Chemical and Process Engineering Resources
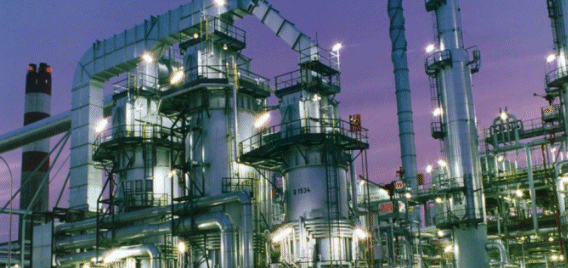
Experiences and Benefits
- Building a refinery LP model is not a trivial exercise. It needs clear understanding of the entire web of refinery operations and the compilation of good quality data. The model development activity is very time consuming and can take about a year for developing a good and robust model. The following important points need to be kept in mind while building the model:
- Make sure that the crude cut strategy represents accurately the qualities (and variations) of the cuts that are critical for a site. For example, if there are issues concerning distillate 95% point or CCR values, characterize your crude cuts very thinly around the heavy gas oil/atmospheric residue cut (typically in the 330 - 390C range).
- Obtain good representation of unit operating modes and parameters from process models. As the LP cannot work with non-linear correlations, there is a need to linearize the non-linear behavior of process units by introducing several linear "vectors.â€Â These vectors can be generated through sound refinery process models (e.g. KBC Profimatics FCC-SIM for the FCC, REF-SIM for a reformer, etc.) for different feeds/crudes, operating conditions (severities, conversion, etc.), etc.
- Ensure that the model has sufficient flexibility to generate feasible solutions in the first place. It is easier to start with a fairly "loose" model, which can be subsequently tightened.
- Make sure that the crude cut strategy represents accurately the qualities (and variations) of the cuts that are critical for a site. For example, if there are issues concerning distillate 95% point or CCR values, characterize your crude cuts very thinly around the heavy gas oil/atmospheric residue cut (typically in the 330 - 390C range).
- Interpretation of LP Output: The task of analyzing the LP output is not a simple exercise, mainly due to the limitations of the technique and the complexity of its output. It requires sustained effort in generating and analyzing the various feasible and optimum solutions and rigorous sensitivity analysis.
- Computation Time: Today, we solve substantially more complex LP problems in mere seconds on our desktop PCs. The running time limitations have lost much of their relevancy with the availability of desktop PCs with higher computing power. For example, solving four-period models takes only about two to three minutes on a Pentium-IV and 256 MB RAM PC.
Benefits of LP in Refinery Planning
LP works on the principles of pure mathematics and Petroleum Refining is more complex than the mathematics that describe it. With all the approximations and uncertainty we should not expect or even desire a “true mathematical optimum.â€Â LP should be viewed only as a mathematical optimization technique, or as a convenient method to obtain a feasible and economic plan for the supply, processing and logistic activities of a petroleum complex, together with a description of its driving forces and constraints.  In day-to-day working, an LP solution helps in achieving two key practical aspects:
- It facilitates in the decision-making process by keeping the focus on profit under any scenario
- It provides the targets and operating strategies for the actual operation
LP does much more than planning for the future. LP refinery models always challenge the people and their deep-rooted rule-of-thumb approach in the refinery operations. The implementation of LP models often creates awareness among executives and management about the profit factor. LP-based planning can provide potential benefits to the tune of 15-20 cents/bbl. One of the major advantages of LP programming is that it acts as a watch dog for the refinery operations – always asking for more, the LP model helps in identifying the bottlenecks in processing more crude and directs in achieving the benchmark for operation. It clearly tells the inefficiency of operations in terms of money, and that’s where it is very close to management’s heart.
The LP solution has not only enabled arriving at a better plan, but has also provided many valuable insights for optimizing unit operations, crude mix and product blending.  The other most important benefit realized is it quantifies the impact of a change in a variable on overall refinery profitability. As a tool, RPMS provides answers to the typical questions that refinery management asks for faster decision making, including: What is optimum HS-LS crude mix?, How to maximize distillate yield and minimize the fuel & loss?, What products to be maximized?, Which units to be run and what capacity levels?, When to plan unit shutdowns?, etc.
Keys to Implementation
The output from an LP model gives us an optimal plan. In practice, the real benefit comes from implementation of the strategies and guidelines from the model.  Implementing all of the LP solutions in a refinery is a difficult task.  Product pricing and unit constraints often change weekly, but changing unit operating philosophy and addressing hardware constraints take time to accomplish.  Even after the steps for improving optimal performance have been identified and implemented, if the pressure to improve is removed, operation tends to return to the older, more comfortable routine. The LP optimization group must continue to stress the potential savings while improving the operations until the savings are achieved.
The key to the successful implementation of LP in refinery planning is an integrated approach that addresses the following issues:
- Regular Model updates and maintenance: There is one human tendency of giving maximum care and attention to the thing which is very valuable or important to him. The same tendency should be kept alive for LP models, as these models provide the decision-making power (involving large amounts of money), money-related policies and future action plans. The models are continuously interacting with inside constraints and outside changes (price and product demands), making them dynamic in nature. All of these factors imply that the maintenance of these models should be carried out as regularly as possible. The type of updates can be a reduction in the yield of unit, change of catalyst, property change of secondary stream, energy consumption reduction due to application of energy conservation suggestion, etc.
- Integrated application of different software solutions: Refineries use a number of stand-alone software solutions like Automation Blenders, Online analyzers and sensors, APC, Scheduling software, Simulation software, RTDBMS for optimization of operations. There is a strong need to integrate the working of such software to create the maximum benefit by bringing the operations and blending close to the LP output.
- Clear and well documented planning procedures: There are no two opinions on using LP based software for planning. The real problem of using the LP for economic decision-making is how to interpret the LP results and how to use it for decision-making. The planning tool needs to be backed by clear cut and systematic planning procedures. The entire planning process should be carried out under the overall supervision and guidance of top management group in an integrated way. The procedures for the four key functions of plan preparation, plan implementation, plan monitoring and “what-if†case studies must be in place and working to enable the success of LP optimization.
The Bottom Line
Petroleum refining in the new millennium will continue to be an extremely competitive business. Â The application of LP methodology has shown potential margin benefits of 15-20 cents/bbl for the refineries.
The bottom line is that experienced people are the key to success: software and computers, no matter how powerful and quick, are not the substitutes for understanding and optimizing the refinery business. However, LP technique has provided an efficient and effective method to quickly evaluate and quantify the impact of internal and external changes on overall refinery profitability.
References
- LP Modeling – Past, Present and Future , Michael A. Tucker, Senior Staff Consultant ,KBC Advanced Technologies, Inc., Houston, Texas
- Notes on LP , Uberne A. Tapia , Manager , Refinery Planning & Optimisation , Honeywell Hi Spec Solutions , Houston , Texas
- Operations Research , 7th Edition , Hamdy A. Taha , Univ. of Arkansas , Fayetteville
- Decision-making and Modeling in Petroleum Refining , Hans Hartmann, Independent Consultant
- Multi Objective Intra-Refinery Optimisation , Ahmed Sirag Khogeer Department of Chemical Engineering , Colorado State University
- Honeywell Web site , www.honeywell.com
- Hartmann, J.C.M.; Distinguish between scheduling and planning models; Hydrocarbon Processing, Vol. 77 Issue 7, p93-98, Jul 98.
- RPMS Introduction http://www.acs.honeywell.com/ichome/Doc/0/O2N58SSJ5BAH3AJ1001B69DOBB/RPMS.pdf
Â
1 Comments