|
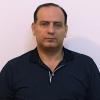
Atmospheric Tank Protection
#1
Posted 22 October 2012 - 02:01 AM
I am working in a project which scope is to design a new cylindical storage tank instead of existing concrete tank which both new/existing tanks are supplied by N2 blanketing.
Existing tank has two type of protection ssytem, first is Breather Valve for protection of tank agianst any malfunction in inbreathing/outbreathing regulator valves(PRV's) and second is relief valve for protection of tank against fire.
Following is existing tank design data:
Type = Rectangular Concrete
Length = 38.6 m , Width = 10.6 m, Height =2.33 m
Design Pressure = 50 mbarg
Design Temp. = -1/50°C
Breather Valve Set Pressure = 40 / 6 (VAC) mbarg (Control Valve Failure)
Relief Valve Set Pressure = 40 mbarg (Fire Case)
The existing Relief Valve is Large,weight loaded emergency vent type same as sketch shown in figure C.3, Annex C of API-2000, 6th Ed,2009.In Fgure C.5 of Annex C the overpressure for this type of venting device shown is around 80% which mean Relief Pressure(when relief valve is fully open) is about 72 mbarg which is above tank design pressure(50 mbarg).
1th question: How this type of RV can protect the tank during Fire Case with Relief Pres.>Design Pres.?
2nd question: Can I use the same protection philosphy for new cylindrecal tank.That means breather valve for PRV failure and relief valve for Fire Case.
3rd question: How I can find the required number and size for wight loaded emergency vent?
The new tank design condition should be as below:
Type: Cone Roof
Dia.= 15 m , Heigh =10 m
Design Pressure = 56 / 8.5 (VAC) mbarg
Design Temp. = 0/50 °C
I am waitng to hearing from you soon.
Best Regards
Afshin
#2
Posted 22 October 2012 - 12:35 PM
My answers to your questions:
1st-Your selection is wrong. With such design pressure you should select an EV with maximum 20% overpressure in full open position.
2nd-With same design pressure seems there would be no problem but with correct setting.
3rd-For specifying EV size and numbers you should just specify relevant relief load in fire case for vendor. Then following to vendor recommendation you will select from existing ones were already produced.
Fallah
#3
Posted 22 October 2012 - 01:46 PM
2: The pressure/vacuum valve should be used for normal venting and the emergency vent for emergency venting, such as fire exposure or PRV failure (see EN 14015 or ISO 28300/API 2000). The pressure/vacuum valve should be set such that the emergency vent remains closed during normal venting.
3: See 1.
#4
Posted 22 October 2012 - 07:07 PM
Afshin,
My answers to your questions:
1st-Your selection is wrong. With such design pressure you should select an EV with maximum 20% overpressure in full open position.
2nd-With same design pressure seems there would be no problem but with correct setting.
3rd-For specifying EV size and numbers you should just specify relevant relief load in fire case for vendor. Then following to vendor recommendation you will select from existing ones were already produced.
Fallah
Fallah
Thank you for your prompt reply.pls. find my replies as below:
1- As I mentioned in my post, this is existing design not my design for new tank .As per your idea existing design is wrong?
2- If for new tank I want to use type of RV same as existing tank (weight loaded), the only way to be sure RV is full open in the relief pressure is to set RV around 30 mbarg (Relief Press.= 54mbarg) which is same as set pressure for outbreathing PRV and also lower than breather valve set pressure (40 mbarg), which seems is not good design.
3- Actualy we are only involve in engineering and not Vendor Data Incorporation but I can tell our instrument to define the type of RV as per existing.
Afshin
Edited by Afshin, 23 October 2012 - 07:20 PM.
#5
Posted 22 October 2012 - 07:23 PM
1: Unless overpressures above design pressure are allowed by the design code the emergency vent should be set at a pressure below the design pressure of the tank. For example, EN 14015 does not allow any overpressure above design pressure (considering the design pressures i expect this is the design code of your new tank). In this case the emergency vent should be set such that the required capacity is reached at design pressure. Loads of vendors provide capacity curves/data on their websites which can be used for (preliminairy) sizing and to determinate the set pressure. Note that the overpressures required to achieve full lift / required capacity are vendor specific, some vendors have pressure vacuum valves and / or emergency vents which achieve full lift at 10% above set pressure.
