|
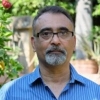
Globe Or Control Valves As Blowdown Valves
#1
Posted 10 October 2008 - 04:53 AM
Can any of the learned forum members throw some light on whether manual globe valves or control valves can be used without any issues for blowdown service in a oil and gas installation. For example, can the BDV of a two-phase separator be a control valve or a manual globe valve.
In one of the company standards for "Relief snd Depressuring", use of control valves is not advised for Blowdown service.
Also in some of the O&G installation P&ID's that I have come across, the BDVs are all FB ball valves with automatic on-off actuation with a downstream orifice.
Some learned members can also provide some practical know how on the subject and also give some sound logic for not using control valves.
Regards,
Ankur.
#2
Posted 10 October 2008 - 05:33 AM
I somehow feel that your 'two phase scenario' resembles Boilers; if true, then I understand, probably pneumatic cotrolled blowdown valves(Control valve in nature) are observed to be used.
Other learned members invited to correct/rectify the conceptuality.
Regards
Qalander
#3
Posted 10 October 2008 - 06:16 AM
As you know the BDVs are part of EDP system allow to reduce pressure from the maximum operating pressure to a specific threshold further to detection of outdoors abnormal F&G conditions. They will be manually trigged by dedicated PBs in CCR and shall be sized based on conditions defined in API 521 for relieving isolated fluid in specified time duration up to the specific pressure and then remain open up to eliminating the cause of emergency condition. Control (restricting) of flow would be done by RO downstream of BDV sized based on DP (Max operating pressure in upstream-Max back pressure of downstream e.g. Flare Header) and Max relief.
Considering above mentioned,and also considering BDVs normally are in closed condition and should be opened quickly (by remote for safety) for relieving large initial flowrate, are you still thinking manual globe valve or control valve could be suitable for defined functions?
Hope this can help.
Regards
#4
Posted 10 October 2008 - 06:18 AM
I somehow feel that your 'two phase scenario' resembles Boilers;
if true, then I understand,
probably pneumatic cotrolled blowdown valves(Control valve in nature) are observed to be used.
Other learned members invited to correct/rectify the conceptuality.
Regards
Qalander
[/quote]
Dear Qalander,
I am sorry to say that you are totally confused about what answer I am looking for. I am talking about Depressurizing scenario in an oil and gas installation where Blowdown valves are used to depressurize equipment such as separators, gas scrubbers etc. in order to mitigate the catastrophic effect event such as an external fire which can lead to equipment failure by rupture. Blowdown valves release the pressure in the pressurized equipment to the connected flare system thereby reducing the probability of rupture of equipment facing an external fire. The combined effect of high pressure and temperature can cause equipment rupture in a short duration. By reducing the pressure by depressurization of the equipment the stress on the equipment material can be reduced and a rupture may be prevented.
I suggest you read API STD 521 to get your fundamentals clear about Vapor Depressuring. It gives precise details about duration and extent of pressure reduction for equipments handling hydrocarbons.
Regards,
Ankur.
#5
Posted 10 October 2008 - 06:51 AM
I think Fallah has given an excellent outline of what usually constitutes a safety procedure in an emergency process blow-down scenario. I have designed and operated the type of process he describes and it is type that I prefer.
I have never seen or heard of automatic control valves being used in blow-down procedures. I have seen and used manual globe valves - although I prefer to design on a remote-actuated, full-bore, ball valve with an engineered Restriction Orifice (RO) located downstream to ensure the rate of controlled discharge (& depressurization). The discharge, of course, is either vapor or gas - not liquids.
The use of the RO mitigates the need for resorting to a control valve to allow some "control" over the discharge. The RO, of course, works on the principle of choked flow (constant mass flow rate) and has no moving parts or maintenance needs.
