|
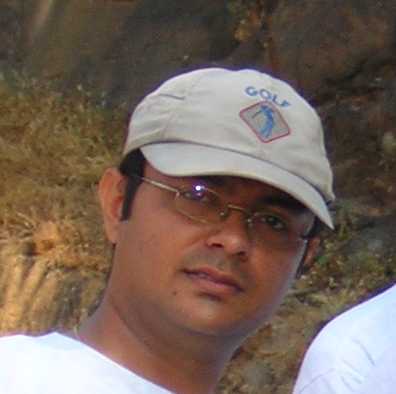
Pump Around Pumps
Started by Ritesh Suratwala, Jan 19 2007 12:32 PM
7 replies to this topic
Share this topic:
#1
Posted 19 January 2007 - 12:32 PM
Hi all,
In distillation column, pump around is used to condense vapor inside column by exchanging
heat with other process stream (mainly feed stream). Liquid is drawn from column tray
through pump, passes through heat exchanger where it exchanges heat with other process
stream and cooled liquid is returned back to column.
I have a question related to control system for pump around loop and safety of pump around
pumps.
In any pump, trip is provided to protect pump in case of low level in suction vessel.
However, in case of pump around pumps, liquid is drawn from tray. Do we require any level
instruments and trip from column tray liquid to protect pumps? In case yes, how to take care
hold-up requirement of tray and what is typical hold up time required?
I have seen many systems where no low level trip / level instrument is provided in column at
draw tray to protect pump around pumps, however pumps are system is running without any
trouble. I have one example where plant is almost 30 years old and do now have any
protection for pump around pumps, eventhough those are very big (HT motor) pumps.
Is it because pump is circulating liquid and there is no probability of drop in liquid level?
I am not able to conclude. Can anyone give me more clarification on pump around system and
instrumentation required specially for pump around pumps?
In distillation column, pump around is used to condense vapor inside column by exchanging
heat with other process stream (mainly feed stream). Liquid is drawn from column tray
through pump, passes through heat exchanger where it exchanges heat with other process
stream and cooled liquid is returned back to column.
I have a question related to control system for pump around loop and safety of pump around
pumps.
In any pump, trip is provided to protect pump in case of low level in suction vessel.
However, in case of pump around pumps, liquid is drawn from tray. Do we require any level
instruments and trip from column tray liquid to protect pumps? In case yes, how to take care
hold-up requirement of tray and what is typical hold up time required?
I have seen many systems where no low level trip / level instrument is provided in column at
draw tray to protect pump around pumps, however pumps are system is running without any
trouble. I have one example where plant is almost 30 years old and do now have any
protection for pump around pumps, eventhough those are very big (HT motor) pumps.
Is it because pump is circulating liquid and there is no probability of drop in liquid level?
I am not able to conclude. Can anyone give me more clarification on pump around system and
instrumentation required specially for pump around pumps?
#2
Posted 19 January 2007 - 05:31 PM
In our refinery we have two crude units. Older unit have active tray (ordinary valve tray with draw off sump) for drawing LGO pumparaund and LGO product. It doesn’t have any protection for pumparaund pump.
New unit have collector tray (chimney tray) with liquid overflow. That tray have level indicator.
In my opinion collector tray is better choice because if you see level going down you can cut back LGO product flow and keep level on that tray, and in that way protect pumaraund pump. We don’t have any other protection for PA pump.
On case with active tray it is much easier to lost level on tray.
Regards,
Milutin
New unit have collector tray (chimney tray) with liquid overflow. That tray have level indicator.
In my opinion collector tray is better choice because if you see level going down you can cut back LGO product flow and keep level on that tray, and in that way protect pumaraund pump. We don’t have any other protection for PA pump.
On case with active tray it is much easier to lost level on tray.
Regards,
Milutin
#3
Posted 19 January 2007 - 08:38 PM
Hi Milutin,
Thanks for reply.
Still I am not sure how this types of tray going to make any difference? According to me, it is all about hold-up time in tray. Can you give more details if you have?
Also, since liquid is being circulated in close loop, what could be possible reasons for loss of liquid in pump draw-off tray?
In any case, direct trip to pump for protection is not given. Is it accepted practice? I would like to know if some one has real experience regarding troubles / failure of pump around pumps.
Thanks.
Thanks for reply.
Still I am not sure how this types of tray going to make any difference? According to me, it is all about hold-up time in tray. Can you give more details if you have?
Also, since liquid is being circulated in close loop, what could be possible reasons for loss of liquid in pump draw-off tray?
In any case, direct trip to pump for protection is not given. Is it accepted practice? I would like to know if some one has real experience regarding troubles / failure of pump around pumps.
