|

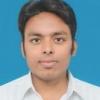
Heat Exchanger
#1
Posted 13 November 2018 - 12:36 AM
#2
Posted 13 November 2018 - 07:37 PM
You should rate the exchanger with a proper software.
#3
Posted 13 November 2018 - 11:25 PM
You should rate the exchanger with a proper software.
The screenshot i have attached is from HTRI and from both option i am getting the acceptable design. I think this is the best software for heat exchanger.
Please go through my question again. what i am asking is basically a doubt which i can get from experience personal only.
#4
Posted 14 November 2018 - 03:24 PM
Experience is something you do not get until just after you need it. You should rate the exchanger with a proper software. Did you use the appropriate inputs? Did you interpret the results correctly? We have no way of knowing.
It is nice when you can get someone to check your work, but when that is not feasible, you just have to make sure you can defend your conclusion, then call the shot and take the consequences. It is certainly possible that the exchanger is good for the new conditions. If I were reviewing your work, the following checks come to mind:
- Is there any phase change for the fluid?
- Is the heat exchange in the film boiling region?
- Are the velocities acceptable?
- Will the pressure drop work in the hydraulic system?
- Is tube vibration a problem?
- Is the differential thermal expansion accounted for in a fixed tubesheet design?
- Is the pressure relief properly designed?
#5
Posted 15 November 2018 - 03:20 AM
Experience is something you do not get until just after you need it. You should rate the exchanger with a proper software.
I know that i will not get experience when i need it but can't i ask the experience personal if i have any doubt?. I have already mention i used HTRI software.
Did you use the appropriate inputs? Did you interpret the results correctly? We have no way of knowing.
Yes i used all the inputs correctly for the "DESIGN-1" (attached screenshot). I am getting the result from both way (DESGN-1 AND DESIGN-2). I can't attached the whole calculation. It will be illegal i think.
It is nice when you can get someone to check your work, but when that is not feasible, you just have to make sure you can defend your conclusion, then call the shot and take the consequences. It is certainly possible that the exchanger is good for the new conditions. If I were reviewing your work, the following checks come to mind:
- Is there any phase change for the fluid?
please the attached. from that it can be find out that phase change is taking place or not.
- Is the heat exchange in the film boiling region?
no boiling
- Are the velocities acceptable?
yes velocity is acceptable
- Will the pressure drop work in the hydraulic system?
for the "DESIGN-2" tube side pressure drop allowed is 0.7kg.cm2 and i am getting 0.68kg/cm2. Is it acceptable or not.
- Is tube vibration a problem?
i am using impingement plate.
- Is the differential thermal expansion accounted for in a fixed tubesheet design?
its u-tube. for tubesheet we have considered for the expansion.
- Is the pressure relief properly designed?
not required for heat exchanger vessel.
Edited by navneet2109, 15 November 2018 - 03:22 AM.
#6
Posted 16 November 2018 - 09:29 AM
Here are my two cents:
1) There are various glycols available, we don't know which one you are using. Maybe you should search some literature with respect to the glycol you are using, this will help you to check whether the glycol is o.k at 60 degC or it can undergo thermal degradation.
2) Temperature difference across the Heat Ex is solely governed by the process.
3) The Client wants you to increase the outlet temperature of one fluid, by keeping the area constant. That can be done by one of the way you have already tried.
#7
Posted 16 November 2018 - 10:56 AM
Here are my two cents:
Your two cents are more valuable.
1) There are various glycols available, we don't know which one you are using. Maybe you should search some literature with respect to the glycol you are using, this will help you to check whether the glycol is o.k at 60 degC or it can undergo thermal degradation.
I will definitely check glycol properties for 60degC.
2) Temperature difference across the Heat Ex is solely governed by the process.
You are correct.
3) The Client wants you to increase the outlet temperature of one fluid, by keeping the area constant. That can be done by one of the way you have already tried.
By this sentence I have gain little bit confidence that it can be done. My main concern was only that we can go of 20 degC difference.
I am very grateful to you for answering after understanding the points.
regards
Edited by navneet2109, 16 November 2018 - 10:58 AM.
Similar Topics
Steam Pressure In Heat ExchangerStarted by Guest_mvanrijnbach_* , 15 Apr 2025 |
|
![]() |
||
Heat Exchanger Steam FlowStarted by Guest_aliebrahem17_* , 25 Nov 2024 |
|
![]() |
||
Discussion - Predict Storage Tank Heat Transfer Precisely By Jimmy D KStarted by Guest_raj shekhar_* , 25 Mar 2025 |
|
![]() |
||
Cross Over Temperature In Countercurrent Heat ExchangerStarted by Guest_panoska_* , 18 Feb 2025 |
|
![]() |
||
Aspen Hysys - Blowdown Utility Heat Flux MethodStarted by Guest_yuvi.ardekar1999@gmail.com_* , 27 Feb 2025 |
|
![]() |