|
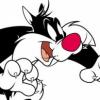
Crude Distillation Units
Started by Zauberberg, Dec 05 2006 05:05 PM
10 replies to this topic
Share this topic:
#1
Posted 05 December 2006 - 05:05 PM
Hello to all members,
I've posted this question at Eng-Tips some time ago, and there was only one - useful, but very brief answer.
From the first start-up of Crude Unit, heat exchangers in the so-called "hot preheat train" (upstream of process heater and downstream of desalters/dehydrators) experience intensive and very progressive fouling. In these exchangers, crude is placed on the shellside, while atmospheric residue flows through the tubes.
Since in all other heat exchangers in CDU crude is placed on the tubeside, I wonder why the designer had choosen this particular configuration in the hot preheat train.
Atmospheric residue does not have any specific hydraulic demands - it has sufficient pressure head (delivered by the pump) to overcome all resistances before entering vacuum unit feed drum. Even if it was placed on the shellside instead of crude oil, for the given fouling rate, calculations show that we could easilly achieve 4 year run-length without shutting down the unit and cleaning the exchangers - as far as process hydraulic is concerned.
So my question is: what do you think about changing flow pattern through these exchangers and place the crude oil on the tubeside? Did you have any similar experiences? Most often, similar units around the world, faced with similar fouling/hydraulic problems, undergo revamp which consists of placing flash drum/column in the middle of preheat train, with the new booster pump. I do not consider it as an attractive option at the moment - it is very expensive, and it has some drawbacks (flash drum foaming, main column products degradation etc.)
Placing crude on the tubeside: the initial pressure drop through the hot preheat train, in such case, would be higher, but I think the rate of fouling/pressure drop building will be much lower, because of velocity profiles; so when the terminal tube velocity is reached, no significant fouling can take place from the crude-side.
Process heater is available to deliver additional duty if heat transfer rate drops (for crude deltaT = 25C = start of run - end of run), because of eventual fouling from the atmospheric residue side.
In most crude units, crude oil is placed on the shell side (in the hot preheat train), and they all suffer from the same disease: crude heater inlet pass vaporization, caused by big pressure drop through the train. So why, then, all designers always place the crude oil on the shellside? Do you have any hints on this?
I've posted this question at Eng-Tips some time ago, and there was only one - useful, but very brief answer.
From the first start-up of Crude Unit, heat exchangers in the so-called "hot preheat train" (upstream of process heater and downstream of desalters/dehydrators) experience intensive and very progressive fouling. In these exchangers, crude is placed on the shellside, while atmospheric residue flows through the tubes.
Since in all other heat exchangers in CDU crude is placed on the tubeside, I wonder why the designer had choosen this particular configuration in the hot preheat train.
Atmospheric residue does not have any specific hydraulic demands - it has sufficient pressure head (delivered by the pump) to overcome all resistances before entering vacuum unit feed drum. Even if it was placed on the shellside instead of crude oil, for the given fouling rate, calculations show that we could easilly achieve 4 year run-length without shutting down the unit and cleaning the exchangers - as far as process hydraulic is concerned.
So my question is: what do you think about changing flow pattern through these exchangers and place the crude oil on the tubeside? Did you have any similar experiences? Most often, similar units around the world, faced with similar fouling/hydraulic problems, undergo revamp which consists of placing flash drum/column in the middle of preheat train, with the new booster pump. I do not consider it as an attractive option at the moment - it is very expensive, and it has some drawbacks (flash drum foaming, main column products degradation etc.)
Placing crude on the tubeside: the initial pressure drop through the hot preheat train, in such case, would be higher, but I think the rate of fouling/pressure drop building will be much lower, because of velocity profiles; so when the terminal tube velocity is reached, no significant fouling can take place from the crude-side.
Process heater is available to deliver additional duty if heat transfer rate drops (for crude deltaT = 25C = start of run - end of run), because of eventual fouling from the atmospheric residue side.
In most crude units, crude oil is placed on the shell side (in the hot preheat train), and they all suffer from the same disease: crude heater inlet pass vaporization, caused by big pressure drop through the train. So why, then, all designers always place the crude oil on the shellside? Do you have any hints on this?
#2
Posted 05 December 2006 - 07:51 PM
hello,
Yours is very interesting post. I'm not expert of heat exchanger design, but I would like to express my thoughts on it.
