Dear All,
I have an application that I will do the heat transfer calculations and the design the possible heater.
Process fluid is HC+H2
Operating Pressure is 490psia
Operating temperature is 460 degree F to 575 degree F
In the process fluid H2 partial pressure is 130psia
Possible film temperature is 1000 degree F.
I have a pretty good idea what type of fired heater I should design. However, in my spec it is recommended to use steam and air in the certain flows and temperature as a guideline during the catalytic regeneration. (I am assuming this may be a steam -air decoking system. The info on the spec says "Burning with a mixture of steam and air and polish burning with a mixture of steam and air")
My question is why I need to know this flow rates and temperatures for the steam air decoking? The operating temperature is not high that will create coke formation in the heater(like a delay coker process)
So my questions are:
1.Shall I consider the steam-air decoking in my design calculations if the recommended process is the steam -air decoking by means?
2.If I design a vertical cylindrical or a box type heater with nesting coils. Shall create more coke in the process tubes?
3.What process is better for decoking using pigging or using air-steam decoking system?
In advance I thank you very much for your inputs to my post.
Kybele
|
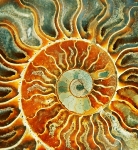
Cataylitic Regeneration
Started by kybele39, Jul 20 2010 10:34 AM
4 replies to this topic
Share this topic:
#1
Posted 20 July 2010 - 10:34 AM
#2
Posted 20 July 2010 - 11:13 AM
From your description it seems that there is a reactor feed heater and the Licensor datasheet mentions Catalyst regeneration case wherein air (low flowrate)is required at some predetermined temperature to burn coke off the catalyst in the downstream reactor. This is not steam air decoking and is simply an extra check case, the duty for such check case would be very low and TMT will not pose a problem.
From your film temperature, i feel that Appropriate coil metallurgy might somewhere around or above P9. These coils have a high design TMTs and decoking ops do not pose any problem. Plants have a recommended flow mass velocity during steam air decoking & these are enough to prevent overheating of tubes. Also firing is low during decoking.
Please check previous references for the particular application (running in your plant or elsewhere) before selecting type of heater. This gives confidence in design.
Pigging is becoming popular nowadays but it requires pigging specialist to come to the refinery and they have their own charges. However, it is quick and efficient.
From your film temperature, i feel that Appropriate coil metallurgy might somewhere around or above P9. These coils have a high design TMTs and decoking ops do not pose any problem. Plants have a recommended flow mass velocity during steam air decoking & these are enough to prevent overheating of tubes. Also firing is low during decoking.
Please check previous references for the particular application (running in your plant or elsewhere) before selecting type of heater. This gives confidence in design.
Pigging is becoming popular nowadays but it requires pigging specialist to come to the refinery and they have their own charges. However, it is quick and efficient.
#3
Posted 20 July 2010 - 12:36 PM
Dear Flame,
Thank you very much for the info, appreciated. Now it makes more sense to me.
However, I am thinking the point of injection is the important and the max.tube metal temperature should be noticed for the injection point of the steam and air, right?
Maybe an enlarged tube size needed to complete the design in the heater. Like towards the radiant outlet.
I also agreed with you to rating the heater for the steam and air feed conditions. But what is the difference between two burning operation :
"burning with a mixture S+A" and "polish burning with a mixture S+A"?
Just one more question====> that is the feed in to heater is not going to be mixed with steam and air mix because this is a different operating case, right? So I have to check the heater behavior for those steam and air flow and the duties against the max tube metal temp.right?
Thanks again.
Kybele
Thank you very much for the info, appreciated. Now it makes more sense to me.
However, I am thinking the point of injection is the important and the max.tube metal temperature should be noticed for the injection point of the steam and air, right?
Maybe an enlarged tube size needed to complete the design in the heater. Like towards the radiant outlet.
I also agreed with you to rating the heater for the steam and air feed conditions. But what is the difference between two burning operation :
"burning with a mixture S+A" and "polish burning with a mixture S+A"?
Just one more question====> that is the feed in to heater is not going to be mixed with steam and air mix because this is a different operating case, right? So I have to check the heater behavior for those steam and air flow and the duties against the max tube metal temp.right?
Thanks again.
Kybele
#4
Posted 21 July 2010 - 08:22 AM
Enlarged tube sizes are in most cases, typical for Vacuum heaters. As per your process fluid description of "HC+H2", and most importantly the operating temperatures and pressures, i am pretty sure that this application is definitely not a vacuum heater and most probably its a reactor feed heater in a hydro processing application. Morever, an enlarged tube size in any applications will just help in limiting the pressure drop.
You are correct. "Burning" or "polish Burning", i think that these cases have nothing to do with steam air decoking. Take it this way, Obtain the thermal properties for these cases and just rate the designed heater for the specified flow rates and terminal conditions. See the results. Results would be normal.
You are correct. "Burning" or "polish Burning", i think that these cases have nothing to do with steam air decoking. Take it this way, Obtain the thermal properties for these cases and just rate the designed heater for the specified flow rates and terminal conditions. See the results. Results would be normal.
#5
Posted 21 July 2010 - 10:01 AM
Dear Flame,
Thank you very much for your response.
Kybele
Thank you very much for your response.
Kybele
Similar Topics
Zeolite Bed RegenerationStarted by Guest_TestTest_UK_* , 28 Jan 2024 |
|
![]() |
||
Adsrober RegenerationStarted by Guest_T_bag_* , 26 Sep 2023 |
|
![]() |
||
Maximum Number Of Regeneration Cycles In Mole SieveStarted by Guest_YouAB_* , 23 Apr 2023 |
|
![]() |
||
Refinery Amine Regeneration UnitStarted by Guest_CHEMSTRONG_* , 16 Jun 2022 |
|
![]() |
||
![]() Tsa Bed Regeneration Heat Energy CalculationStarted by Guest_Bitan729_* , 17 Mar 2022 |
|
![]() |