I can agree that in any emergency situation where depressurization is of high priority, even the use of a manual globe valve is of some value. However, in the design of the system it is hard to justify the immediate presence of a willing human being to be present at the precise spot where the globe valve is located in order to initiate the de-pressurization. The de-pressurization scenario is most often brought about due to the possibility of the Fire Case in the vicinity of high pressure, gas-filled vessels. I have always taken the attitude that in the event of the Fire Case, all workers in the area should not be there - but rather in a position where they can best control and monitor the Fire safely.
#6
Posted 10 October 2008 - 07:33 AM
The use of the RO mitigates the need for resorting to a control valve to allow some "control" over the discharge. The RO, of course, works on the principle of choked flow (constant mass flow rate) and has no moving parts or maintenance needs.
Dear Art,
Thanks for your valuable and complimentary explanations,but as far as i know choked flow would be created while upstream pressure is constant and the downstream pressure is below critical pressure of the fluid being relieved.
Thus, i think chocked flow is not the case around the RO downstream of BDV during Depressuriztion,because supposing constant back pressure e.g. in flare header, the upstream pressure is decreasing with time (gas filled vessel) and therefore mass flowrate would be decreased.
Please correct me if i am wrong.
Regards
#7
Posted 10 October 2008 - 12:35 PM
Whenever the ratio of the absolute source pressure to the absolute downstream ambient pressure is less than [ ( k + 1 ) / 2 ] ^(k / ( k - 1 )), then the gas velocity is non-choked (i.e., sub-sonic) where k is cp / cv of the gas or the isentropic expansion coefficient.
Regards
Manjeet
#8
Posted 10 October 2008 - 05:53 PM
I have designed and have had depressurization systems based on a controlled blowdown rate depending only on the RO – which depends on the steady, constant mass flow rate at choked flow. I am not the only one who bases their blowdown calculations and process design based on this and I have found that the design is conservative and it works. I believe that practical sense tells us that if one is depressuring to a presumed outlet pressure of approximately 2-5 psig, the pressure vessel gas contents will undergo choked flow since the vessel is obviously at an initial pressure of 15 psig or greater ---- if it isn't, then there is no need for controlled blowdown.
Contrary to what you indicate, the blowdown pressure will reach sonic (choked) flow when (as Manjeet infers) the ratio of the absolute source pressure to the absolute downstream ambient pressure is GREATER than [(k + 1) / 2]^(k / (k - 1)). And if you think about it carefully, you will note that this is true in almost all cases requiring careful depressuring control. Granted, the real, factual truth is that any classical API 521 depressuring case is basically a BATCH OPERATION, so that the vessel pressure is slowly being reduced as time goes on. However, the conditions mandating choked flow continue to apply until the above ratio is reduced to approximately 1.825 to 1.865 (in the case of methane gas). This means that the vessel will cease to produce sonic flow when it pressure is dropped down to approximately 27 to 28 psia – a pressure level that is of little concern compared to when the vessel is at an initial 500 psia.
Many process design engineers continue to rely on the choked flow controlled by an RO because of the simplicity and basic, fool-proof nature of the application – especially if the results are conservative and safety in the blowdown is ensured.
Installing a control valve in the system does not accomplish the type of flow control that the RO provides – at least not unless you install a lot of sophisticated flow and logic instrumentation to complement its operation. And that, basically is why the CV is not normally employed in a depressuring design.
#9
Posted 11 October 2008 - 05:17 AM
I accept choked flow would be existed in most time of depressurizing duration,but because of variable upstream pressure we would have chocked flow with variable mass flowrate.
I have attached a PDF file as output of PRO II simulator for Depressurizing of a vessel from 40bar to around 7 bar in fire case.Special attention to mass flowrate values (decreasing with time) is requested.
Regards
Attached Files
#10
Posted 13 October 2008 - 08:03 AM
I accept choked flow would be existed in most time of depressurizing duration,but because of variable upstream pressure we would have chocked flow with variable mass flowrate.
I have attached a PDF file as output of PRO II simulator for Depressurizing of a vessel from 40bar to around 7 bar in fire case.Special attention to mass flowrate values (decreasing with time) is requested.
Regards
Await for any comment/reply.