There are many criteria to decide the configuration of Shell & Tube (S&T) Heat Exchanger as provided in many literature and are very well known. Based on those, there are mainly two reasons i'm able to think for crude pre-heat train.
[1] In general, hot fluid is preferentially put on tube side in any kind of S&T HE. The reason is that you don't loose any heat to atmosphere when you put it on tube side. If it is on shell side, there are chances of heat being lost to atmosphere.
[2] The fluid with higher fouling should be placed on tube side. The reason is that tubeside velocities are always higher compared to shell side. At higher velocities, fouling can be avoided upto longer time than that at lower velocities. Basically, fouling is nothing but deposits of fluid on the metal surface of tubes/shell. So, if you have higher velocities, this kind of deposition can be avoided upto some extent.
Now, you said that why Atmospheric Residue is not placed on shell side. In my opinion, even if you place it on shell side, it is bound to foul the tubes outer surface!!! It would affect heat exchange in this case also almost in same magnitude as the original case of Atmospheric residue on tube side.
I think these are the possible reasons for atmospheric residue being put on 'tube side'.
I do not think there is any issue of 'hydraulics' attached with the prbolem. The feed pump is selected based pressure required to overcome various resistances in circuit. Tubeside pressure drop would be higher and you may required higher pump head. But I don't think it would affect that much higher to be a deciding factor. Meaning you don't decide to put fluid on shell side or tube side based on pump selection. Rather, pump is selected based on requirement.
Any more opinions?
Thank you,
Yours is very interesting post. I'm not expert of heat exchanger design, but I would like to express my thoughts on it.
There are many criteria to decide the configuration of Shell & Tube (S&T) Heat Exchanger as provided in many literature and are very well known. Based on those, there are mainly two reasons i'm able to think for crude pre-heat train.
[1] In general, hot fluid is preferentially put on tube side in any kind of S&T HE. The reason is that you don't loose any heat to atmosphere when you put it on tube side. If it is on shell side, there are chances of heat being lost to atmosphere.
[2] The fluid with higher fouling should be placed on tube side. The reason is that tubeside velocities are always higher compared to shell side. At higher velocities, fouling can be avoided upto longer time than that at lower velocities. Basically, fouling is nothing but deposits of fluid on the metal surface of tubes/shell. So, if you have higher velocities, this kind of deposition can be avoided upto some extent.
Now, you said that why Atmospheric Residue is not placed on shell side. In my opinion, even if you place it on shell side, it is bound to foul the tubes outer surface!!! It would affect heat exchange in this case also almost in same magnitude as the original case of Atmospheric residue on tube side.
I think these are the possible reasons for atmospheric residue being put on 'tube side'.
I do not think there is any issue of 'hydraulics' attached with the prbolem. The feed pump is selected based pressure required to overcome various resistances in circuit. Tubeside pressure drop would be higher and you may required higher pump head. But I don't think it would affect that much higher to be a deciding factor. Meaning you don't decide to put fluid on shell side or tube side based on pump selection. Rather, pump is selected based on requirement.
Any more opinions?
Thank you,
#3
Posted 06 December 2006 - 05:53 PM
Thanks for feedback Nirav, your comments are always very appreciated.
[1] I agree with you; hotter fluid generally has a bigger fouling potential.
[2] I also agree. Placing dirtier fluid on the tube sude is also a rule of thumb, in 99% of cases.
I was wandering: you have to choose between heat recovery and hydraulic demands of your system. Higher heat recovery means that your hydraulic demand is also higher. So the questions arrive:
- If additional heat input needed (because of HEx fouling) which must be delievered by process heater, is not an operating constraint (oversized heater, for example), should not hydraulic demand have been considered as the primary criterion for tube flow-pattern selection - because it is a cause for shutting down the unit?
I other words, what would you choose if someone says to you: "You do not have any heat input concerns. You must account only for hydraulic demands of your system. Tell me what flow pattern do you want for crude oil and atmospheric residue? What heat exchanger design do you need?"
I am thinking in such interesting situation... AES, perhaps. But I would certainly not choose crude on the shellside. There is no crude unit in the world, I think, where this is not a problem. And I have seen solutions worldwide only for treating the symptom but not treating the cause of problem.
Best regards, friend
[1] I agree with you; hotter fluid generally has a bigger fouling potential.
[2] I also agree. Placing dirtier fluid on the tube sude is also a rule of thumb, in 99% of cases.
