Chemical and Process Engineering Resources
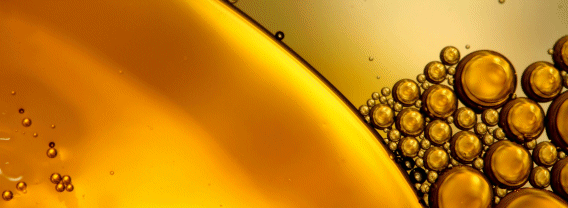
Selection of Mode of Operation
Extractors can be operated in crosscurrent or counter-current mode. The following section compares these configurations.
Cross-Current Operation
Crosscurrent mode is mostly used in batch operation. Batch extractors have traditionally been used in low capacity multi-product plants such as are typical in the pharmaceutical and agrochemical industries. For washing and neutralization operations that require very few stages, crosscurrent operation is particularly practical and economical and offers a great deal of flexibility. The extraction equipment is usually an agitated tank that may also be used for the reaction steps. In these tanks, solvent is first added to the feed, the contents are mixed, settled and then separated. Single stage extraction is used when the extraction is fairly simple and can be achieved without a high amount of solvent. If more than one stage is required, multiple solvent-washes are given.
Though operation in crosscurrent mode offers more flexibility, it is not very desirable due to the high solvent requirements and low extraction yields. The following illustration gives a quick method to calculate solvent requirements for crosscurrent mode of extraction.
A single-stage extractor can be represented as:
where
F = Feed quantity / rate, massR = Raffinate quantity / rate, massS = Solvent quantity / rate, massE = Extract quantity / rate, mass
Xf, Xr, Ys, and Ye are the weight fractions of solute in the feed, raffinate, solvent and extract, respectively.
Partition coefficient 'm' is defined as the ratio of Ye to Xr at equilibrium conditions
The flows and concentrations are represented in solute-free basis as such a representation leads to simplification of equations. For example, for a 100 kg/hr feed containing 10% weight acetic acid, F = 100-10 = 90 kg/hr, Xr = 0.1/(1-0.1) = 0.111
The component mass balance can be represented as:F Xf + S Ys = R Xr + E Ye
Assuming (i) immiscibility of feed and solvent and (ii) the initial solvent is free of solute, i.e., F = R, S = E and Ys = 0 and using the equilibrium relation of Ye = m Xr, this equation simplifies to
S = F/m (Xf /Xr-1)
or
reduction ratio, Xf /Xr = 1+ m S/F
For multi-stage crosscurrent operation:
Assuming that the partition coefficient (m) is constant over the concentration range and the solvent quantity in each of the 'n' stages is the same, i.e., S1 = S2 =.....=S n = S/n,
Solvent Requirement is
S = n * F/m [(Xf /Xr)1/n - 1]
reduction ratio Xf /Xr = (1+mS/nF)n
It can be proved mathematically that the total solvent quantity would be minimum if the solvent were distributed equally between washes.
Diminishing Returns
The following chart shows solvent requirements for a typical reduction ratio (X f /Xr) of 10 using crosscurrent extraction.
![]() |
Figure 1: Reduction Ratio for Crosscurrent Extraction |
With one stage, 18,000 kg of solvent is required for 1,000 kg of feed (m = 1 and Xf / Xr = 10). With two stages, solvent requirement reduces to 8,650 kg, and with three stages, it reduces further to 6,930 kg. However, as can be seen from the chart, using more than three stages has minimal effect on solvent usage. This fact combined with practical limitations of solvent handling and increased batch time confines the number of solvent washes to three.
Counter-Current Operation
As described above, the crosscurrent operation is mostly used in low capacity multi-product batch plants. For larger volume operation and more efficient use of solvent, countercurrent mixer-settlers or columns are employed. Countercurrent operation conserves the mass transfer driving force and hence gives optimal performance.
Equations for countercurrent extraction get more complicated with increasing number of stages. It can be shown that for a 'n' stage operation, the raffinate concentration would be
Xr = Xf * (mS/F - 1)/ ( [mS/F] n+1 -1)
The solvent requirement for any raffinate concentration Xr could be determined by iteration from the above equation.
For mS/F = 1, the equation takes the form of Xr = Xf / (n + 1)
The dimensionless term mS/F, included in all the above equations, is called the extraction factor (E), and is an important parameter in the design of extraction processes. For a given number of stages, the higher the E factor, the higher is the reduction ratio and easier is the extraction. Systems with E of less than 1.3 are not likely to be commercially feasible.
Comparing Counter versus Cross Flow Operation
The following graph compares the reduction ratios (Xf / Xr) of the crosscurrent and countercurrent modes of operation.
![]() |
Figure 2: Comparing Counter and Cross Flow Extraction |
The graph shows that for a given extraction factor (E), and number of stager (n), the countercurrent mode of operation outperforms the crosscurrent mode. This is demonstrated in a case study presented at the end of this paper. Koch-Glitsch has demonstrated these benefits on their pilot and commercial scale extraction columns for several systems.
The equations given above can be used to compare solvent requirements for various modes of operation and can serve as a starting point for identifying scope for optimizing solvent quantity. However, these equations should be used with caution as the assumptions of immiscibility, constancy of partition coefficient over desired range and solute-free fresh solvent are not valid in all practical applications.
As the solvent quantity is reduced, the solute concentration in the extract increases. This usually affects the physical properties and the selectivity. Therefore optimization exercise should be backed up by laboratory extraction data.
1 Comments
good sharing, mr madhavan!