|
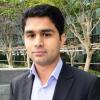
How To Calculate Time Required To Reach Compressor Discharge Temp At 1
Started by ilyas_khokhar, Dec 10 2012 11:12 PM
11 replies to this topic
Share this topic:
#1
Posted 10 December 2012 - 11:12 PM
hello, please advise how can i calculate the time required to reach compressor discharge temp at 150 C.
While compressor is centrifugal driven by fixed speed motor and fluid is air at atm conditions. thanks.
While compressor is centrifugal driven by fixed speed motor and fluid is air at atm conditions. thanks.
#2
Posted 10 December 2012 - 11:19 PM
Ilyas,
You can calculate the work done by compressor and then equate it to M*Cp*dT.
Experts, please correct me in case it is wrong.
Regards,
Arpit
You can calculate the work done by compressor and then equate it to M*Cp*dT.
Experts, please correct me in case it is wrong.
Regards,
Arpit
#3
Posted 11 December 2012 - 12:18 AM
Thanks Arpit,
But I need to calculate the time.
Work = M*Cp*dT can't give this information.
May be I need to develop dynamic simulation model?
Don't know..
But I need to calculate the time.
Work = M*Cp*dT can't give this information.
May be I need to develop dynamic simulation model?
Don't know..
#4
Posted 11 December 2012 - 03:30 AM
Don't know if I am correct but the answer may be derived as:
mCpT|in= mCpT|out + d(MCpT)/dt - Power
Here m = mass flow rate
M = mass accumulated in the compressor (This can be calculated by knowing the internal volume and using the PVr = const)
Power= compressor power
Please consult some experts to verify this.
Regards
Arpit
mCpT|in= mCpT|out + d(MCpT)/dt - Power
Here m = mass flow rate
M = mass accumulated in the compressor (This can be calculated by knowing the internal volume and using the PVr = const)
Power= compressor power
Please consult some experts to verify this.
Regards
Arpit
#5
Posted 11 December 2012 - 07:10 AM
Ilyas:
Why are you concerned with the time requirement for you to visualize the discharge in a centrifugal compressor reach a pre-determined temperature? I have operated compressors – both Positive displacement and centrifugal for years and never paid attention to that. I am curious about your concern.
The centrifugal compressor will achieve a discharge temperature that you can see and that temperature will depend on the gas, the compression ratio for that stage, the suction temperature, the heat capacitance of the compressor’s mass and all the connected hardware – including the piping. When a compressor achieves its operating speed – which is a matter of a minute or so, it starts immediately to generate the expected polytropic discharge temperature. However, there are heat transfers taking place continuously in and around the compressor: these are conduction, convection, and a little radiation. The majority of the heat of compression being transmitted is due to conduction. When the operation reaches steady state, you will have steady heat losses and this will be reflected in your discharge temperature.
Why are you expecting 150 oC as the discharge temperature? That seems like a very high discharge temperature, even for a centrifugal unit. Please explain what it is that you are trying to accomplish or observe. Unless you can calculate the steady state heat loss, you can’t calculate discharge temperature. And even if you did, it would be theoretical and not actual. What you will see in the field will be different – by as much a 10 to 20% perhaps.
If you furnish an explanation of what I ask, perhaps we can discuss this further.
Why are you concerned with the time requirement for you to visualize the discharge in a centrifugal compressor reach a pre-determined temperature? I have operated compressors – both Positive displacement and centrifugal for years and never paid attention to that. I am curious about your concern.
The centrifugal compressor will achieve a discharge temperature that you can see and that temperature will depend on the gas, the compression ratio for that stage, the suction temperature, the heat capacitance of the compressor’s mass and all the connected hardware – including the piping. When a compressor achieves its operating speed – which is a matter of a minute or so, it starts immediately to generate the expected polytropic discharge temperature. However, there are heat transfers taking place continuously in and around the compressor: these are conduction, convection, and a little radiation. The majority of the heat of compression being transmitted is due to conduction. When the operation reaches steady state, you will have steady heat losses and this will be reflected in your discharge temperature.