I was wandering: you have to choose between heat recovery and hydraulic demands of your system. Higher heat recovery means that your hydraulic demand is also higher. So the questions arrive:
- If additional heat input needed (because of HEx fouling) which must be delievered by process heater, is not an operating constraint (oversized heater, for example), should not hydraulic demand have been considered as the primary criterion for tube flow-pattern selection - because it is a cause for shutting down the unit?
I other words, what would you choose if someone says to you: "You do not have any heat input concerns. You must account only for hydraulic demands of your system. Tell me what flow pattern do you want for crude oil and atmospheric residue? What heat exchanger design do you need?"
I am thinking in such interesting situation... AES, perhaps. But I would certainly not choose crude on the shellside. There is no crude unit in the world, I think, where this is not a problem. And I have seen solutions worldwide only for treating the symptom but not treating the cause of problem.
Best regards, friend
#4
Posted 06 December 2006 - 08:17 PM
Zauberberg,
Thank you for your greeting.
You have raised two issues in relation to original post. [1] Hydraulic demand; [2] Placing atmospheric residue on tube or shell side. I would try to share my views.
Let's discuss of hydraulic first.
As a designer of new plant, I would never try to impose "equipment constraints" on my process. I would always try to make equipments & machinery to work as per requirement of process. Consider these cases for crude pre-heat train.
[Case A] Based on possibilities, if you put more exchangers in pre-heat train, there will be higher head requirement of feed pump. If you put crude-oil on tube-side (as per your opinion), you would again need little bit of higher head due to higher pressure drop on tube side of H.E.
[Case B] Crude-oil is on shell side (normal practice). Total numbers of pre-heat exchangers are less than Case A. Because you consider that process heater is able to heat the crude up to required temperature (But, your operating cost is increased due to higher fuel gas requirements in process heater). In this case, you will have lower head requirement for pump than case A.
What I was trying to explain is that the difference in head required in above two cases may differ maximum up to 2 bar. (higher head in Case A due to higher pressure drops). This is not significant difference from the point of view of capital cost of feed pump. So, in any case, I would finalize pump after designing pre-heat train. Initially, I would try to fix the requirements of process by making 'heat exchanger analysis' in which heat recovery is optimum.
Let's discuss second point.
You want to put Atmospheric Residue on shell side. How it would prevent fouling?
In my opinion, it will not help. Because, as I said before, atmospheric residue on shell side now start fouling "outer" surface of heat exchanger tubes!!!! There is no way you can stop Atmospheric residue from fouling your exchanger just by flowing it on shell side. Because, it is nature of residue. In fact, putting residue on shell side would worsen the problem. Because velocities on shell side are low. Therefore, fouling would start early.
This is the reason why higher fouling fluid is kept on tube side, if there are not other constraints. This helps to avoid fouling up to longer period.
You said people are not treating the cause of problem. BUT the cause of fouling problem is Residue itself. You can not avoid it. The reason for fouling is not because 'residue' is on tube side or shell side of exchanger. But because it is the inherent characteristic of the residue to deposit carbon on tubes. It causes lowering of heat exchange.
Therefore, you try to maximize the time period before you are 'stuck' due to fouling. You use all efforts to run your unit for longer durations before total shut-down which is must to clean up the fouled equipments. Therefore, across whole world, you have seen solutions to treat the symptoms of fouling.
Therefore, to answer your question, I would always try to put flow pattern of crude-oil & residue in which I can avoid fouling for longer duration. i.e. Crude oil on Shell side & Residue on tube side.
I hope I am able to put my words appropriately for what I want to convey.
I'm also looking for others opinions who have experience in operating crude distillation units.
Thank you,
Thank you for your greeting.
You have raised two issues in relation to original post. [1] Hydraulic demand; [2] Placing atmospheric residue on tube or shell side. I would try to share my views.
Let's discuss of hydraulic first.
As a designer of new plant, I would never try to impose "equipment constraints" on my process. I would always try to make equipments & machinery to work as per requirement of process. Consider these cases for crude pre-heat train.
[Case A] Based on possibilities, if you put more exchangers in pre-heat train, there will be higher head requirement of feed pump. If you put crude-oil on tube-side (as per your opinion), you would again need little bit of higher head due to higher pressure drop on tube side of H.E.
