Chemical and Process Engineering Resources

Experienced Based Rules of Chemical Engineering
Nov 08 2010 01:00 PM | Chris Haslego
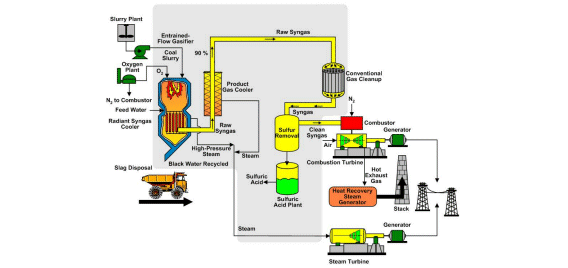
A. With industrial cooling towers, cooling to 90% of the ambient air saturation level is possible.
B. Relative tower size is dependent on the water temperature approach to the wet bulb temperature:
Twater-Twb (°F) | Relative Size |
5 | 2.4 |
15 | 1.0 |
25 | 0.55 |
C. Water circulation rates are generally 2-4 GPM/ft2 (81-162 L/min m2) and air velocities are usually 5-7 ft/s (1.5-2.0 m/s)
D. Countercurrent induced draft towers are the most common. These towers are capable of cooling to within 2 °F (1.1 °C) of the wet bulb temperature. A 5-10 °F (2.8-5.5 °C) approach is more common.
E. Evaporation losses are about 1% by mass of the circulation rate for every 10 °F (5.5 °C) of cooling. Drift losses are around 0.25% of the circulation rate. A blowdown of about 3% of the circulation rate is needed to prevent salt and chemical treatment buildup.
Conveyors
A. Pneumatic conveyors are best suited for high capacity applications over distances of up to about 400 ft. Pneumatic conveying is also appropriate for multiple sources and destinations. Vacuum or low pressure (6-12 psig or 0.4 to 0.8 bar) is used for generate air velocities from 35 to 120 ft/s (10.7-36.6 m/s). Air requirements are usually in the range of 1 to 7 cubic feet of air per cubic foot of solids (0.03 to 0.5 cubic meters of air per cubic meter of solids).
B. Drag-type conveyors (Redler) are completed enclosed and suited to short distances. Sizes range from 3 to 19 inches square (75 to 480 mm). Travel velocities can be from 30 to 250 ft/min (10 to 75 meters/min). The power requirements for these conveyors is higher than other types.
C. Bucket elevators are generally used for the vertical transport of sticky or abrasive materials. With a bucket measuring 20 in x 20 in (500 mm x 500 mm), capacities of 1000 cubic feet/hr (28 cubic meters/hr) can be reached at speeds of 100 ft/min (30 m/min). Speeds up to 300 ft/min (90 m/min) are possible.
D. Belt conveyors can be used for high capacity and long distance transports. Inclines up to 30° are possible. A 24 in (635 mm) belt can transport 3000 ft3./h (85 m3/h) at speeds of 100 ft/min (30.5 m/min). Speeds can be as high as 600 ft/min (183 m/min). Power consumption is relatively low.
E. Screw conveyors can be used for sticky or abrasive solids for transports up to 150 ft (46 m). Inclines can be up to about 20°. A 12 in (305 mm) diameter screw conveyor can transport 1000-3000 ft3./h (28-85 m3/h) at around 40-60 rpm.
Crystallization
A. During most crystallizations, C/Csat (concentration/saturated concentration) is kept near 1.02 to 1.05
B. Crystal growth rates and crystal sizes are controlled by limiting the degree of supersaturation.
C. During crystallization by cooling, the temperature of the solution is kept 1-2 °F (0.5-1.2 °C) below the saturation point at the given concentration.
D. A generally acceptable crystal growth rate is 0.10 - 0.80 mm/h
Drivers and Power Recovery
A. Efficiencies: 85-95% for motors, 40-75% for steam turbines, 28-38% for gas engines and turbines.
B. Electric motors are nearly always used for under 100 HP (75 kW). They are available up to 20,000 HP (14,915 kW).
C. Induction motors are most popular. Synchronous motors have speeds as low as 150 rpm at ratings above 50 HP (37.3 kW) only. Synchronous motors are good for low speed reciprocating compressors.
D. Steam turbines are seldom used below 100 HP (75 kW). Their speeds can be controlled and they make good spares for motors in case of a power failure.
E. Gas expanders may be justified for recovering several hundred horsepower. At lower recoveries, pressure let down will most likely be through a throttling valve.
Download these rules of thumb in MS Excel format.
Drum Type Vessels
A. Liquid drums are usually horizontal. Gas/Liquid separators are usually vertical.
B. Optimum Length/Diameter ratio is usually 3, range is 2.5 to 5.
C. Holdup time is 5 minutes for half full reflux drums and gas/liquid separators. Design for a 5-10 minute holdup for drums feeding another column.
