I am running a cryogenic materials into a heat exchanger. How would we know that the heat exchanger would not freeze?
How to prevent it from freezing?
If it freezes, how to solve this problem?
Thanks,
Dylan
|
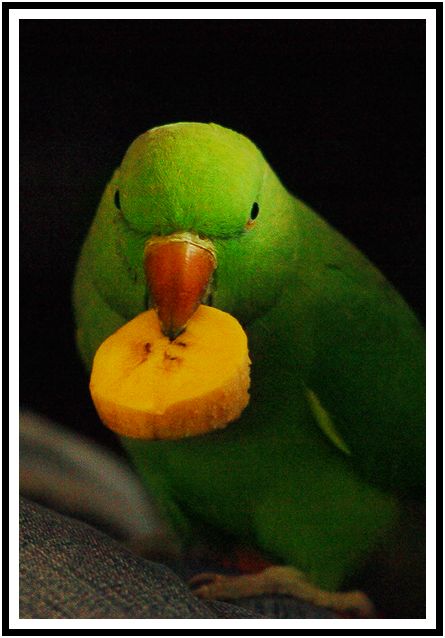
Freezing Heat Exchanger
Started by dylant, Mar 08 2007 04:14 PM
7 replies to this topic
Share this topic:
#1
Posted 08 March 2007 - 04:14 PM
#2
Posted 08 March 2007 - 09:07 PM
Dylan:
This is a very easy and simple problem for you to resolve or to overcome --- if you give us the Specific Basic Data.
You must tell us exactly what you are up against and what is motivating your concern in order for us to help you out. Otherwise we can't help you. The quality of our response and our help is directly proportional to the quality of your query. You haven't told us any specifics; therefore, how can you expect us to be specific -- or to even gather enough curiousity or good will so as to respond to your need(s).
Help us to help you. Give us specifics --- and be honest and forthright with your query. The more truthful information you deprive us of, the less we can help. Don't be afraid to bring your ignorance or lack of knowledge into the spotlight. Don't forget: You are a STUDENT. You are supposed to be ignorant of a lot of stuff that you haven't learned yet. That's why you are in a University - to learn, not to teach. It is no sin or crime to be an engineering student that is ignorant of a lot of engineering stuff. It is an awful mistake to not admit to it and, as a consequence, not reap or harvest the straight, truthful and helpful answers we can furnish to you and erase a lot of the stuff that you are ignorant of. Ignorance is simply a lack of knowledge in a specific area. It is not a defect or a failing --- unless, of course, you leave it just like that and don't ask questions or study the material.
What fluid(s) are you dealing with? What is their composition? What are the process conditions? What is your scope of work (just exactly what is it you are trying to accomplish & how)? What have you run up against that is stopping you from progressing towards an answer? What work effort have you put into it and what has caused your present situation? What are your thoughts on the subject? What type of exchanger are you studying? Why do you think it will freeze?
We await your specific reply --
#3
Posted 08 March 2007 - 10:20 PM
Art:
I apologize for not providing details.
I am heating up pure liquid methane (-150 Celcius) by running it through shell and tube heat exchanger. The fluid I use to heat up the methane is sea water (15 Celcius). The temperature of the liquid methane is extremely low, thus the higher temperature driving force, and I am afraid it would freeze the sea water inside the heat exchanger.
Will this happen? or will this not? If this will happen, how could we prevent such a situation? A senior engineer said that in the real life, it will never happen unless the plant is shut down. But. theoretically, I think it might happen.
Regards,
Dylan
I apologize for not providing details.
I am heating up pure liquid methane (-150 Celcius) by running it through shell and tube heat exchanger. The fluid I use to heat up the methane is sea water (15 Celcius). The temperature of the liquid methane is extremely low, thus the higher temperature driving force, and I am afraid it would freeze the sea water inside the heat exchanger.
Will this happen? or will this not? If this will happen, how could we prevent such a situation? A senior engineer said that in the real life, it will never happen unless the plant is shut down. But. theoretically, I think it might happen.
Regards,
Dylan
#4
Posted 09 March 2007 - 07:57 AM
Dylan:
OK. Now the picture is much clearer – although some additional details would have helped in yielding a more detailed response. My response is:
You are correct. Unless careful design and instrumentation is provided, it is very possible to freeze the coolant sea water with the LNG. This would be a catastrophic failure and you have good reason to be concerned and ask the question.
