|
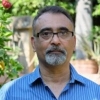
Conservatism In Chemical Process Design
#1
Posted 06 November 2008 - 08:41 AM
This is a topic I have been having in mind for a very long time and finally I felt that this needs discussion in an open forum and what better place than "Cheresources".
When designers say that their design is conservative, they normally imply that their design can cater for duties/functions beyond the normal parameters defined for the function/duties of that particular piece of equipment or for that matter the whole unit or plant. But what most designers forget that extra performance costs money.
In these modern times of budget crunches and cost reductions how much is a conservative design warranted. I would like to give a few examples of so called conservative design which may really not be warranted:
a) Putting a margin on flow rates for liquid/gas transport devices (pumps/compressors) over and above the rated capacity as defined and agreed per the mass balance of the equipment/unit/plant. This has a major impact on both CAPEX and OPEX.
b)Over specifying safety devices such as relief valves, emergency shutdown devices etc. without any reasonable logic such as life cycle cost of the equipment/plant/unit.
c) Using exotic metallurgy for MOC of equipments/devices again without evaluating the life cycle cost of the equipment.
d) Overspecifying fouling factors or giving unreasonable design margins on surface area of heat exchange equipment.
e) Using extremely conservative norms for piping and pipeline velocities without proper evaluation of factors such as noise, surge, vibrations, erosion etc. Many veteran designers will be shocked to see the kind of velocities mentioned in "Norsok Standard P-001 Rev. 5" for liquid lines.
These are just a few examples. In these changing times designers need to shed their old inhibitions and look for optimized designs. The concept of "value engineering" is getting more and more important by the day. When large engineering companies take up "Lumpsum Turnkey" (LSTK) jobs the concept of optimized design has to be ingrained in the psyche of the engineering personnel, simply for the reason that every dollar saved is profit for the company as well as avoiding time overruns and wasteful expenditure on oversized equipment/plant.
The introspection needs to be greater for design professionals and hopefully we will see optimized designs and optimized plant performances in the near future.
Would appreciate comments from stalwarts like Art, Zauberberg, Joe, Guido and others.
Regards,
Ankur.
#2
Posted 06 November 2008 - 05:39 PM
I will try to give you some opinions even I am not on your preferred list. I will consider myself in the "others" category.
I am working for an EPC company, and I am seeing a deeper and deeper implication of the client (operator) in the process of establishing the performance benchmarks and the design margins of a project. Some of them developed their own standards and they demand to be followed in every aspect by any contractor working with them. And I think that's right because it's client's money, so he has to be involved. That is as long as no recognized standard is broken in the process, of course. More or less conservative design in my current understanding means to meet the client's expectations.
Another trend I've noticed, maybe some knew it for a long time especially in oil&gas. If the plant was designed for a certain capacity, say 100%, the operator is running it at 115-120%, based on a certain design margin the designer supposedly considered. Right? Wrong? I don't know. Maybe as long as nobody get's hurt it's all right.
Recently somebody came to us asking to reevaluate their existing flare header. They were planning an expansion, something like doubling the existing capacity. The purpose of all endeavor? They were planning to use the same header for all the expanded plant, and avoid installing one additional. For sure that header had some design margin incorporated, but 100%? How about the age? Right? Wrong?
You mentioned Value Engineering as something gaining importance in the design process. You are right, it is a fashionable subject. But is it really providing value for the buck you spend? I've seen a lot of strange things happening on that subject, let's call them strange, not more than that. A lot of people think in very good terms at value engineering, I am not fully convinced of it's real value. There are some people that prefer to call it as it is: cost cut exercise.
You mentioned LSTK projects. Yes, more and more clients want this kind of project. But their real reasons have nothing to do with design or execution quality or any technical aspect. The real driving forces are purely financial. The result? As long as the contractual terms are met everything is fine, and nothing matters. Following my latest experience, I will always say: You want quality? Go with reimbursable type of project. You want something quick and dirty? Go LSTK.
Regards
#3
Posted 06 November 2008 - 06:15 PM
I made similar argument to one of the senior process engineer in my company located in Houston, TX.
According to him, most of the design is done based on the sound engineering judgement. To make sure that design will work in all specified normal as well as abnormal condition, he consider conservative approach. Nowadays there are some green engineers trying to optimize the system, end up making poor engineering judgement. Sometimes this type of optimized design pose significant risk to the project.
I am right now working with an optimization project for Shell. They have done conceptual design of the their facility and asked us to optimize their concept. After the thorough study, we found that there is a significant project risk in their conceptual design. The concept we have proposed costs higher than their original design.
Anyway, I would like to know the views from other forum members as well.
#4
Posted 07 November 2008 - 05:15 AM
Dear Ankur Hello/Good Afternoon,
First of all two clarifications
1) I am not among the stalwarts and we do honour,respect and value their opinion; may be I get qualified for 'others' category.
2) I consider your question as very interesting/inviting responses.