Why are you expecting 150 oC as the discharge temperature? That seems like a very high discharge temperature, even for a centrifugal unit. Please explain what it is that you are trying to accomplish or observe. Unless you can calculate the steady state heat loss, you can’t calculate discharge temperature. And even if you did, it would be theoretical and not actual. What you will see in the field will be different – by as much a 10 to 20% perhaps.
If you furnish an explanation of what I ask, perhaps we can discuss this further.
#6
Posted 11 December 2012 - 11:43 PM
Dear Mr. Art,
Thanks for your reply.
Here I explain:
There is a hydrogen booster compressor. I need to perform its test run with air as hydrogen is not yet available.
As you mentioned discharge temperature is influenced by the molecular weight. Therefore in air case, (according to HYSYS results), discharge temperature increases to about 400 C, if operated at same capacity as hydrogen. Whereas the design temperature of the hydrogen network is 150 C.
So it is necessary to calculate the time for compressor to reach at 150 C discharge temp and analyze whether it is feasible or not to run H2 booster compressor on air.
Thanks and regards..
Thanks for your reply.
Here I explain:
There is a hydrogen booster compressor. I need to perform its test run with air as hydrogen is not yet available.
As you mentioned discharge temperature is influenced by the molecular weight. Therefore in air case, (according to HYSYS results), discharge temperature increases to about 400 C, if operated at same capacity as hydrogen. Whereas the design temperature of the hydrogen network is 150 C.
So it is necessary to calculate the time for compressor to reach at 150 C discharge temp and analyze whether it is feasible or not to run H2 booster compressor on air.
Thanks and regards..
#7
Posted 12 December 2012 - 02:20 AM
Ilyas,
The formula for a stage discharge temperature for a centrifugal compressor is:
T2 = T1*(P2 / P1)n-1/n
where:
T2 = stage discharge temperature, K
T1 = stage suction temperature, K
P2 = stage discharge pressure, kPaa
P1 = stage suction pressure, kPaa
n = polytropic exponent
(n - 1) / n = (κ - 1) / κ*ηpoly
where:
κ = specific heat ratio = Cp / Cv (1.4 for air and 1.407 for hydrogen)
ηpoly = polytropic efficiency (normally for large volumetric capacity centrifugal compressors it ranges from 75 to 80% (0.75 to 0.80))
From above it is clear that the discharge temperature is dependent on the pressure ratio (P2 / P1), the specific heat ratio κ and the polytropic efficiency.
If you compare the specific heat ratio of air and hydrogen they are quite similar. Considering that that the polytropic efficiency is not effected much, than the theoretical discharge temperature for a fixed pressure ratio for both hydrogen and air will be quite similar.
When I check your case considering a pressure ratio of 3.33 and a suction temperature of 40°C, I get almost the same discharge temperature of 216°C for both hydrogen and air.
To conclude, the discharge temperature is not changing much between hydrogen and air but the power required for the same pressure ratio for hydrogen would be much higher compared to air. This is evident from the fact that the compressor inlet volume flow for hydrogen for a unit mass flow rate (1 kg/h) at 15°C and atmospheric pressure (101.325 kPaa) is 5.75 m3/h whereas for air for a unit mas flow rate it would be 0.40 m3/h. This is a 14-fold increase in inlet volume flow rate for hydrogen compared to air. The reason is obvious - the large difference in the molar mass of hydrogen and air (2.015 versus 28.97). Notice that the volume flow rate increase for hydrogen is in the same ratio as the ratio of the molar masses of air to hydrogen.
Hope this helps.
Regards,
Ankur.