If you make a simple heat and mass RATE balance around the heat exchanger, you will quickly come to the conclusion that there is a critical flow that corresponds to the sea water fluid. If it fails to flow faster than this critical rate, it will start to accumulate the required loss of its Latent Heat of Fusion. When (and if) this happens, the sea water will freeze and simultaneously EXPAND and yield a tremendous hydraulic pressure that ultimately results in the heat exchanger or the piping bursting in order to relieve the pressure generated. Here, it is important for all engineers to learn that water has some of the most unique properties on our planet. It is one of the few fluids that expands when solidified. This is the reason why residential water pipes in Minnesota will burst in the Winter unless they are kept insulated and/or heated. This is also why some people in Minnesota always keep their water faucets running with a constant dripping during the winter nights when it is sub-zero outside. If you keep the water moving, you make it difficult for the water to freeze and subsequently burst your pipes.
The engineer that said it will never happen in the real life unless the plant is shut down is dead wrong! It can happen – and it WILL happen if the sea water flow is reduced below the rate that it takes to avoid it losing all its Latent Heat of Fusion. In the real life this can easily occur within the exchanger in certain spots and locations --- without causing ultimate serious damage. For example, bear in mind that you have many “dead spots” within a normal heat exchanger – locations where the flow is virtually at a standstill or very slightly moving. This is so because you have mechanical construction characteristics that force the fluid to make a lot of 90o and 180o turns inside the apparatus. All the baffles and partitions inside the exchanger have crevices and areas where there is little or nil flow. Where these appear is where your potential for freezing is most likely to be. It depends on the type, the size, and the orientation of your heat exchanger (actually, your “vaporizer”).
You failed to tell us the characteristics of your heat exchanger and that’s why I can’t comment any further. That’s what I meant about furnishing ALL the basic data.
Now, allow me to make some comments. You are vaporizing LNG (liquefied natural gas), so therefore you have a vaporizer – not a generic heat exchanger. That what I meant by being specific. The LNG is saturated – it is at -260 oF and only needs its Latent Heat of Vaporization to vaporize. I know this because I worked on LNG projects in the 1970’s and am very familiar with LNG vaporizers. I am also very familiar with the hazard of freezing of any water used to vaporize a cold liquid. I designed and built liquid CO2 vaporizers and had to design around this hazard. Liquid CO2 exists at -20 oF. So I am familiar with what concerns you. This type of vaporizer application should be designed and built by experienced and knowledgeable engineers. It is a very special application and one that requires a lot of thought on the alloys used, the potential hazards, the characteristics of the fluids, and the safety that must be designed into it.
If you are a student, how have you obtained the comments of a senior engineer?
I hope this helps resolve your concern.
#5
Posted 09 March 2007 - 09:14 AM
Dylan:
I think Art has provided you with an excellent presentation of the hazards that might exist. You (and your heat exchanger designer) must now develop a design with features incorporated to mitigate these hazards. In my mind, this is the essense of engineering.
I am not experienced in LNG, and the experience I have in anhydrous ammonia (and a little bit in Ethylene Plants) is not sufficient to fully identify proper mitigation strategies. I would think it prudent to interrupt the flow of LNG into the Vaporizer if the outlet cooling water flow or temperature were to drop to an abnormally low value. Stagnant areas where the two fluids are in thermal contact must be avoided. Other features may be needed, but I'll stop here before I get myself into trouble.
Good luck,
Doug
I think Art has provided you with an excellent presentation of the hazards that might exist. You (and your heat exchanger designer) must now develop a design with features incorporated to mitigate these hazards. In my mind, this is the essense of engineering.
I am not experienced in LNG, and the experience I have in anhydrous ammonia (and a little bit in Ethylene Plants) is not sufficient to fully identify proper mitigation strategies. I would think it prudent to interrupt the flow of LNG into the Vaporizer if the outlet cooling water flow or temperature were to drop to an abnormally low value. Stagnant areas where the two fluids are in thermal contact must be avoided. Other features may be needed, but I'll stop here before I get myself into trouble.
Good luck,
Doug
#6
Posted 09 March 2007 - 12:33 PM
Thank you for your response. Appreciate it.
I just build the model in HYSYS. I have not gotten into the details of what kind of equipment or type of heat exchanger we will be using, thus, I cannot provide you with that.