Further more I envisage your whole query concept to be a sort of 'Constrained Optimization' case encountered in LP and other areas .i.e. there have be certain safety guidelines codes& standards to limit/over-ride the extent of economical capital minimization efforts; since this has and will result into catastrophic failure even endangering human lives and other highly valued assets even hurting the goodwill and inviting huge penalties/litigation costs.
However your point of excessive costs are already being checked/reviewed presently in many ways by the designers/operators or End-user/ Owners through their participation and involvement at many of the phases of projects.
As indicated by our forum colleagues Andrei & suren both the concerns in a way.
This query in itself is going to be a huge discussion and others inputs are ancipitated to reply you in much better ways.
Best regards
Qalander
#5
Posted 09 November 2008 - 05:07 AM
Dear Qalander,
Andrei and Suren have been very clear in their expression and I could understand each and every word and sentence.
However, I have a real difficulty in understanding what you have written. Is your language from the Victorian era or is it from another planet? My understanding of the english language is somewhat limited as regards to adjectives and superlatives.
Regards,
Ankur.
#6
Posted 10 November 2008 - 01:25 AM
Dear ankur,
May I merely apologise on the language account / my poor communications.
Regards
Qalander
#7
Posted 10 November 2008 - 10:33 PM
I was perfectly able to understand what was written by " others". I must say, these were very valuable inputs.
Optimisation problem is nothing new to veterans and " others". I have carried out a simple optimisation excercise based on Example 13.1 of the book " Optimisation of Chemical Processes" Second Edition by Edgar, Himmelblau and Lasdon, and inhouse cost figures.
The results of the excercise match "conventional" wisdom for line size selection.
Regards
Rajiv Narang
#8
Posted 10 November 2008 - 11:38 PM
Thanks very much for this helping info; actually what I intended to communicate was as is the case of graphical representation of constrained optimisation has defining limits for otherwise normal optimisation through linear programming.
One gets new optimised solution for the same problem
This will be the case for the query put forward
to reach a compromise between economical dictating parameters conditioned(constrained through safety related limits posed)
Hope this explains what was the communication'in-brief'
Regards
Qalander
#9
Posted 11 November 2008 - 01:58 AM
Dear Rajiv,
First of all if you propose to read carefully, the subject is regards conservative approaches in design. The examples mentioned for conservative design were generic in nature and many international companies do not follow what is written in chemical engineering textbooks such as "Himmelblau". They generate their own standards which not so surprisingly to me are sometimes very contradictory to standard textbooks and international standards. For them, running any operations is a combination of all factors including safety, environment and not to forget revenue and profits.
Let me be more specific. API RP 14E (ISO 13703) mentions the erosional velocity limit for two-phase gas/liquid flow with the equation:
Ve = C / Sqrt(Rhomixture)
where C is an empirical constant
and Rhomixture is the gas/liquid mixture density
The value of C as proposed by API 14E is in the range of 100 for mixtures with solids and 150-200 if the gas-liquid mixture is solids-free. Many operatinng companies who have augmented their production of oil/gas production from existing wells through their main transport pipeline find that they cannot increase their production if they stick to the API 14E norms, which have been proven overly conservative. Many argue that the erosional velocity limits are much higher than what is proposed by API 14E. I know for sure that a middle east O&G company does not accept the API 14E norms since they rejected the API 14E norms when it was proposed by me for their company standard. I was asked to refer "BP Erosion Guidelines" to get a true picture. What Iwas surprised was that C values of higher than 300 could be used when the fluid was solids free. What better example of conservatism in design!
Another example was the time when I was in operations. The main plant was having a name plate capacity of 90 TPD. However the excessive design margin could push the plant to 115 TPD without any impact on quality. Our downstream processing units were only geared up for 90 TPD plus 10%.
Our MD had questioned us that we asked for a nameplate capacity of 90 TPD and with some excess in design (10%) we get 100 TPD. How is that we are able to produce 115 TPD? Did we end up paying more to the licensor/designer for what we didn't ask for? Was it possible to reduce the CAPEX /OPEX had we gone for a 75 TPD plant with the same in-built design margin? Tough questions to answer gentlemen! . It was his money that he had put up for setting up the plant and his licensor/designer/consultant ended up giving him a "Sports Car" when he just wanted a "Sedan".
Sometimes when we work as professionals we simply work by rote and employ the "cut-paste" approach to design, when it is probably required have an "out-of-the-box" thinking, being innovative and resourceful. This is what in my terms is mindless conservatism.
Regards,
Ankur.
#10
Posted 11 November 2008 - 02:24 AM
Dear ankur,
Although the reply addressed to Rajiv, May I dare adding few words
1) your conceptual approach is not in-correct as such
2)This is the very basic job of the design and consultancy professionals to take decision and accept challenges/finding the way-out 'on case to case basis' alone.
3)But I tend to diagree that general conesnsus practice is possible i.e. a sort of emperical rule of thumb
Hope I am clearer in comminication for now.
Best regards
Qalander
#11
Posted 12 November 2008 - 02:34 PM
I think it starts to be more and more clear from the discussions that the designer has to take a responsible decision when he/she recommends a certain equipment/pipe size. And that cannot be accomplished without considering all the aspects. Since there are good and not so good people, there will be good and not so good designs coming out of their hands.
