|
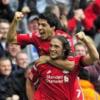
9 replies to this topic
Share this topic:
#1
Posted 19 March 2012 - 11:21 AM
Does any one here working on SCF extraction for essential oil from different spices ??///
#2
Posted 19 March 2012 - 11:32 AM
#3
Posted 20 March 2012 - 07:37 PM
Faizan:
I have already sent you a private message asking you to stop Hijacking another old thread with the following post. I have copied that post and am putting it here in order to continue with this thread which is yours and specifically addresses your topic. I will delete your other threads in a few days. Use this thread to deal with this topic. Your other post follows:
"Hello Mr. Art Montemayor
Well, actaully the basic problem I’m having with my supercritical process is recycling CO2 and using Liquid CO2 from a tank.
The problem is the pump: we maintain a tank at 23 bars and filled with liquid CO2 cylinder which have more or less 60 bars pressure and temperatre -5 C and our tank temperate is -15 C and the plunger pump we are using does not work at 23 bars but it works wonderfully well at 60 bars from liquid CO2 cylinder and if the pump worked then its body starts to freeze after 10 mins of processing.
Please can you suggest any pump that can work at such low pressure to high pressure of 350 bars?
Thanking you "
Now I address your post above:
Your explanation in English is difficult to understand. There is one engineering universal language - an accurate, detailed sketch or schematic of your process showing all the flow rates, temperatures, pressures (always state if the pressure is absolute or gauge) and phases. You should provide us with such a schematic drawing in order to better understand what you have and what you are describing.
Yours is not a difficult problem. I can resolve very easily if I am given the basic data I require in order to address the problem in an accurate manner.
Await your reply.
I have already sent you a private message asking you to stop Hijacking another old thread with the following post. I have copied that post and am putting it here in order to continue with this thread which is yours and specifically addresses your topic. I will delete your other threads in a few days. Use this thread to deal with this topic. Your other post follows:
"Hello Mr. Art Montemayor
Well, actaully the basic problem I’m having with my supercritical process is recycling CO2 and using Liquid CO2 from a tank.
The problem is the pump: we maintain a tank at 23 bars and filled with liquid CO2 cylinder which have more or less 60 bars pressure and temperatre -5 C and our tank temperate is -15 C and the plunger pump we are using does not work at 23 bars but it works wonderfully well at 60 bars from liquid CO2 cylinder and if the pump worked then its body starts to freeze after 10 mins of processing.
Please can you suggest any pump that can work at such low pressure to high pressure of 350 bars?
Thanking you "

Now I address your post above:
Your explanation in English is difficult to understand. There is one engineering universal language - an accurate, detailed sketch or schematic of your process showing all the flow rates, temperatures, pressures (always state if the pressure is absolute or gauge) and phases. You should provide us with such a schematic drawing in order to better understand what you have and what you are describing.
Yours is not a difficult problem. I can resolve very easily if I am given the basic data I require in order to address the problem in an accurate manner.
Await your reply.
#4
Posted 21 March 2012 - 05:56 AM
Hello Mr Art.
how are you hope you are fine. The thing is that the project Mr. AJ khan was working on is the same project and im appointed as replacement for him. there are alot of changes have been made on this project. I am making a new PFD in relation with ur discussions with MR AJ. Ill attach as soon as possible surely till this sunday Im also a fresh graduate because our boss only hire fresh graduates.
Thank you for waiting Ill soon be send you all details
Faizan Raza
how are you hope you are fine. The thing is that the project Mr. AJ khan was working on is the same project and im appointed as replacement for him. there are alot of changes have been made on this project. I am making a new PFD in relation with ur discussions with MR AJ. Ill attach as soon as possible surely till this sunday Im also a fresh graduate because our boss only hire fresh graduates.
Thank you for waiting Ill soon be send you all details
Faizan Raza
#5
Posted 21 March 2012 - 05:56 AM
and I am sorry for writing on the old thread
please accept my apology
please accept my apology
#6
Posted 21 March 2012 - 07:29 AM
Faizan:
Thank you for responding in a positive manner and explaining your situation. I am now familiar with what you are confronting locally and perhaps can be of help.
