is the way ASME does not relate the maximum allowable pressure limits to relief valve capacity. ASME, Section VIII, Division 1, refers to MAWP throughout the entire document when talking about relief valve set pressure and allowable overpressure. I believe the reader may have been referring to and interpreting what is stated in paragraph UG-125 of ASME Section VIII, Division 1. It states in part,
All pressure vessels other than unfired steam boilers shall be protected by a pressure relief device that shall prevent the pressure from rising more than 10% or 3 psi, whichever is greater, above the maximum allowable working pressure except as permitted in (1) and (2) below.
Sub-paragraphs (1) and (2) mention cases where the pressure rise may be higher.
However, when ASME talks about certifying the capacity of a relief device, MAWP is never mentioned. ASME Section VIII, Division 1 clearly states in Paragraph UG-131, para c(1) that
Capacity certification tests shall be conducted at a pressure which does not exceed the pressure for which the pressure relief valve is set to operate by more than 10% or 3 psi, whichever is greater, except as provided in para c(2)...
Sub-paragraph para c(2) covers a fire case.
Another area of confusion might involve the definition of capacity and how the term is used in ASME and API. Relieving rates are determined from "what can go wrong" scenarios and if allowed to go unchecked, would overpressure the vessel. Once the Process Engineer determines the controlling relieving rate from all the scenarios, the required relief valve orifice size is determined using the appropriate equation given in API. Once the required relief valve orifice size is calculated, an actual orifice size equal to or greater than the calculated orifice size is chosen from a selection available from a particular manufacturer. The maximum flow through this actual valve will be the valve's capacity.
Conclusion
The problem and solution can be summarized as follows:
Capacity based on MAWP + Allowable Overpressure
CODE AS WRITTEN
Capacity based on Set Pressure + Allowable Overpressure
Code clearly requires that the relief valve's capacity be based solely on set pressure and not on the vessel's maximum allowable working pressure. Indeed, as shown above, if the relief valve's capacity was based on MAWP, then code might even force the Process Engineer into an unsafe design. A good analogy is highway speed limits. In the United Stated, many highway speed limits are set for 65 miles per hour. This does not mean a driver cannot travel slower and, under certain conditions for safety, it is almost a necessity that one does.
If it is safe to do so and the protected vessel can be allowed to pressurize to a greater extent, the relief valve set pressure can be increased, thereby reducing the relief valve's size and cost. Remember also that there is piping and possibly downstream equipment to "catch" and process the relieving fluid associated with the relief valve which may also benefit by this reduction.
One way of accomplishing a reduction in relief valve size is by increasing the vessel's design pressure. There is an economic trade off here as the vessel's cost can increase above what you may save by reducing the size of the valve. Another approach to consider is increasing the relief valve's set pressure right up to MAWP after receiving the certified vessel drawings. However, depending on project schedule, the cost savings may be offset by the high costs associated with late design changes.
Final Say
I welcome and encourage your feedback. Feel free to E-Mail me at the Internet address below. All correspondences that include a name will be published in this column. Better yet, I encourage discussion of any topic I cover utilizing The Chemical Engineers' Resource Message Board. This will enable the entire Internet community to join and learn.
References
- Ahmad, S.
- Letters to the Editor
- API
- ASME "Ease Relief System Design and Documentation," Chem. Eng. Progress, pp 43-50 (May 2000) Chem. Eng. Progress, p 10 (October 2000) (www.api.org) Recommended Practice 520, "Sizing, Selection, and Installation of Pressure-Relieving Device in Refineries, Part 1-Sizing and Selection", 7th Edition (January 2000) (www.asme.org) "Boiler and Pressure Vessel Code, Section VIII, Division 1" (1998)
Author/Community Member Discussion Regarding This Article
The following discussions were added July 21, 2001.
Discussion One
From Mr. Jeffrey Niemeier:
Philip,
I am responding to your column in Cheresources.com.
Also, contrary to what you have in your article it is many times advantageous to have a set pressure much lower than the MAWP. This is especially true if runaway reaction is a possibility. A low set pressure allows the reactants to start venting much earlier, thereby removing reactant from the vessel before the temperature and reaction rate get too high. Check out the DIERS literature.
I think you should remove your column.
Philip Replies:
Mr. Niemeier,
Thank you for taking the time to read my article "Relief Valve Set Pressures" in the "Process Engineering-As I See It" section of "The Chemical Engineers' Resource Page and for your feedback.
Allow me to respond.
You write,
"I disagree with your interpretation of the ASME code. The capacity of a relief device that is used to determine adequacy of design is based on the allowable overpressure. If the overpressure is higher the flow will be higher. You can take credit for this. UG-125 makes it clear that the only requirement is that the pressure not exceed 110% of the MAWP (121% for a fire). The stamped capacity is there only for reference."
