|
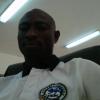
Effect Of Hipps With Prv As Overpressure Protection
Started by asade abiodun, Oct 21 2010 02:02 AM
6 replies to this topic
Share this topic:
#1
Posted 21 October 2010 - 02:02 AM
What effects would HIPPS (High Integrity Pressure Protection Systems)have when it is used along with PRV on compressor discharge line to prevent the system from overpressure due to block discharge outlet?
I understand that HIPPs cannot replace the action of a PRV, but it can reduce the relief load expected from the system. If this is achievable, what fration of the load would PRV relief?
I would appreciate input and queries.
Regards
I understand that HIPPs cannot replace the action of a PRV, but it can reduce the relief load expected from the system. If this is achievable, what fration of the load would PRV relief?
I would appreciate input and queries.
Regards
#2
Posted 22 October 2010 - 10:47 AM
As far as I know HIPPS can be replaced with pressure relief devices except for fire case.
But I have seen a refinery plant for which the basic designer has considered some HIPPS failure scenarios among the insttaled HIPPS systesm for sizing of the flare network but in my view this is very conservative design.
But I have seen a refinery plant for which the basic designer has considered some HIPPS failure scenarios among the insttaled HIPPS systesm for sizing of the flare network but in my view this is very conservative design.
#3
Posted 22 October 2010 - 01:30 PM
Hi,
I would suggest you to read the following:
http://people.clarks...esign/hipps.pdf
See also this website:
http://www.sis-tech....urces.html#HIPS
Regards
I would suggest you to read the following:
http://people.clarks...esign/hipps.pdf
See also this website:
http://www.sis-tech....urces.html#HIPS
Regards
Edited by sheiko, 22 October 2010 - 01:33 PM.
#4
Posted 25 October 2010 - 03:18 AM
The function of HIPPS - the way I know it - is to actually replace mechanical relief devices. In some process applications where it is not possible (or not safe, or not economical) to install RV's, HIPPS are employed as the ultimate overpressure protection systems, and their reliability is considered as high as that of mechanical relief devices. We have had a similar discussion in the forums some time ago.
#5
Posted 25 October 2010 - 05:15 AM
Sheiko, thanks for your information.
Below is my challenge:
I understand that HIPPS can reduce the relief load in a flare system. HIPPS can be designed for trip conditions (pump trip, compressor trips). In our case, we considered that block outlet at the compressor discharge line is a possible cause of overpressure in the process system. If it happens, the system needs to be protected by a safety system which can be provided by the PSH for compressor trip, PRV as the final safety device and BDV for system depressurization (this is initiated).
According to API RP 521, the expected relief load is equivalent to the gas flow (1,617,236.51 kg/hr) through the compressor. Designing the flare system to handle this relief load gives a bigger flare system dimensions (especially the flare header and flare KO drum). In order to mitigate against this, we are considering the installation of HIPPS on the compressor discharge line and removing this relief load from the total relief load used for the flare system design. This would give a reasonable flare system dimensions (flare header and KO drum).
What are your queries about this?
Below is my challenge:
I understand that HIPPS can reduce the relief load in a flare system. HIPPS can be designed for trip conditions (pump trip, compressor trips). In our case, we considered that block outlet at the compressor discharge line is a possible cause of overpressure in the process system. If it happens, the system needs to be protected by a safety system which can be provided by the PSH for compressor trip, PRV as the final safety device and BDV for system depressurization (this is initiated).
According to API RP 521, the expected relief load is equivalent to the gas flow (1,617,236.51 kg/hr) through the compressor. Designing the flare system to handle this relief load gives a bigger flare system dimensions (especially the flare header and flare KO drum). In order to mitigate against this, we are considering the installation of HIPPS on the compressor discharge line and removing this relief load from the total relief load used for the flare system design. This would give a reasonable flare system dimensions (flare header and KO drum).
What are your queries about this?

#6
Posted 25 October 2010 - 05:57 AM
Sorry i don't have much practical experience with HIPS. Moreover you didn't provide any PID, so that we can efficiently assist you. Anyway, i believe you have enough material (API, sis-tech website) to continue in the right direction.