In preparing your basic data and sketches, use an Excel workbook to compile all your work: sketches and calculations. That way we and all our interested Forum members can communicate efficiently and accurately. As a young engineering graduate it is important for you to learn how to best communicate with peers and others in an efficient and accurate way. You can use the prior Excel Workbooks generated for AJ Khan's thread and we can go from there. Always retitle a revised or new workbook. When you modify a workbook, always put a Revision number on it. The number should be progressive. That way, we know exactly what is what and what came first and how changes have been incorporated during the project's development.
Thank you for responding in a positive manner and explaining your situation. I am now familiar with what you are confronting locally and perhaps can be of help.
In preparing your basic data and sketches, use an Excel workbook to compile all your work: sketches and calculations. That way we and all our interested Forum members can communicate efficiently and accurately. As a young engineering graduate it is important for you to learn how to best communicate with peers and others in an efficient and accurate way. You can use the prior Excel Workbooks generated for AJ Khan's thread and we can go from there. Always retitle a revised or new workbook. When you modify a workbook, always put a Revision number on it. The number should be progressive. That way, we know exactly what is what and what came first and how changes have been incorporated during the project's development.
#7
Posted 26 March 2012 - 10:08 AM
Hello Mr. Art
Hope you are fine. I have prepared and Excel sheet in which i mention the Process description the problem statement PFD and the equipment list.
hope i did it right this time and communicate properly.
thanking you
Faizan Raza
Hope you are fine. I have prepared and Excel sheet in which i mention the Process description the problem statement PFD and the equipment list.
hope i did it right this time and communicate properly.
thanking you
Faizan Raza
Attached Files
#8
Posted 05 April 2012 - 10:13 PM
Faizan:
Please refer to and read the attached Rev1 copy of your Workbook. Study my comments throughout the workbook and you will note that I don't see any difficulty with resolving what you have as problems. You simply haven't given us enought information to get down to specific details.
However, with the correct design, installation, and operation of a feed pump and a recompressor, you should not have any problems. This process is easy and convenient to design accurately and with full confidence. The hardest part of the process is the mechanical equipment and the safety hazards surrounding it during the design and operation. I hope I have succeeded in explaining to you how you can resolve your problems and that you can study and master the thermodynamics involved and the process operations required.
Please refer to and read the attached Rev1 copy of your Workbook. Study my comments throughout the workbook and you will note that I don't see any difficulty with resolving what you have as problems. You simply haven't given us enought information to get down to specific details.
However, with the correct design, installation, and operation of a feed pump and a recompressor, you should not have any problems. This process is easy and convenient to design accurately and with full confidence. The hardest part of the process is the mechanical equipment and the safety hazards surrounding it during the design and operation. I hope I have succeeded in explaining to you how you can resolve your problems and that you can study and master the thermodynamics involved and the process operations required.
Attached Files
#9
Posted 07 April 2012 - 03:10 AM
hello,
Sir,
How are you, Hope you are fine. I am really sorry that you having difficulties in understanding my description due to my poor English skill. I' ll try to improve on my English as well to communicate with you in a better way.
and also I want to thank you for responding on my issues
1. I have attached 3 file the first file is my reply to you comments and suggestions
2. the flow restrictor catalogue
3. the pump catalogue which is available in our market
Also i want to ask you that can this process be simulated in Hysys or Aspen one or Chemcad or any other simulation software?
Hope I did able to communicate with you better
Thanking you
Faizan Raza
Sir,
How are you, Hope you are fine. I am really sorry that you having difficulties in understanding my description due to my poor English skill. I' ll try to improve on my English as well to communicate with you in a better way.
and also I want to thank you for responding on my issues
1. I have attached 3 file the first file is my reply to you comments and suggestions
2. the flow restrictor catalogue
3. the pump catalogue which is available in our market
Also i want to ask you that can this process be simulated in Hysys or Aspen one or Chemcad or any other simulation software?