#11
Posted 13 October 2008 - 01:37 PM
Thanks for your valuable and complimentary explanations,but as far as i know choked flow would be created while upstream pressure is constant and the downstream pressure is below critical pressure of the fluid being relieved.
Thus, i think chocked flow is not the case around the RO downstream of BDV during Depressuriztion,because supposing constant back pressure e.g. in flare header, the upstream pressure is decreasing with time (gas filled vessel) and therefore mass flowrate would be decreased.
Please correct me if i am wrong.
Regards
fallah,
I think Art was focused on this statement and was attempting to explain that you would have choked flow throughout the depressurizing operation. He is absolutely correct in saying that.
I think we are all assuming that the downstream pressure will remain relatively constant and is not terribly important to this discussion. As long as the upstream pressure is >= 1.845*downstream pressure, then you will have choked flow. This range would cover nearly all of typical depressurizing operations. For example, using the numbers previously mentioned in this thread, between pressures of 500 psia and 33.8 psia (={14.7 + [2 + 5]/2} * 1.845) chocked flow conditions would exist. Only for the last small amount of depressurizing from 33.8 to 18.2 psia would we not be choked. Since this is the low pressure portion of the operation, it is of the least interest. So we can say the entire depressurizing operation is (essentially) at choked flow conditions.
I will concede your contention that the mass flow will decrease with time. That is because as the upstream pressure drops, so does the gas density. The gas velocity remains sonic, so the mass flowrate decreases.
#12
Posted 15 October 2008 - 03:54 PM
Typical issue with globe or control valve use in Emergency Depreussuring System :
i) The internal may fail and limit flow when it is on demand
ii) Failure of globe or control valve to full open position could lead to excessive flow
#13
Posted 16 October 2008 - 09:17 AM
Typical issue with globe or control valve use in Emergency Depreussuring System :
i) The internal may fail and limit flow when it is on demand
ii) Failure of globe or control valve to full open position could lead to excessive flow
Your opinion about the another Mr Montemayor's statement as:constant mass flowrate during Depressurization?
#14
Posted 17 October 2008 - 01:34 AM
#15
Posted 17 October 2008 - 03:52 AM
Sorry for extention of this thread. I fully accept in most time of depressurizing duration (except in the end part) choked flow would govern. But my specific statement is: due to upstream pressure decreasing, even though choked flow is remained (but with different upstream condition), the mass flowrate would be decreased.
What I have attached in one of my previous posts, is output of PRO II simulator for Depressurizing of a BDV among tens of them. I can send the relevant BDV report of a gas treating plant for showing that in all BDVs, regardless of their different conditions such as you mentioned above, the mass flowrate decreasing with time during depressurizing process.
#16
Posted 17 October 2008 - 12:47 PM
I accept choked flow would be existed in most time of depressurizing duration,but because of variable upstream pressure we would have chocked flow with variable mass flowrate.
I have attached a PDF file as output of PRO II simulator for Depressurizing of a vessel from 40bar to around 7 bar in fire case.Special attention to mass flowrate values (decreasing with time) is requested.
Regards
Await for any comment/reply.
Hi
In batch type of situation, as the pressure goes down, the density changes and it will change the mass flow rate, though the choked flow will remain.
Manjeet
Similar Topics
Parallel Control Valves Downstream Relief ScenarioStarted by Guest_pklavinsJ_* , 18 Jun 2025 |
|
![]() |
||
![]() Level Control ValveStarted by Guest_Ilyes_* , 03 Jun 2025 |
|
![]() |
||
Aspen Hysys - Blowdown Utility Heat Flux MethodStarted by Guest_yuvi.ardekar1999@gmail.com_* , 27 Feb 2025 |
|
![]() |
||
![]() Ditance Between Globe Valve And Ball ValveStarted by Guest_sima-f_* , 05 Jan 2025 |
|
![]() |
||
![]() Breather Valves - Liquid Movement In Breathing ScenarioStarted by Guest_panoska_* , 14 Dec 2024 |
|
![]() |