Chemical and Process Engineering Resources
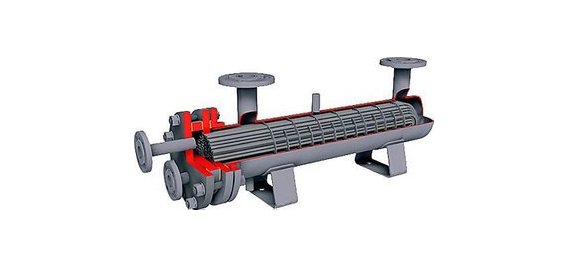
Exploring Other Considerations in Heat Exchanger Specification
Prior to completing the heat exchanger specification data sheet, the engineer should answer questions such as:
Are there any phase changes expected to occur in the heat exchanger?
Are there any dissolved gases in either stream?
Are there any dissolved or suspended solids in either stream?
What are the operating pressures of the streams?
How much pressure loss is available in the exchanger (for existing pumps)?
What are the fouling tendencies of the fluids involved?
Are either of the fluids non-newtonian?
Are either of the fluids corrosive? What material of constructions are required?
What types of elastomers and/or compression gaskets are compatible with the fluids?
Are either of the fluids considered lethal to plant personnel?
Is mechanical cleaning expected to be necessary for one or both fluids?
Is there a cleaning solution that may be effective for the exchanger?
How much room is required for maintenance of the new exchanger?
Having answers to these questions can help ensure that your heat exchanger specification, and ultimately the heat exchanger that you purchase, is right for your heat transfer duty.
Phase Change
Even in liquid-liquid heat transfer duties, it's important to recognize the potential for phase changes inside the heat exchanger. For example, if a process stream is available to 350 °F to plant water from 100 °F to 300 °F, it's very important to note that both the inlet and outlet pressure of the plant water stream. If the water stream is not under enough pressure, it may undergo partial vaporization. In this case, the vapor pressure of water at 300 °F is about 52 psig. So, for a heat exchanger with a nominal pressure loss of 10 psig, the process water should enter the exchanger at a minimum pressure of around 70 psig.
Dissolved Gases
While not always common, there are several instances where a mostly liquid process stream may pickup dissolved gases. It's important to recognize that dissolved gases can have a profound negative impact on liquid heat transfer as the dissolved gases serve as a significant resistance to heat transfer. If you suspect that dissolved gases may be present, the best bet is to run the process stream through a separation vessel to allow for vapor disengagement prior to transferring heat to or from the stream. Trying to design for a stream with dissolved gases is very difficult and often times uneconomical. A classic example of this can often be found in the interchangers in amine units used to treat natural gases. Through the absorption column, the amine solutions can pick up significant quantities of carbon dioxide that should be removed prior to transferring heat with the amine solution.
Dissolved and Suspended Solids
Dissolved solids can be very common in the chemical processing industry. In fact, a general rule of thumb for cooling tower water is that it should not be heated to temperatures in excess of 120 °F. The reason behind this guideline is that at temperatures above 120 °F, some of the common water treatment chemicals used in the water can quickly plate out onto heat transfer surfaces. Usually, these are carbonate salts which follow an inverse solubility curve. This means that as temperature increases, the salts actually become less soluble in water rather than more soluble as is usually the case. Inverse soluble salts can be found in other processing stream as well and are not confined only to cooling tower water.
Suspended solids can pose obvious problems for heat exchangers. Aside from the common problem of pluggage, suspended solids can also cause erosion of the heat transfer surfaces if the velocity in the heat exchanger is too high. If suspended solids are present, it's advisable to obtain a particle size distribution and chemical analysis to determine the relative hardness of the particles. For example, hard particles that range in size from a few microns to up to 0.20 mm would have to be addressed differently than a slurry of relatively soft particles such as a powdered solid. Usually, a plant will have a well documented history of what type of exchangers work well with a solid-laden stream and often times, plants will establish velocity limitations for pipelines and other processing equipment.
Operating Pressure
Examine the operating pressures of each stream that are to enter the heat exchanger. Many companies have policies dictating that the design pressure of a process vessel must be a certain factor above the highest operating pressure. For example, if the highest operating pressure for a heat exchanger is to 100 psi, then a reasonable design pressure may be 150 psi or 200 psi. Remember, that the higher the design pressure, the more expensive the exchanger will become as the wall becomes thicker.
