|
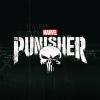
Compressor Intercooler Operating Failure.
#1
Posted 11 July 2012 - 12:52 AM
This is with reference with my Previous Post (dated 20th April). I am Currently Commissioning an Air Separation Unit.
For the past few months I have been struggling to figure out the possible reason of water Carryover along with Process Air from A direct Contact vessel.
The Configuration is: Hot Air discharged from an Air Compressor is to be cooled in a Direct Contact Vessel with Chilled water. There is a Low Point Drain in the Process Air Line before entering the Vessel.
As per Start up scheme: First, Air is introduced in the Vessel; then water Supply is started. As soon as water is introduced into the cooler, we can see water coming out from the above mentioned Low Point Drain. How is this Back Flow possible?
With Considerable time we see the Compressor is observing a back pressure suggesting a Liquid hold in the packings. But we couldn't fathom the backflow of water through that drain. On Closing this drain, we see water spilling out from the discharge air line downstream of the Vessel.
Operating Vessel Pressure = 8.6 kg/cm2(g)
Packing Height = 5 meters
Can you please help me out in sorting out this BackFlow Phenomenon? Also, it would be of great help if you all can aid me with Literatures that describes Packing and Holdups in them.
Regards
Bodhisatya.
#2
Posted 11 July 2012 - 12:59 AM
Breizh
#3
Posted 11 July 2012 - 10:04 AM
Please find the attached Simplified Flow chart for better understanding.
It is that Low Point Drain from where Water Spilling is observed once water flow is established into the Vessel by starting the Pump.
Please help me out by giving some valuable insights to crack this riddle.
Regards
Bodhisatya
Attached Files
Edited by Bodhisatya, 11 July 2012 - 10:06 AM.
#4
Posted 11 July 2012 - 03:15 PM
Let us check whether water flow capacity out of the Direct Cooler is adequate. If so, one could search for another reason, more complicated. If not, water level in the bottom of Direct Cooler is rising. When it meets air intake, some water (not all) is discharged through low point drain of compressed air line. Following increase of packing ΔP indicates that water level is still going higher, touching the packing. This is intensified by closing the drain valve, hence water entrainment occurs.
A preliminary check could be to operate only the water pump without the compressor (along with flow out system) and see whether water flows through the low point drain valve. If it does, a simple level gauge can be placed on the Direct Cooler (e.g. a glass column, from level of air intake to packing bottom) to see water level when both air compressor and water pump are in operation.
Above interpretation may be naive, yet unexpected cases do occur in Operations, the possibility of which has to be excluded. One can have a much better image by following the case close by.
A weak point of above interpretation is that "as soon as water is introduced we see water coming out from the above mentioned Low Point Drain", which would have been observed after some time of water introduction. Probably water is coming down by contacting the internal walls of the Direct Cooler (something contrary to packing channeling), yet to be partially diverted into the compressed air line looks improbable.
#5
Posted 11 July 2012 - 06:55 PM
Breizh
#6
Posted 11 July 2012 - 10:49 PM
As I said, the Start Up procedure is to fill a certain Level of water in the Vessel Sump and then introduce Air into the System to prevent Air entering into Cooling Water Header. On Starting the Water Pump, the Vessel Sump is maintained at an optimum level by a Level Controller.
Initial suspicion was that the Level Transmitter might be erroneous so Level Gauges were installed. Both readings tallied ruling out malfunctioning of LT.
Another suspicion was that the maintained Level (that was initially 60% of the total range) was very close to the air inlet nozzle. After consulting the GA diagram, the level was brought down to as Low as 18%, but still similar results were obtained.
I had a talk with the vendor who supplied the packing internals and he said channeling probability is very less in this vessel because it's dia is only 800 mm.
The exercise of only running the pump will result only in increasing the water level as it doesn't have any downward resistance to return back to the return Header.
It is very true that the phenomenon of back flowing is highly improbable, but it's happening and I have no technical justification regarding the same.
Regards
Bodhisatya.
#7
Posted 12 July 2012 - 07:08 AM
Waiting for some sort of insights.
Regards
Bodhisatya.
#8
Posted 12 July 2012 - 03:41 PM
For how long have you left the drain valve open and witnessed water coming out? Could this water be from condensation of humid air in the compressor that eventually settles in the drain leg?