[Case B] Crude-oil is on shell side (normal practice). Total numbers of pre-heat exchangers are less than Case A. Because you consider that process heater is able to heat the crude up to required temperature (But, your operating cost is increased due to higher fuel gas requirements in process heater). In this case, you will have lower head requirement for pump than case A.
What I was trying to explain is that the difference in head required in above two cases may differ maximum up to 2 bar. (higher head in Case A due to higher pressure drops). This is not significant difference from the point of view of capital cost of feed pump. So, in any case, I would finalize pump after designing pre-heat train. Initially, I would try to fix the requirements of process by making 'heat exchanger analysis' in which heat recovery is optimum.
Let's discuss second point.
You want to put Atmospheric Residue on shell side. How it would prevent fouling?
In my opinion, it will not help. Because, as I said before, atmospheric residue on shell side now start fouling "outer" surface of heat exchanger tubes!!!! There is no way you can stop Atmospheric residue from fouling your exchanger just by flowing it on shell side. Because, it is nature of residue. In fact, putting residue on shell side would worsen the problem. Because velocities on shell side are low. Therefore, fouling would start early.
This is the reason why higher fouling fluid is kept on tube side, if there are not other constraints. This helps to avoid fouling up to longer period.
You said people are not treating the cause of problem. BUT the cause of fouling problem is Residue itself. You can not avoid it. The reason for fouling is not because 'residue' is on tube side or shell side of exchanger. But because it is the inherent characteristic of the residue to deposit carbon on tubes. It causes lowering of heat exchange.
Therefore, you try to maximize the time period before you are 'stuck' due to fouling. You use all efforts to run your unit for longer durations before total shut-down which is must to clean up the fouled equipments. Therefore, across whole world, you have seen solutions to treat the symptoms of fouling.
Therefore, to answer your question, I would always try to put flow pattern of crude-oil & residue in which I can avoid fouling for longer duration. i.e. Crude oil on Shell side & Residue on tube side.
I hope I am able to put my words appropriately for what I want to convey.
I'm also looking for others opinions who have experience in operating crude distillation units.
Thank you,
#5
Posted 08 December 2006 - 01:42 AM
It is known that if you are processing high #TAN crude blends then the material selection for the crude resid is governing and of course the hottest of the two mediums. There is a strong preference to put the Crude Resid tube-side for corrosion reasons. Equally we have experience with crude on the tubes and Resid shell-side and the Resid fouls just as much, if not more, than the crude. Thus the fouling of this particular HEX unit is predominantly shell-side dominated and by fouling.
Hope this helps.
Hope this helps.
#6
Posted 16 December 2006 - 03:27 PM
Nirav and George, thanks for your replies.
Preheat train revamps mostly include new booster pumps - with or without unit preflash section - which will be able to deliver additional pressure head for crude oil to overcome pressure losses, but still below MAWP of downstream heat exchangers (that is what I had in mind when talking about "only treating the symptoms"). I would like to hear your opinion about following design issues and possible variations in industrial/refinery practice:
Fluid Allocation
1. Tube side is preferred under these circumstances:
§ Fluids which are prone to foul
• The higher velocities will reduce buildup
• Mechanical cleaning is also much more practical for tubes than for shells.
§ Corrosive fluids are usually best in tubes
• Tubes are cheaper to fabricate from exotic materials
• This is also true for very high temperature fluids requiring alloy construction
§ Toxic fluids to increase containment
§ Streams with low flow rates to obtain increased velocities and turbulence
§ High pressure streams since tubes are less expensive to build strong
§ Streams with a low allowable pressure drop
2. Viscous fluids go on the shell side, since this will usually improve the
rate of heat transfer.
§ On the other hand, placing them on the tube side will usually lead to lower pressure drops. Judgment is needed.
According to these rules of thumb and field observations, placing crude oil on the tube-side will result in higher initial pressure drop, but also in significantly lower rate of fouling and pressure loss build-up by time.
Placing viscous fluid on the shell-side (residue) is also favorable in such case, because acceptable pressure drop for residue has a very high margin (beside negative heat transfer effects).
I wonder why is it feasible to buy new booster pumps (very expensive items!) for crude oil, instead of changing fluid allocation. Of course, this what I have said applies only if you have hydraulic constraints because of fouling, and additional (extra) capacity of fired heater is not a problem for you.