![]() |
Figure 5: Operating Pressure vs. Time Chart |
Additionally, give some thought to what will happen if a leak occurs within the heat exchanger. The higher pressure fluid will leak to the lower pressure fluid. For example, consider a process stream at 50 psi and cooling tower water at 75 psi. If a leak occurs, the cooling tower water will leak into the process stream. The engineer must evaluate the consequences of such leakage and determine which fluid should be at the higher pressure.
As with any piece of chemical process equipment, it can be subject to mechanical fatigue. Consider a heat exchanger where the two streams have operating pressures that are very close to one another. Without extreme pressure stability (which is often difficult to maintain), a run chart of the pressure versus time may look like the chart in Figure 5.
Notice how the stream can be allowed to actually cross pressures in the heat exchanger if the two streams are close in operating pressures. This scenario, if extreme enough, can cause flexing of thinner material surfaces inside of heat exchangers and lead to premature failures.
Available Pressure Loss
If preparing to install a heat exchanger in an existing process system, the engineer should examine any pumps in the system to determine how much pressure loss is available. Generally speaking, most heat exchangers should need between 5 and 15 psi of pressure loss to operate effectively. For known fouling fluids, a higher pressure loss (corresponding to a higher velocity) will help keep the exchanger clean for a longer period of time. Also remember that pressure loss is proportional to the fluid viscosity. Specifying a pressure loss of 5 psi for a process fluid with a viscosity of 300 cP may result in a very large heat exchanger.
If your pumping system cannot handle the necessary additional pressure loss to obtain a good heat exchanger design, then an impeller change out, a new pump, or an additional pump in series may be justified. When utilizing a shell and tube exchanger, you can expect the pressure loss on the tube side to be higher than the shell side in most cases.
Fouling Tendencies of the Fluid
The engineer should also be aware of the fouling tendencies of the fluids involved. Through personal experience, interviews with other plant personnel, or investigation into other heat exchangers, the engineer can usually determine how quickly a particular fluid may foul an exchanger. Many plants will have a library of shell and tube fouling factors for various process duties.
Probably one of the most common errors made in specifying a new heat exchanger is overdesign. Anticipating fouling is smart, overdesigning too far however will ensure that fouling will occur. Choose your fouling coefficient carefully. Remember, that specifying too large a fouling factor will often result in more tube or parallel channels. This will lower the velocity in the exchanger and actually promote the fouling. This is a balancing act that is well worth a little time and effort.
When considering a fouling factor, it's very important to note the type of equipment that may be used in the service. Another common mistake during heat exchanger specification is to apply fouling factor information from one type of equipment to a completely different type of equipment.
Remember that shell and tube fouling factors have been compiled over decades through experience and temperature measurement. Also, realize that typical overall heat transfer coefficients for shell and tube may range from 150 to 400 Btu/h ft2 °F while compact heat transfer technologies can easily obtain overall heat transfer coefficients ranging from 600 to 1000 Btu/h ft2 °F. If we examine the equation:
![]() | Eq. (6) |
for a shell and tube exchanger and for a compact heat exchanger, we'll see how the difference can impact designs. If the engineer were to specify a fouling factor of 0.001 h ft2 °F/Btu independent of the type of heat exchanger used, the result would look like this:
So, the U-value for the shell and tube went from 136 to 120 Btu/h ft2 °F through the fouling coefficient. The U-value for the compact exchanger went from 445 to 308 Btu/h ft2 °F through the fouling coefficient. Therefore, the shell and tube overdesign is about 12% while the compact exchanger overdesign is over 40%.
The specifying engineer must realize where the fouling factor information is derived from and apply it properly in the future. While shell and tube exchangers have long used fouling factors, compact heat exchangers generally utilize a "heat transfer margin"Â that is typically 10-25% over the clean heat transfer coefficient. This change in language was designed to avoid confusion as shown above and to bring the overdesign between the two technologies onto even ground to avoid problems. Also realize that overdesigning in compact heat exchangers is even more detrimental to performance than in a shell and tube heat exchanger.
