Chemical and Process Engineering Resources
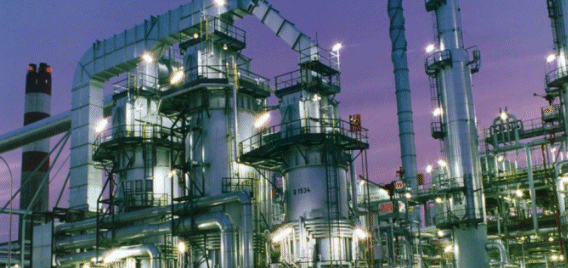
Refinery planning forms the foundation for the business decisions that have the biggest impact on refinery profitability.
A refinery typically prepares the following types of plans:
- Annual plans for annual budgeting, term crude contracts and maintenance shutdown planning
- Monthly rolling plans for spot crude purchases and conducting refinery operations inline with product demands
- Weekly plans for finding operating strategies for units at the weekly level, i.e. the refinery knows precisely which crudes it has and must decide which crude cocktails to run, how long to do so and how it is going to meet any particularly large or difficult product demands
- Strategic plans for future years and expansion projects
- Profitability improvement plans for plant -level modifications and revamp projects
The preparation of any of the above types of plans requires a set of standard procedures and an LP model customized for the refinery configuration.
Developing the Refinery LP Model
Development of a refinery planning LP model primarily involves customization of commercially available LP modeling software to refinery configuration. Table 1 provides a list of major suppliers and the LP software.
Supplier | LP Software |
Honeywell Hi-Spec Solutions | RPMS – Refinery & Petrochemical |
Aspentech | PIMS - Process Industry Modeling System |
Haverly | GRMPTS |
Development of a refinery LP model is an arduous task that demands sound, accurate and complete understanding of the refining process and planning functions. It requires compilation of enormous plant data and meticulous documentation of the same.
Steps in Developing a Refinery LP Model
Some of the major steps involved in the development of a refinery LP model include:
- Mapping of the existing planning process and data collection
- Development of a future planning process inline with best practices
- Finalization of Functional and Design Specifications (FDS) for the refinery LP model building, software and hardware configuration
- Refinery model building as per FDS
- Factory acceptance test of refinery model
- Tuning of model at site and trial usage for planning and case studies
- Site acceptance test of the refinery LP model
The list of steps mentioned is not exhaustive and requires micro-level activity planning. The role of an LP consultant is very important as he has to balance the needs of the refinery planner and the intricacies involved in modeling each constraint and options.  Initially, it is better to keep the model simple and understand its behavior.  The complexities must be added gradually, keeping in mind what economic impact they have on refinery profitability.
Description of the Refinery LP Model
A good LP model is one that closely represents the operational reality of a refinery. A typical refinery LP model contains the end-to-end configuration of the refinery with a detailed representation of primary and secondary processing units, blending facilities, power and utilities. A model contains structural data, or fixed data, which represents the physical reality concerned, and variable data, which expresses the contingency of the particular problem. The addition of variable data like costs, prices, raw materials availabilities and products requests, process unit’s capacities and product quality specifications enables the model to set up a problem, from which infinite variant cases can be created and run to arrive at the optimal plan.
Mathematically, an LP model consists of a matrix, while for the users it can be better thought of as a set of data tables necessary and sufficient for the automatic matrix generation. A typical refinery model represents an LP matrix with 1,500 rows, 3,500 columns, 1,500 equations, 1,500 constraints and 5,000 variables. The LP software uses different optimizers like MOPS, XPRESS, OSL, etc. to solve the matrix.  RPMS uses the state-of-the-art XPRESS optimizer software licensed from Dash Associates.Â
The model can have different time period variants to meet different planning objectives associated with Annual Planning (1X4 quarter), Quarterly Planning (1X3 months) and Monthly Planning (1X4 weeks).
Some of the key features of a refinery LP model include:
Objective function in an LP modelÂ
A refinery LP model is generally configured with a single objective function of maximizing the profit as explained below:
- To maximize {S (Product value) - S (Raw Material cost) - S (Refinery Variable Costs), subject to the various constraints defined in the model including the inventory value and carrying cost parameters.
Modeling techniques and optimization features
A refinery LP model contains modeling capabilities like Successive Linear Programming (SLP), Mixed integer programming (MIP), Implicit and Explicit Pooling, Multi-period modeling, Distributive property recursion, attribute error tracking, rigorous sulfur distribution, etc. Compared to an approach based on average values, these techniques provide very accurate estimates of yields and qualities of finished goods, all the while keeping short computation times.
Additional information can be obtained by referring to standard books on LP to understand the meaning of the LP terms used above. A good reference book is Operations Research, 7th Edition by Hamdy A. Taha, Univ. of Arkansas, and Fayetteville.
The refinery LP models use latest unit modeling techniques like swing cut modeling, delta vector modeling and mode wise modeling.
The crude and vacuum unit is modeled based on the stream TBP (True Boiling Point ) cut point scheme. The crude assay manager software like ASSAY2, PASSMAN uses TBP cuts and the TBP curve of the crude oils from the various crude assay database for generating the crude wise yields and properties. It is possible to model the single physical crude unit into several logical units depending refinery specific requirement. For example, a refinery processing high sulfur (HS) and low sulfur (LS) crudes in blocked out operation can be modeled with two logical unit one for HS and another for LS crude operation.
The secondary units are modeled using delta-yield vector or mode wise yield vectors. For example, the catalytic cracker is generally modeled by setting up base yield vectors with yield controlling delta vectors for Feed UOP K, MeABP and Severity/Conversion. The static input data for determination of delta vectors can be generated from kinetic models, test runs and standard correlations. Relevant capacity and quality constraints on the feed and product side are configured. All possible blending options for unit feed and products are configured. Unit wise steam, power, fuel consumption and catalyst consumption are also built in. The rigorous recursion structure for feed and product stream properties is set up. For example, sulfur in cat cracker streams is recalculated on the basis of feed sulfur changes.
1 Comments