2: The pressure/vacuum valve should be used for normal venting and the emergency vent for emergency venting, such as fire exposure or PRV failure (see EN 14015 or ISO 28300/API 2000). The pressure/vacuum valve should be set such that the emergency vent remains closed during normal venting.
3: See 1.
CMA010,
Thank you for yor fast reply.please see my answers as per below:
1- I think this type of RV with 10% overpressure are pilot type(Annex C of API 2000), which will be same as existing breather valve type.But as I mentioned before in existing design different type of emergency RV has been used, which is weigh loaded type.In this regards, could you give me some reference for vendor data which I can use in prelimenary sizing.
2- Can we size weight loaded RV which in case of maximum required load in fire case the RV still not be fully open.Let say vendor
can find RV opening percentage during full required load?
Afshin
#6
Posted 23 October 2012 - 04:57 AM
1- As I mentioned in my post, this is existing design not my design for new tank .As per your idea existing design is wrong?
2- If for new tank I want to use type of RV same as existing tank (weight loaded), the only way to be sure RV is full open in the relief pressure is to set RV around 30 mbarg (Relief Press.= 54mbarg) which is same as set pressure for outbreathing PRV and also lower than breather valve set pressure (40 mbarg), which seems is not good design.
3- Actualy we are only involve in engineering and not Vendor Data Incorporation but I can our instrument to define the type of RV as per existing.
Afshin,
1-EV set pressure is wrong. It should be set such that in full open position the tank pressure wouldn't pass design pressure.
2-For setting the opening pressure of safety devices on top of the tank you should have adequate margin between set points to avoid any interaction.
3-You specify the relief load and other data for vendor in relevant instrument data sheet. Then leave the issue for a qualified vendor to select proper one. Obviously vendor needs your confirmation on selected item.
Fallah
#7
Posted 23 October 2012 - 08:10 PM
Afshin,
1-EV set pressure is wrong. It should be set such that in full open position the tank pressure wouldn't pass design pressure.
2-For setting the opening pressure of safety devices on top of the tank you should have adequate margin between set points to avoid any interaction.
3-You specify the relief load and other data for vendor in relevant instrument data sheet. Then leave the issue for a qualified vendor to select proper one. Obviously vendor needs your confirmation on selected item.
Fallah
Dear Fallah,
Thank you for your fast reply.
1- If existing tank EV(RV) set pressure is wrong.What should be wright set pressure.Pls. refer to attachment which shown existing Tank protection arrangement.
2- Noted.
3- It seems RV set pressure related to type of EV(RV) which I need to select in this stage,in other hand in EV(RV) and Tank datasheet and also P&ID I need to show type of EV(RV). I can't wait for tank vendor to select type of EV(RV).
Afshin
Attached Files
Edited by Afshin, 23 October 2012 - 08:15 PM.
#8
Posted 24 October 2012 - 05:21 AM
1-If overpressure of the EV in full open position which is reported by vendor would be around 20%, then set pressure of EV equal to 40 mbar is OK. I mentioned it is wrong based on overpressure of 80%. If you specify the overpressure of EV then the set pressure can be determined easily.
2-OK
3-EV isn't so a complicated device which you would have problem to show it on the relevant documents! Also there is no need to indicate on e.g. the PID; if the EV is weight loaded cover type or spring loaded cover type or...
Fallah
#9
Posted 24 October 2012 - 08:26 PM
1- If I want following existing tank EV(RV) type , need to be weight loaded which overpressure is about 80%.
which set pressure can't be less than 40mbarg. for reason refer to attachment which showing the new tank normal venting and protection arrangement and set pressure. Also based on client standard the maximum Design Pressure for this type of tank maximum is 56 mbarg.This is source of confusion in the design.
2- Actually the P&ID symbole for weight loaded RV is different than other type of RV and in attached sketch to tank datasheet should be shown as possible with prelimenary size.
Afshin
Attached Files
Edited by Afshin, 24 October 2012 - 08:52 PM.
#10
Posted 25 October 2012 - 01:02 AM
I would focus on the discussion on the sketch of new tank, then my comments on the tank's safety divices are as follows:
1- Overpressure of the RV can be maximum 40% (40*1.4=56).
2-Set pressure of the BV and that of RV cannot be equal.
3-You might combine the BV and blanketing upper limit (PRV at 30 mbarg) just at the BV terminated to a single vent and set the BV at 30 mbarg. Then it would have dual function: Normal vent and Blanketing vent. By this you would remove any interaction between BV and RV. Of course this raw suggestion should be investigated in detail to be actually practical.
