Chemical and Process Engineering Resources
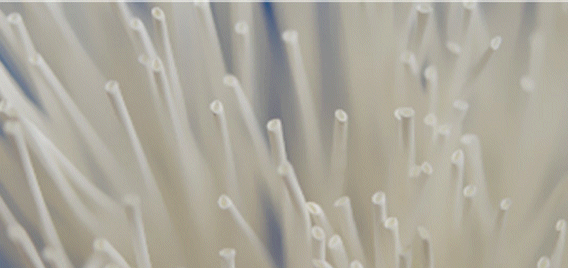
Advantages and Disadvantages of Membranes
Hollow fiber is one of the most popular membranes used in industries. It is because of its several beneficial features that make it attractive for those industries. Among them are:
- Modest energy requirement: In hollow fiber filtration process, no phase change is involed. Consequently, need no latent heat. This makes the hollow fiber membrane have the potential to replace some unit operation which consume heat, such as distillation or evaporation column.
- No waste products: Since the basic principal of hollow fiber is filtration, it does not create any waste from its operation except the unwanted component in the feed stream. This can help to decrease the cost of operation to handle the waste.
- Larger surface per unit volume: Hollow fiber has large membrane surface per module volume. Hence, the size of hollow fiber is smaller than other type of membrane but can give higher performance.Â
- Flexibility: Hollow fiber is a flexible membrane, it can carry out the filtration by 2 ways, either is "inside-out" or "outside-in".
- Low operating costs: Hollow fiber need low operation cost compare to other types of unit operation.
However, it also have some disadvantages which lead to its application constraints. Among the disadvantages are:
- Membrane fouling: Membrane fouling of hollow fiber is more frequent than other membrane due to is configuration. Contaminated feed will increase the rate of membrane fouling, esapecially for hollow fiber.
- Expensive: Hollow fiber is more expensive than other membrane which available in market. It is because of its fabrication method and expense is higher than other membranes.
- Lack of research: Hollow fiber is a new tachnology and so far, research done on it is less compare to other types of membrane. Hence, more research will be done on it in future because of its potential.
- Cleaning and temperature restraints: Since hollow fibers of made of polymers there are constraints with regards to what types of chemicals they can contact and the temperatures at which they can operate.
Membrane Process
Various types of membrane processes can be found in almost all of the literature references. In this text, we will confine ourselves to the few membrane processes that we will encounter in the further discussion of the industrial applications.
Reverse Osmosis (RO)
![]() |
Figure 1: Membrane Configurations |
There is considerable confusion in the open literature as to the distinction between few membrane separation processes, i.e., the microfiltration (MF), ultrafiltration (UF) and reverse osmosis (RO). Occasionally one will see it referred to by other names such as "hiperfiltration (HF)". In order to distinguish these separation processes clearly, Porter in his paper presented one of the useful method based on the smallest particles or molecules which can be retrained by the various membranes. Accordingly, RO has the separation range of 0.0001 to 0.001mm (i.e., 1 to 10 Ã… ) or < 300 mol wt.
RO is a liquid-driven membrane process, with the RO membranes are capable of passing water whilst rejecting microsolutes, such as salts or low molecule weight organics (< 1000 daltons). Pressure driving force (1 to 10 MPa) needed to overcome the force of osmosis that cause the water to flow from dilute permeate to concentrated feed. The principle use of this membrane process is desalination, which show its great advantage over the conventional technique of desalination, i.e. ion exchange.
Pervaporation (PV)
In this process, liquid mixture are fed under pressure to a non-porous membrane, where components pass through the membrane by solution-diffusion and evaporate at the permeate side of the membrane. This technique is able to separate an azeotropic mixture. It current usage is well know in dehydration of the organic solvents and mixtures and the removal of organics from aqueous stream. The future application of this process, which is now under the main interest of the researcher is the hydrocarbon separation,, which shows its advantages of energy require compared to the conventional distillation technique.
Gas Separation
Two type of gas separation processes have been encountered: gas permeation (GP) and gas diffusion (GD). The gas separation of the industrial interest is the former process, which is a pressure driven process where vapor components pass through a non-porous membrane by a solution-diffusion mechanism; analogous to RO. While gas diffusion process can be done for the microporous membranes, operating under a concentration or partial pressure gradient.
1 Comments
Helo sir,
I am having a doubt...What is the difference between membrane seperation and adsorption process?