D. For drums feeding a furnace, a holdup of 30 minutes is a good estimate.
E. Knockout drum in front of compressors should be designed for a holdup of 10 times the liquid volume passing per minute.
F. Liquid/Liquid separators should be designed for settling velocities of 2-3 inches/min
G. Gas velocities in gas/liquid separators:
![]() | Eq. (5) |
where:
k is 0.35 with horizontal mesh de-entrainers and 0.167 with vertical mesh deentrainers
k is 0.1 without mesh de-entrainers
velocity is in ft/s
?L is liquid density (lb/ft3)
?V is vapor density (lb/ft3)
H. A six inch mesh pad thickness is very popular for such vessels.
I. For positive pressure separations, disengagement spaces of 6-18 inches before the mesh pad and 12 inches after the pad are generally suitable.
Drying of Solids
A. Spray dryer have drying times of a few seconds. Rotary dryers have drying times ranging from a few minutes to up to an hour.
B. Continuous tray and belt dryers have drying times of 10-200 minutes for granular materials or 3-15 mm pellets.
C. Drum dryers used for highly viscous fluids use contact times of 3-12 seconds and produce flakes 1-3 mm thick. Diameters are generally 1.5-5 ft (0.5 - 1.5 m). Rotation speeds are 2-10 rpm and the maximum evaporation capacity is around 3000 lb/h (1363 kg/h).
D. Rotary cylindrical dryers operate with air velocities of 5-10 ft/s (1.5-3 m/s), up to 35 ft/s (10.5 m/s). Residence times range from 5-90 min. For initial design purposes, an 85% free cross sectional area is used. Countercurrent design should yield an exit gas temperature that is 18-35 °F (10-20 °C) above the solids temperature. Parallel flow should yield an exiting solids temperature of 212 °F (100 °C). Rotation speeds of 4-5 rpm are common. The product of rpm and diameter (in feet) should be 15-25.
E. Pneumatic conveying dryers are appropriate for particles 1-3 mm in diameter and in some cases up to 10 mm. Air velocities are usually 33-100 ft/s (10-30 m/s). Single pass residence time is typically near one minute. Size range from 0.6-1.0 ft (0.2-0.3 m) in diameter by 3.3-125 ft (1-38 m) in length.
F. Fluidized bed dryers work well with particles up to 4.0 mm in diameter. Designing for a gas velocity that is 1.7-2 times the minimum fluidization velocity is good practice. Normally, drying times of 1-2 minutes are sufficient in continuous operation.
Electric Motors and Turbines
A. Efficiencies range from 85-95% for electric motors, 42-78% for steam turbines 28-38% for gas engines and turbines.
B. For services under 75 kW (100 hp), electric motors are almost always used. They can be used for services up to about 15000 kW (20000 hp).
C. Turbines can be justified in services where they will yield several hundred horsepowers. Otherwise, throttle valves are used to release pressure.
D. A quick estimate of the energy available to a turbine is given by:
![]() | Eq. (6) |
where:
?H = actual available energy, Btu/lb
Cp = heat capacity at constant pressure, Btu/lb °F
T1 = inlet temperature, °R
P1 = inlet pressure, psia
P2 = outlet pressure, psia
x = Cp/Cv
Evaporation
A. Most popular types are long tube vertical with natural or forced circulation. Tubes range from 3/4"" to 2.5"" (19-63 mm) in diameter and 12-30 ft (3.6-9.1 m) in length.
B. Forced circulation tube velocities are generally in the 15-20 ft/s (4.5-6 m/s) range.
C. Boiling Point Elevation (BPE) as a result of having dissolved solids must be accounted for in the differences between the solution temperature and the temperature of the saturated vapor.
D. BPE's greater than 7 °F (3.9 °C) usually result in 4-6 effects in series (feed-forward) as an economical solution. With smaller BPE's, more effects in series are typically more economical, depending on the cost of steam.
E. Reverse feed results in the more concentrated solution being heated with the hottest steam to minimize surface area. However, the solution must be pumped from one stage to the next.
F. Interstage steam pressures can be increased with ejectors (20-30% efficient) or mechanical compressors (70-75% efficient).
Download these rules of thumb in MS Excel format.
Filtration
A. Initially, processes are classified according to their cake buildup in a laboratory vacuum leaf filter : 0.10 - 10.0 cm/s (rapid), 0.10-10.0 cm/min (medium), 0.10-10.0 cm/h (slow).
