Chemical and Process Engineering Resources

Experienced Based Rules of Chemical Engineering
Nov 08 2010 01:00 PM | Chris Haslego
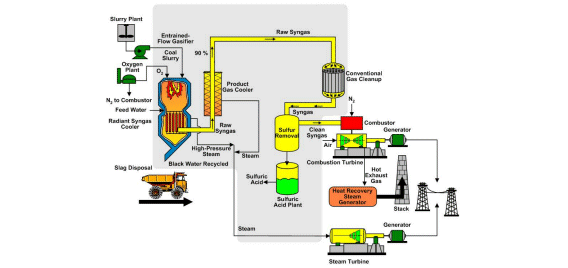
Pressure and Storage Vessels
Pressure Vessels
A. Design Temperatures between -30 and 345 °C (-22 to 653 °F) is typically about 25 °C (77 °F) above maximum operating temperature, margins increase above this range.
B. Design pressure is 10% or 0.69 to 1.7 bar (10 to 25 psi) above the maximum operating pressure,
C. For vacuum operations, design pressures are 1 barg (15 psig) to full vacuum.
D. Minimum thicknesses for maintaining tank structure are:
6.4 mm (0.25 in) for 1.07 m (42 in) diameter and under
8.1 mm (0.32 in) for 1.07-1.52 m (42-60 in) diameter
9.7 mm (0.38 in) for diameters over 1.52 m (60 in)
E. Allowable working stresses are taken as 1/4 of the ultimate strength of the material.
F. Maximum allowable working stresses:
Temperature | -20 to 650 °F | 750 °F | 850 °F | 1000 °F |
 | -30 to 345 °C | 400 °C | 455 °C | 540 °C |
CS SA203 | 18759 psi | 15650 psi | 9950 psi | 2500 psi |
 | 1290 bar | 1070 bar | 686 bar | 273 bar |
302 SS | 18750 psi | 18750 psi | 15950 psi | 6250 psi |
 | 1290 bar | 1290 bar | 1100 bar | 431 bar |
G. Thickness based on pressure and radius is given by:
![]() | Eq. (7) |
where pressure is in psig, radius in inches, stress in psi, corrosion allowance in inches.
**Weld Efficiency can usually be taken as 0.85 for initial design work
H. Guidelines for corrosion allowances are as follows: 0.35 in (9 mm) for known corrosive fluids, 0.15 in (4 mm) for non-corrosive fluids, and 0.06 in (1.5 mm) for steam drums and air receivers.
Storage Vessels
I. For less than 3.8 m3 (1000 gallons) use vertical tanks on legs
J. Between 3.8 m3 and 38 m3 (1000 to 10,000 gallons) use horizontal tanks on concrete supports.
K. Beyond 38 m3 (10,000 gallons) use vertical tanks on concrete pads.
L. Liquids with low vapor pressures, use tanks with floating roofs.
M. Raw material feed tanks are often specified for 30 days feed supplies.
N. Storage tank capacity should be at 1.5 times the capacity of mobile supply vessels. For example, 28.4 m3 (7500 gallon) tanker truck, 130 m3 (34,500 gallon) rail cars.
Piping
A. Liquid lines should be sized for a velocity of (5+D/3) ft/s and a pressure drop of 2.0 psi/100 ft of pipe at pump discharges. At the pump suction, size for (1.3+D/6) ft/s and a pressure drop of 0.4 psi/100 ft of pipe. **D is pipe diameter in inches.
B. Steam or gas lines can be sized for 20D ft/s and pressure drops of 0.5 psi/100 ft of pipe.
C. Limits on superheated, dry steam or line should be 61 m/s (200 ft/s) and a pressure drop of 0.1 bar/100 m or 0.5 psi/100 ft of pipe.
D. For turbulent flow in commercial steel pipes, use the following:
![]() | Eq. (8) |
where:
ΔP = fricitional pressure drop (psi) / 100 equivalent feet of pipe
M = mass flow, lb/hr
μ = viscosity, cP
ρ = density, lb/ft3
D = pipe inside diameter, in.
** for smooth heat exchanger steel tubes, replace 20,000 with 23,000
E. For two phase flow, an estimate often used is Lockhart and Martinelli:
First, the pressure drops are calculated as if each phase exist alone in the pipe, then
![]() | Eq. (9) |
now, the total pressure drop can be calculated by one of the following:
![]() | Eq. (10) |
where:
YL = 4.6X-1.78 + 12.5X-0.68 + 0.65
YG = X2 YL
F. Control valves require at least 0.69 bar (10 psi) pressure drop for sufficient control.
G. Flange ratings include 10, 20, 40, 103, and 175 bar (150, 300, 600, 1500, and 2500 psig).
H. Globe valves are most commonly used for gases and when tight shutoff is required. Gate valves are common for most other services.
