Chemical and Process Engineering Resources
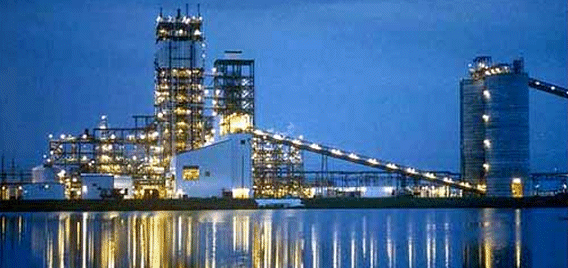
Steam reforming of hydrocarbons for ammonia production was introduced in 1930. Since then, the technology has experienced revolutionary changes in its energy consumption patterns.
Ranging from an early level of 20 Gcal/tonne (79.4 MBtu/tonne) to about 7 Gcal/tonne (27.8 MBtu/tonne) in the last decade of the 20th century.
Reforming Section Developments
In the conventional process, steam reforming is carried out in a fired furnace of the side fired or top fired type. Both need large surface areas for uniform heat distribution along the length of the catalyst tubes.
![]() |
Figure 1: Overall Layout of a Steam Reforming Plant for Ammonia Synthesis (Click to Enlarge) |
This process has several disadvantages. For example, it is a thermally inefficient process (about 90% including the convection zone) and there are mechanical and maintenance issues. The process is difficult to control and reforming plants require a large capital investment.
Gas Heated Reformers
Future technologies include the use of Gas Heated Reformers (GHR), which are tubular gas-gas exchangers. In the GHR, the secondary reformer outlet gases supply the reforming heat. Though it is not presently being used widely, GHR has certain advantages over fired furnaces. Table 1 shows a list of these advantages. Kellogg's Reforming Exchanger System is an example of GHR technology. Although GHR results in reduced energy consumption, a comprehensive energy conservation network should be established to maximize the benefits of a GHR system.
Fired Furnace | Gas Heated Reformers |
Large volumes | Smaller volumes |
Larger surface area and heat loss | Reduced surface area and heat loss |
Complex instrumentation | Simplified instrumentation |
High maintenance costs | Low maintenance costs |
Large convection zone | No convection zone |
Stack losses | No stack losses |
High fixed capital costs | Low fixed capital costs |
Reduced catalyst tube loss from high temperature and uneven heat distribution | Longer tube life due to uniform heat distribution |
Increased downtime required for shut down | Reduced downtime required for shut down |
Well established process | Yet to gain wide acceptance |
0 Comments