Chemical and Process Engineering Resources
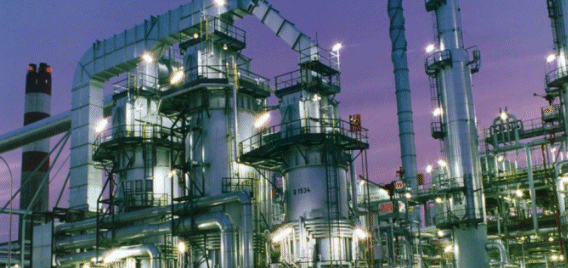
Need for Optimization in a Refinery
Most refineries are owned by integrated oil companies having a variety of interests, from exploration and production through refining and marketing to retail sales. Within such an organization the refinery works under the direction of the Head office. The Head office negotiates long-term and short-term crude supply contracts while the product Supply and Distribution department sells products. The refinery itself typically works within the overall framework of the organization to maximize the corporate profitability. This makes the refining an extremely complex and dynamic activity. Along with the complexity of refining, there also exists a great degree of freedom in refinery operations. For example, one of the most commonly used refinery products is fuel for automobiles, and the customer does not care about the complexity or simplicity of the refinery, what crudes it purchased, which processing technology it used, what blending or additive components it used in making the fuel. The customer is only concerned with the proper running of his vehicle and the value for the money spent. Therefore, the refiners have got both an enormous complexity and considerable freedom to satisfy the customer requirement and make profit. This requires the optimization of multiple objectives in the refinery’s business supply chain.
The objectives of refinery optimization include:
- Minimize crude landed cost at refinery
- Optimize refinery crude mix
- Optimize black oil generation and upgradation, optimize overall product mix and dispatch
- Minimize quality giveaway
- Optimize fuel consumption, minimize losses
- Optimize utilization of the assets
- Optimize inventory management
- Optimize capacity utilization and shutdown planning
- Optimize unit operations maintaining highest standards of safety, catalyst life and activity, etc.
All of the objectives mentioned above present a refinery with a challenging problem and an opportunity to maximize the overall profitability.
In a nutshell, the need and scope for optimization is so vast in a refinery that it is essential to use software tools not only to arrive at the best plan, but also to quickly evaluate the new optimum with internal or external changes in the business scenario. However, in today’s refinery environment, data acquisition, simulation and optimization tools often reside in “silos†in different groups across the refinery. This results in various local and plant-level optimizations only, not the most profitable refinery-wide optimization. A holistic view via an integrated model of the refinery is required to give refinery planners the ability to evaluate opportunities optimally, accurately and quickly.
Optimization means "the action of finding the best solution within the given constraints and flexibilities.†Linear Programming (LP) is a mathematical technique for finding the maximum value of some equation subject to stated linear constraints. It is commonly used in refinery planning to identify with confidence the most profitable refinery-wide operating strategy.
LP has been around since the 1940s and has now reached a very high level of advancement with the meteoric rise in computing power. The "linear" in LP stands for the algebraic aspect, i.e. all the constraints and objective functions are linear and satisfy two fundamental properties: proportionality and additivity. The "programming" in LP actually means "planning" only. The implementation of LP involves the development of an integrated LP model representing the refinery operations with all constraints and flexibilities and then solving it to determine the optimum plan.
The refinery-wide optimization using an LP model has been proven to bring economic gains far higher than unit-specific simulation models or advance process control techniques.
In short, the LP model is an excellent economic evaluation tool to drive the entire supply chain toward higher profit.
Some of the key areas for LP applications in the oil industry are:
- Grassroots refinery design/configuration
- Selection and evaluation of crude oils and raw materials
- Long-range and short-term operations planning
- Capital investments evaluation for process equipment
- Analysis of the profitability of merging and acquisition plans and the creation of ad-hoc models for joint venture refineries
- Evaluation of processing agreements and product exchange contracts
- Evaluation of new process technologies
- Control of the refinery performance
- Product blending control
- Down-time planning
- Inventory management
1 Comments