My friend's dad is a chemical engineer. I talked to him and he said that's not possible unless the plant is shut down or something goes wrong. And if that might happen, the solution is to increase the stream velocity. Theoretically it would, but in the real life it would not happen.
Is he wrong?
Regards,
Dylan
I just build the model in HYSYS. I have not gotten into the details of what kind of equipment or type of heat exchanger we will be using, thus, I cannot provide you with that.
My friend's dad is a chemical engineer. I talked to him and he said that's not possible unless the plant is shut down or something goes wrong. And if that might happen, the solution is to increase the stream velocity. Theoretically it would, but in the real life it would not happen.
Is he wrong?
Regards,
Dylan
#7
Posted 09 March 2007 - 02:50 PM
Dylan
As per my opinion you must have to talk about Vaporisers and not Heat Exchangers. You may either go for designing of Vertical Shell and Tube Vaporiser with glycol water in service or Open Rack Vaporiser with seawater in service. But in my opinion better to go for Open Rack Vaporiser. Hope This will give you exact idea about the designing.
Dharmesh
As per my opinion you must have to talk about Vaporisers and not Heat Exchangers. You may either go for designing of Vertical Shell and Tube Vaporiser with glycol water in service or Open Rack Vaporiser with seawater in service. But in my opinion better to go for Open Rack Vaporiser. Hope This will give you exact idea about the designing.
Dharmesh
#8
Posted 09 March 2007 - 03:39 PM
Dylan:
Your comment about doing the design on HySys is the main factor that I always find being the major obstacle in allowing Chem E students to fully understand the mechanisms and workings of the equipment that they are expected to design, erect, and operate in the future.
HysYs (or any simulator) knows exactly nothing about the pros and cons of different heat exchangers - including vaporizers. All HySys can do is exactly what you can do: calculate the latent heat of vaporization required to vaporize the LNG and possibly superheat it. That is not a job for a simulator program. That calculation can be done by you on a single calculation sheet.
Your problem really lies in visually conceiving what is going to happen when the -260 oF LNG enters the vaporizer and as it proceeds down the path of heat transfer. Take a look at the enclosed Excel workbook and try to see what I have sketched out. Please excuse the poor quality of the sketches; I've done them in a hurry because I'm on my way home for the weekend. I've sketched out the two diametrically opposed types of design for a vaporizer that uses a liquid fluid as the heat source. The simplest -and I think the most practical and safest - design is the "coil-in-a-box". This design is not as silly as you might first think. Visualize the fact that it is very easy to control and to ensure that the water does not damage the vaporizing coil in the event that it freezes. The box can be totally enclosed; all that is important is that it have an air vapor space that allows for expansion in the event of a freeze.
Now look at a common shell & tube heat exchanger that could be used as a vaporizer. Do you see the potential trouble spots? This type has no air space for expansion. In fact, I didn't have time to draw a mandatory expansion joint(s) on the shell side. Can you understand that since the shell is working at -260 oF and the tubes are working at an original 15 oF, you are going to have a tremendous differential expansion problem between the shell and the tubes? This is a major mechanical and structural problem with this design. I personally would stay far away from this type of vaporizer design. Now look at the silly coil-in-a-box design again. It doesn't look that silly anymore, does it? It automatically compensates itself for any temperature differential - without causing any mechanical stress or forces. That's what I mean by practical and safe design. It doesn't have to look sexy or avant guard; but it has to work consistently and safely. This, as Doug so accurately coined it, "is the essense of engineering".
I'm trying to make a strong point, trying to help you out in your design, and also help other students who may be reading this and thinking about how to handle their present and future engineering asignments. Do not place any faith on any simulator doing your engineering work. Rather, only place your faith in your ability to think out the problem, use your God-given ingenuity and the tools you have been taught, and apply them safely to the problem. That, in a nutshell, is engineering.
I believe you should concentrate on calculating the correct heat transfer rate that you need to vaporize the LNG to the temperature you require. After you have done that (which should be a piece of cake), sit down and start sketching out the type of heat transfer apparatus that will effect the required heat transfer you calculated in a consistant and safe manner. Study it well and scrutinize its disadvantages. It is commendable that you were able to challenge the idea of using sea water without considering a potential freeze-up problem. That was an excellent exercise of good engineering. However, now that you have found that it is possible to create a potentially hazardous situation if you use the wrong type of vaporizer, you should investigate all the other types available to you and settle for one that suits your needs and is proven to be safe by your logic and knowledge. After doing this, then you can model the correct type of vaporizer all your little heart desires. The real, tough engineering work will have been done by then.
