|
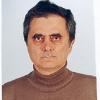
Npsha For Fuel Oil Centrifugal Pump
#1
Posted 31 December 2009 - 02:19 PM
Operating temperature : t=60 0C
sg (at 60 0 C) : 0.89 - 0.96
max viscosity (at 60 0 C) : 150 cSt
max vapor pressure of HC (at 60 0 C) : 0.004 kgf/cm2 abs (HC=hydrocarbon)
The pump took suction from a big fuel oil atmospheric tank (heated under temperature control to maintain t=60 0C).
The fuel oil vapor pressure Ps (to be considered in the calculation of NPSHa) was an issue.
According to view No 1, there is always some water in fuel oil. Specification usually calls for 0.1% water (w/w) in fuel oil. Water content can be much more in case of ship unloading (possible case for the mentioned tank). Since water and HCs are practically immiscible, Ps is the sum of vapor pressure for HC and water. That is Ps=0.004+0.203=0.207 kgf/cm2 abs, irrespectively of the water content in fuel oil.
According to view No 2, any water content in fuel oil will settle down and go away through drains, so Ps=0.004 kgf/cm2 abs. No need to consider water content in the fuel oil pumped. Some older pump data sheets seemed to support this view.
The issue had not much practical significance then, since design was preliminary and mainly for cost estimation. But advise / opinions would be useful. Which is right, view No 1 or view No 2?
I think the question can be extended to white fuels, since all of them (except aviation fuels) can contain little water, practically immiscible to HCs. Of course it is not so important (lower t, higher vapor pressure of HC).
Hoping this question is not a chore to members in the new year - best season greetings!!!
Note: any more clarifications welcomed.
#2
Posted 04 January 2010 - 04:38 PM
I would say that the vapor pressure to use is the vapor pressure of the fluid that is actually moving through the pump. So you should consider any water that may be DISSOLVED in the fuel oil, but you should not add multiple independent vapor pressures just because there is a water phase beneath the fuel oil phase. I'm guessing that this is pretty much View #2, so I'd say that I support that view. However, if you can be drawing slugs of 60C water into your pump, then you should be using its vapor pressure in your NPSH calcs. I'd suggest that you should NOT be drawing such slugs of water into your pump and should design and operate your system in such a way as to avoid this problem.
#3
Posted 06 January 2010 - 06:02 PM
Djack77494, sincere thanks for your thoughts. Potential arguments for the other View # 1 (as developed at that time) is presented for further consideration.I would say that the vapor pressure to use is the vapor pressure of the fluid that is actually moving through the pump. So you should consider any water that may be DISSOLVED in the fuel oil, but you should not add multiple independent vapor pressures just because there is a water phase beneath the fuel oil phase. I'm guessing that this is pretty much View #2, so I'd say that I support that view. However, if you can be drawing slugs of 60C water into your pump, then you should be using its vapor pressure in your NPSH calcs. I'd suggest that you should NOT be drawing such slugs of water into your pump and should design and operate your system in such a way as to avoid this problem.
(a) Once a professor advised on the total vapor pressure of two stagnant immiscible liquids of different density (one totally beneath the other) : sum of their vapor pressures, as if each of them were pure substance; for the heavier liquid will find a way to have some free area on the surface of lighter liquid, according to thermodynamics (I did not understand the relation to thermo).
On the other hand a book of physical chemistry supports sum of vapor pressures in this case, but on the condition of strong mechanical agitation.
I have not found a clear answer so far in case of stagnant (i.e. still) liquids. Advice would be welcomed.
(β) Irrespectively of the above, it is quite probable that water is dispersed into the fuel oil as droplets (I have heard even of emulsions). Fuel oil and water have densities close to each other, so settling time of water would be quite long. And pumping could occur during settling, transferring this (say) “dispersion” to the pump inlet, where there is mixing (equivalent to agitation) in addition. This “dispersion” is the fluid actually moving through the pump and supports View # 1 . Such a status may be rather common.
Edited by kkala, 06 January 2010 - 06:06 PM.
#4
Posted 06 January 2010 - 06:13 PM
#5
Posted 21 January 2010 - 08:57 AM
And a SG of 0.9 - 0.96 for FO appears to be out of the way.
In my experience with centrif pumps, what is of concern is the water % and viscosity. If water % is high and is not adequately drained off the tank, the slugs of water (SG=1) amidst the regular stream of FO (of SG 0.6-0.7) causes sudden spikes in pump vibration & motor amps.
