Chemical and Process Engineering Resources
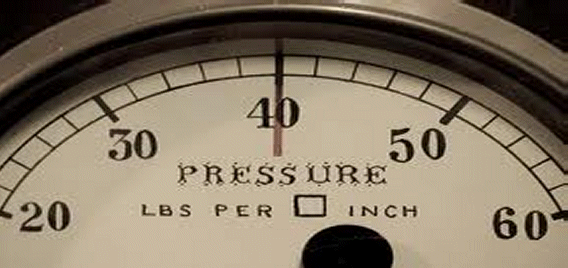
As the title of this column implies, I intend to present various topics related to Process Engineering Design based on my knowledge and experiences. I will convey what approaches I think you should be taking.
I will stress "the correct way" so don't expect short cuts and rules of thumbs. Notice, I use the word "I" a lot. These will be my thoughts, my ideas. I will present facts and in instances, my interpretation of the facts. I might even editorialize. This inaugural column starts a series on Relief Valves.
The Problem
In the May 2000 issue of Chemical Engineering Progress1 (CEP), there was an article entitled "Ease Relief System Design and Documentation". While I'm not intending to discuss the article in whole, the author stated something that appeared to get one reader's attention. The author wrote,
If you want to reduce the size of a relief device for cost savings, then design it at a higher set pressure; however, the MAWP of the weakest link should not be ignored.
This statement prompted a "Letters to the Editor" in the October 200 issue of CEP2 (no, it wasn't me) where a reader wrote,
This is not true; for a certain MAWP, the capacity of the relief device is not a function of its set point, but of MAWP alone. For example, for a MAWP of 100 psig, the relief valve capacity will be same whether it is set at 80 psig or 100 psig. In both cases, the maximum relieving pressure for the ASME non-fire case (or BS 5500 fire case) is 124.7 psia and the discharge capacity will remain identical. The only difference is that if the set point is 80 psig, the allowable overpressure will be 37.5%, while, at the same for a set point of 100 psig, it will be 10%. For the ASME fire case, the values will be 51.25% and 21% respectively. These are defined very clearly in API 520, Tables 2 to 6.
I'm seeing that people do not quite understand what API 5203 and the ASME Boiler and Pressure Vessel Code, Section VIII, Division 14, are really saying. (For those not familiar with API and ASME, ASME, or the American Society of Mechanical Engineers, is the organization that sets the codes in the United States that determine how pressure vessels are to be designed and protected. These codes are law and must be followed. The American Petroleum Institute, or API, sets the standards by which the codes are followed. API publishes the Recommended Practices 520 and 521, among others.)
MAWP and Design Pressure
In paragraph 1.2.3.2, para b, API 520 defines maximum allowable working pressure (MAWP) as:
... the maximum gauge pressure permissible at the top of a completed vessel in its normal operating position at the designated coincident temperature specified for that pressure.
The operative word here is "completed".
In the same paragraph, API 520 says that the MAWP is normally greater than design pressure. The Process Engineer usually sets the design pressure at the time the vessel specification is being written. The design pressure is the value obtained after adding a margin to the most severe pressure expected during normal operation at a coincident temperature. Depending upon the company the engineer works for, this margin is typically the maximum of 25 psig or 10%. The vessel specification sheet contains the design pressure, along with the design temperature, size, normal operating conditions and material of construction among others. It is this document that will eventually end up in a fabricator's lap and from which the mechanical design is made.
Relief Valve Set Pressure
Unfortunately, project schedules may require that relief valve sizing be carried out way before the fabricator has finished the mechanical design and certified the MAWP. The Process Engineer must use some pressure on which to base the relieving rate calculations. In paragraph 1.2.3.2, para. c, API 520 states that the design pressure may be used in place of the MAWP in all cases where the MAWP has not been established. Guess what pressure the Process Engineer usually sets relief valves at? There are even times when the relief valve must be set even lower than design pressure. For example, a high design pressure may be desirable for mechanical integrity but a PSV set at the design pressure may end up with a coincidental temperature that would require the use of exotic materials of construction or that promotes decomposition and/or run-away reaction.
0 Comments