You are falling into the same trap that most people fall into and this is precisely why I wrote the article in the first place. The certified capacity which determines adequacy of design of a relief valve (which is the 'device' I assume you are referring to since the capacity of a stand alone rupture disk is different) is based on the criteria described in ASME Section VIII, Divison 1, Paragraph UG-131, not Paragraph UG-125. Paragraph UG-131 states that, except for some very specific exceptions, the overpressure is to be 10% or 3 psi, whichever is greater and is to be referenced to set pressure. If set pressure happens to be equal to MAWP, fine, but as you point out
later in your letter, this is not always the case. There are no provisions that I can find that allow a vendor to certify a relief valve for
overpressures greater than these. In addition, the certified capacity is the only flow that is guaranteed by the relief valve vendors, nothing more or less. Using greater overpressures than the 10% or 3 psi described above in calculations for required relieving rate does not alter the guaranteed capacity provided by the vendor and which is required by ASME, Paragraph UG-129.
If you require further evidence of these points, feel free to contact Farris Engineering, a well-known relief valve vendor at http://www.cwfc.com/. However, I can save you some time because I didn't write the article without doing some research first.
Now, you think capacity certification (stamped capacity) is just for reference?!? It is this certified capacity, not the calculated maximum relieving rate, which must be used when sizing inlet lines to the relief valve (using the 3% rule, ASME Section VIII, Division 1, Appendix M, Paragraph M-7) and in many cases, the outlet lines as well.
I invite you to re-read the article, specifically the paragraph titled "So, Why the Confusion? and also read ASME Section VIII, Division 1, Paragraph UG-131. The code is like a bowl of spaghetti. You have to weave through all the pertinent paragraphs to get to the end... and the full story.
For your information, the stamped capacity for relief valves in vapor/gas service is usually given in terms of SCFM of air at set pressure plus 10% overpressure and 60 degress F. Valves in steam service are stamped in terms of pounds per hour of steam at set pressure plus 10% overpressure at the saturation temperature. ASME Section VIII, Division 1, Appendix 11 gives you a means for converting to your particular vapor/gas. Valves in liquid service are given in terms of gallons per minute of water at set pressure
plus 10% overpressure and 70 degrees F.
You continued in your letter with the following (still referring to the stamped capacity):
"It could not possibly be used to make a judgement on two-phase flow capacity."
I don't know why you mention two-phase flow since I didn't in my article. However, I agree, relief valve manufacturers at the present time do not have capacity certification capability for two-phase flow.
You then added:
"Also, contrary to what you have in your article it is many times advantageous to have a set pressure much lower than the MAWP."
I invite you to re-read my paragraph titled, "Relief Valve Set Pressure" specifically the sixth line where I write, "There are even times when the relief valve must be set even lower than design pressure."
Are we talking about the same article here? Did you actually read my article?
You finish your letter with:
"I think you should remove your column."
MAWP, design pressure, relief valve set pressure, what is allowed overpressure, calculated relieving rates, certified capacity, etc. appears to be a very confusing and misunderstood concept that most people are having when dealing with safety relief systems; you included. And this is precisely why my column must not only stay but also grow. My only regret at this time is that I obviously did not get the point across to you and for that I apologize. I hope this response clarifies those points you misunderstood. I will be more than happy to answer any other concerns you may have or even further discuss the points you already brought up.
Mr. Jeffrey Niemeier Replies:
I still disagree with you. It is basic physics that you will get more flow if you have a higher driving pressure. There is no reason not to take credit for overpressures above 10% as long as you don't go above the maximum allowable pressure for the valve. See the following memo from Paul Papa, director of engineering for Farris:
As you mentioned, all of our certified capacities are based on testing that is done at 10% overpressure. Nameplates are therefore marked with capacities at 10% overpressure in the appropriate certification fluid (steam, air, or water). From a selection standpoint, valves are typically sized based on 10 % overpressure. As you correctly pointed out, Section VIII of the ASME Code indicates that ASME Code stamped pressure vessels require a relief device that must pass all of the required flow without allowing the pressure to go any higher than 10% above the maximum allowable working pressure (MAWP).
There are many cases where a vessel is being used at a pressure at much less than its MAWP. In those cases, you can size and select the valve at an overpressure greater than 10%. This will allow you to use a smaller valve as
the valves capacity will increase as the pressure increases. Per ASME Code, the pressure must still be kept to the 10% accumulation pressure, that is no more than 10% above the MAWP.
For the most part, this is not a problem for the valve as long as the higher overpressure does not exceed the maximum pressure limit of the valve at the relieving temperature.
