|
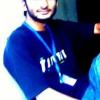
Hydrogen Compressor Increased Discharge Temperature
Started by Pankaj Rohilla, Aug 19 2012 02:03 AM
6 replies to this topic
Share this topic:
#1
Posted 19 August 2012 - 02:03 AM
increase in discharge temperature of hydrogen make up gas compressor (reciprocating) in dhds (diesel hydro desulphurisation unit ).
Temp. Is rising approaching tripping limit, plz share control measures too..
If u hav any file related
Mail me @ pankhrohilla@yahoo.com
Reply Asap..
Temp. Is rising approaching tripping limit, plz share control measures too..
If u hav any file related
Mail me @ pankhrohilla@yahoo.com
Reply Asap..
#2
Posted 19 August 2012 - 03:39 AM
If you are sure the machine are in good shape (no mechanical wear, cooling system running ok, water flow and temp. to designed level), and unit parameters are not changes, pls. check the hydrogen gases make-up composition? make comparision with designed conditions, changing the compresibility factor Z of gases could give some issues. In case it's you have an anti-surge system check the cooler (if is) or other abnormal leak, recycling around the compressor stage. Success
#3
Posted 19 August 2012 - 08:01 AM
thanks, but have you full detail, i've to give presentation of the topic, or a handbook.
#4
Posted 19 August 2012 - 08:17 AM
A good indicator to check mechanical state of any compressor is the polytropic exponent (n). The actual value shall not be higher than the manufacturer's one. A sudden increase would indicate a mechanical issue (suction or discharge valves for a reciprocating compressor) as n is independant of process conditions.
The polytropic exponent "n" can be back-calculated with:
(n-1)/n = ln(Td/Ts)/ln(Pd/Ps),
T and P at discharge and suction conditions shall be in absolute units.
Source: Bonem J M, "Problem Solving for Process Operators and Specialists", Wiley, 2011.
The polytropic exponent "n" can be back-calculated with:
(n-1)/n = ln(Td/Ts)/ln(Pd/Ps),
T and P at discharge and suction conditions shall be in absolute units.
Source: Bonem J M, "Problem Solving for Process Operators and Specialists", Wiley, 2011.
Edited by sheiko, 19 August 2012 - 12:29 PM.
#5
Posted 19 August 2012 - 12:20 PM
Pankaj:
As is usual, we get an “ASAP” request with a minimum of basic data and background information. Not even a decent sketch.
From what little information you have furnished, I can only tell you that you should stop the compressor and remove the discharge valves of the compression stage that is showing a high discharge temperature. If the discharge valves look OK, then the only reason for the high discharge would be that you have a double-acting piston in that compressor stage and the piston rings have failed or are leaking.
This is a typical problem with a reciprocating compressor that is not subject to routine, detailed valve and piston ring maintenance. I know, because I process designed, installed, and operated reciprocating compressors for many years – single-acting, double-acting, horizontal, vertical, in-tandem, balanced-opposed, electric motor driven, steam engine driven, gas engine driven, US and European manufacture, etc., etc. One of the outstanding clues that tell of a discharge valve failure to close is the burnt paint on the discharge valve covers. There is no need to calculate any "n" exponent on any of the stages. a reliable temperature gage that should be installed on all of the discharge lines should easily tell you where you stand with regards to the discharge temperature. In my days as production manager, I would merely run my hand over the discharge valve covers and with practice I could easily tell when the valves were running hotter than normal.
I am assuming this is an oil-lubricated cylinder hydrogen compressor and not a non-lube model. If it is a non-lube model, then the piston rings and riders are high suspects for failure. Your discharge temperatures on each stage of compression should be approximately 250 to 275 oF – assuming that this is a well-designed reciprocating compressor from an experienced and recognized manufacturer. Your temperature alarms on the discharge should be set around 300 oF and the compressor high temperature shutdown switch should be made at approximately 340 to 350 oF. I would not allow a reciprocating compressor (with oil lubricated cylinders) to operate beyond that level. A non-lubricated cylinder should alarm and trip out well below these levels of temperature.
I don’t know what you expect as help in an electronic file, but I think you are being naïve in believing that that will be of help. What you need to do is get “hands-on” on inspecting the mechanical and physical condition of your compressor valves and possibly also of your piston rings. That is where your present problems are located. (Of course, I am assuming that you are successfully intercooling between stages and not allowing hot suction hydrogen gas to enter any of the compression stages. Reciprocating compressors are simple, direct, and very easy to diagnose for operating problems. When simple and routine maintenance is applied to a well-designed compressor, the valves should easily last for 4,000 to 5,000 hours of continuous operation. And the cleaner and purer the gas, the longer the good operation.