Good Luck.
LNG_Vaporizer.xls 36.5KB
185 downloads
Your comment about doing the design on HySys is the main factor that I always find being the major obstacle in allowing Chem E students to fully understand the mechanisms and workings of the equipment that they are expected to design, erect, and operate in the future.
HysYs (or any simulator) knows exactly nothing about the pros and cons of different heat exchangers - including vaporizers. All HySys can do is exactly what you can do: calculate the latent heat of vaporization required to vaporize the LNG and possibly superheat it. That is not a job for a simulator program. That calculation can be done by you on a single calculation sheet.
Your problem really lies in visually conceiving what is going to happen when the -260 oF LNG enters the vaporizer and as it proceeds down the path of heat transfer. Take a look at the enclosed Excel workbook and try to see what I have sketched out. Please excuse the poor quality of the sketches; I've done them in a hurry because I'm on my way home for the weekend. I've sketched out the two diametrically opposed types of design for a vaporizer that uses a liquid fluid as the heat source. The simplest -and I think the most practical and safest - design is the "coil-in-a-box". This design is not as silly as you might first think. Visualize the fact that it is very easy to control and to ensure that the water does not damage the vaporizing coil in the event that it freezes. The box can be totally enclosed; all that is important is that it have an air vapor space that allows for expansion in the event of a freeze.
Now look at a common shell & tube heat exchanger that could be used as a vaporizer. Do you see the potential trouble spots? This type has no air space for expansion. In fact, I didn't have time to draw a mandatory expansion joint(s) on the shell side. Can you understand that since the shell is working at -260 oF and the tubes are working at an original 15 oF, you are going to have a tremendous differential expansion problem between the shell and the tubes? This is a major mechanical and structural problem with this design. I personally would stay far away from this type of vaporizer design. Now look at the silly coil-in-a-box design again. It doesn't look that silly anymore, does it? It automatically compensates itself for any temperature differential - without causing any mechanical stress or forces. That's what I mean by practical and safe design. It doesn't have to look sexy or avant guard; but it has to work consistently and safely. This, as Doug so accurately coined it, "is the essense of engineering".
I'm trying to make a strong point, trying to help you out in your design, and also help other students who may be reading this and thinking about how to handle their present and future engineering asignments. Do not place any faith on any simulator doing your engineering work. Rather, only place your faith in your ability to think out the problem, use your God-given ingenuity and the tools you have been taught, and apply them safely to the problem. That, in a nutshell, is engineering.
I believe you should concentrate on calculating the correct heat transfer rate that you need to vaporize the LNG to the temperature you require. After you have done that (which should be a piece of cake), sit down and start sketching out the type of heat transfer apparatus that will effect the required heat transfer you calculated in a consistant and safe manner. Study it well and scrutinize its disadvantages. It is commendable that you were able to challenge the idea of using sea water without considering a potential freeze-up problem. That was an excellent exercise of good engineering. However, now that you have found that it is possible to create a potentially hazardous situation if you use the wrong type of vaporizer, you should investigate all the other types available to you and settle for one that suits your needs and is proven to be safe by your logic and knowledge. After doing this, then you can model the correct type of vaporizer all your little heart desires. The real, tough engineering work will have been done by then.
Good Luck.

Similar Topics
Steam Pressure In Heat ExchangerStarted by Guest_mvanrijnbach_* , 15 Apr 2025 |
|
![]() |
||
Heat Exchanger Steam FlowStarted by Guest_aliebrahem17_* , 25 Nov 2024 |
|
![]() |
||
Discussion - Predict Storage Tank Heat Transfer Precisely By Jimmy D KStarted by Guest_raj shekhar_* , 25 Mar 2025 |
|
![]() |
||
Cross Over Temperature In Countercurrent Heat ExchangerStarted by Guest_panoska_* , 18 Feb 2025 |
|
![]() |
||
Aspen Hysys - Blowdown Utility Heat Flux MethodStarted by Guest_yuvi.ardekar1999@gmail.com_* , 27 Feb 2025 |
|
![]() |