The size of the RV might be shown on PID as hold till finalizing the size with relevant vendor. For the symbol i don't think there would be any problem.
Fallah
Edited by fallah, 25 October 2012 - 01:02 AM.
#11
Posted 25 October 2012 - 02:27 AM
See my answers in your comments:
1- How we can limit the overpressure? Can we specidied overpressuer in RV datasheet then vendor doing
sizing based on this limitation.In case of Vendor select weigh loaded they need to increase the size to
meet ovepressure requirement in maximum required flow, please advise if I am wrong.
2- What will happen if we have same setting for BV and RV?
3- Is it allowed by code which tank normal out-breathing will be by safet device (Breather valve)?
is not rule which we need to have two level of safety protection?
Size is not very important I can follow your advise but I need to show RV with exact symbole in P&ID and datasheet.
Afshin
#12
Posted 25 October 2012 - 01:42 PM
1-Overpressure must be specified by vendor then you cannot do anything in this regard.
2-Interaction of two safety devices!
3-Code has nothing to say about this matter. Indeed, blanketing vent isn't considered as a layer of protection. My suggestion included combining a BV with blanketing vent due to a narrow tank's operating range.
Fallah
Edited by fallah, 25 October 2012 - 01:44 PM.
#13
Posted 28 October 2012 - 07:40 PM
1- Could you reply in 2nd part of my question.
2- OK.
3- I tried to say due to BV considered as final protection(Mechanical Device) we need a control device for pressure control (PRV).
In this regards, Instead of removal of outbreathing PRV can I increase EV(RV) set pressure to 45mbarg which is above BV relief
pressure (40 x1.1=44 mbarg).
Afshin
Edited by Afshin, 28 October 2012 - 07:40 PM.
#14
Posted 29 October 2012 - 01:36 AM
1- You can select a RV type to meet your requirement regarding overpressure value.
2- ...
3- Final protection would be EV(RV). You can keep EV(RV) set pressure at 40 mbarg and remove outbreathing PRV with lowering BV set point to 30 mbarg. Of course all suggested modifications should be investigated in depth and especially overpressure/blowdown of each devica should be considered.
Fallah
#15
Posted 30 October 2012 - 07:43 PM
What is your idea about my suggestion to increase EV(RV) set pressure to 45 mbarg?
Refer to section C.2.2 of API 2000, 6th ed.a larger EV(RV) need to be selected by vendor to meet required relief capacity in design pressure (56 mbarg).That means vendor need to size EV(RV) based on only 24% required overpressure for maximum relief capacity in fire case.
Afshin
Edited by Afshin, 30 October 2012 - 07:44 PM.
#16
Posted 31 October 2012 - 02:33 AM
As i mentioned previously, set pressure of an EV(RV) on one hand depends on tank design pressure (should be equal or lower than it) and on the other hand depends on EV overpressure. If design pressure of the tank would be 50 mbarg you can increase the set pressure of the EV to 45 mbarg just when the overpressure of the EV for full lift relief (reported by vendor) to be 10% of the EV set pressure.
Fallah
#17
Posted 02 November 2012 - 01:31 AM
Thank you for your complete answer.
Afshin
#18
Posted 12 November 2012 - 12:44 AM
I recevied a same recommendation from vendor which is removing of out-breathing PRV.
Hrere below is their reason for removing outbreathing PRV:
"Weight loaded Pressure and Vacuum Relief Valves are used for several purposes, one purpose is, acting as a low pressure safety valve to protect as the last barrier. A second purpose is acting as a breather valve. A weight loaded valve is quite tight, in case pressures, lower 90 % of the set pressure, the leakage rate of a Protego 6" valve is smaller than 0.05 liter per minute (max. allowable leakage accord. API is 0.23 lpm). So there should be no technical reason to prefer a control valve."
For me Breather Valve just considered as final protection when one of the inbretahing/outbreathing PRV's failing
Still this is not solve for me why we don't need this PRV and why we let tank to outbreathing through Bretaher Valve instead of PRV.
Another question for me is leakage of BV.From above statement we can say when pressure is below 36 mbarg N2 lost is 3 lit/hr (26 m3/year). Why we need this amount of N2 lost?
With above information, are you think still we need delete outbreathing PRV?
Afshin
Edited by Afshin, 12 November 2012 - 12:46 AM.