Hope I did able to communicate with you better
Thanking you
Faizan Raza

Attached Files
#10
Posted 07 April 2012 - 11:18 PM
Faizan Raza:
Please do not apologize for your poor English. We can make up for that with good, professional, and safe engineering. I gladly attempt to try to help you out of what you are having problems with for several reasons:
1. That is what we hope the Forums can do for our members;
2. I have many years of working directly with CO2 systems in design, fabrication, installation, and operation and I willingly offer my experience to anyone who needs it in this Forum;
3. I sense a lack of experience and understanding in processing a compressed gas and a super critical fluid (SCF) – such as CO2. This has all the possibilities of creating some very serious and dangerous hazards and I would not want anyone getting seriously hurt or killed upon making a mistake with this kind of process;
The last reason is why I continue to emphasize that you must heed and understand what I explain to you and take the advice with a serious note of precaution and trusting that I know what I am writing about because of many years of experience in this field. I am an engineering consultant at the present time and companies pay me for my advice - not because I am very smart or brilliant, but because I am very experienced, old, and have done many of these things successfully in the past. There is an old saying in Spanish: “The Devil is not a dangerously clever person because he is the Devil; he is dangerously clever because he is OLD.”
In addition, I ask you to heed my advice seriously because I give it hoping it will spare you any negative results in your work while improving, perfecting, and operating this process. This process, as I have said before, is very simple. However, do not take it for granted and feel overly confident with it. Easy processes can also be very dangerous if not designed and operated correctly and safely.
I would not waste my time trying to design this simple process on a simulation program. That is a very gross “over-kill”. That is the same as using an elephant to move a kitchen chair. This process is too simple and more importantly requires practical, hands-on project engineering rather than a process simulation. In my opinion, you are over-reacting and concentrating on superficial things when you should be more concerned with other, more important details about the process.
Your LCO2 pumping rate is only 25 cubic inches per minute, 0.10 gpm, a miniscule flow rate that makes it difficult to select a proper LCO2 pump. Why you selected such a small flow rate is not stated by you. You can fill the extractor much faster than that and heat up your LCO2 while it is in the extractor. I recommend you obtain a proper, LCO2 transfer pump for this process. Hydro-Test makes good cylinder testing equipment; I often recommend them as suppliers of hydrotesting equipment. But I would not use their pump for this process. If your boss is concentrating on only buying cheap equipment, then that is probably a big reason for all the problems you are having. You cannot expect to have an efficient and safe SCF extraction process with cheap equipment that hasn’t been designed and operated by experienced and capable engineers. That costs money and there is no reasonable way to get around that. Either you boss spends the capital money to make sure that the proper, safe equipment is bought, or he gets out of the business of trying to extract oil with a low-cost investment attitude.
Every time you have to submit information on this thread you should use the same, original Workbook we started which is named SCF Process and update the Rev number. That is the proper, smart and organized engineering way to keep track of all documentation and revisions. I am submitting SCF Process Rev2 with this post.
You now submit new basic data that you did not submit before. By submitting basic data piece-by-piece, you are prolonging the time and effort it takes to finish this thread. You yourself have expressed that this information is need by you fast. Why, then, haven’t you followed my requests for all the basic data and sent it in the first time? I can only respond to accurate, complete, and concise basic data. For example I now learn of the pump and the compressor – but only partly, because I don’t know the capacity, flow rate and other compressor information.
You should be using a 2-stage reciprocating compressor, properly designed. How you are going to get this done is something that you (or your boss) will have to resolve. I know exactly how to do it and how to specify all the equipment. But I am a consultant. I can help you on this Forum, but I can’t give your boss “free” engineering for this project.
You should be heating your LCO piping and extractor with approximately 75 oC glycol solution. That is the safest way to get to the SCF phase. Your flows are so small, you must be using ½ inch OD stainless steel tubing. If this process is only a Pilot Plant, that is something else that you have not revealed. If it is supposed to be a commercial process, it is very small and your boss should keep his fingers out of the design and concentrate on getting sufficient capital monies for the true investment.