Non-Newtonian Fluids
While most fluids in the chemical processing industry are Newtonian in their flow behavior, some are not. In short, a Newtonian fluid is one whose viscosity in NOT dependent on the forces acting upon it (shear stress in heat exchangers), only on the fluid's temperature. Some fluid, know as being non-Newtonian, have flow characteristics such that they can actually become more or less viscous depending on the forces acting on the fluid. Confirming that a fluid is Newtonian during the design stage can save the engineer from procuring a heat exchanger that is vastly over or under sized later.
Corrosion Potential and Materials of Construction
Specifying materials on construction for the heat exchanger is an extremely important part of the overall process. Again, most plants have some history regarding what metals are appropriate for their process fluids. Typically, if one fluid requires a higher metallurgy than another, then that fluid is placed on the tube side of a shell and tube exchanger to minimize costs as cladding a shell can become quite expensive.
It's important to consider temperature and pH when deciding on a material of construction for your exchanger. If you're not sure what metal you need, consult with a corrosion expert as this is one aspect of heat exchanger design that no one can afford to get wrong.
If your duty does require an expensive alloy, then a compact heat exchanger may cost significantly less considering their higher overall heat transfer coefficients. Another point to remember is that just because a fluid is compatible with a stainless steel tube for example, it may not be compatible with a stainless steel plate that has been pre-stressed (during the pressing process). Pre-stressing of metals can make them susceptible to pitting corrosion such as chloride attack. Consult with manufacturers of compact equipment. While they will seldom take the legal responsibility for choosing a material of construction, then can point you in the right direction and save you from making a costly mistake.
Elastomer and Compreesion Gasket Compatibility
Depending on the type of heat transfer technology that is being considered for the application, a check of gasket compatibility may be required. Elastomer gaskets are most commonly offered in materials such as EPDM, Nitrile, PTFE, and FKMG (a generic form of Viton-G from Dupont). Elastomer gaskets can seldom be rated for temperatures in excess of 320 °F. Generally speaking, the engineer should seek a recommendation from the heat exchanger manufacturer as they usually have extensive databases that show the best gasket choice for a given application.
For compression gaskets, such as those used on the heads of shell and tube exchangers, there are a couple of rules of thumb to keep in mind. In addition to the need for the gasket to be compatible with the process or service fluid, the engineer may need to decide between a metallic or non-metallic compression gasket. Consider this guideline:
Find the value of : Operating Pressure (psig) x Operating Temperature (°F) If this value exceeds 250,000, the use of a metallic gasket should be strongly considered. Additionally, non-metallic gaskets are seldom used at pressures in excess of 1200 psig and temperatures in excess of 850 °F. |
Lethal Service Requirements
The ASME pressure vessel code stipulates very specific pressure vessel requirements for heat transfer service that are qualified as "lethal"Â. If the service requires an ASME "L"Â stamp, be sure to specify this to the heat exchanger manufacturer.
Cleaning Considerations
Some process fluids can leave fouling deposits that can be especially difficult to remove. Sometimes, these deposits can be removed by chemical cleaning. Chemical cleaning of heat exchangers, in general, is popular in industries that utilize sanitary protocols (food, pharmaceutical, etc.) and chemical cleaning is widely accepted in the chemical process industry in Europe. Chemical cleaning requires additional equipment, cleaning chemical, and a method of disposing of the chemical cleaning agent. Chemical cleaning can be a good choice in the following instances:
- The fouling deposit can be easily dissolved and removed by a readily available cleaning agent.
- The heat exchanger fouls quickly and must be cleaned fairly often (4 or more times a year)
- The heat exchanger to be cleaned has a relatively small hold up volume so that chemical cleaning equipment and the volume of cleaning agents can be minimized.
For heat transfer duties where chemical cleaning does not seem like the best choice, the engineer must be sure that the fouling fluid is placed on a side of the heat exchanger that is readily accessible for mechanical cleaning. Mechanical cleaning usually consists of a high pressure water spray of the affect area, although additional scraping can sometimes be necessary. Floating head shell and tube heat exchangers, gasketed plate exchangers, spiral heat exchangers, and some welded plate heat exchangers allow good access for mechanical cleaning.
A final consideration for mechanical cleaning is the space required around the heat exchanger. When choosing an installation location, be sure that the necessary maintenance space is available for proper and safe maintenance of the new equipment.
1 Comments
what happens if temperature cross occurs in heat exchanger?