I. Screwed fitting are generally used for line sizes 2 inches and smaller. Larger connections should utilize flanges or welding to eliminate leakage.
J. Pipe Schedule Number = 1000P/S (approximate) where P is the internal pressure rating in psig and S is the allowable working stress of the material is psi. Schedule 40 is the most common.
Pumps
A. Power estimates for pumping liquids:
kW = (1.67) [Flow (m3/min)] [Pressure drop (bar)] / Efficiency | Eq. (11) |
hp = [Flow (gpm)] [Pressure drop (psi)] / 1714 (Efficiency) | Eq. (12) |
**Efficiency expressed as a fraction in these relations
B. NPSH is defined as:
NPSH = (pressure at impeller eye-vapor pressure) / (density*gravitational constant) | Eq. (13) |
Common range is 1.2 to 6.1 m (4-20 ft) of liquid.
C. An equation developed for efficiency based on the GPSA Engineering Data Book is:
Efficiency = 80-0.2855F+.000378FG-.000000238FG2+.000539F2-.000000639(F2)G+ 0.0000000004(F2)(G2) | Eq. (14) |
where Efficiency is in fraction form, F is developed head in feet, G is flow in GPM
Ranges of applicability are F=50-300 ft and G=100-1000 GPM
Error documented at 3.5%
D. Centrifugal pumps: Single stage for 0.057-18.9 m3/min (15-5000 GPM), 152 m (500 ft) maximum head;
For flow of 0.076-41.6 m3/min (20-11,000 GPM) use multistage, 1675 m (5500 ft) maximum head;
Efficiencies of 45% at 0.378 m3/min (100 GPM), 70% at 1.89 m3/min (500 GPM), 80% at 37.8 m3/min (10,000 GPM).
E. Axial pumps can be used for flows of 0.076-378 m3/min (20-100,000 GPM). Expect heads up to 12 m (40 ft) and efficiencies of about 65-85%.
F. Rotary pumps can be used for flows of 0.00378-18.9 m3/min (1-5000 GPM). Expect heads up to 15,200 m (50,000 ft) and efficiencies of about 50-80%.
G. Reciporating pumps can be used for 0.0378-37.8 m3/min (10-100,000 GPM). Expect heads up to 300,000 m (1,000,000 ft). Efficiencies: 70% at 7.46 kW (10 hp), 85% at 37.3 kW (50 hp), and 90% at 373 kW (500 hp).
Download these rules of thumb in MS Excel format.
Tray Towers
A. For ideal mixtures, relative volatility can be taken as the ratio of pure component vapor pressures.
B. Tower operating pressure is most often determined by the cooling medium in condenser or the maximum allowable reboiler temperature to avoid degradation of the process fluid.
C. For sequencing columns:
- Perform the easiest separation first (least trays and lowest reflux.
- If relative volatility nor feed composition vary widely, take products off one at time as the overhead.
- If the relative volatility of components do vary significantly, remove products in order of decreasing volatility.
- If the concentrations of the feed vary significantly but the relative volatility do not, remove products in order of decreasing concentration.
D. The most economic reflux ratio usually is between 1.2Rmin and 1.5Rmin.
E. The most economic number of trays is usually about twice the minimum number of trays. The minimum number of trays is determined with the Fenske-Underwood Equation.
F. Typically, 10% more trays than are calculated are specified for a tower.
G. Tray spacings should be from 18 to 24 inches, with accessibility in mind.
H. Peak tray efficiencies usually occur at linear vapor velocities of 2 ft/s (0.6 m/s) at moderate pressures, or 6 ft/s (1.8 m/s) under vacuum conditions.
I. A typical pressure drop per tray is 0.1 psi (0.007 bar).
J. Tray efficiencies for aqueous solutions are usually in the range of 60-90% while gas absorption and stripping typically have efficiencies closer to 10-20%.
K. The three most common types of trays are valve, sieve, and bubble cap. Bubble cap trays are typically used when low-turn down is expected or a lower pressure drop than the valve or sieve trays can provide is necessary.
L. Seive tray holes are 0.25 to 0.50 in. diameter with the total hole area being about 10% of the total active tray area.
M. Valve trays typically have 1.5 in. diameter holes each with a lifting cap. 12-14 caps/square foot of tray is a good benchmark. Valve trays usually cost less than seive trays.