Preheat train revamps mostly include new booster pumps - with or without unit preflash section - which will be able to deliver additional pressure head for crude oil to overcome pressure losses, but still below MAWP of downstream heat exchangers (that is what I had in mind when talking about "only treating the symptoms"). I would like to hear your opinion about following design issues and possible variations in industrial/refinery practice:
Fluid Allocation
1. Tube side is preferred under these circumstances:
§ Fluids which are prone to foul
• The higher velocities will reduce buildup
• Mechanical cleaning is also much more practical for tubes than for shells.
§ Corrosive fluids are usually best in tubes
• Tubes are cheaper to fabricate from exotic materials
• This is also true for very high temperature fluids requiring alloy construction
§ Toxic fluids to increase containment
§ Streams with low flow rates to obtain increased velocities and turbulence
§ High pressure streams since tubes are less expensive to build strong
§ Streams with a low allowable pressure drop
2. Viscous fluids go on the shell side, since this will usually improve the
rate of heat transfer.
§ On the other hand, placing them on the tube side will usually lead to lower pressure drops. Judgment is needed.
According to these rules of thumb and field observations, placing crude oil on the tube-side will result in higher initial pressure drop, but also in significantly lower rate of fouling and pressure loss build-up by time.
Placing viscous fluid on the shell-side (residue) is also favorable in such case, because acceptable pressure drop for residue has a very high margin (beside negative heat transfer effects).
I wonder why is it feasible to buy new booster pumps (very expensive items!) for crude oil, instead of changing fluid allocation. Of course, this what I have said applies only if you have hydraulic constraints because of fouling, and additional (extra) capacity of fired heater is not a problem for you.
#7
Posted 17 December 2006 - 08:21 PM
QUOTE (Zauberberg @ Dec 17 2006, 05:27 AM) <{POST_SNAPBACK}>
1. Tube side is preferred under these circumstances:
§ Streams with a low allowable pressure drop
2. Viscous fluids go on the shell side, since this will usually improve the
rate of heat transfer.
§ On the other hand, placing them on the tube side will usually lead to lower pressure drops. Judgment is needed.[/color]
§ Streams with a low allowable pressure drop
2. Viscous fluids go on the shell side, since this will usually improve the
rate of heat transfer.
§ On the other hand, placing them on the tube side will usually lead to lower pressure drops. Judgment is needed.[/color]
Hello zauberberg,
After reading your post, I wanted to give you immediate response on above two points. Because, your interpretation is reverse to what is actually happening.
I would like to repeat the step of system design in brief again.
You finalize your system resistance (pressure drop) before you design the pump. Means try to fix your process requirements at first place. Then decide what is required to meet those requirements. So, pump is selected afterwards. If there is high pressure drop in system, you choose higher head of pump. If there is low pressure drop in system, you choose lower head of pump. In any case, Pump has to be selected based on system's need.
You want to say.....
[1] Streams with low allowable pressure drop (dP) is preferred on tube side
I would try to explain why it is NOT the case, in general.
You will agree with me that pressure drop is higher in tubes than in shell. The reason is the flow area. You have very high flow area on shell side. Therefore, pressure drop on shell side is lower. Do you agree? If yes, then.... your doubt should be clear.
For a moment, forget about design. Consider any of your present heat exchanger in your plant.
A particular fluid, say "A", is placed on tube side & "B" on shell side. In such case, measure dP of "A"(tube side) & "B"(Shell side).
You will notice that dP is higher for "A"(tube side) & lower for "B"(shell side).
Now, if you reverse the fluids on heat exchanger, the statement observation is....
You will notice dP is higher for "B"(tube side) & lower for "A"(shell side)
In both the cases, tubeside dP is higher. No matter what the fluid is.
What I am trying to explain is : Tubeside of heat exchanger has always higher dP than shell side.
So, if you put fluid with "low allowable dP" on tube side, you are making situation more difficult. It will give higher dP than what was there on shell side for that particular fluid.
Now, let's see your second thought.
You want to say.....
[2] Placing high viscous fluid on tubeside will lead to low pressure drop
The answer is "NO". Why?
Because,
1) dP is directly proportional to viscosity. If flow area is constant, pressure drop of high viscous fluid will be higher compared to low viscous fluid.
2) dP is inversely proportional to flow area. If fluid properties are constant, pressure drop in lower flow area will be higher. So, it will increase dP of the fluid if you put it on tube side compared to what it was on shell side.
I guess you are reading heat exchanger datasheet and making yourself in doubt.