#19
Posted 12 November 2012 - 02:03 AM
Please refer again to my previous post (No. 10). Indeed, we don't need to N2 loss! The leakage through a breather valve in the pressures near its set point is natural, but it is better to be as minimum as possible. It may differ from one vendor to another.
Fallah
#20
Posted 12 November 2012 - 03:15 AM
The mentioned leakage refer to noraml tank pressure.For pressure above 36 mbarg as you mentioned N2 loss will be higher.
In this regards, what is your idea about my first question?
I also like to know other forum members idea with any experince in this regards.
Afshin
Edited by Afshin, 12 November 2012 - 03:19 AM.
#21
Posted 12 November 2012 - 04:03 AM
Fallah,
The mentioned leakage refer to noraml tank pressure.For pressure above 36 mbarg as you mentioned N2 loss will be higher.
In this regards, what is your idea about my first question?
I also like to know other forum members idea with any experince in this regards.
Afshin
Afshin,
Yes, obviously for pressures above 90% of the set pressure the leakage rate would be higher, but the tank operating pressure rarely reaches to such point and if the tank had been properly designed there would be no concern regarding the N2 leakage through the valve.
About your first question as i mentioned refer to post No. 10.
Fallah
#22
Posted 12 November 2012 - 09:33 PM
During tank filling by upstream pump or N2 expansion due to increase in Amb. temperature tank operating pressure can increase to BV set pressure when there is no any pressure control device (e.g. outbreathing PRV).
Could you advise how tank pressure can't reach to BV set pressure (Let say 30 mbarg as per your recommendation) by properly design of tank?
Afshin
Edited by Afshin, 12 November 2012 - 09:33 PM.
#23
Posted 13 November 2012 - 01:56 AM
I did recommend combination of blanketing vent and BV could be a solution to avoid interaction between these two valves operation due to low difference between their set points. If you can set these two valves such that there would be no interaction, you can ignore my recommendation. But if you have to combine them, it might tank operating pressure increase to BV set pressure during tank filling and there would be no problem because in this situation BV acts as blanketing vent while keeps its potential to act as normal vent as well.
Fallah
#24
Posted 13 November 2012 - 04:15 AM
I did recommend combination of blanketing vent and BV could be a solution to avoid interaction between these two valves operation due to low difference between their set points. If you can set these two valves such that there would be no interaction, you can ignore my recommendation.
There is 10 mbarg margin between out-breathing PRV and BV set pressures which set at 30 and 40 mbarg respectively. The only thing I can do is increasing of RV set pressure to 45 mbarg to avoid any intreaction between RV and BV. The vendor recommendation for RV is simple manhole type with overpressure of 10% which means RV relief pressure still is less than tank design pressure.The only problem is, this type of RV only can support set pressure up to 40 mbarg and above this range RV will be more expensive.
But if you have to combine them, it might tank operating pressure increase to BV set pressure during tank filling and there would be no problem because in this situation BV acts as blanketing vent while keeps its potential to act as normal vent as well.
In this case the BV can set in 30 mbarg and RV in 40 mbarg, but still the nitrogen can leak through BV during tank filling or increasing in ambient temperature.
Pls correct me if my understanding is wrong.
Afshin
Edited by Afshin, 13 November 2012 - 04:24 AM.
#25
Posted 13 November 2012 - 04:39 AM
If you want to keep both the blanketing vent and BV separated, you have to increase the RV set point. In this way, you might choose that RV type can be applied for set pressure of 45 mbarg with maximum 10% overpressure at full open.
Reaching to BV set pressure during tank filling or increase in ambient temperature depends on the normal out-breathing rate due to such events. Then it might or might not be reached. If it reaches N2 loss from BV would be occured.
Fallah
Similar Topics
![]() Steam Sparger In Atmospheric Water TankStarted by Guest_owe_* , 16 May 2025 |
|
![]() |
||
![]() Phosphoric Acid 56% Tank LiningStarted by Guest_Phosphoric123_* , 20 Apr 2025 |
|
![]() |
||
![]() Tank Inlet Diffuser LengthStarted by Guest_RAFAELDAVE_0752_* , 08 Apr 2025 |
|
![]() |
||
Discussion - Predict Storage Tank Heat Transfer Precisely By Jimmy D KStarted by Guest_raj shekhar_* , 25 Mar 2025 |
|
![]() |
||
Tank Filing TimeStarted by Guest_not_mikhail_* , 17 Mar 2025 |
|
![]() |