|
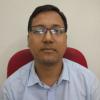
Need Set Pressure To In/out-Breathing,emergency Relief Of Storage Tank
#1
Posted 20 September 2012 - 11:15 AM
We are in a process of changing a floating roof tank to floating cum fixed used for storage of hexane(food grade). Tank dia:20m H: 9.6 m. The tank will is nitrogen blanketed. I wanted to know what will be the in/out breathing set pressure and relief pressure. Following parameters are known:
Design pressure: full of water with nitrogen blanketing with 50 mm WC.
Vapor pressure of hexane(98% purity at 40 deg cel)) to be 400mbara,
Cut point : 63-70 Deg cel.
I have calculated the flowrates for in/out breathing as per API 2000 but I cant seem to find a way to set the trigger pressure.
Kindly help
#2
Posted 20 September 2012 - 01:43 PM
The standard cannot do this for you. Each situation is unique.
#3
Posted 23 September 2012 - 03:47 AM
As Paul well explained don't worry about the set point value determination; it should be set such that just there would be no interaction between adjacent devices and be within MAWP and MAWV of the tank. In this way be noted that saving the blanketing gas consumption due to lowering the set point is very small.
Fallah
#4
Posted 23 September 2012 - 03:41 PM
#5
Posted 26 September 2012 - 06:03 AM
Typical case-
Tank design pressure = say 300 mmWCg
ERV (fire case,hatch) opens above 200 mmWCg 300/200 ~ 50% margin
Breath out valve opens above 150 mmWCg 200/150 ~ 33% margin
N2 Blanketing valve closes above 100 mmWCg 150/100 50% margin -- maximize this margin to minimize inert into tank
N2 Blanketing valve opens below 100 mmWCg
Breath in opens at & below -25 mmWCg
Tank design pressure (negative side) -50 mm
#6
Posted 26 September 2012 - 07:44 AM
I normally prefer @ 25 to 50% margin between each setting.
DB Shah,
It should be noted that the margin between each two settings should be included both of dead band margin (to prevent interacting) and operating margin (overpressure, blowdown, lock-up pressure, droop pressure,....). Hence, there isn't a prespecified range by which the margins between settings are to be adjusted and each case should be investigared as per its own design information. As a sample, you consider tank design pressure/vacuum equal to 50 mmWCg/-5mmWCg and try to set all devices between these two values.
Fallah
Edited by fallah, 26 September 2012 - 08:02 AM.
#7
Posted 26 September 2012 - 06:09 PM
#8
Posted 27 September 2012 - 02:07 AM
#9
Posted 19 February 2013 - 10:01 AM
Dear Sirs,
Your recommendations were also somehow useful to us but we have a
problem similar to Mr. Phukan's problem.
An Old Fixed Cone Roof Tank filling with LPG and blanketing gas. The Diameter
is 20m and 15 Height. The Tank is over 30 years old and its PVSV is out of use.
I'm responsible to determine the exact set point of Vacuum/Positive
Pressure to buy a New one. For that, we have tried to obtain the MAWP of the
Tank during filling or suddenly draining the Tank. The obtained values are
mentioned below:
Vacuum: -0.03 psig
Positive Pressure: +0.35 psig
At these values, the Tank started to have dangerous vibrations. Could you
please let me know the way to use these values to pass the responsibility? Or is
there any relation between these values and the set point of the PVSV?
Thanks
Ghaffari
#10
Posted 19 February 2013 - 01:37 PM
Sir, your test reveals some significant structural issues with the tank at relatively low pressures. Certainly you could not operate anywhere near these points. If I were asked to place a system on such a tank that results in the tank operating at pressure and vacuum, I would refuse.
Paul
#11
Posted 20 February 2013 - 01:41 AM
Hi,
As Paul rightly stated, not only the tank's PVSV is out of use but also appears the tank itself should be put aside...
#12
Posted 22 February 2013 - 01:08 PM
Hi,
Thanks for your help. I'll try to have positive effects at uor sessions to repaire/ modify or better refusing the Tanks. I hope I could do that as well as possible.
#13
Posted 12 March 2013 - 03:01 PM
Following the line of PROINWV and Mr Shah, I suggest that you have a vessel design engineer physically inspect the tank and re-evaluate the rating of the vessel. This is your starting point. Have the vessel engineer then specify the % over pressure that would be allowed for relief calculations. Depending on the design, you may be allowed anywhere from 0% overpressure to 10% overpressure in the relief calculation.
Go to a press / vac vent supplier and find the performance curves for your situation and design basis. Assuming 0% overpressure is allowed, what pressue would you have to set the pressure side in order to relieve your calculated relief rate such that the pressure never exceeds the pressure rating. Do the same thing on the vacuum side (using the in-flow vapor rate). Once you have these parameters, you can talk to an instrument engineer to determine if there is suffient spread between the pressures to provide pad gas control (including some dead band)--you could have a difficult time in this application
Similar Topics
Is Emergency Venting Required For Polyethylene Storage Tank In Fire ScStarted by Guest_chem55_* , Yesterday, 03:06 PM |
|
![]() |
||
![]() Relief Path To Be Considered For Inlet Pressure Drop CalculationStarted by Guest_Ascanio E._* , 09 Jul 2025 |
|
![]() |
||
![]() Free Vent For Api 650 Tank - Bug Screen / Bird Screen RequirementStarted by Guest_Cabbarbeybaba_* , 03 Jul 2025 |
|
![]() |
||
![]() Negative Pressure Discharge / Negative At High PointStarted by Guest_felderosfelder101021_* , 05 Jul 2025 |
|
![]() |
||
![]() Rupture Disc Failure Well Below Max PressureStarted by Guest_vaibhav02_* , 02 Jul 2025 |
|
![]() |