I've handled FOs, whose viscosity used to be 200 cSt at 60C and 900 cSt at 40C. So, high motor amps and high pump vibration caused by the viscous drag have been an issue, but never VP. Depending on the discharge nozzle size of centrifugal pumps, the max viscosity they canbe safely subjected to is available in the form of nomographs.
#6
Posted 26 January 2010 - 02:51 AM
Dears akslzf& djack Hello/Good Afternoon,First of all, for hydrocarbons like FO, VP is negligible and therefore not a concern at all for NPSHA calculation, except in the case of low static head, high frictional loss..., whether it is for recip or centrif pumps.
And a SG of 0.9 - 0.96 for FO appears to be out of the way.
In my experience with centrif pumps, what is of concern is the water % and viscosity. If water % is high and is not adequately drained off the tank, the slugs of water (SG=1) amidst the regular stream of FO (of SG 0.6-0.7) causes sudden spikes in pump vibration & motor amps.
I've handled FOs, whose viscosity used to be 200 cSt at 60C and 900 cSt at 40C. So, high motor amps and high pump vibration caused by the viscous drag have been an issue, but never VP. Depending on the discharge nozzle size of centrifugal pumps, the max viscosity they canbe safely subjected to is available in the form of nomographs.
Both of you have described the issue very correctly and I second you people.
My experience with high viscosity F Oil has been mostly similar to what explained by 'akslzf'in the preceding post.
However it is pertinent to share here
1)My experience and observation for fairly large externally insulated employing top free vent vertical steel storage (API 650 design)tanks equipped with bed heating coils is that if the pocketed water layer is covered by a very huge level bulk of heavy fuel oil and the storage temperatures of both liquids are around 60 Celsius or so it hardly matters to have real effect whatsoever on the centrifugal pump's operation.But viscosity&point pumping temperatures do affect the Electric drive's load variations.
2)If the F Oil covering layer is very thin and stored liquids(F Oil& water layers)temperature rises beyond 80 Celsius conditions do effect pumping efficiency since some degree of miscibility is affected.(we have to ensure water layer removal through regular draining out from usually provided bottom sumps to ensure safe system)
3)God forbids if the system is not attended/maintained properly and excessive unchecked heating of(pocketed)water layer prevails;then consequences may not only be adverse for pump's efficiency but could also lead to even worst disasterorous scenario's involving mechanical integrity risk for storage tank system.
Since spontaneous bulk vaporisation risk of underneath water layer approaching its boiling point can not be ruled out.I witnessed something similar making the top roof seam (Roof/Shell single fillet weld) yielding to such stresses.
Hope this in some way proves helpful!
3)
#7
Posted 15 February 2010 - 08:03 AM
A. Remarks
A1. There are fuel oils of sg close to 1.0, even though ASTM D 396 specification reports density only for fuels No 1 & 2. E.g. sg of No 5 heavy fuel is 0.910 - 1.061, of No 6 fuel 0.934 - 1.064 (Perry, 7th ed., Chap 27 - fuels, Fig 27-2 viscosity, boiling range and gravity relationships for petroleum fuels). My original question refers to these heavy fuel oils, often burnt in refinery boilers.
A2. Hydrocarbon vapor pressure can be negligible, so water vapor pressure can have significant contribution to NPSHa calculation of a fuel oil centrifugal pump; unless there is complete separation of water from hydrocarbon liquid. Heavy fuel oils can be heated up to about 93 0C, not higher, because of the risk of boil over (Qalander seems to have witnessed it). Over here a whole tank roof had gone away, as informed.
A3. Problems (beside the reported) of water chunks in fuel oil also concern its introduction to Vacuum Distillation tower, "upset" by fast vaporized water. Certainly the water "chunks" must be removed by settling and drain. The question is whether remaining fuel oil in the tank (after drains) can be quite free of water.
A5. Clarification by djack77494 (6th Jan 2010), on the total vapor pressure of an immiscible hydrocarbon - water mixture, settles down a long query of mine. Agitation can merely accelerate the equilibrium state, where total vapor pressure is the sum of hydrocarbon and water vapor pressure.
B. Main question.
My conclusion is that heavy fuel oil should be considered mixed with water to form an immiscible mixture, even after settling / drain in tanks, unless there are specific indications for the opposite (ie no water in it). This is based on the following.
B1. Seen specifications for fuel oils report not less than 0.1% bw water. Sediment and water (BSW) per ASTM D 396 is specified as 2% bv for fuel No 6 (1% for No 5). Min BSW = 0.2% bv (1). Not all BSW settles to the bottom, some stays in suspension. Most of BSW forms a black or brown muck, mixed with water, found on tank bottoms (1). Local tank suctions are quite close to bottoms.
