Chemical and Process Engineering Resources
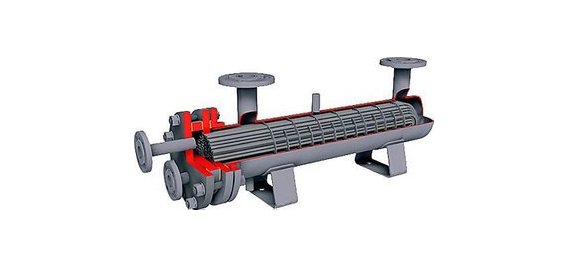
Avoiding Specifications That Are Too Specific
One final pitfall that the specifying engineer should avoid is making the heat exchanger specification too rigid. The engineers that design the heat exchangers are the experts, give them as much freedom as possible and allow them to present you with the best option(s) that will work well for your application.
As an example, consider the following:
A process stream requires Alloy C-276 material to guard against corrosion. The stream needs to be cooled with cooling water before being sent to storage. The metallurgy makes the process stream an immediate candidate for the tube side of a shell and tube heat exchanger. The cooling water is available at 80 0F and must be returned at a temperature no higher than 115 0F. The process engineer realizes that with the water flow being placed on the shell side, larger flow rates will enhance the heat transfer coefficient. The basis for the heat exchanger quotation was specified as follows:
Tube Side | Shell Side | |
Flow Rate (GPM) | 500 | 1800 |
Temperature In (°F) | 280 | 80 |
Temperature Out (°F) | 150 | 92 |
Allowable Pressure Drop (psig) | 15 | 15 |
According to the engineer's calculations, these basic parameters should provide a good shell and tube design with a minimum amount of Alloy C-276 material (an expensive alloy). The completed specification sheet is forwarded to many manufacturers, including those that could easily quote plate and frame or another compact technology. A typical plate and frame unit designed to meet this specification would have about 650 ft2 of area compared to about 420 ft2 for a shell and tube exchanger. A plate and frame unit designed to the above specification is limited by the allowable pressure drop on the cooling water. If the cooling water flow is reduced to 655 GPM and the outlet water temperature rose to 115 °F, the plate and frame heat exchanger would contain about 185 ft2 of area. The unit is smaller, less expensive, and uses less water. The load being transferred to the cooling tower is the same.
The theory that applied to the shell and tube heat exchanger (increasing water flow will minimize heat transfer area), works in exactly the opposite direction for compact technologies. The larger water flow actually drives the cost of the unit upward. Rather than supplying a rigid specification to all heat exchanger manufacturers, the engineer should have explained his goal in regards to the process stream. Then he could have stated the following:
The process stream is to be cooled with cooling water. Up to 2000 GPM of water is available at 80 °F. The maximum return temperature is 115 °F.
This simple statement could result in vastly different configurations when compared with the designs that would result from the original specification.
1 Comments
what happens if temperature cross occurs in heat exchanger?