Chemical and Process Engineering Resources
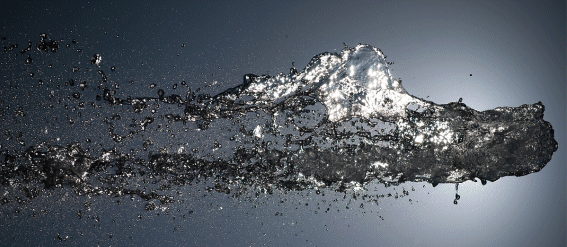
Selecting a Valve Type
When speaking of valves, it's easy to get lost in the terminology. Valve types are used to describe the mechanical characteristics and geometry (Ex/ gate, ball, globe valves). We'll use valve control to refer to how the valve travel or stroke (openness) relates to the flow:
1. Equal Percentage: equal increments of valve travel produce an equal percentage in flow change
2. Linear: valve travel is directly proportional to the valve stoke
3. Quick opening: large increase in flow with a small change in valve stroke
So how do you decide which valve control to use? Here are some rules of thumb for each one:
1. Equal Percentage (most commonly used valve control)
a. Used in processes where large changes in pressure drop are expected
b. Used in processes where a small percentage of the total pressure drop is permitted by the valve
c. Used in temperature and pressure control loops
2. Linear
a. Used in liquid level or flow loops
b. Used in systems where the pressure drop across the valve is expected to remain fairly constant (ie. steady state systems)
3. Quick Opening
a. Used for frequent on-off service
b. Used for processes where "instantly" large flow is needed (ie. safety systems or cooling water systems)
Now that we've covered the various types of valve control, we'll take a look at the most common valve types.
Gate Valves
Best Suited Control: Quick Opening
Recommended Uses:
1. Fully open/closed, non-throttling
2. Infrequent operation
3. Minimal fluid trapping in line
Applications: Oil, gas, air, slurries, heavy liquids, steam, noncondensing gases, and corrosive liquids
Advantages:
1. High capacity
2. Tight shutoff
3. Low cost
4. Little resistance to flow
Disadvantages:
1. Poor control
2. Cavitate at low pressure drops
3. Cannot be used for throttling
Recommended Uses:
1. Fully open/closed, non-throttling
2. Infrequent operation
3. Minimal fluid trapping in line
Applications: Oil, gas, air, slurries, heavy liquids, steam, noncondensing gases, and corrosive liquids
Advantages:
1. High capacity
2. Tight shutoff
3. Low cost
4. Little resistance to flow
Disadvantages:
1. Poor control
2. Cavitate at low pressure drops
3. Cannot be used for throttling
Globe Valves
Best Suited Control: Linear and Equal percentage
Recommended Uses:
1. Throttling service/flow regulation
2. Frequent operation
Applications: Liquids, vapors, gases, corrosive substances, slurries
Advantages:
1. Efficient throttling
2. Accurate flow control
3. Available in multiple ports
Disadvantages:
1. High pressure drop
2. More expensive than other valves
Recommended Uses:
1. Throttling service/flow regulation
2. Frequent operation
Applications: Liquids, vapors, gases, corrosive substances, slurries
Advantages:
1. Efficient throttling
2. Accurate flow control
3. Available in multiple ports
Disadvantages:
1. High pressure drop
2. More expensive than other valves
Ball Valves
Best Suited Control: Quick opening, linear
Recommended Uses:
1. Fully open/closed, limited-throttling
2. Higher temperature fluids
Applications: Most liquids, high temperatures, slurries
Advantages:
1. Low cost
2. High capacity
3. Low leakage and maint.
4. Tight sealing with low torque
Disadvantages:
1. Poor throttling characteristics
2. Prone to cavitation
Recommended Uses:
1. Fully open/closed, limited-throttling
2. Higher temperature fluids
Applications: Most liquids, high temperatures, slurries
Advantages:
