|
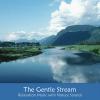
Condensate Recovery
#1
Posted 10 December 2010 - 05:15 PM
#2
Posted 10 December 2010 - 06:22 PM
How can we help you if you don't tell us specifics about what it is that you need help on?
How can we tell what material is relevant if you don't tell us what part or phase of condensate recovery it is that you don't understand or are having problems with?
We need your full description of your problem with condensate recovery.
#3
Posted 11 December 2010 - 08:27 AM
The condensate has just been passed through a flash drum to produce medium pressure steam.
1.Please critique the system
2. help me with the standards or rule of thumb for locating isolation valves upstream/ downstream of a pump and control valves.
3 What is the usual distance of locating elbows reducers before and after a pump/control valve.
4.The distance to locate a check valve from a pump discharge.
#4
Posted 11 December 2010 - 10:42 AM
Kabtik:
- We can’t critique your system since you have not uploaded any file or drawing.
- We can help you with your problem, but we can’t design it for you. You have to do your own design. We are professional engineers who help each other on these Forums; but we work for a living as well – charging a fee for our professional services. If you need help, you have to furnish us with your work product to see where and how we can help. But we can’t generate your work product without getting paid – as you would be also.
Await your response.
#5
Posted 11 December 2010 - 10:55 AM
Attached Files
#6
Posted 11 December 2010 - 12:04 PM
Kabtik:
My comments to your sketch are:
- I presume you apply a back pressure on the flash drum (actually nothing more than a vapor-liquid separator, not a flash drum) with a Control Valve on the exiting flash steam to provide the “medium pressure steam. The pressure in the Flash Drum must be lower than that in the process heat loads. Otherwise, the steam traps will not be able to transfer the condensate to the flash drum. Your flash drum being maintained at an elevated flash steam pressure doesn’t mean that the steam downstream of the back pressure control valve will be at the “medium steam pressure” you desire. You have to generate an accurate steam balance around the flash drum, taking the upstream and downstream conditions into consideration together with any variances in flow conditions existing among them from time-to-time. This involves intimate knowldege of the process requirements and characteristics and the generation of an accurate P&ID. In order to maintain a steady “medium steam pressure”, you must ensure a steady HP condensate flow rate flashing into the Flash Drum – constantly. Any trouble with the steam traps functioning properly 100% of the time and you could have problems in the rest of the system.
- There are no standards or “rules of thumb”. Just use common engineering sense and logic in designing the system to achieve what you want or need. We don’t have your complete scope of work or detailed basic data, so we can’t make any specific recommendations. If have multiple condensate pumps and they are operated manually, then certainly you will require block valves to manually switch and maintain these. If your system is to be remotely operated, then you need remote operated valves and controls. This is common sense.
- The usual distance of locating elbows reducers before and after a pump/control valve is dependent on the conditions of the fluid and its flashing/cavitation tendencies. We don’t know these because you haven’t furnished detailed basic data. But these are usually not critical if you size your velocities and pressure drops conservatively.
- The distance to locate a check valve from a pump discharge is hardly ever critical. I don’t understand the concern here – if there is one. I usually allow my piping configuration to determine the location of the check valve, always trying to place it in a convenient place, close to the pump discharge.
#7
Posted 11 December 2010 - 12:26 PM
#8
Posted 12 December 2010 - 11:07 PM
You mentioned in your attachment -"Drum operating pressure is 5 barg. This pressure in the drum will add to the NPSHa"
Your drum is at equilibrium and drum pressure = vapour pressure. Any amuont of pressure in the drum WILL NOT contribute to the NPSHa for the pump. NPSHa = (elevation) - (losses). Be careful in specifing NPSHa in the pump datasheet.
I had carried out such modification in the exisitng plant. I confirmed the chest pressure of the reboilers for actual heat balance and trap functioning. Most critical aspect for such design is -
-avaiable pressure level of heat in the reboiler - check chest pressure
-Hydraulics of the trap and pipings
-NPSHa for the pump
#9
Posted 12 December 2010 - 11:58 PM
#10
Posted 13 December 2010 - 10:45 AM
what s your idea about eliminating pump because,as shown in page 3 of attached file, condensate receiver pressure is atmospheric and there is enough differential pressure to send condensate from flash drum to condensate receiver.
#11
Posted 14 December 2010 - 10:08 PM
Dear frinds,
what s your idea about eliminating pump because,as shown in page 3 of attached file, condensate receiver pressure is atmospheric and there is enough differential pressure to send condensate from flash drum to condensate receiver.
Yes you can definitely do away with the pump. With or without pump I will like to add one more suggestion - Install the LV as close to the atmospheric drum as possible to minimize 2 phase region at the downstream of control valve.
#12
Posted 17 December 2010 - 12:02 PM
1. Yes, most probably you can eliminate the condensate pump, as we did in a similar system. Condensate flow along whole line would be two phase -- this did not disturb flow (e.g. noise, vibration) in our case. If velocity of flow (gas+liquid) is higher than 5 m/s, resulting "emulsified" (or homogeneous) flow is of no problem (N.P. Lieberman, A working guide to Process equipment, 2008, para 39.3 mixed phase velocity). With available ΔP~5Bar, this velocity could be realized.
2. Vent on the atmospheric "drum" should be adequate to discharge (to safe location) maximum steam escape due to failure of the biggest trap (this can often be considered same as max steam consumption of the biggest consumer A, B, C, D).
3. One rule of thumb for condensate pipe size -- consider it 100% liquid and size the pipe for 0.3 - 0.9 m/s. But you had better check resulting ΔP and mixed flow velocity for the selected pipe size (consider para 1 above).
4. Condensate collected in D2 may need treatment, depending on the intended use. E.g. for use as boiler feed water, it usually undergoes polishing by cation and anion resins to reduce soluble and colloidal iron to 0.05 mg/l; if oily, (hydrocarbon) oil is reduced to 0.5 mg/l by a settling tank/coalescer and activated carbon filters.
Similar Topics
Vacuum RecoveryStarted by Guest_Paper_* , 25 Feb 2025 |
|
![]() |
||
How To Remove The Condensate In A Wet Gas StreamStarted by Guest_ksagarzazu_* , 25 Feb 2025 |
|
![]() |
||
Off Spec Condensate Storage TankStarted by Guest_shekhar dhuri_* , 05 Sep 2013 |
|
![]()
|
||
![]() Opportunities For Heat Recovery In A Chemical Process PlantStarted by Guest_tanyongboon1_* , 29 Nov 2024 |
|
![]() |
||
![]() ![]() Steam Condensate Pipeline Water HammerStarted by Guest_kaidlut_* , 06 Sep 2024 |
|
![]() |