Please make note of the comments I have made (in bold RED) on your latest queries. I calculate that your present storage tank has a maximum LCO2 capacity of 232 kgs, based on using 80% of the internal volume – which is standard, safe industrial practice in the CO2 industry. I don’t know how your boss installed 49 meters of refrigerating coil inside the tank, but he surely did not weld inside the tank, so I can only guess that he simply inserted the loose coils inside and it is laying in the bottom of the tank, where it can’t give any efficient heat transfer to the incoming warm, recovered CO2 gas.
One additional point: The restrictor element is doing nothing but causing a pressure drop. As I have previously told you, you must use your engineering ability to know how unit operations work – especially positive displacement pumps. You must do this since your boss is not an engineer and incapable of knowing that a PD pump such as the LCO2 pump delivers the same quantity (flow) of LCO2 on every stroke. That means that if the speed and stroke of the pump are fixed, the flow rate is constant – regardless of anything downstream of the pump. And that includes the “restrictor”. Nothing can “restrict” the discharge of a PD pump. It will continue to pump the same flow even if the discharge is blocked; and when that happens a properly pressure relief valve should already be installed and safely discharge the high pressure flow. That is only one of the safety issues that must be addressed on this process. If your boss doesn’t like the Tomco pump because it is too expensive, then try: Industrial Carbonics, Danville, IL 61834
http://ico2.com/Co2Pumps.htm
He will also find that these pumps are not “cheap”. But they operate without problems and safety issues.
If you have any further queries in the future, please organize them in a logical order. I have had to go all over the spreadsheet and the post to address your different queries.
Please do not apologize for your poor English. We can make up for that with good, professional, and safe engineering. I gladly attempt to try to help you out of what you are having problems with for several reasons:
1. That is what we hope the Forums can do for our members;
2. I have many years of working directly with CO2 systems in design, fabrication, installation, and operation and I willingly offer my experience to anyone who needs it in this Forum;
3. I sense a lack of experience and understanding in processing a compressed gas and a super critical fluid (SCF) – such as CO2. This has all the possibilities of creating some very serious and dangerous hazards and I would not want anyone getting seriously hurt or killed upon making a mistake with this kind of process;
The last reason is why I continue to emphasize that you must heed and understand what I explain to you and take the advice with a serious note of precaution and trusting that I know what I am writing about because of many years of experience in this field. I am an engineering consultant at the present time and companies pay me for my advice - not because I am very smart or brilliant, but because I am very experienced, old, and have done many of these things successfully in the past. There is an old saying in Spanish: “The Devil is not a dangerously clever person because he is the Devil; he is dangerously clever because he is OLD.”
In addition, I ask you to heed my advice seriously because I give it hoping it will spare you any negative results in your work while improving, perfecting, and operating this process. This process, as I have said before, is very simple. However, do not take it for granted and feel overly confident with it. Easy processes can also be very dangerous if not designed and operated correctly and safely.
I would not waste my time trying to design this simple process on a simulation program. That is a very gross “over-kill”. That is the same as using an elephant to move a kitchen chair. This process is too simple and more importantly requires practical, hands-on project engineering rather than a process simulation. In my opinion, you are over-reacting and concentrating on superficial things when you should be more concerned with other, more important details about the process.
Your LCO2 pumping rate is only 25 cubic inches per minute, 0.10 gpm, a miniscule flow rate that makes it difficult to select a proper LCO2 pump. Why you selected such a small flow rate is not stated by you. You can fill the extractor much faster than that and heat up your LCO2 while it is in the extractor. I recommend you obtain a proper, LCO2 transfer pump for this process. Hydro-Test makes good cylinder testing equipment; I often recommend them as suppliers of hydrotesting equipment. But I would not use their pump for this process. If your boss is concentrating on only buying cheap equipment, then that is probably a big reason for all the problems you are having. You cannot expect to have an efficient and safe SCF extraction process with cheap equipment that hasn’t been designed and operated by experienced and capable engineers. That costs money and there is no reasonable way to get around that. Either you boss spends the capital money to make sure that the proper, safe equipment is bought, or he gets out of the business of trying to extract oil with a low-cost investment attitude.