Allowable dP mentioned for tube side fluid ("A" for example) could be "0.7" or "1.0" bar
Allowable dP mentioned for shell side fluid ("B" for example) could be "0.1" or "0.2" bar
You might be thinking that placing "B" on tubeside will give dP of 0.2 bar. Is it that what you are thinking ????? If yes, then unfortunately you are leading yourself in incorrect situation.
Those values are NOT based on fluid. They are based on characteristics of "tubeside" & "shell side" of heat exchanger. Higher allow dP is mentioned for "tube side" because, otherwise, you wont' be able to design heat exchanger. If you say tubeside allow dP is "0.2" bar, it will be almost impossible to have configuration which will match this requirement.
I have written very looong explanation. But I hope I'm explaining what I want to.
Now, if whatever I said is correct, your next question is...
Why residue (high viscous fluid) is placed on tubeside???? Because placing them on shell side would give lower dP. Yes, that is true.
BUT, I already tried to explain before in earlier post as below.
QUOTE (Nirav)
[2] The fluid with higher fouling should be placed on tube side. The reason is that tubeside velocities are always higher compared to shell side. At higher velocities, fouling can be avoided upto longer time than that at lower velocities.
You may need higher head of pump due to higher pressure drops in heat exchangers. If this is the case, you must select higher head pump or put booster pump. No problem.
Then your question would be why to incur such capital cost. Instead of that, put residue on shell side. BUT I would again repeat as following.
QUOTE (Nirav)
You want to put Atmospheric Residue on shell side. How it would prevent fouling?
In my opinion, it will not help. Because, as I said before, atmospheric residue on shell side now start fouling "outer" surface of heat exchanger tubes!!!! There is no way you can stop Atmospheric residue from fouling your exchanger just by flowing it on shell side. Because, it is nature of residue. In fact, putting residue on shell side would worsen the problem. Because velocities on shell side are low. Therefore, fouling would start early.
This is the reason why higher fouling fluid is kept on tube side, if there are not other constraints. This helps to avoid fouling up to longer period.
In my opinion, it will not help. Because, as I said before, atmospheric residue on shell side now start fouling "outer" surface of heat exchanger tubes!!!! There is no way you can stop Atmospheric residue from fouling your exchanger just by flowing it on shell side. Because, it is nature of residue. In fact, putting residue on shell side would worsen the problem. Because velocities on shell side are low. Therefore, fouling would start early.
This is the reason why higher fouling fluid is kept on tube side, if there are not other constraints. This helps to avoid fouling up to longer period.
If you put residue on shell side as you want, you will probably have additional one or two more shut downs to clean heat exchanger. This will be huge production loss. Instead of that, putting booster pump is far better.
I hope, you are not tired of reading of what I said.
Thank you,
#8
Posted 18 December 2006 - 10:02 AM
Dear friend, thank you for your prompt reply.
I apologize to you if I made a confusion - I do not know if I have presented my observations correctly.
Of course, placing fluid on the tube-side results in higher pressure drop (compared to the shell-side). But what happens in extremely fouling applications, described in my previous posts?
1. Placing crude oil on the shell-side results in initial pressure drop approx = 1bar (3 HEX in series). Then, the total crude oil pressure at HEXs outlet is about 18barG.
2. Placing crude oil on the tube-side results in initial pressure drop approx = 3bar (the same 3 HEXs in series). In such case, crude oil pressure at HEXs outlet is about 16barG.
Minimum crude oil pressure at fired heater inlet passes control valves is 13barG. Fired heater is located just downstream of the HEXs that I am writing about.
Now this is what I meant:
1. Having crude oil on the shell-side, after 2 years of operation, its pressure falls to 13barG due to massive fouling. This is the time when unit must be shut down.
2. At the same time, the residue pressure (which is on the tube-side) falls only for 1bar.
If I place crude oil on the tube-side, I will have 16 or 15barG at HEXs outlet at the beginning of operation (instead of 18barG when crude is on the shell-side) - but still more than enough to operate the unit. After 2 years of operation, this pressure will fall for 1bar - and I can still run the unit!
Crude Unit is shut down because of crude oil hydraulic constraints - not because of heat transfer losses (due to fouling). Fired heater can supply additional heat required, if hydraulic losses were not a problem for us.
