Chemical and Process Engineering Resources
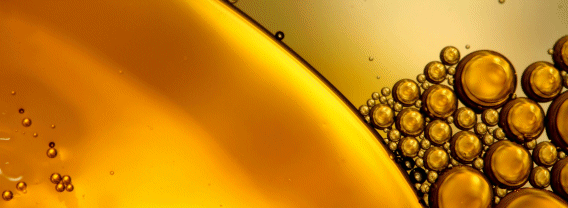
Selecting the Type of Extractor
Commercially important extractors can be classified into the following broad categories.
Mixer-Settlers
Centrifugal devices
Column contactors (static) - Examples include spray columns, sieve plate columns, and random or structurally packed columns.
Column contactors (agitated) - Agitated columns can be further split into rotary or reciprocating type. Examples of rotary agitated columns include rotary disc contactor, Scheibel column, Kuhni column. Examples of reciprocating agitated columns include the Karr column and the pulsed column.
Mixer-Settlers
As the name indicates, are usually a series of static or agitated mixers interspersed with settling stages. These are mostly used in the metal industry where intense mixing and high residence time is required by the reactive extraction processes.
In batch mode of operation, these mixer-settlers could be simple batch vessels where feed and solvent are mixed and settled. This operation is repeated with fresh solvent washes as described earlier.
Centrifugal Contactors
Centrifugal contactors are high-speed rotary machines that offer advantages of very low residence time. The number of stages in a centrifugal device is usually limited to one, but currently devices with multiple numbers of stages are common. These extractors are mainly used in pharmaceutical industry.
Counter-current Column Contactors
Counter-current column contactors are most popular in the chemical industry. These could be static or agitated. Several types of extractors are available (see Table 2) and each has its own advantages.
Factors Affecting the Selection of Contactors
Important factors to consider when selecting extractor types are the stage requirements, fluid properties and operational considerations. The following table outlines the capabilities and characteristics of different extractor-types:
Property | Mixer-Settler | Centrifugal Contactor | Static Column | Agitated Column |
Number of Stages | Low | Low | Moderate | High |
Flow Rate | High | Low | Moderate | Moderate |
Residence Time | Very High | Very Low | Moderate | Moderate |
Interfacial Tension | Moderate to High | Low to Moderate | Low to Moderate | Moderate to High |
Viscosity | Low to High | Low to Moderate | Low to Moderate | Low to High |
Density Difference | Low to High | Low to Moderate | Low to Moderate | Low to High |
Floor Space | High | Moderate | Low | Low |
The Karr reciprocating plate extractor can effectively handle low interfacial tension systems. Other factors governing extractor selection are presence of solids, safety and maintenance requirements.
Design Criteria
The basic function of extraction equipment is to mix two phases, form and maintain droplets of dispersed phase and subsequently separate the phases. The following section outlines some of the factors that need to be considered while designing and optimizing extraction equipment.
- Mixing - The amount of mixing required is determined by physical properties such as viscosity, interfacial tension and density differences between the two phases. It is important to provide just the right amount of mixing. Less mixing causes the formation of large droplets and decreases interfacial area (interfacial area varies with the square of the droplet diameter). This reduces mass transfer and decreases stage efficiency. Higher agitation (more mixing) minimizes mass transfer resistance during reactions and extraction but contributes to the formation of small and difficult-to-settle droplets or emulsions. In agitated batch extractors, the agitator design is often optimized for reaction and heat transfer, not extraction, as these are generally multi-purpose vessels.The agitator imparts maximum energy at the tip where the velocity is highest and minimum energy at the center. This creates non-uniform droplet sizes, with the smallest being formed at the agitator tip. Reaching extraction equilibrium is controlled by the largest droplet size and the smallest droplet controls settling time. Therefore, over-agitation sometimes takes its toll by causing difficulties in phase separation. Usually a redesign in terms of configuration or change in agitation speed helps in optimizing batch time.Static extraction columns rely completely on the packing/internals and fluid flow velocities past the internals to create turbulence and droplets. Therefore these are restricted by minimum flow requirement of at least one of the phases. Agitated columns have more operating flexibility as the specific energy input can be varied in most designs. Axial mixing (along column length) in column contactors reduces stage efficiency. Baffles or similar arrangements are used to minimize axial mixing in static as well as agitated columns. It is also important to avoid temperature gradients in columns to prevent thermal currents contributing to axial mixing.
- Settling - The settling characteristics depend on the fluid properties (density difference, interfacial tension, and continuous phase viscosity) and the amount of mixing. Settling in agitated batch vessels is carried out by stopping the agitator. In continuous columns, a settling section is provided either as a part of the extractor or as a separate piece of equipment downstream of the extractor. Emulsions are usually formed due to over agitation and in such cases, settling needs to be carried out over an extended period. Emulsions can also form due to the inherent nature of the chemical compounds involved or due to contaminants that substantially lower the interfacial tension. Sometimes coagulants are added to prevent or minimize emulsification. Passing the emulsion layer through a coalescer can break some of these emulsions. In continuous extractors, the creation of emulsions is less severe as good droplet size distribution can be attained at lower agitation speeds in a lesser diameter column. Also, columns such as the Karr reciprocating plate extractor impart uniform energy throughout the radius as a result of the reciprocating motion and this creates a much narrower droplet distribution.A similar phenomenon to emulsions is the formation of a 'rag layer'. This is a layer containing loose solid substances that float at the interface. These solid substances are generally foreign impurities that exist in the feed streams or those that precipitate from the system during extraction. In continuous extraction the liquid interface containing the rag layer can be continuously withdrawn, filtered and sent back to extractor. Selection of continuous and dispersed phases can have an effect on formation of emulsion and rag layer. Reversing continuous and dispersed phases sometimes drastically reduces or eliminates emulsion formation. Changing extraction temperature could also help in reducing emulsion and rag layer.
- Selection of Continuous and Dispersed Phase - In column extractors, the phase with the lower viscosity (lower flow resistance) is generally chosen as the continuous phase. Also note that the phase with the higher flow rate can be dispersed to create more interfacial area and turbulence. This is accomplished by selecting an appropriate material of construction with the desired wetting characteristics. In general, aqueous phases wet metal surfaces and organic phases wet non-metallic surfaces. Change in flows and physical properties along the length of extractor should also be considered. Choosing a continuous phase is generally not available in batch processes, as the larger liquid phase usually becomes the continuous phase.
Conclusions
As we have seen in the previous sections, there are a number of factors affecting extraction performance. Laboratory and pilot plant testing using actual feed and solvent help immeasurably in optimization. The study could often be an iterative cycle involving laboratory testing followed by process simulation and design. In most industrial extractors, there is usually a good scope for optimizing solvent usage and energy consumption.
[attachment=4404:extrac29.gif]References
- Robbins, Chem. Eng. Prog., 76(10), 58-61 (1980).
- Cusack, R.W., & Glatz, D., et al, "A Fresh Look at Liquid-Liquid Extraction", Chemical Engineering, February, March & April 1991.
1 Comments
good sharing, mr madhavan!