B2. Solubility of H2O in oils is approx 0.3 % on molar basis at 60 0C (W. L. Nelson, Petroleum refinery engineering, McGraw-Hill 1958, Chapter 5, Fig 5-24, Approx solubilities of water in oil..), that is about 0.0135 % bw (assuming MW=400 for fuel oil). This in combination with B1 indicates free water content in fuel oil, even if it cannot be seen.
B3. Settling velocity can be very slow for water particles of (say) 0.005 in at 60 oC. For viscosity of 115 cSt and sg=0.97, settling time was estimated at 118 hr/m (to descent 1 m of height); 310 hr/m for 200cSt and sg=0.98. Water droplet in emulsion is assumed to have such a size, or smaller.
B4. Even if fuel oil is found water free at a time, water content can be soon be detected due to: leaking steam coil, fall in, loose caps or manholes, excessive heating (causing sediment and H2O)(1). I have heard that even moisture from atmosphere can be absorbed.
B5. So fuel oil can be free of immiscible water vapor pressure (that is water content be low enough for it) only under special conditions. E.g. if it has been recently heated above 120 oC by flue gas coil (water must evaporate, if tank height not too high), or probably after treatment in centrifugal separators to feed reciprocating engines (like Alcap type, to separate sediment).
Therefore fuel oil pump NPSHa calculation should take water into account, adding its vapor pressure (at max operating temperature) to the hydrocarbon vapor pressure. Exception can be in specific cases, ascertaining that fuel oil is actually free of water.
Any comment on the above opinion would be gladly welcomed.
#8
Posted 15 February 2010 - 01:07 PM
Few years ago we had to specify a centrifugal pump transferring fuel oil of following characteristics.
Operating temperature : t=60 0C
sg (at 60 0 C) : 0.89 - 0.96
max viscosity (at 60 0 C) : 150 cSt
max vapor pressure of HC (at 60 0 C) : 0.004 kgf/cm2 abs (HC=hydrocarbon)
The pump took suction from a big fuel oil atmospheric tank (heated under temperature control to maintain t=60 0C).
The fuel oil vapor pressure Ps (to be considered in the calculation of NPSHa) was an issue.
According to view No 1, there is always some water in fuel oil. Specification usually calls for 0.1% water (w/w) in fuel oil. Water content can be much more in case of ship unloading (possible case for the mentioned tank). Since water and HCs are practically immiscible, Ps is the sum of vapor pressure for HC and water. That is Ps=0.004+0.203=0.207 kgf/cm2 abs, irrespectively of the water content in fuel oil.
According to view No 2, any water content in fuel oil will settle down and go away through drains, so Ps=0.004 kgf/cm2 abs. No need to consider water content in the fuel oil pumped. Some older pump data sheets seemed to support this view.
The issue had not much practical significance then, since design was preliminary and mainly for cost estimation. But advise / opinions would be useful. Which is right, view No 1 or view No 2?
I think the question can be extended to white fuels, since all of them (except aviation fuels) can contain little water, practically immiscible to HCs. Of course it is not so important (lower t, higher vapor pressure of HC).
Hoping this question is not a chore to members in the new year - best season greetings!!!
Note: any more clarifications welcomed.
Dear kkala, Hello/Good Night, I really admire and appreciate your thorough summarization after reviewing deeply these post(s);
I would like you to focus on three points as regards settling out and draining out of water;
1. Storage temperature's gradual increase with a target of 60~70 Celsius to thin-out the viscous pocketing enclave and helping water droplets Coalesces
2. Providing sufficient residence time in the storage tank to ensure separation of layers in aqueous lower layer and Hydrocarbon upper layer.
3. Careful water drain-out in patient way ensuring complete removal as far as possible; such that the tank bottom heal is almost having Nil free water.
After this all the hazards associated/anticipated to affect adversely the NPSH through water's vapor pressure or water pocketed/mixed with Fuel Oil entering the centrifugal pump suction are almost nullified or minimized to best tolerable conditions.<BR style="mso-special-character: line-break"><BR style="mso-special-character: line-break">
Hope this helps/shows some way forward.<BR style="mso-special-character: line-break"><BR style="mso-special-character: line-break">
Also presumably if Doug's and mine post points were found valid, then in all fairness some positive points in rating were deserved by both.
#9
Posted 22 February 2010 - 11:44 PM
Hopefully you might have read through email reply my explanation of the issue.
