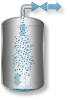
Process systems containing large inventories of gas and light hydrocarbon liquids at high pressure have the potential to create a major hazard during a plant upset. To minimize the potential for the creation of a major hazard, blow down valves shall be used for depressuring all equipment containing large inventories of high pressure gas / liquid in the event of a fire, a serious operating excursion, or a utility failure.
The depressuring system shall reduce the pressure of the equipment within a fire zone to 7barg or 50% of the design pressure, whichever is lower, within 15 minutes for high-rate depressuring or within 60+ minutes for low-rate depressuring. Blow down valves sized for the above cases will also be sized for maintenance and normal shutdowns.
Depressuring can be done as follows;
- Fire (Hot) Depressuring API 521 (Immediate depressurization of system fires) – Used as the governing case when sizing blowdown valves
- Adiabatic Depressuring/Isochoric (Cold) Depressuring (depressuring during utility failure or equipment shutdown, not due to fire)
- Vessel Dimensions: vessel dimensions must be entered such that you represent volume occupied by each phase (I usually enter the minimum wetted area expected), metal weight of model or thickness. For compressor depressuring enter the total volume between each stage between each ESD.
- Valve Specifications: Any valve type can be used usually for the fire case it is best to determine use the calculate CV option and then use the same parameters when doing isochoric depressuring to determine vessel MDMT. For depressuring fluids in the dense phase it is best to use the general valve sizing equation and “calculate pressure” adjusting the valve size to meet the required 7barg
- Heat Loss Model: I usually select the detailed method to provide more accurate results however “none” is often used for fire case to be more conservative:
o Metal thickness
o Insulation thickness
o Ambient Temperature
1)Hot Depressuring
- This case is usually used to predict the size of the blow down relief valve
- Initial pressure – should be your PSV set pressure or highest possible operating pressure
- Initial temperature – highest operating temperature
- Final Pressure – 7barg or 50% of your PSV set pressure whichever is lower
- Time – 15 minutes
- Liquid level – higher level is more conservative
- Heat input model – API 521
- This case is usually used to predict attain the minimum vessel design temperature, associated piping design temperature and material (carbon steel, stainless steel, etc)
- Initial pressure – for adiabatic start with the settle out pressure of the compressor attained from the settle out calculation or for isochoric start with the design pressure to be conservative although normal operating pressure can also be used
- Initial temperature – use the minimum ambient temperature as a conservative assumption for the isochoric approach or the compressor settle out temperature for adiabatic
- Final pressure should be 0.5 bar or atmospheric
- Liquid level – lower provides lower MDMT
Depressuring from the supercritical point Hysys is not able to find a solution most of the time this is due to the instability of Hysys to predict fluid properties. What you will probably notice is that the vapour phase fraction will go from 0 to 1 while the depressuring utility is running.
To help solve the problem one can adjust what is known as the dense phase tuning (DPT) factor between 0.5<DPT<2 . DPT above 1 favours the vapour region and DPT below 1 favours the liquid region.
In addition to this it is best to separate out components such as water, TEG, other than light hydrocarbons that are likely to be vapour at atmospheric pressure etc. and the initial temperature using a component splitter and use the result stream to depressure the system.
My trick to selecting the best DPT is trial and error, I would incrementally increase the DPT while trying to attain the highest vapour molecular weight. To do this you must use a two phase separator that you use to split vapour and liquid at the final condition (atm pressure). Adjust it until the vapour molecular weight becomes constant with any change in the tuning factor.
Note: I found Hysys does not give accurate results when adjusting the time step to a very low value like 0.01sec its best to use a higher time step for more accurate results.
If you would like more detailed information the aspentech website offers great information on Dynamic depressuring.
We just released a new technology here at Aspen Technology that specifically caters to dense-phase depressurization.
We have an upcoming webinar that will show exactly how to use this tool (it is more rigorous, and more complex than DPU). You don't have to attend -- but just by registering you will get an email with a lot of content to help you if you ever need to use the tool in the future. I recommend checking it out:
http://www.aspentech...nar/?src=cer-aq