Every time you have to submit information on this thread you should use the same, original Workbook we started which is named SCF Process and update the Rev number. That is the proper, smart and organized engineering way to keep track of all documentation and revisions. I am submitting SCF Process Rev2 with this post.
You now submit new basic data that you did not submit before. By submitting basic data piece-by-piece, you are prolonging the time and effort it takes to finish this thread. You yourself have expressed that this information is need by you fast. Why, then, haven’t you followed my requests for all the basic data and sent it in the first time? I can only respond to accurate, complete, and concise basic data. For example I now learn of the pump and the compressor – but only partly, because I don’t know the capacity, flow rate and other compressor information.
You should be using a 2-stage reciprocating compressor, properly designed. How you are going to get this done is something that you (or your boss) will have to resolve. I know exactly how to do it and how to specify all the equipment. But I am a consultant. I can help you on this Forum, but I can’t give your boss “free” engineering for this project.
You should be heating your LCO piping and extractor with approximately 75 oC glycol solution. That is the safest way to get to the SCF phase. Your flows are so small, you must be using ½ inch OD stainless steel tubing. If this process is only a Pilot Plant, that is something else that you have not revealed. If it is supposed to be a commercial process, it is very small and your boss should keep his fingers out of the design and concentrate on getting sufficient capital monies for the true investment.
Please make note of the comments I have made (in bold RED) on your latest queries. I calculate that your present storage tank has a maximum LCO2 capacity of 232 kgs, based on using 80% of the internal volume – which is standard, safe industrial practice in the CO2 industry. I don’t know how your boss installed 49 meters of refrigerating coil inside the tank, but he surely did not weld inside the tank, so I can only guess that he simply inserted the loose coils inside and it is laying in the bottom of the tank, where it can’t give any efficient heat transfer to the incoming warm, recovered CO2 gas.
One additional point: The restrictor element is doing nothing but causing a pressure drop. As I have previously told you, you must use your engineering ability to know how unit operations work – especially positive displacement pumps. You must do this since your boss is not an engineer and incapable of knowing that a PD pump such as the LCO2 pump delivers the same quantity (flow) of LCO2 on every stroke. That means that if the speed and stroke of the pump are fixed, the flow rate is constant – regardless of anything downstream of the pump. And that includes the “restrictor”. Nothing can “restrict” the discharge of a PD pump. It will continue to pump the same flow even if the discharge is blocked; and when that happens a properly pressure relief valve should already be installed and safely discharge the high pressure flow. That is only one of the safety issues that must be addressed on this process. If your boss doesn’t like the Tomco pump because it is too expensive, then try: Industrial Carbonics, Danville, IL 61834
http://ico2.com/Co2Pumps.htm
He will also find that these pumps are not “cheap”. But they operate without problems and safety issues.
If you have any further queries in the future, please organize them in a logical order. I have had to go all over the spreadsheet and the post to address your different queries.
Attached Files
Similar Topics
![]() Supercritical Fluid Flowrate - He Tube RuptureStarted by Guest_flarewolf_* , 07 Apr 2025 |
|
![]() |
||
Prv Vs Extraction Condensing TurbineStarted by Guest_mj311_* , 13 Nov 2024 |
|
![]() |
||
Ll Extraction TowerStarted by Guest_dpunnn_* , 22 Nov 2024 |
|
![]() |
||
Ll Extraction: Equilibrium Stages Calculation With Matlab CodeStarted by Guest_MGFX70_* , 14 Apr 2022 |
|
![]() |
||
Best Practices For Extraction Of Amines From Wood TarStarted by Guest_quantum31_* , 19 Jun 2023 |
|
![]() |