Please feel free to contact I will try to further explain what I have;not only envisaged,but also got practical hands-on field evidence
ascertaining that the concept was very much closed to ground realities faced/ encountered.
#10
Posted 26 February 2010 - 02:43 PM


After communication with Qalander (Chem), whom I sincerely thank for the help and interest, conclusions on the issue are revised as follows:Hopefully you might have read through email reply my explanation of the issue.
Please feel free to contact I will try to further explain what I have;not only envisaged,but also got practical hands-on field evidence
ascertaining that the concept was very much closed to ground realities faced/ encountered.
A1. Vapors of a liquid exerting a pressure become "credible" for consideration as and when its vapors are in contact with its surface, an equilibrium of liquid molecules escaping into vapor space & vapors re-condensing into liquid takes place in an almost closed system.
In the particular case of
hydrocarbon mixtures (defined in the thread as fuel oil)
forming a thick layer as main stored material
on top of any aqueous water layer (not coming almost ever in contact with storage tank vapor space),
then
no case of any water vaporization/ re-condensation seems "credible" for consideration, since upper layer keeps the aqueous layer sealed off throughout usual storage.
A2. However exception to the above could be in some cases, e.g.
a) when the tank is near emptying out and top layer is so much reduced to have aqueous layer in contact with vapor space
β) when temperature of water layer is highly increased to push out top oily layer and become in contact with vapor space
c) or probably when oil& water get emulsified for any reason.
A3. This is the idea assumed as practically happening in real storage tanks and accordingly vapor pressure from any water layer can not be worth considering when very thick Oil Blanket layer keeps segregated the water from contacting the vapor space.
B1. Above is assumed to be generally true for stored fuel oil, and could explain why found fuel oil pump data sheets do not seem to consider water vapor pressure. Hydrostatic pressure of liquid hydrocarbon can make seal of water stronger.
B2. It is noted that equilibrium theory may support that water in hydrocarbon liquid will find a way to make a free surface (i.e. in contact with tank vapor space), so total vapor pressure is sum of water and hydrocarbon vapor pressure. But it does not specify time needed for this and size of water free surface. That is why info detected on total vapor pressure of a mixture of immiscible liquids does not seem clear. Equilibrium can be very late, unless the immiscible phases are agitated. In case of agitation, water is not "covered" by the hydrocarbon.
B3. It is also pointed out that "fuel oil manual" by P F Smith gives the impression that little "free" (not diluted into hydrocarbons) water exists in fuel oil at any case; this can be also considered as "covered", or be somehow combined with sediment or muck.
C1. Nevertheless, there are cases where water vapor pressure should be considered, since water is not totally "covered", e.g.
a) when fuel oil is so heavy that its specific gravity is around unity; then the two liquids cannot be separated by gravity.
β) when operating conditions do not allow time for water settling & drain so that both hydrocarbons & water go to the pump suction (e.g. case of slops in thread of hydrocarbons & oil, 13 Feb 10)
c) probably when water is emulsified, but interfacial tension complicates the issue. Emulsions tend to break down by heating, while presure within water droplet can be quite high (as in surface tension).
C2. I wish I had worked in a big factory, to try to measure something experimentally. Once a situation as the attached sketch was faced. Fuel oil hot return from boilers (133 oC) was directed to pump suction. In low boiler loads pump suction would approach 133 oC. Pump would not operate, if water vapor pressure had a real contribution. Then design changed to simple fuel oil tranfer to a day tank near boilers, by simple chance. So issue was bypassed, but query remained.
C3. Hoping the issue will be covered more completely and rightly by other contributions, I apologize for the long messages (it happens with uncertain matters).
Edited by kkala, 26 February 2010 - 02:55 PM.
#11
Posted 27 February 2010 - 05:30 AM
boilers.bmp 1.96MB 26 downloads
boilers.bmp 1.96MB 26 downloads
After communication with Qalander (Chem), whom I sincerely thank for the help and interest, conclusions on the issue are revised as follows:
Hopefully you might have read through email reply my explanation of the issue.
Please feel free to contact I will try to further explain what I have;not only envisaged,but also got practical hands-on field evidence
ascertaining that the concept was very much closed to ground realities faced/ encountered.
A1. Vapors of a liquid exerting a pressure become "credible" for consideration as and when its vapors are in contact with its surface, an equilibrium of liquid molecules escaping into vapor space & vapors re-condensing into liquid takes place in an almost closed system.
In the particular case of
hydrocarbon mixtures (defined in the thread as fuel oil)
forming a thick layer as main stored material
on top of any aqueous water layer (not coming almost ever in contact with storage tank vapor space),
then
no case of any water vaporization/ re-condensation seems "credible" for consideration, since upper layer keeps the aqueous layer sealed off throughout usual storage.