My (design) statement "Tube side is preferred under these circumstances: Streams with a low allowable pressure drop" is applicable only for extremely fouling services, as I see it. Why? Because you cannot afford high pressure drop build-up over time. Low initial pressure drop, when you put dirty fluid on the shell-side, is more than 5 times multiplied after only 2 years of operation. I hope you have a little bit clearer picture of what I was trying to say.
I am never tired to listen to advices from experienced professionals - so you are always welcome to comment.
Thank you again, friend.
I apologize to you if I made a confusion - I do not know if I have presented my observations correctly.
Of course, placing fluid on the tube-side results in higher pressure drop (compared to the shell-side). But what happens in extremely fouling applications, described in my previous posts?
1. Placing crude oil on the shell-side results in initial pressure drop approx = 1bar (3 HEX in series). Then, the total crude oil pressure at HEXs outlet is about 18barG.
2. Placing crude oil on the tube-side results in initial pressure drop approx = 3bar (the same 3 HEXs in series). In such case, crude oil pressure at HEXs outlet is about 16barG.
Minimum crude oil pressure at fired heater inlet passes control valves is 13barG. Fired heater is located just downstream of the HEXs that I am writing about.
Now this is what I meant:
1. Having crude oil on the shell-side, after 2 years of operation, its pressure falls to 13barG due to massive fouling. This is the time when unit must be shut down.
2. At the same time, the residue pressure (which is on the tube-side) falls only for 1bar.
If I place crude oil on the tube-side, I will have 16 or 15barG at HEXs outlet at the beginning of operation (instead of 18barG when crude is on the shell-side) - but still more than enough to operate the unit. After 2 years of operation, this pressure will fall for 1bar - and I can still run the unit!
Crude Unit is shut down because of crude oil hydraulic constraints - not because of heat transfer losses (due to fouling). Fired heater can supply additional heat required, if hydraulic losses were not a problem for us.
My (design) statement "Tube side is preferred under these circumstances: Streams with a low allowable pressure drop" is applicable only for extremely fouling services, as I see it. Why? Because you cannot afford high pressure drop build-up over time. Low initial pressure drop, when you put dirty fluid on the shell-side, is more than 5 times multiplied after only 2 years of operation. I hope you have a little bit clearer picture of what I was trying to say.
I am never tired to listen to advices from experienced professionals - so you are always welcome to comment.
Thank you again, friend.

#9
Posted 18 December 2006 - 07:42 PM
Hi Zauberberg,
I think i was not getting what you were trying to explain before. But now, i'm very much clear of your all concerns. thanks for detail explanation again.
this is the best example of difference in point of view & the problem of communication through "writing". Had there been verbal communication between us, it would have been clearer much more faster.
I always tried to see it through design point of view. while you tried to explain from operation point of view over a period of 2 yrs.
Anyway.
Now, there are two options as i see it.
[1] Place crude oil on shell side, residue on tube side. : This would mean better heat transfer for long period. BUT high dP due to fouling on tube side after a particular time period. Therefore, to run unit for longer period, you need booster pump which will add to capital cost & operating cost of additional power.
[2] Place crude oil on tube side, residue on shell side : This would mean poorer heat transfer which can be compensated by process heater. This would be higher operating cost due to additional usage of fuel gas. At the same time, required area of heat exchanger would be higher which would add capital cost. BUT you might be able to operate for longer period than option [1] which could be advantageous.
Both these options have implications over capital & operating costs. Both will require shut down at some point of time, sooner or later.
What could be optimum between above two can be decided based on experience, research of past data & literatures etc. and thorough study of the unit. Unfortunately, I'm not that much experienced particularly about crude distillation units. I must thank you for providing feed back on problems of operation over a period of time.
Of course you and I are not the first one to think over this matter because crude distillation unit is one of the the oldest inventions for a refinery. I would try to find why it is mostly followed to put crude oil on shell side. I'm not sure, but as I tried to explain above, there is a chance that when you compare option [1] & [2] in overall terms of
a] capital & operating costs and,
b] period of shut down due to severe fouling;
the 1st option proved viable. This is my opinion based on your observation of the fact that most units in the world put atmospheric residue on tube side & crude oil on shell side (some units might have put it reverse).
But I need to do some study over it !!!!!
Thank you,
I think i was not getting what you were trying to explain before. But now, i'm very much clear of your all concerns. thanks for detail explanation again.
this is the best example of difference in point of view & the problem of communication through "writing". Had there been verbal communication between us, it would have been clearer much more faster.