Good luck.
As is usual, we get an “ASAP” request with a minimum of basic data and background information. Not even a decent sketch.
From what little information you have furnished, I can only tell you that you should stop the compressor and remove the discharge valves of the compression stage that is showing a high discharge temperature. If the discharge valves look OK, then the only reason for the high discharge would be that you have a double-acting piston in that compressor stage and the piston rings have failed or are leaking.
This is a typical problem with a reciprocating compressor that is not subject to routine, detailed valve and piston ring maintenance. I know, because I process designed, installed, and operated reciprocating compressors for many years – single-acting, double-acting, horizontal, vertical, in-tandem, balanced-opposed, electric motor driven, steam engine driven, gas engine driven, US and European manufacture, etc., etc. One of the outstanding clues that tell of a discharge valve failure to close is the burnt paint on the discharge valve covers. There is no need to calculate any "n" exponent on any of the stages. a reliable temperature gage that should be installed on all of the discharge lines should easily tell you where you stand with regards to the discharge temperature. In my days as production manager, I would merely run my hand over the discharge valve covers and with practice I could easily tell when the valves were running hotter than normal.
I am assuming this is an oil-lubricated cylinder hydrogen compressor and not a non-lube model. If it is a non-lube model, then the piston rings and riders are high suspects for failure. Your discharge temperatures on each stage of compression should be approximately 250 to 275 oF – assuming that this is a well-designed reciprocating compressor from an experienced and recognized manufacturer. Your temperature alarms on the discharge should be set around 300 oF and the compressor high temperature shutdown switch should be made at approximately 340 to 350 oF. I would not allow a reciprocating compressor (with oil lubricated cylinders) to operate beyond that level. A non-lubricated cylinder should alarm and trip out well below these levels of temperature.
I don’t know what you expect as help in an electronic file, but I think you are being naïve in believing that that will be of help. What you need to do is get “hands-on” on inspecting the mechanical and physical condition of your compressor valves and possibly also of your piston rings. That is where your present problems are located. (Of course, I am assuming that you are successfully intercooling between stages and not allowing hot suction hydrogen gas to enter any of the compression stages. Reciprocating compressors are simple, direct, and very easy to diagnose for operating problems. When simple and routine maintenance is applied to a well-designed compressor, the valves should easily last for 4,000 to 5,000 hours of continuous operation. And the cleaner and purer the gas, the longer the good operation.
Good luck.
#6
Posted 19 August 2012 - 12:39 PM
thnks admin, problem is solved nw..
And the data was suction pressure 22.09 kg/cm2,
temp 32.08 C
discharge pressure 49.06 kg/cm2,
Discharge temp 126.1 C and rising...
trip value of discharge temp. 153 c
And yeah ! It is double acting reciprocating compressor... Used here as hydrogen make up gas compressor...
And the data was suction pressure 22.09 kg/cm2,
temp 32.08 C
discharge pressure 49.06 kg/cm2,
Discharge temp 126.1 C and rising...
trip value of discharge temp. 153 c
And yeah ! It is double acting reciprocating compressor... Used here as hydrogen make up gas compressor...
#7
Posted 23 November 2012 - 12:33 PM
Unfortunately, this OP doesn't even share with us what the problem was and what was the solution.
One of the prime reasons for our Forum is the SHARING of experience and information between our engineering members for the benefit of all. In this case, this has been a "one-way" street; only one member profited.
One of the prime reasons for our Forum is the SHARING of experience and information between our engineering members for the benefit of all. In this case, this has been a "one-way" street; only one member profited.
Similar Topics
![]() Negative Pressure Discharge / Negative At High PointStarted by Guest_felderosfelder101021_* , 05 Jul 2025 |
|
![]() |
||
Compressor Suction DrumStarted by Guest_Lyne_* , 04 Jul 2025 |
|
![]() |
||
![]() Pipe Fluid Temperature Increase Due To Solar LoadingStarted by Guest_HeemeshJ126_* , 06 Apr 2016 |
|
![]()
|
||
Design Capacity Of Hydrogen Pullet During Hydroprocessing Units UpsetStarted by Guest_Divid Kelin_* , 18 Jun 2025 |
|
![]() |
||
Psv On Centrifugal Compressor DischargeStarted by Guest_Lyne_* , 10 Jun 2025 |
|
![]() |