In the vacuum furnace we usually maintain a coil outlet temperature of 386 degrees for reduced crude from CDU. Why cracking not happening here.?
|
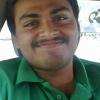
Cracking Temperature Of Hcs
Started by hari2020pkr, Oct 25 2012 10:16 PM
3 replies to this topic
Share this topic:
#1
Posted 25 October 2012 - 10:16 PM
#2
Posted 25 October 2012 - 11:00 PM
A bit does.
Bobby
Bobby
#3
Posted 26 October 2012 - 10:27 PM
but usually what is the usual cracking temp of RCO
#4
Posted 27 October 2012 - 10:35 AM
Bottoms of atmospheric columns are generally kept below about 700 F (371 C) because around that temperature thermal cracking begins to increase with coke formers and metals getting into the gas oil. By distilling the bottoms again in a vacuum, additional gas oils can be recovered and thermal cracking kept to a minimum. Flash zone temperatures in a vacuum column are generally a bit higher, but not by much. Cracking increases with the amount of time the material is hot. The compromise is to allow some cracking and recover the optimum quantity and quality of gas oils. 386 C is not an abnormal furnace outlet temperature. But just because you operate at 386 C does not mean that absolutely no cracking occurs.
You can find where cracking becomes noticeable by getting the lab to run a distillation and then plot the results. Around 700 F or so you should see where the curve begins to not follow the expected extrapolation of boiling points and looks like it is trying to level off. The change in slope is due to cracking.
Remember that you are working with a stream that contains thousands of components. Some will be more prone to cracking than others. Not all components which boil at the same temperature are alike. It is convenient to think of crude composition in terms of stable pseudocomponents of a certain boiling point range, but in reality you will have a different actual composition in your products than you do in your feed due to cracking and polymerization. This is the reason that when simulating the vacuum column distillation, it is best practice to force the feed composition to be the sum of the column products. If you were to start with the feed being the measured topped crude, then the simulated products would never match the real world.
You can find where cracking becomes noticeable by getting the lab to run a distillation and then plot the results. Around 700 F or so you should see where the curve begins to not follow the expected extrapolation of boiling points and looks like it is trying to level off. The change in slope is due to cracking.
Remember that you are working with a stream that contains thousands of components. Some will be more prone to cracking than others. Not all components which boil at the same temperature are alike. It is convenient to think of crude composition in terms of stable pseudocomponents of a certain boiling point range, but in reality you will have a different actual composition in your products than you do in your feed due to cracking and polymerization. This is the reason that when simulating the vacuum column distillation, it is best practice to force the feed composition to be the sum of the column products. If you were to start with the feed being the measured topped crude, then the simulated products would never match the real world.
Similar Topics
![]() Pipe Fluid Temperature Increase Due To Solar LoadingStarted by Guest_HeemeshJ126_* , 06 Apr 2016 |
|
![]()
|
||
![]() Distillation Tower Top And Bottom Temperature And PressureStarted by Guest_student55_* , 27 Mar 2016 |
|
![]()
|
||
![]() High Stack Temperature In Ccr HeatersStarted by Guest_viba0124_* , 30 Nov 2024 |
|
![]() |
||
Cross Over Temperature In Countercurrent Heat ExchangerStarted by Guest_panoska_* , 18 Feb 2025 |
|
![]() |
||
Flowing Temperature- PsvStarted by Guest_stu_* , 17 Feb 2025 |
|
![]() |