I always tried to see it through design point of view. while you tried to explain from operation point of view over a period of 2 yrs.
Anyway.
Now, there are two options as i see it.
[1] Place crude oil on shell side, residue on tube side. : This would mean better heat transfer for long period. BUT high dP due to fouling on tube side after a particular time period. Therefore, to run unit for longer period, you need booster pump which will add to capital cost & operating cost of additional power.
[2] Place crude oil on tube side, residue on shell side : This would mean poorer heat transfer which can be compensated by process heater. This would be higher operating cost due to additional usage of fuel gas. At the same time, required area of heat exchanger would be higher which would add capital cost. BUT you might be able to operate for longer period than option [1] which could be advantageous.
Both these options have implications over capital & operating costs. Both will require shut down at some point of time, sooner or later.
What could be optimum between above two can be decided based on experience, research of past data & literatures etc. and thorough study of the unit. Unfortunately, I'm not that much experienced particularly about crude distillation units. I must thank you for providing feed back on problems of operation over a period of time.
Of course you and I are not the first one to think over this matter because crude distillation unit is one of the the oldest inventions for a refinery. I would try to find why it is mostly followed to put crude oil on shell side. I'm not sure, but as I tried to explain above, there is a chance that when you compare option [1] & [2] in overall terms of
a] capital & operating costs and,
b] period of shut down due to severe fouling;
the 1st option proved viable. This is my opinion based on your observation of the fact that most units in the world put atmospheric residue on tube side & crude oil on shell side (some units might have put it reverse).
But I need to do some study over it !!!!!

Thank you,
#10
Posted 19 December 2006 - 04:13 PM
Nirav,
Are you of opinion that placing residue on the shell-side will result in much poorer heat transfer (compared to actual case)?
Can you write in a little bit more details about this issue; my observations tell me there would not be any significant changes - not more than 10-15% worse, compared to situation that we have with current configuration.
Are you of opinion that placing residue on the shell-side will result in much poorer heat transfer (compared to actual case)?
Can you write in a little bit more details about this issue; my observations tell me there would not be any significant changes - not more than 10-15% worse, compared to situation that we have with current configuration.
#11
Posted 02 May 2009 - 12:10 PM
QUOTE (Zauberberg @ Dec 20 2006, 02:13 AM) <{POST_SNAPBACK}>
Nirav,
Are you of opinion that placing residue on the shell-side will result in much poorer heat transfer (compared to actual case)?
Can you write in a little bit more details about this issue; my observations tell me there would not be any significant changes - not more than 10-15% worse, compared to situation that we have with current configuration.
Are you of opinion that placing residue on the shell-side will result in much poorer heat transfer (compared to actual case)?
Can you write in a little bit more details about this issue; my observations tell me there would not be any significant changes - not more than 10-15% worse, compared to situation that we have with current configuration.
Dear,
Again a response to a very old post, that might have been resolved already.
I feel that putting bottoms residue on shell side may result in drastically low 'heat transfer coefficient' within a short duration of operation
Where Heavier or Higher TAN no. Crude(s)or Crude blends processing being the cause.(containing higher asphaltenes% or other foulants)
In such cases the increment in up-time (extention in processing period)will not be achievable;I suspect.
As regards decresing the back pressure on any pumping system a careful fouled conditions hydraulic survey needs to be crried out thus deciding about either booster pump(s)
or increased no of exchanger in parallel must be given a serious thoughtful consideration to provide additional heat tranfer area(s) minimisation of back pressure possibilities
thereby [b]much increased up-time and lesser loss of energy over a longer period[/b].
Hope this is giving another option.
Similar Topics
Distillation Column Reboiler QuestionsStarted by Guest_AlanC079_* , 07 Jul 2025 |
|
![]() |
||
![]() Distillation Column Top PressureStarted by Guest_halkeshhulk_* , 27 Jun 2025 |
|
![]() |
||
Design Capacity Of Hydrogen Pullet During Hydroprocessing Units UpsetStarted by Guest_Divid Kelin_* , 18 Jun 2025 |
|
![]() |
||
![]() Distillation Column Top & Bottom TemperaturesStarted by Guest_halkeshhulk_* , 09 Jun 2025 |
|
![]() |
||
![]() Distillation Tower Top And Bottom Temperature And PressureStarted by Guest_student55_* , 27 Mar 2016 |
|
![]()
|