|

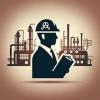
Low Velocity Problem Of Fluid In Hairpin Heat Exchangers
#1
Posted 16 January 2023 - 11:43 AM
Because the capacities and flow rates are low the surface area of heat transfer is very low, less than 10 square meters and less than 0.1 megawatt duty.
So I decided to use hairpin or double pipe heat exchangers.
My main concern and problem is low velocity while my fluid is dirty with 0.000344 m2.k/w fouling resistance
I designed both cases, double pipe is ok but usually needs 4-8 shells in series with more than 3.65 m long (up to 6.09 m)
So my boss insist using harpin heat exchangers.
Harpin cases results lighter heat exchanger in one shell but my problem is very low velocity in shell and tube side from 0.09 m/s to 0.2 m/s.
Shell diameter is usually from 4 inch to 6 inch, mainly 5 inch. So i haven't many options to adjust them to reach higher velocities.
So I wanted to know are these current velocities could cuase very serious problems in operation which make it impractical and is there any solution to solve this problem.
Consider that we can't finned tubes and pipes.
The second question, I tried to increase dp of shell and velocity by adding baffles and increase crosposses but it results 40 to 70 crosspasses for 3.65 to 6.09 tube length and 4 to 6 inch shell diameter for 0.3 t0 0.5 bar pressure loss.
Is this usuall to use these high number of crosspasses?
In some of my runs in htri I faced with this message that my baffle cut is higher than maximum calculated baffle cut for current layout of heat exchanger, but I haven't any rule for this i know recommended baffle cut is 15-45 and mainly 25-35 percent.
But I haven't seen anything about maximum baffle cut related to the layout of exchanger, anyone knows reason of this message?
Thanks in advance, hope you could help me.
#2
Posted 16 January 2023 - 01:08 PM
A hairpin exchanger is reasonable for that surface area. You do not necessarily have to perform the detail design of the heat exchanger. I suggest you develop a thermal performance data sheet describing your fluids and requirements and constraints. Send the data sheet to your hairpin exchanger vendor and ask them to design it to your specifications. Review their resulting design and correct what is unsuitable before ordering.
#3
Posted 16 January 2023 - 03:14 PM
A hairpin exchanger is reasonable for that surface area. You do not necessarily have to perform the detail design of the heat exchanger. I suggest you develop a thermal performance data sheet describing your fluids and requirements and constraints. Send the data sheet to your hairpin exchanger vendor and ask them to design it to your specifications. Review their resulting design and correct what is unsuitable before ordering.
Thank you Pilesar
Do you have any idea about measurements which can be useful for increase of fluid velocity inside shell?
#4
Posted 16 January 2023 - 05:44 PM
I don't know your fluids, the temperatures, the phase changes, or much at all about your system. Shell-side velocity has limited adjustment. If the double pipe exchanger barely meets your shell side velocity needs, then multitube exchanger will have lower shell side velocity. Heat exchanger design is a compromise. A hairpin may not be able to satisfy all your requirements. Another heat transfer option may be needed. There are non-tube options also such as spiral and plate and frame. I don't know if your boss is right or not in this case, but I do know that bosses are not always right -- especially when they have not actually done the calculations.
#6
Posted 25 January 2023 - 06:37 AM
Plate heat exchangers are suitable for clean services, spiral for less than 10 bar operational pressure.hi, what about other technology? let say plate heat exchanger? Btw we don't have any information about the materials, the flow rate, the temperature profile... Only guess. Breizh
Flow rates are less than 5 tons/hour for hydrocarbon such as benzene and toluene for temperature reduction from 75 and 170 to 45 centigrade degree with cooling water supply at 35 centigrade degree and cwr at 45.
Reply to this topic

Similar Topics
![]() Recommended Fluid VelocityStarted by Guest_crn_* , 16 Apr 2025 |
|
![]() |
||
Steam Pressure In Heat ExchangerStarted by Guest_mvanrijnbach_* , 15 Apr 2025 |
|
![]() |
||
Heat Exchanger Steam FlowStarted by Guest_aliebrahem17_* , 25 Nov 2024 |
|
![]() |
||
![]() Supercritical Fluid Flowrate - He Tube RuptureStarted by Guest_flarewolf_* , 07 Apr 2025 |
|
![]() |
||
Discussion - Predict Storage Tank Heat Transfer Precisely By Jimmy D KStarted by Guest_raj shekhar_* , 25 Mar 2025 |
|
![]() |