Mahesh A&M
#9
Posted 13 July 2012 - 11:00 AM
#10
Posted 14 July 2012 - 02:19 PM
1. So bottom of Direct Cooler (DC) is filled with water, then air compressor starts, then water pump starts, immediately you see water coming out of low point drain. Installed level gauges are electronic (to show indications in a panel) or optical (so that actual liquid level is visible)?
2. In case they are electronic, running the water pump without the compressor (easy task) could reveal something useful. If water does not flow from low point drain, it is the air flow causing the disturbance. If water does, capacity of water discharged from DC is inadequate, for it is expected to cover the case of no air flow. This does not necessitate flow through low point drain, when air compressor operates; it is only an indication of potential inadequacy of water discharge system (LCV, plugging, etc).
3.Calibration/ check of instruments is assumed to have been already implemented. An optical level gauge, if the installed ones are electronic will be useful. Water balance (in, out with air, out from DC bottom, out through low point drain) based on measured water flows (except that going out with air, to be estimated) may give useful signs.
Edited by kkala, 14 July 2012 - 02:42 PM.
#11
Posted 15 July 2012 - 02:32 AM
Dear Sir
We have both electronic as well as optical Level Indicators to measure DC Sump level. The values from both instruments tend to match. As for running the pump without the compressor, as I pointed out in my previous post, the water will not get any back resistance to return back to the header, hence the level in DC will tend to rise and finally when it reaches the air inlet nozzle, it will start pouring out of the Low Point Drain. To check the inadequecy of the Out Supply of the water through the DCAC, I did the Manual draining of water coming into DCAC, still found water at the LPD.
One interesting observation during these trial runs was that on increasing the water flow rate the %age opening of Control valve increased by merely 1 %. Does this mean that the water being fed in the vessel is not coming to the bottom Sump at all? Rather, it is being held up in the void areas of the packing? Also, my Compressor is having an unload offset of 0.4 bar, which means the compressor will unload if the Measured pressure is 0.4 bar more than that of the Set Point. And it has been noticed that the Compressor gradually unloaded after a time, suggesting that an additional pressure of 0.4 bar is being felt. Now the packing height is 5 m, which corresponds to a 0.5 bar pressure. Does this throw some light on the ongoing anomaly?
Regards
Bodhisatya
#12
Posted 15 July 2012 - 01:35 PM
During manual draining of water coming into DC, there was water flow through lp drain. Did you open the LCV manually, or another valve was used (e.g. bypass)? Was air compressor running?
2. Level in DC bottom (sump) is set at 18%. Is observed visual indication of LG stable during operation? Anticipated answer is "yes", please confirm. Which means that water flowing from low point drain comes from up, not from bottom. So disturbance is due to flowing compressed air, making things more complicated.
3. Diagnosing from a distance is quite difficult is such a situation. Following documents are thought to be needed, apart from info already asked. Of course procedure may be long and fruitless, but more effective.
α. Updated PID from compressor exit to water pump included; also indicating all new instruments added, the water discharge from DC, suction of water pump (hand mark additions would be OK).
β. Data sheet of: Air Compressor, Direct cooler (with dimensions on a sketch and noting the normal water level of 18%), Water Pump, LCV.
γ. Flow sheet covering mentioned equipment (hopefully available).
d. Brief description of trials to settle the problem, in addition to these already described.
4. Help from other members would be welcomed, familiarity would accelerate result, which might depend on an unsuspected detail, operating "evidently well".
5. Some personal comments subject to criticism.
5.1 Water coming down by contacting the internal walls of DC means "licking" its internal walls (not channeling of the packing), but passing into air intake while flowing down looks improbable.
5.2 Water flows counter currently to air in the 5 m packing, air frictional pressure drop is not necessarily 0.5 m. Any flooding will increase ΔP.
5.3 In steady state, water going to DC bottom can be estimated by mass balance. Increase q of water pump flow will result in increase q of flow to DC bottom, if droplet entrainement considered insignificant (but there is also the lp drain flow).
5.4. LCV opening indication may be not correct, or the valve oversized (??).
#13
Posted 20 July 2012 - 12:15 AM
This supposes that the DC can be adequately "drained " (without flow from lp drain) when the compressor is not running, which is good practice. I would try to assure it first, e.g. by checking the PCV and relevant piping (mentioned in previous letters).
I am leaving for the country today to get rid of local summer heat, not having a permanent web connection available there. But please inform about the solution of this problem, when it is found out (hopefully soon).
Edited by kkala, 20 July 2012 - 12:19 AM.