A2. However exception to the above could be in some cases, e.g.
a) when the tank is near emptying out and top layer is so much reduced to have aqueous layer in contact with vapor space
β) when temperature of water layer is highly increased to push out top oily layer and become in contact with vapor space
c) or probably when oil& water get emulsified for any reason.
A3. This is the idea assumed as practically happening in real storage tanks and accordingly vapor pressure from any water layer can not be worth considering when very thick Oil Blanket layer keeps segregated the water from contacting the vapor space.
B1. Above is assumed to be generally true for stored fuel oil, and could explain why found fuel oil pump data sheets do not seem to consider water vapor pressure. Hydrostatic pressure of liquid hydrocarbon can make seal of water stronger.
B2. It is noted that equilibrium theory may support that water in hydrocarbon liquid will find a way to make a free surface (i.e. in contact with tank vapor space), so total vapor pressure is sum of water and hydrocarbon vapor pressure. But it does not specify time needed for this and size of water free surface. That is why info detected on total vapor pressure of a mixture of immiscible liquids does not seem clear. Equilibrium can be very late, unless the immiscible phases are agitated. In case of agitation, water is not "covered" by the hydrocarbon.
B3. It is also pointed out that "fuel oil manual" by P F Smith gives the impression that little "free" (not diluted into hydrocarbons) water exists in fuel oil at any case; this can be also considered as "covered", or be somehow combined with sediment or muck.
C1. Nevertheless, there are cases where water vapor pressure should be considered, since water is not totally "covered", e.g.
a) when fuel oil is so heavy that its specific gravity is around unity; then the two liquids cannot be separated by gravity.
β) when operating conditions do not allow time for water settling & drain so that both hydrocarbons & water go to the pump suction (e.g. case of slops in thread of hydrocarbons & oil, 13 Feb 10)
c) probably when water is emulsified, but interfacial tension complicates the issue. Emulsions tend to break down by heating, while presure within water droplet can be quite high (as in surface tension).
C2. I wish I had worked in a big factory, to try to measure something experimentally. Once a situation as the attached sketch was faced. Fuel oil hot return from boilers (133 oC) was directed to pump suction. In low boiler loads pump suction would approach 133 oC. Pump would not operate, if water vapor pressure had a real contribution. Then design changed to simple fuel oil tranfer to a day tank near boilers, by simple chance. So issue was bypassed, but query remained.
C3. Hoping the issue will be covered more completely and rightly by other contributions, I apologize for the long messages (it happens with uncertain matters).
Dear kkala Hello/Good Afternoon,Thanks for considering the viewpoint.
A minor thing to add,Might have been a part of or missed somehow during our emails exchanged on this topic.I believe it worth mentioning here.
If the Fuel Oil stored with water contents and these contents are agitated or stirred and no settle-out and water drain-out is practicable.with the storage temperatures on the higher side near water boiling point and
the fuel oil sp. gravity very near to water
Then it is envisaged that if this fuel oil with water contents mixture enters the centrifugal pump's suction eye it gets vaporized almost instantaneously resulting into
Vapor locking/cavitation
Extent of such a condition occurring as noticeable as disturbing or highly damaging scenario for the pump depends mainly on water contents %age,pumping temperature.
On further seeing your hand drawn sketch the possibility of agitated contents and finding their way seems most probable if no control on water contents then presumably pump is at Risk of (through erosion and slug flow conditions and possible consequent corrosion.)what was identified above.
Hope that this also gives some food for thought/point to ponder,contributes in showing way forward for problem resolution.
Edited by Qalander (Chem), 01 March 2010 - 02:43 AM.
Similar Topics
Thermal Oil Pump Motors Blew OffStarted by Guest_lizelle_* , Today, 03:47 AM |
|
![]() |
||
Centrifugal Pump In Recycle Mode: Constant Power Consumption But FluctStarted by Guest_Kakka_* , 23 Jan 2025 |
|
![]() |
||
Need Help Understanding Increased Power Consumption In Injection PumpStarted by Guest_Kakka_* , 21 Feb 2025 |
|
![]() |
||
Improving Safety By Re-Routing Priming Vent Line In Centrifugal Pump HStarted by Guest_Srinivas Agastheeswaran_* , 31 Jan 2025 |
|
![]() |
||
![]() Centrifugal PumpsStarted by Guest_panoska_* , 01 Feb 2025 |
|
![]() |