N. The most common weir heights are 2 and 3 in and the weir length is typically 75% of the tray diameter.
O. Reflux pumps should be at least 25% overdesigned.
P. The optimum Kremser absorption factor is usually in the range of 1.25 to 2.00.
Q. Reflux drums are almost always horizontally mounted and designed for a 5 min holdup at half of the drum's capacity.
R. For towers that are at least 3 ft (0.9 m) is diameter, 4 ft (1.2 m) should be added to the top for vapor release and 6 ft (1.8 m) should be added to the bottom to account for the liquid level and reboiler return.
S. Limit tower heights to 175 ft (53 m) due to wind load and foundation considerations.
T. The Length/Diameter ratio of a tower should be no more than 30 and preferrably below 20.
U. A rough estimate of reboiler duty as a function of tower diameter is given by:
Q = 0.5 D2 for pressure distillation
Q = 0.3 D2 for atmospheric distillation
Q = 0.15 D2 for vacuum distillation
where Q is in Million Btu/hr and D is tower diameter in feet.
Packed Towers
A. Packed towers almost always have lower pressure drop than comparable tray towers.
B. Packing is often retrofitted into existing tray towers to increase capacity or separation.
C. For gas flowrates of 500 ft3/min (14.2 m3/min) use 1 in (2.5 cm) packing, for gas flows of 2000 ft3/min (56.6 m3/min) or more, use 2 in (5 cm) packing.
D. Ratio of tower diameter to packing diameter should usually be at least 15.
E. Due to the possibility of deformation, plastic packing should be limited to an unsupported depth of 10-15 ft (3-4 m) while metallatic packing can withstand 20-25 ft (6-7.6 m).
F. Liquid distributor should be placed every 5-10 tower diameters (along the length) for pall rings and every 20 ft (6.5 m) for other types of random packings.
G. For redistribution, there should be 8-12 streams per sq. foot of tower area for tower larger than three feet in diameter. They should be even more numerous in smaller towers.
H. Packed columns should operate near 70% flooding.
I. Height Equivalent to Theoretical Stage (HETS) for vapor-liquid contacting is 1.3-1.8 ft (0.4-0.56 m) for 1 in pall rings and 2.5-3.0 ft (0.76-0.90 m) for 2 in pall rings
J. Design pressure drops should be as follows:
Service | Â | Pressure drop (in water/ft packing) |
Absorbers and Regenerators | Â | |
 | Non-Foaming Systems | 0.25 - 0.40 |
 | Moderate Foaming Systems | 0.15 - 0.25 |
Fume Scrubbers | Â | |
 | Water Absorbent | 0.40 - 0.60 |
 | Chemical Absorbent | 0.25 - 0.40 |
Atmospheric or Pressure Distillation | 0.40 - 0.80 | |
Vacuum Distillation | 0.15 - 0.40 | |
Maximum for Any System | 1.0 |
Â
Reactors
A. The rate of reaction must be established in the laboratory and the residence time or space velocity will eventually have to be determined in a pilot plant.
B. Catalyst particle sizes: 0.10 mm for fluidized beds, 1 mm in slurry beds, and 2-5 mm in fixed beds.
C. For homogeneous stirred tank reactions, the agitor power input should be about 0.5-1.5 hp/1000 gal (0.1-0.3 kW/m3), however, if heat is to be transferred, the agitation should be about three times these amounts.
D. Ideal CSTR behavior is usually reached when the mean residence time is 5-10 times the length needed to achieve homogeneity. Homogeneity is typically reached with 500-2000 revolutions of a properly designed stirrer.
E. Relatively slow reactions between liquids or slurries are usually conducted most economically in a battery of 3-5 CSTR's in series.
F. Tubular flow reactors are typically used for high productions rates and when the residence times are short. Tubular reactors are also a good choice when significant heat transfer to or from the reactor is necessary.
G. For conversion under 95% of equilibrium, the reaction performance of a 5 stages CSTR approaches that of a plug flow reactor.
H. Typically the chemical reaction rate will double for a 18 °F (10 °C) increase in temperature.
I. The reaction rate in a heterogeneous reaction is often controlled more by the rate of heat or mass transfer than by chemical kinetics.
J. Sometimes, catalysts usefulness is in improving selectivity rather than increasing the rate of the reaction.
Download these rules of thumb in MS Excel format.
13 Comments
Progreso es compartir el conocimiento. Gracias
Thanks for the good information.
amazing. thank you!
thank u for information.
nice
design calc. of heat transfer equipment needed
good
Thanks so much
all process engineering at a glance, excellent
really, this is a very helpful data.
i need one more help.
I need the vapor pressure data of cetyl chloride, if any one can help me...please do the needful.
very nice.