#14
Posted 22 July 2012 - 12:25 AM
Sorry for the Late Reply.Was on a Vacation. Providing Techinical Specifications and Datasheets will be a bit difficult as these items are Copyrighted with my Organization as well as with our Vendors. Please let know the exact queries and I will answer. At best I will try to upload the General Arrangement Diagram of DC.
The Exercise of reducing Air Flow to the Vessel was done to a certain extent, the Design Air flow to the system is around 5,800 Nm3/hr, By venting out the Air from a manual vent upstream of DC, I reduced air flow to vessel. But I still observed carryover, although it was not iterated and few more trials were not done. So couldn't come to the conclusion at best what is the minimum flow to be fed in the system. What I wonder is if suppose Air superficial velocity is higher and vessel dia. is inappropriate then entrainment at the outlet of the vessel is understandable, but how come a back of water in the Air Line?
Regards
Bodhisatya.
#15
Posted 22 July 2012 - 11:49 AM
1) as obvious for a field engineer a flow diagram is ideal while the problem is physical; we need a actual layout drawing;
2) the air compressor will be having a saturated air and on compression will have a superheated air at higher pressure and on cooling will definitely drop water; from your drawing i am not clear about the level control being discussed; is the level maintained by inlet regulation or by outlet dumping; the pdf doesnot show any level control; at what level is the water maintained and what is the inlet elevation of the air pipe; is there a vertical or siphon leg on the air inlet pipe?
3) the more important aspect is the level of the compressor and the vessel; combined with the level on the point above and the actual reading of iso elevation of the air inlet piping we can look out siphoning of water ; this will also show how the water is removed from an upstream point (theoretically at a higher pressure and hence not possible) as the water leg will overcome the delp on the air line;
once you give us an iso of the inlet piping and the level control arrangement we can crack the issue
cheers
neelakantan
#16
Posted 16 August 2012 - 02:24 AM
It is a difficult task to make a consise description of the whole issue again, clarifying all points touched in above posts; followed by one elaborated drawing to summarize all information already requested from several diagrams (including piping arrangement and elevations per post No 15), limited to the area of interest. Nevertheless I think this would not violate any copyright agreement and can greatly contribute to solution.
You could even contact someone experienced in trouble shooting (beside Forums), if this laborious effort results in a fruitfull document.
Norman P Lieberman in the Introduction of "A Working Guide to Process Equipment" (McGraw Hill, 2008, 3rd edition) writes:
....Liz and I would be happy to discuss any questions you might have pertaining to the process equipment discussed in our book. You can phone or fax us in the United States at Phone: (504) 887-7714 FAX (504) 456-1835 . But if you call us with a question, my first response is likely to be, "Have you looked the problem over in the field?" Norman P Lieberman E-mail: norm@lieberman-eng.com.
Of course an easier option (and costlier) is to invite a specialist to the site. Said document can still be useful
#17
Posted 10 September 2012 - 03:24 AM
Regards
Bodhisatya.
#18
Posted 12 September 2012 - 06:26 AM
Diameter of Direct Cooler increased from 800 to 850 mm, decreasing superficial air velocity in it by about 11.4% (say from 0.43 to 0.38 m/s). This may be too small to affect flooding, replacement of packing is assumed to have actually "corrected" the operation. However opinions from others would be welcomed on this point (no relevant experience).
According to Perry (5th edition, 18-21, packed columns) "the design through-put for a packed column should allow for a +/- 30 percent error in the predicted flood point" (Perry, 5th edition, 18-21, packed columns).
#19
Posted 12 September 2012 - 06:43 AM
What about the distributor(s)?
Thanks for sharing
Breizh
#20
Posted 13 September 2012 - 09:22 AM
Similar Topics
Psv On Centrifugal Compressor DischargeStarted by Guest_Lyne_* , 10 Jun 2025 |
|
![]() |
||
![]() Lng Boil Off Gas Compressor Suction DrumStarted by Guest_Lyne_* , 04 Jun 2025 |
|
![]() |
||
Parallel Compressor Setup With Uneven CapacitiesStarted by Guest_sinrem_* , 13 May 2025 |
|
![]() |
||
![]() Hysys Expander/compressor Input Using Dimensionless CurveStarted by Guest_Alfreedo_* , 21 Apr 2025 |
|
![]() |
||
Check Valve FailureStarted by Guest_Falah_* , 26 Mar 2025 |
|
![]() |