The formula for a stage discharge temperature for a centrifugal compressor is:
T2 = T1*(P2 / P1)n-1/n
where:
T2 = stage discharge temperature, K
T1 = stage suction temperature, K
P2 = stage discharge pressure, kPaa
P1 = stage suction pressure, kPaa
n = polytropic exponent
(n - 1) / n = (κ - 1) / κ*ηpoly
where:
κ = specific heat ratio = Cp / Cv (1.4 for air and 1.407 for hydrogen)
ηpoly = polytropic efficiency (normally for large volumetric capacity centrifugal compressors it ranges from 75 to 80% (0.75 to 0.80))
From above it is clear that the discharge temperature is dependent on the pressure ratio (P2 / P1), the specific heat ratio κ and the polytropic efficiency.
If you compare the specific heat ratio of air and hydrogen they are quite similar. Considering that that the polytropic efficiency is not effected much, than the theoretical discharge temperature for a fixed pressure ratio for both hydrogen and air will be quite similar.
When I check your case considering a pressure ratio of 3.33 and a suction temperature of 40°C, I get almost the same discharge temperature of 216°C for both hydrogen and air.
To conclude, the discharge temperature is not changing much between hydrogen and air but the power required for the same pressure ratio for hydrogen would be much higher compared to air. This is evident from the fact that the compressor inlet volume flow for hydrogen for a unit mass flow rate (1 kg/h) at 15°C and atmospheric pressure (101.325 kPaa) is 5.75 m3/h whereas for air for a unit mas flow rate it would be 0.40 m3/h. This is a 14-fold increase in inlet volume flow rate for hydrogen compared to air. The reason is obvious - the large difference in the molar mass of hydrogen and air (2.015 versus 28.97). Notice that the volume flow rate increase for hydrogen is in the same ratio as the ratio of the molar masses of air to hydrogen.
Hope this helps.
Regards,
Ankur.
#8
Posted 13 December 2012 - 05:48 AM
Dear Ankur Sir,
Many thanks for your direct and clear reply. I also revised my calculations. Results were the same as you explained.
One more question I want to ask is:
How to calculate surge flow rate?
In my case compressor vendor has provided only one estimated performance curve (for Hydrogen gas).
But I want to calculate surge flow rate in air case.
I tried to use Multiple MW curves option in Hysys but its not working. I guess Hysys needs two/three or more curves as a reference to regress the performance curve for a different Mol. Wt. gas. (I am not sure).
And the problem is driver for the compressor is a fixed speed motor. I was thinking that it is not possible for a fixed speed motor to have performance curves at different RPMs therefore vendor provided only one performance curve at specific RPM.
Am I right? or flawed..
Anyway please recommend and guide about how I can calculate surge flow rate for air case.
Thanks again..
Kind regards,
ilyas
Many thanks for your direct and clear reply. I also revised my calculations. Results were the same as you explained.
One more question I want to ask is:
How to calculate surge flow rate?
In my case compressor vendor has provided only one estimated performance curve (for Hydrogen gas).
But I want to calculate surge flow rate in air case.
I tried to use Multiple MW curves option in Hysys but its not working. I guess Hysys needs two/three or more curves as a reference to regress the performance curve for a different Mol. Wt. gas. (I am not sure).
And the problem is driver for the compressor is a fixed speed motor. I was thinking that it is not possible for a fixed speed motor to have performance curves at different RPMs therefore vendor provided only one performance curve at specific RPM.
Am I right? or flawed..
Anyway please recommend and guide about how I can calculate surge flow rate for air case.
Thanks again..
Kind regards,
ilyas
#9
Posted 13 December 2012 - 08:11 AM
may I suggest ASME PTC10 and/or any good textbook discussing this matter?
You should contact the manufacturer to be sure that your centrifugal compressor designed for hydrogen (Mw 2) can be tested with air (Mw 28),
there are many mechanical limits (including power required) to verify before to go on,
I would be very prudent about takingt the result of a simulation based on uncertain inputs (and the same considering the limts of these models).
You should contact the manufacturer to be sure that your centrifugal compressor designed for hydrogen (Mw 2) can be tested with air (Mw 28),
there are many mechanical limits (including power required) to verify before to go on,
I would be very prudent about takingt the result of a simulation based on uncertain inputs (and the same considering the limts of these models).
