Chemical and Process Engineering Resources
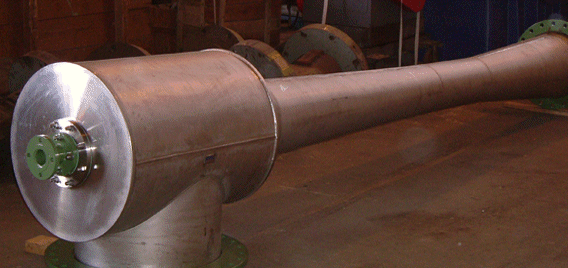
Multistage, No Load Vacuum
Typically, a multistage ejector system is started up backwards from the last (Z) stage to the first. The Y stage cannot operate properly until the Z stage is working, the X stage will not work unless the Y and Z are operating, and so on.
The next step is to performance-test the stage in question by checking its no-load vacuum. For example, if the stage being checked is the Y stage of a three-stage ejector system, a blank should be installed on the Y suction flange. Since the Y stage is designed to discharge to a vacuum created by the Z stage, the Z stage, and intercondenser if present, must operate simultaneously during this test.
With the Y stage steam valved off, first check and record the Z stage no-load vacuum to be sure it is meeting the manufacturer's tested value. Then, with the vacuum gage still connected to the Z stage, turn the Y stage steam on. If the Z stage vacuum steadily falls off, the intercondenser is most likely the cause of trouble and should be inspected.
As mentioned in the preliminary checklist, a condenser temperature rise much greater or less than design may be an indication of a water-flow problem. A water-flow problem can result in a higher condenser temperature and an overloading of the following stage with uncondensed vapor. In this case, as the Z stage falls off, the Y stage vacuum would follow.
Examples of direct-contact condenser problems include: a blocked tailpipe, air leakage into tailpipe, damaged water distributor, or a plugged water nozzle. Surface condenser problems include: a blocked drain, air leakage into tailpipe, or split or fouled tubes.
If the Z stage vacuum is within specifications, move the vacuum gage to the Y stage. If the Y stage vacuum measures exactly the same as that of the Z stage, a blocked Y stage nozzle may be the cause. However, at this point, if the Y stage vacuum does not measure reasonably close to the manufacturer's tested no-load value, the stage should be disassembled for internal inspection.
Finding the Y and Z stage vacuums within specifications, remove the blind flange from the Y stage suction and repeat the procedure at the X stage. It is important to remember that each stage must meet its design vacuum before continuing the testing.
At times it may be impractical to make and install a blind flange on the suction connection of an ejector due to the size of the unit. In most cases, however, these larger stages will be the W or X. If the no-load testing has ruled out the Y and Z stages and the condensers ass possible causes of the vacuum problem, and internal inspection of these larger stages may be the more practical step to follow.
Internal Inspection
There are several things to look for when performing internal inspection of an ejector. Usually any kind of corrosion or erosion that is obvious to the eye and touch will affect the performance of an ejector. An indication of wet steam will show as lines ("wiredrawing") etched up and down the inside of the steam nozzle. The point along the diameter where the steam contacts the venturi is another location that may be gouged due to wet steam.
Steam leaking around the nozzle puts an artificial load on that stage, resulting in poor vacuum. Leakage of this sort should be noticeable as a discoloration where the nozzle seats on the steam chest, or as erosion of the nozzle threads. A process that causes corrosion or buildup of material on the internals of an ejector will also effect the performance of that unit.
Critical dimensions such as the nozzle orifice or venturi bore diameter, obtained from the manufacturer, will enable a measurement of dimensions to determine extent of wear. Part numbers of the various ejector components should be checked to ensure they are in the right unit. Many ejector parts, and complete stages, are physically interchangeable and care must be taken not to mix them.
Keep Spares on Hand
At a minimum, keep at least the following components in stock:
- One steam nozzle for every single nozzle ejector stage
- One diffuser for every stage, at least in sizes through 6 in. -- higher, if continuity of service is critical
If continuity of service is important to a process, keep a spare steam nozzle in stock for every size ejector in the system. Spare diffusers are also worthwhile to keep in stock, especially for smaller systems. While it is theoretically possible for the plant engineer to recondition these parts, the practice is not recommended because critical dimensions may be altered.
Since most nozzles are relatively inexpensive they should be considered sacrificial; if wear is evident they may be discarded and easily replaced. A complete Z stage should be kept in stock for important systems in critical operations.
If these simple tips fail, don't despair. Check the nameplate and call the manufacturer. A condition may be new to you, but chances are the manufacturer has seen it, and corrected it, many times before. Since troubleshooting an ejector system is quite straightforward, suppliers can usually work with you over the phone to get the problem corrected. Experienced service people estimate that at least 50% or more of the troubles referred to them can be solved over the phone.
Of all vacuum-producing devices, the steam-jet ejector is the most forgiving. Occasional inspection, replacement of parts, and adherence to design conditions will keep it operating reliable for many years. Knowledge of these simple procedures for avoiding trouble, and locating it if it does occur, will save time and product in you plant.
This article first appeared in Chemical Engineering magazine in May 1992. Special thanks to Mr. Norman Diegnan for permitting the reproduction of this article at The Chemical Engineers' Resource Page. |
3 Comments
Excellent Article !
very informative article.. thnx
Additional information on the <air to steam mass ratio> for each pressure level or for a certain compression ratio would be greatly appreciated. There might be any calculation tool available on this subject, isn't it?
Tanks in advance.