Regards.
Regards.
Edited by sheiko, 25 October 2010 - 05:59 AM.
#7
Posted 29 October 2010 - 11:51 AM
asade,
Your plan to use HIPPS to shutdown the compressor, and exclude this load from the flare system design, is a good one. In your last post, however, it sounds like you have some doubt or further questions about this, but it's not clear what those questions are. I'll try to answer your questions if you state them clearly.
Functionally, the HIPPS for this compressor will be very simply. The HIPPS will monitor the pressure on the discharge side of the compressor and trip the power when the pressure exceeds the trip set point. There might also be a need to close an automatic discharge valve, depending on whether or not back-flow is a potential problem.
The first step in the HIPPS design is to determine the necessary SIL requirement for this application. The SIL can be based on a thorough hazard evaluation, or you can simply default to a conservative SIL3 design. You'll see some people say that all HIPPS must be SIL3, but that's not true. A SIL3 design is needed if the user or operating company does not have established risk criteria. Companies that do have established risk criteria can use that to determine the necessary SIL. Refer to API 521 Annex E for guidance.
Once the SIL has been determined, then complete the instrumentation design based on that SIL. If your company doesn't have internal expertise in SIS (safety instrumented system) design, then I strongly suggest paying a vendor to do this for you. There are lots of companies that specialize in SIS design and implementation.
Another point that is critically important to understand is that HIPPS (and other SISs too) are not for everyone. The H & I in HIPPS stand for High Integrity, and that integrity is only maintained when the owner performs the necessary testing and maintenance on these HIPPS systems. If the owner has good process safety, management-of-change, and integrity management programs, then HIPPS are a great safety and cost saving tool. If the operating company doesn't have that discipline and integrity, then HIPPS ought not be used.
Your plan to use HIPPS to shutdown the compressor, and exclude this load from the flare system design, is a good one. In your last post, however, it sounds like you have some doubt or further questions about this, but it's not clear what those questions are. I'll try to answer your questions if you state them clearly.
Functionally, the HIPPS for this compressor will be very simply. The HIPPS will monitor the pressure on the discharge side of the compressor and trip the power when the pressure exceeds the trip set point. There might also be a need to close an automatic discharge valve, depending on whether or not back-flow is a potential problem.
The first step in the HIPPS design is to determine the necessary SIL requirement for this application. The SIL can be based on a thorough hazard evaluation, or you can simply default to a conservative SIL3 design. You'll see some people say that all HIPPS must be SIL3, but that's not true. A SIL3 design is needed if the user or operating company does not have established risk criteria. Companies that do have established risk criteria can use that to determine the necessary SIL. Refer to API 521 Annex E for guidance.
Once the SIL has been determined, then complete the instrumentation design based on that SIL. If your company doesn't have internal expertise in SIS (safety instrumented system) design, then I strongly suggest paying a vendor to do this for you. There are lots of companies that specialize in SIS design and implementation.
Another point that is critically important to understand is that HIPPS (and other SISs too) are not for everyone. The H & I in HIPPS stand for High Integrity, and that integrity is only maintained when the owner performs the necessary testing and maintenance on these HIPPS systems. If the owner has good process safety, management-of-change, and integrity management programs, then HIPPS are a great safety and cost saving tool. If the operating company doesn't have that discipline and integrity, then HIPPS ought not be used.
Similar Topics
![]() Storage Tanks Diked Area Fire Protection Using Foam MakerStarted by Guest_mkhattaby_* , 30 Jan 2025 |
|
![]() |
||
![]() Location Of Pts For HippsStarted by Guest__1angelia23_* , 10 Jan 2025 |
|
![]() |
||
Effect Of Continuous Blow Down To Boiler Feed WaterStarted by Guest_Dyames027_* , 21 Nov 2024 |
|
![]() |
||
![]() Multiple Effect Evaporation 5 Stage CalculationStarted by Guest_pentakota.koti_* , 26 Jun 2018 |
|
![]() |
||
![]() Effect Of Bundle Entrance Rho-V2 And Tube Material Of Shell And Tube TStarted by Guest_prince1pahariaa_* , 21 May 2024 |
|
![]() |