#10
Posted 14 December 2012 - 05:36 AM
Yes. The final decision will be made by vendor.
But before that i need to calculate preliminary data as you mentioed duty, etc.
I have looked into Asme Ptc10. Thanks for suggesting. It is a more rigorous experiment based standard.
Whereas what i am looking for is some shortcut analytical/empirical formulation from which I can calculate the estimated surge flow rate. Plz share your thoughts about it also.
Thanks and regards.
But before that i need to calculate preliminary data as you mentioed duty, etc.
I have looked into Asme Ptc10. Thanks for suggesting. It is a more rigorous experiment based standard.
Whereas what i am looking for is some shortcut analytical/empirical formulation from which I can calculate the estimated surge flow rate. Plz share your thoughts about it also.
Thanks and regards.
#11
Posted 16 January 2013 - 12:52 PM
Ilyas,
what I have done in my compressor commission duing startup air sep plants, start compressor do not load compressor, perform surge test
do that compressor and all valves in manual mode. surge test can be done at IGV's 25%,40%,50%,75% etc.
allow temp and vorbrtaion to stablizxze for 20 min, and then slowy reduce blowoff vavle s1% to 0.25% while obersving trents and screen on PLC. observe running apms, vibrations, and temp and pressure,recoed running apms and discharge pressure,while instability in vibraion and current observed ,leave comprssor in surge will cause compressor trip,operators must be prepare of rapidly open blow-off vavle. repere slowly moving back to surge condition,with record values and plot surge line, raise to surge, I have attached one of my exaple of ploting surge curve.
hope this will help you understand more on compressor sure tests and surge line plotting.
Alpen
what I have done in my compressor commission duing startup air sep plants, start compressor do not load compressor, perform surge test
do that compressor and all valves in manual mode. surge test can be done at IGV's 25%,40%,50%,75% etc.
allow temp and vorbrtaion to stablizxze for 20 min, and then slowy reduce blowoff vavle s1% to 0.25% while obersving trents and screen on PLC. observe running apms, vibrations, and temp and pressure,recoed running apms and discharge pressure,while instability in vibraion and current observed ,leave comprssor in surge will cause compressor trip,operators must be prepare of rapidly open blow-off vavle. repere slowly moving back to surge condition,with record values and plot surge line, raise to surge, I have attached one of my exaple of ploting surge curve.
hope this will help you understand more on compressor sure tests and surge line plotting.
Alpen
Attached Files
#12
Posted 16 January 2013 - 01:19 PM
Alpen,
Can you check what you have written? To me and I am sure to anybody who is reading your post it does not convey any meaning. Besides wrongly spelling most words, it is littered with grammatical errors and fails to get across what you want to say.
Can you be more careful about what you write? I don't claim to be an anglophile but such trashing of the English language makes me cringe.
Regards,
Ankur.
Can you check what you have written? To me and I am sure to anybody who is reading your post it does not convey any meaning. Besides wrongly spelling most words, it is littered with grammatical errors and fails to get across what you want to say.
Can you be more careful about what you write? I don't claim to be an anglophile but such trashing of the English language makes me cringe.
Regards,
Ankur.
Similar Topics
![]() Hysys Expander/compressor Input Using Dimensionless CurveStarted by Guest_Alfreedo_* , 21 Apr 2025 |
|
![]() |
||
Tank Filing TimeStarted by Guest_not_mikhail_* , 17 Mar 2025 |
|
![]() |
||
Centriugal CompressorStarted by Guest_Rahimzadeh_* , 02 Mar 2025 |
|
![]() |
||
Physical Properties Of Liquid Discharge For Kod SizingStarted by Guest_mahmooddalvi09_* , 26 Feb 2025 |
|
![]() |
||
Pulsation Device In Reciprocating CompressorStarted by Guest_zaidanamir_* , 17 Feb 2025 |
|
![]() |