Philip Replies:
Jeff,
I'm not saying, nor have I ever said that you can't calculate the required relieving rate for the MAWP + overpressure and then choose a valve based on this. Remember fire cases? They go to 21% overpressure (set pressure basis) don't they and are often the sizing criteria for the valve. However, this still does not alter the guaranteed (stamped capacity) flow rate of the valve which is based strictly on set pressure + 10% (for the most part). And it is this flow that your maximum calculated relieving requirement cannot exceed and which is subsequently used in the hydraulic calculations, per ASME. I don't know how many times I have to say this. And this is what my article was strictly about; the criteria used to obtain the certified (stamped) capacity. Also, I also don't see in the Farris response you sent me where they will guarantee any number other than what they are allowed to stamp even if MAWP is 100 psig and you want to allow the pressure to go to 110 psig. If a valve is set for 50 psig, it will be certified based on 55 psig, clear and simple! Neither Farris nor any other vendor will guarantee that your valve will pass a different flow rate at any other condition. Nor will they tell you to use any other value in subsequent hydraulic or downstream sizing equations.
I would love to see you prove the calculations that give you that extra margin you keep talking about. You think it's simple? Try doing the calculations at a high pressure for something very non-ideal such as ethylene. All of the equations shown in ASME and API fall apart rather severely since they are all based on ideal gas. Try convincing an OSHA inspector that at conditions which exceeded the capacity certification test at the time of equipment failure that your valve was properly sized and should have been big enough. If you can do this via flow equations derived properly for non-ideal gases from the sound use of thermodynamics, great and there is no argument from me. Heck, I'll even write about it!! After all, ASME and API specifically state that the engineer is to use good engineering judgment and if in question, work with the relief valve vendor. As a matter of fact, you can even deviate from the code if you can prove that a given relief valve will not be adversely affected from whatever you are trying to do. As an example, I am currently on a project where the inlet line loss for one particular valve is in the 6% range. Notwithstanding the fact that the 3% rule is "non-mandatory" (but is still considered good engineering practice), we are working with Farris to determine if this would adversely
affect the valve. If it doesn't, we can live with the current piping configuration.
What I wrote was about stamped capacity and how this is what is recognized by Code, nothing more or less. Stamped capacity being the only guaranteed flow rate is fact, not interpretation. When to use stamped capacity has been set down by both Code and interpretation. You can disagree all you want with what I wrote. That is fine and I just love getting into these types of discussions. How else can we learn and grow? But you made some rather inaccurate statements in your first letter about what was stated, or not
stated in the article and that still leads me to feel you didn't totally understand it.
I've been giving this debate some further thought and I hope this will finally put it to rest. You and I seem to be disagreeing on the concept of sizing versus what you do with the valve once it has been sized.
My article on the Web site starts off with a statement made by the author of an article published in the May 2000 issue of CEP. This person made a statement that basically said if you want to decrease the size of a given relief valve, find a way to increase it's set pressure. However, the following Letter to the Editor in the October 2000 issue inspired my article. It stated, "This is not true; for a certain MAWP, the capacity of the relief device is not a function of its set point, but of MAWP alone." Now, had you really read my article, you would have seen these quotes! As I've said before and written in my article, per ASME, capacity for a given valve (which I am defining as certified capacity) is a function of set point only, not MAWP. Therefore, to increase the certified capacity of a given
size valve, one can increase the set pressure. Alternatively, to reduce the size and cost of the purchased valve, one can increase the set pressure of a smaller valve and maintain the same certified capacity.
The whole point should be "safety", not who can buy the smallest relief valve. If you want to stretch what ASME is trying to convey just to buy a smaller relief valve, go ahead; you don't work for me. If you did work for me, I wouldn't allow it. I'll take the conservative approach, it just isn't worth the potential liability. After all Jeff, you'll never know if the valve you bought is the right one unless the system over pressure is caused by the controlling scenario and the valve does or does not work. And guess what? This rarely happens since most controlling scenarios are loaded with conservative assumptions that are never achieved in real life.
One last point if I may. I still can't understand why you would want to set the relief valve at a lower pressure (50 psig) and still allow the system to achieve the much higher pressure (110 psig). This makes no engineering sense to me. You should just specify the set pressure at MAWP and go with the allowable overpressures. Then you won't have any debates. You mention run away reaction? I'm sorry but this is bad engineering practice and if you do this at your site, I would stop the practice. Run away reactions can occur
too fast for relief valves to react. I would use a stand alone rupture disk set at the lower burst pressure (your 50 psig example) for the run away reaction scenario and use the relief valve for other scenarios set at the 100 psig MAWP. This is a much safer design.
0 Comments