|
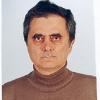
Steam Condensate Design Pressure
#1
Posted 01 August 2009 - 01:36 PM
I believe that design pressure of condensate has to be same as that of steam in this case. Only design temperature of condensate can be lower than that of steam.
Steam can escape downstream of the trap, so pipe design pressure should not be lower downstream of it (exactly as in a control valve).
Can the low design pressure of 14 Barg be justified for the condensate line? Any advise would be gladly welcomed.
#2
Posted 02 August 2009 - 06:27 AM
I believe that design pressure of condensate has to be same as that of steam in this case. Only design temperature of condensate can be lower than that of steam.
Steam can escape downstream of the trap, so pipe design pressure should not be lower downstream of it (exactly as in a control valve).
Can the low design pressure of 14 Barg be justified for the condensate line? Any advise would be gladly welcomed.
Seems steam trap might act as a certified and credible spec break.Check the type and specification of the trap in this regard.
Point of fallah is noted with thanks. The steam trap has not yet been specified in this case, but I have detected a similar Refinery case in the past (steam 44 Barg, condensate 14 Barg). The steam trap was of the thermodynamic type without any PRV on it.
Considering an inverted bucket trap (without PRV on it): if a valve on the condensate line is closed, the whole upstream piping will get the steam pressure, as soon as the bucket gets full of liquid (under the conditions of the case).
I do not know whether there are steam traps (without PRV) able to assure lower downstream design pressure. This is possible through a PRV, preferably installed on the condensate pipe (not on the trap).
I suspect that in the past a "habit" of condensate design pressure of 14 Barg was established, that is 2 Bar over operating pressure, without further check (for certified spec break, etc). But the steam has oper / design pressure 40 / 44 Barg. Can the "habit" be justified, or should it be replaced by a safer one?
#3
Posted 03 August 2009 - 03:16 AM
I have gone through your query. Me too is working in a design company of Refining sector. So I have some idea about that as I am preparing Design Pressure and temperature diagram of CDU, LPGRU etc.
I think the DP of condensate line should be 44barg i.e. the upstream DP. If you just think of the practical scenarion there would be some possibilities to carry over the steam through the condensate line. So it should be designed for high pressure viz. 44 barg as on the basis of DPDT you can allocate the pipe spec. The presence of any valve or relief system can cause drop in Operating pressure but not the design pressure and piping should always be designed for higher spec.
I have a doubt to on the difference between steam and condensate DP. Usually these should be same.Please check and let me know what is the reason behind this difference.
With warm regards,
Shubhasis <img src="http://www.cheresour...>/rolleyes.gif" style="vertical-align:middle" emoid="

#4
Posted 03 August 2009 - 04:56 AM
I think if the relief system to be designed properly,there is no need downstream piping to be designed for higher upstream spec.
#5
Posted 03 August 2009 - 02:27 PM
In the considered case (44 Barg steam / 14 Barg condensate) I think an error was made in the past creating a wrong / unsafe habit (see note Aug 1st), so I want to be quite sure before assessing this habit already applied.
fallah is right, a properly rated PRV shall assign same design pressure as its set point. However a valve can cause a drop in operating pressure, but the design pressure remains same.
#6
Posted 03 August 2009 - 11:19 PM
I agree with Fallah. Thanks for raising a good point.
#7
Posted 05 August 2009 - 11:50 AM
I agree with Fallah. Thanks for raising a good point.
Just to remind& re-affirm what 'fallah' has mentioned is that we have to consider 'Most Credible Scenarios' for process safety& optimized resource utilization's sake.
#8
Posted 07 August 2009 - 02:11 PM
Another related question: The 2/3 or 10/13 rule applies to exchangers (topic: Heat exchanger tube rupture from Sep 2 07 on). E.g. if DP=100 Barg in the high pressure side, the low pressure side does not need a PRV, if its design pressure is higher than 67 Barg (2/3 rule) or 77 Barg (10/13 rule), depending on exchanger hydrostatic test pressure.
Can this rule be applied in piping, e.g. steam design pressure 10 Barg, condensate desin pressure 6.7 Barg? We speak of existing pipes connected to each other, since 10 Barg would be set as design pressure for new pipes. If so, is there a written note that this rule is approved and safe enough?
#9
Posted 14 August 2009 - 11:09 PM
The condensate from the steam trap will be routed to the condensate flash vessel. There would not be any isolation between the steam trap and the condensate vessel. The flash vessel would be protected by it's own Pressure Safety Valve. Therefore, the piping downstream of the steam trap would also be protected against overpressure by this PSV. In view of this the design pressure of the condensate line need not be increased.
The 10/13 rule or 2/3 rule is to protect the low pressure side of the heat exchanger for tube rupture. As far as I know there is no extension of this rule for piping. (I may be mistaken though).
-abhishek
Edited by abhi_agrawa, 14 August 2009 - 11:13 PM.
#10
Posted 21 August 2009 - 02:59 AM
Judging by the design pressures mentioned, it appears the HP steam is being let-down to MP steam conditions.The Cond flash drum would have its own PSV.It would be much easier to analyze if P&ID/sketch were attached.
I too have never come across the 10/13 or 2/3 rules being applied for piping.
Best Regards,
A.Shetty
#11
Posted 04 September 2009 - 12:33 PM
I agree with Abhishek,
Judging by the design pressures mentioned, it appears the HP steam is being let-down to MP steam conditions.The Cond flash drum would have its own PSV.It would be much easier to analyze if P&ID/sketch were attached.
I too have never come across the 10/13 or 2/3 rules being applied for piping.
Best Regards,
A.Shetty
#12
Posted 13 September 2009 - 06:20 AM
I believe abhishek is right under the stated conditions, that is: no isolation between the stream trap and the condensate vessel. DP of condensate line is the PSV setting plus max ΔP from trap to vessel.
However in the original case (reported on Aug 1st 09) there are valves (not locked open) along the condensate line and no PSV on it, as indicated in the scdp.xls.
It is also noted that a standby heater with steam trap is similarly connected to the HP condensate header (not shown on scdp.xls).
Under these conditions, condensate design pressure is believed to be that of steam (44 Barg, not 14 Barg). It seems that this case is not common, but it can occur (e.g. in refineries).

#13
Posted 13 September 2009 - 08:12 PM
In case the valves you have shown are not locked open, the design pressure of the condensate line should be increased to HP Steam design pressure. It is probable, in your attached drawing, that one of the valve on the condensate line is closed and the operator opens that steam to the exchanger. In such a case, the condensate line will see HP steam pressure. So to protect this line, we should increase the design pressure.
Hope this helps,
Abhishek
Similar Topics
![]() Relief Path To Be Considered For Inlet Pressure Drop CalculationStarted by Guest_Ascanio E._* , Today, 03:02 AM |
|
![]() |
||
![]() Steam Used In ReboilersStarted by Guest_aliebrahem17_* , 05 Jul 2025 |
|
![]() |
||
![]() Negative Pressure Discharge / Negative At High PointStarted by Guest_felderosfelder101021_* , 05 Jul 2025 |
|
![]() |
||
![]() Rupture Disc Failure Well Below Max PressureStarted by Guest_vaibhav02_* , 02 Jul 2025 |
|
![]() |
||
![]() Distillation Column Top PressureStarted by Guest_halkeshhulk_* , 27 Jun 2025 |
|
![]() |