B. Continuous filtration methods should not be used if 0.35 sm of cake cannot be formed in less than 5 minutes.
C. Belts, top feed drums, and pusher-type centrifuges are best for rapid filtering.
D. Vacuum drums and disk or peeler-type centrifuges are best for medium filtering.
E. Pressure filters or sedimenting centrifuges are best for slow filtering.
F. Cartridges, precoat drums, and sand filters can be used for clarification duties with negligible buildup.
G. Finely ground mineral ores can utilize rotary drum rates of 1500 lb/day ft2 (7335 kg/day m2) at 20 rev/h and 18-25 in Hg (457-635 mm Hg) vacuum.
H. Course solids and crystals can be filtered at rates of 6000 lb/day ft2 (29,340 kg/day m2) at 20 rev/h and 2-6 in Hg (51-152 mm Hg) vacuum.
Heat Exchangers
A. For the heat exchanger equation, Q = UAF (LMTD), use F = 0.9 when charts for the LMTD correction factor are not available.
B. Most commonly used tubes are 3/4 in. (1.9 cm) in outer diameter on a 1 in triangular spacing at 16 ft (4.9 m) long.
C. A 1 ft (30 cm) shell will contains about 100 ft2 (9.3 m2)
A 2 ft (60 cm) shell will contain about 400 ft2 (37.2 m2)
A 3 ft (90 cm) shell will contain about 1100 ft2 (102 m2)
D. Typical velocities in the tubes should be 3-10 ft/s (1-3 m/s) for liquids and 30-100 ft/s (9-30 m/s) for gases.
E. Flows that are corrosive, fouling, scaling, or under high pressure are usually placed in the tubes.
F. Viscous and condensing fluids are typically placed on the shell side.
G. Pressure drops are about 1.5 psi (0.1 bar) for vaporization and 3-10 psi (0.2-0.68 bar) for other services.
H. The minimum approach temperature for shell and tube exchangers is about 20 °F (10 °C) for fluids and 10 °F (5 °C) for refrigerants.
I. Cooling tower water is typically available at a maximum temperature of 90 °F (30 °C) and should be returned to the tower no higher than 115 °F (45 °C)
J. Shell and Tube heat transfer coefficient for estimation purposes can be found in many reference books or an online list can be found at one of the two following addresses:
http://www.cheresources.com/uexchangers.shtml
K. Double pipe heat exchangers may be a good choice for areas from 100 to 200 ft2 (9.3-18.6 m2)
L. Spiral heat exchangers are often used to slurry interchangers and other services containing solids
M. Plate heat exchanger with gaskets can be used up to 320 °F (160 °C) and are often used for interchanging duties due to their high efficiencies and ability to "cross" temperatures. More about compact heat exchangers can be found at: http://www.virginiaheattransfer.com/
Mixing and Agitation
A. Mild agitation results from superficial fluid velocities of 0.10-0.20 ft/s (0.03-0.06 m/s). Intense agitation results from velocities of 0.70-1.0 ft/s (0.21-0.30 m/s).
B. For baffled tanks, agitation intensity is measured by power input and impeller tip speeds:
 |  | Power Requirements | Tip Velocity | ||||||||||
 | HP/1000 gal | kW/m3 | ft/s | m/s | |||||||||
Blending | 0.2 | - | 0.5 | 0.033 | - | 0.082 | -------------------- | ------------------ | |||||
Homogeneous Reaction | 0.5 | - | 1.5 | 0.082 | - | 0.247 | 7.5 | - | 10.0 | 2.3 | - | 3.1 | |
Reaction w/ Heat Transfer | 1.5 | - | 5.0 | 0.247 | - | 0.824 | 10.0 | - | 15.0 | 3.1 | - | 4.6 | |
Liquid-Liquid Mixture | 5.0 | 0.824 | 15.0 | - | 20.0 | 4.6 | - | 6.1 | |||||
Liquid-Gas Mixture | 5.0 | - | 10.0 | 0.824 | - | 1.647 | 15.0 | - | 20.0 | 4.6 | - | 6.1 | |
Slurries | 10.0 | 1.647 | -------------------- | ------------------ |
C. Various geometries of an agitated tank relative to diameter (D) of the vessel include:
Liquid Level = D
Turbine Impeller Diameter = D/3
Impeller Level Above Bottom = D/3
Impeller Blade Width = D/15
Four Vertical Baffle Width = D/10
D. For settling velocities around 0.03 ft/s, solids suspension can be accomplished with turbine or propeller impellers. For settling velocities above 0.15 ft/s, intense propeller agitation is needed.
E. Power to mix a fluid of gas and liquid can be 25-50% less than the power to mix the liquid alone.
Download these rules of thumb in MS Excel format.
13 Comments
Progreso es compartir el conocimiento. Gracias
Thanks for the good information.
amazing. thank you!
thank u for information.
nice
design calc. of heat transfer equipment needed
good
Thanks so much
all process engineering at a glance, excellent
really, this is a very helpful data.
i need one more help.
I need the vapor pressure data of cetyl chloride, if any one can help me...please do the needful.
very nice.