Thanks.
#4
Posted 20 January 2007 - 01:25 AM
You are right it is all about hold-up time on tray, time to cope with upsets. Active tray have short residence time, on that tray you have only level above outlet weir which is (depending of design) few centimeters high and in addition height of tray sump. On chimney tray outlet weir is much higher and quantity of liquid is larger. Also on chimney tray we have level indicator which really helps.
Typical residence time is from 3-7 minutes, in our case 4 minutes.
You can loss level on PA tray when you dry off that tray for that can be numerous reasons: unit upset, different crude switch, attempt to draw more product from that tray then possible, etc.
In some new designs I saw also pump protection, when pump lost discharge pressure, pump trip.
Regards,
Milutin
Typical residence time is from 3-7 minutes, in our case 4 minutes.
You can loss level on PA tray when you dry off that tray for that can be numerous reasons: unit upset, different crude switch, attempt to draw more product from that tray then possible, etc.
In some new designs I saw also pump protection, when pump lost discharge pressure, pump trip.
Regards,
Milutin
#5
Posted 22 January 2007 - 10:49 AM
My experience:
pumparound drawn-off from single chimney-tray having 3-4 min hold up; external standpipe for holding tray level transmitters and switches.
Pumparound is under level control throttling a LCV on pump discharge line.
Pumps protection is made through Lo/Hi levels switches on tray standpipe that trip/change-over the pump. (Normally pumps are grade located so they have large NPSH av.).
On pump dicharge line minimum flow (with separate FCV) recycle to the chimney tray.
Rgds.
_Lf_
pumparound drawn-off from single chimney-tray having 3-4 min hold up; external standpipe for holding tray level transmitters and switches.
Pumparound is under level control throttling a LCV on pump discharge line.
Pumps protection is made through Lo/Hi levels switches on tray standpipe that trip/change-over the pump. (Normally pumps are grade located so they have large NPSH av.).
On pump dicharge line minimum flow (with separate FCV) recycle to the chimney tray.
Rgds.
_Lf_
#6
Posted 23 January 2007 - 10:34 AM
One of the keys of succesful and smooth operation of pumparound loops, is to provide sufficient liquid residence time on the draw-off tray, for the purpose of liquid degassing. Employing chimney trays with recessed sumps is a standard design practice during last several decades. On the other side, active trays do not provide enough time for liquid degassing (I do not know about the newest designs); in such circumstances, the pumparound exit nozzle cavitation occurs and pumparound flow is greatly reduced - regardless of the liquid level on the draw-off tray. This adversely affects column heat balance and unit operation.
The optimum configuration is to draw the product from the same tray as for the pumparound stream - this minimizes startup, shutdown and feed-switching upsets in column operation.
To protect P/A or other high head/high flow pumps from loosing the liquid flow, suction pressure control can be employed. And if properly designed, it works very well.
The optimum configuration is to draw the product from the same tray as for the pumparound stream - this minimizes startup, shutdown and feed-switching upsets in column operation.
To protect P/A or other high head/high flow pumps from loosing the liquid flow, suction pressure control can be employed. And if properly designed, it works very well.
#7
Posted 23 January 2007 - 03:01 PM
Palusa you mentioned:
Is this LCV on product (to storage) line? It looks like control arrangement on vacuum distillation unit or FCCU main fractionator.
Regards,
Milutin
QUOTE (palusa @ Jan 22 2007, 10:49 AM) <{POST_SNAPBACK}>
Pumparound is under level control throttling a LCV on pump discharge line.
Is this LCV on product (to storage) line? It looks like control arrangement on vacuum distillation unit or FCCU main fractionator.
Regards,
Milutin
#8
Posted 24 January 2007 - 04:53 AM
Milutin,
you are right: what i described is the side arrangement of a fractionating column.
Regards.
_Lf_
you are right: what i described is the side arrangement of a fractionating column.
Regards.
_Lf_
Similar Topics
Thermal Oil Pump Motors Blew OffStarted by Guest_lizelle_* , 02 May 2025 |
|
![]() |
||
Centrifugal Pump In Recycle Mode: Constant Power Consumption But FluctStarted by Guest_Kakka_* , 23 Jan 2025 |
|
![]() |
||
Need Help Understanding Increased Power Consumption In Injection PumpStarted by Guest_Kakka_* , 21 Feb 2025 |
|
![]() |
||
Improving Safety By Re-Routing Priming Vent Line In Centrifugal Pump HStarted by Guest_Srinivas Agastheeswaran_* , 31 Jan 2025 |
|
![]() |
||
![]() Centrifugal PumpsStarted by Guest_panoska_* , 01 Feb 2025 |
|
![]() |