1. Low cost
2. High capacity
3. Low leakage and maint.
4. Tight sealing with low torque
Disadvantages:
1. Poor throttling characteristics
2. Prone to cavitation
Butterfly Valves
Best Suited Control: Linear, Equal percentage
Recommended Uses:
1. Fully open/closed or throttling services
2. Frequent operation
3. Minimal fluid trapping in line
Applications: Liquids, gases, slurries, liquids with suspended solids
Advantages:
1. Low cost and maint.
2. High capacity
3. Good flow control
4. Low pressure drop
Disadvantages:
1. High torque required for control
2. Prone to cavitation at lower flows
Recommended Uses:
1. Fully open/closed or throttling services
2. Frequent operation
3. Minimal fluid trapping in line
Applications: Liquids, gases, slurries, liquids with suspended solids
Advantages:
1. Low cost and maint.
2. High capacity
3. Good flow control
4. Low pressure drop
Disadvantages:
1. High torque required for control
2. Prone to cavitation at lower flows
Other Valves
Another type of valve commonly used in conjunction with other valves is called a check valve. Check valves are designed to restrict the flow to one direction. If the flow reverses direction, the check valve closes. Relief valves are used to regulate the operating pressure of incompressible flow. Safety valves are used to release excess pressure in gases or compressible fluids.
References
Rosaler, Robert C., Standard Handbook of Plant Engineering, McGraw-Hill, New York, 1995, pages 10-110 through 10-122
Purcell, Michael K., "Easily Select and Size Control Valves", Chemical Engineering Progress, March 1999, pages 45-50
16 Comments
Hi, Chris
I'm Emad Elgebesy. Senior process engineer in Worley Parsons. First of all, thanks for your clear efforts on the community, And im willing to share my experiance in this regard.
In Worley Parsons, we did the valve calculation for, single phase & two phase. The above mentioned calculation did not demonstrate which phase is, But i think this liquid phase valve calculation only.
After calculating the Cv, Supplier should verify the strock range (10% to 90%) is commnly used, noise level& body size as well.
Finally, there is many free control valve software of FirstVue do regirous calculation
Regards
Emad
thanks for the info Chris
Dear Chris,
If the vendor did not supply the valve chart, is there any we can get the control valve opening by using calculated Cv and rated Cv?
Cv charts are generally made for experimental data. If your valve supplier doesn't have a Cv chart for a valve that they sold to you...find a new valve supplier...that is not acceptable.
Chris,
Nice article!
I'd like to make a suggestion for a follow-up article. There are many times that we size liquid control valves in systems where the source pressure comes from a gas in the system instead of a pump (I am thinking of scrubber dump valves). In these situations, after sizing the liquid valve, we often need to determine the "gas blowby" rate, which is how much gas would flow through the valve if the liquid level control loop failed and left the valve wide open. This is often required when sizing pressure safety valves further downstream in the system. It would be great to add an additional step to this article to calculate the maximum gas flow through the selected liquid control valve.
Regards,
Paul
Great job
Thanks Chris
Really Helpful post for someone like me who is recent graduate, explained in very easy way.
I have few questions.
1. is this procedure and equations are useful for compressible fluids/ Gases
2. Do you have anything for selecting control valve for compressible fluids/gases ? (Explaining Nice and easy with thumb rules for selection criteria, like gain should never be less than 0.5 etc.)
I found a handbook from Emerson on control valve. That procedure seems to be too complicated or theoretical.( Too many contents no thumb rules ) Page 118 of Fisher control valve handbook, Emerson (its free on google - couldn't post the link)
Beautiful thanks Chris
Dear all,
In maximum case of flowrate, why the pressure dropcontrol valve should have the minimum limitation?
For example, when calculating hydraulic balance, at max case ( 120% normal flowrate), the pressure drop of control valve for liquid service is from 0.5 to 1 kg/cm2?
In my opinion, if the pressure drop of CV is too small, the Cv of CV will be very big. Therefore, even though the CV is full open at max. case, CV can not control the flowrate is the case, right?