Following some standards in our engineering activity is giving us some common ground of discussion and is ensuring that everybody is using more or less same language. But that shouldn't prevent us to think and come up with solutions that are better than before but not necessary according to the letter of the standard, that’s how the progress works. As a matter of fact we should all recognize that the greatest human discoveries were defying all the standards at their time.
Speaking of API RP14E, a good example of errosional velocity use is the design of the line between vacuum fire heater and vacuum tower. It is known that there is a huge amount of flashing along the line and a bad decision can affect both operating ability and capital cost. It is known that well known operators, like Shell, have their own designs for those lines, that not necessary follow API RP14.
What you are saying in the end of your last post is actually confirming what I was saying in my first posting regarding the way some operators are running the plants. One thing you should be more specific: what kind of days you are referring at when you are giving the capacities: operating days or calendar days. I spent the first third of my career in operations, and I remember that I was doing exactly the same thing: running the plant above the nameplate capacity.
Let me ask something: what good is to you if you run the plant at 120% design capacity for two months and you bring it down on third for unscheduled maintenance? What good is to you if you run the plant at 120% capacity for two years and you bring it down in the third because your market is saturated or you don't have the required raw materials?
If a designer guarantees a certain capacity that has to be met at all times during the plant life, and not only during some limited time intervals. To do that he/she has to take responsible decisions, the market will judge how good were his/her decisions.
Regards
.
#12
Posted 13 November 2008 - 01:12 AM
Best regards
Qalander
#13
Posted 13 November 2008 - 11:55 AM
More seriously though, equipment has margins. If you buy a pump that supposedly develops 100 feet or meters of head at your design flowrate, that is sort of a "reasonable estimate" of its performance. The actual pump sitting on the ground may develop 103 feet or 97. Look over your pump specs or the vendor's offering and you should see the details. Piping that can carry your product to a tank located half a mile away while needing only 20 psid to do so will deteriorate and years down the road may need an extra 10% or 15% pressure differential to maintain the delivery rate. In practice, I would "overdesign" my system by that 10-15%. I would also NEVER buy a new pump with the maximum size impeller installed. It should do the job, but if the construction crew did a minor re-routing of the piping in the field and the pump I specified is not up to the job, I'd much rather be talking to my client about them needing a new impeller rather than a new pump and motor. Call it wasteful overdesign if you will, but I will continue to think of it as prudent foresight.
An interesting side note - For decades one hydrostatically tested pressure vessels at 150% of their MAWP rating. Recently, however, the rules changed and pressure testing now is done at 130% of MAWP. I think this means that we've increased our collective knowledge as to how to design pressure vessels, and, as a result, there is less "overdesign" in modern designs.
Conclusion: Knowledge = Less Overdesign?
#14
Posted 13 November 2008 - 12:30 PM
I am impressed. You have really summed it up nicely.
I was eagerly awaiting a response from senior members like you and Art to give some insight on the subject based on your long and illustrious career and the rich experience you have gathered in the rough and tumble of engineering design.
I hope you will keep on sharing your views on the forum and enrich the members on the forum.
Regards,
Ankur.
#15
Posted 13 November 2008 - 07:07 PM
First, thanks for your invitation to comment...
Conservatism...simple term but i really have difficulties in ...
Just wants to bring up a few points with my limited knowledge...
Operator quality - is the one who operate the plant. How much a plant can produce and how safe is a plant is very subject to how they operate and manage the plant. Education, awareness, quality of operator is one of the key factor.
Organization Culture i.e. no-blame culture - is also affecting the decision and performance of the operator and hence the plant performance.
Organization approach / principle - Some organization tends to explore new technologies in order to put their organization in front of others. Some organization would tends to see some success stories before a "new" technology is implemented.
Risk - How much risk that a project can take can affect the conservative level
Knowledge & Experiences - As Doug mentioned, it significantly affect the conservative level.
I do think above affecting the conservatism in Design... but how much it affect and how to quantify and work out a good "margin" is really outside my knowledge...
The more you know about a system, in many event it helps to reduce "margin". However, in some event, you may increase the "margin" as you knew that the "margin" that you have put in earlier design was "under-margin"...

#16
Posted 14 November 2008 - 06:54 AM
Splendid Responses ideed! Dear Doug and Joe,
This as anticipated is proving very useful positive responding thread.
Best Regards
Qalander
Similar Topics
Chemical Engineering ResourcesStarted by Guest_Pilesar_* , 24 Apr 2025 |
|
![]() |
||
![]() Scrubber DesignStarted by Guest_nasss_* , 07 Aug 2024 |
|
![]() |
||
Refinery Lpg Deethanizer Column DesignStarted by Guest_Ilyes_* , 15 Feb 2025 |
|
![]() |
||
Alkaline Electrolytic Cell/stack Sizing/design For H2 ProductionStarted by Guest_BRS09_* , 13 Mar 2025 |
|
![]() |
||
![]() Heat Exchanger Network DesignStarted by Guest_Kakashi-01_* , 21 Feb 2025 |
|
![]() |