Chemical and Process Engineering Resources
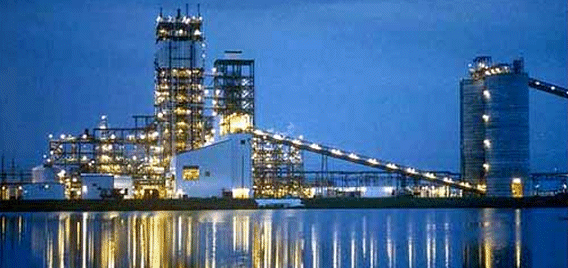
Hydrogen Separation
Lechatelier's Principle states that a reaction equilibrium can be shifted by applying external forces. This offers a means of removing products from the reaction mixture to increase the conversion per pass. In reforming, experiments have been performed up to 500 °C (932 °F) and 20 bar (294 psig) using a palladium membrane to remove the product hydrogen. These experiments have results in a significant increase in methane conversion as can be seen by the following case study.
Case Study on the Membrane Separation Process
The separation of hydrogen from the product gas of the reforming process can result in significant productivity gains when compared to the current processes being employed. The base case for this study is a conventional steam reforming plant based on natural gas operating at 1750 tonnes per day. The operating conditions of the plant are assumed to be the same as those typically employed today and the only modification is the introduction of hydrogen separation. The tests for the membrane separation have been carried out at 500 °C (932 °F) and 20 bar (294 psig), these conditions will function as upper limits for the process to be considered in this study. Membrane units will be considered after the primary reformer (at 60% hydrogen separation), after the secondary reformer (at 60% hydrogen separation), and after the High Temperature Shift (HTS) converters (at a 50% hydrogen separation)
The following assumptions are made in this case study:
- The natural gas feed at the primary reformer is the same for both cases.
- The primary reformer exit temperature is the same for both units.
- The primary reformer operating pressure is the same for both units.
- The process air is fed to the secondary reformer at optimal conditions and any remaining nitrogen that is required is supplied through an Air Separation Unit (ASU) and is available at 0.1 kg/cm2 (1.42 psig)
- Any extra energy consumption in the ASU is considered for the revamp case.
- All of the heat from the process gas from the primary reformer to the carbon dioxide removal section is used in a steam network.
- No changes in the carbon dioxide removal system are considered.
- The pressure drop across the front end of the process is kept constant for both systems, thus the synthesis gas compressor suction pressure remains constant.
- The loop pressure is the same for both processes and is controlled by changing the purge gas quantity.
- The existing compressors are capable of handling any additional loads.
- No scheme changes are considered in the synthesis loop.
- All hydrogen from the membrane separation unit is available at 9.0 kg/cm2 (128 psig)
- The productivity analysis is carried out on the ammonia plant only (the urea plant is excluded)
- A complete steam balance is included on both processes. Changes in the steam balance are considered for:
Steam generation from the front end of the processes
Steam generation from the back end of the processes
Additional steam in the carbon dioxide removal section caused by a reduction in the heat available from the process gas
Additional power for the synthesis compressor due to changes in flow and composition
Additional power in the ammonia refrigeration compressor
Reduced load on the process air compressor
Additional power for low pressure hydrogen separated through membranes
Additional power for nitrogen compression
Additional power for the air compressors of the ASU
Small changes in other drives and small equipment
Production rise from 1750 to 1854 tonnes per day | +6.0% rise in capacity |
Process Change | Energy Change (Gcal/tonne) |
Gain in feed and fuel including steam superheater | +0.36 |
Loss in steam generation (front end) | 0.00 |
Loss in steam generation (back end) | -0.02 |
Loss in additional steam for carbon dioxide removal | -0.27 |
Gain in energy in synthesis gas compressor | +0.01 |
Extra energy in refrigeration compressor | 0.00 |
Gain in energy in process air compressor | +0.16 |
Extra power in hydrogen compressor | -0.22 |
Extra power for nitrogen from ASU | -0.12 |
Steam savings in primary reformer | +0.08 |
Other rotary drives and equipment | +0.04 |
Total Gain | +0.02 |
It is evident from these results that the major losses occur in the carbon dioxide removal section of the plant. These losses are the result of consuming additional steam and compression energy for hydrogen separation. With additional minimization of these losses, additional savings can result. For a production gain of 6% over the base case, the energy saving is 0.02 Gcal/tonne (0.08 MBtu/tonne).
This development could yield savings by increasing methane conversion in reformers and increasing the carbon monoxide conversion in shift reactors. The energy savings can be as high as 0.50 Gcal/tonne (1.98 MBtu/tonne) depending on the adopted process configuration. Hydrogen separation technology can also result in increased ammonia plant capacity as illustrated in the above case study.The reduced air requirement (about 80% of conventional plants) in the secondary reformer is required with a 60% hydrogen removal rate in the reformer. This will also require an additional source of nitrogen. Therefore, the technologies in which nitrogen is being added separately, either from an Air Separation Unit (ASU) or from any other sources, will become more important in this case.
Isobaric Manufacturing
The primary hurdle in the isobaric method of manufacturing ammonia is the poor conversion of methane at elevated pressure. The bottleneck is the maximum permissible temperature range due to metallurgical constraints in the reformer tubes. Synthesis pressures are no longer an issue with the development of the Kellogg Advanced Ammonia Process (KAAP), which utilizes a ruthenium-based catalyst operating at 90-100 ata (1470 psia). Thus, if the methane conversion can be increased by hydrogen separation, the process can be operated at higher isobaric pressures.
The synthesis compressor can be reduced to one small compressor at the natural gas feed. The power consumption in this compressor will be 3.0 MW for an isobaric pressure of 100 ata in the front end because of reduced gas flow and reduced differential pressure. The gas flow in synthesis compressor remains near 200,000 Nm3/h (117,715 scfm) while the flow will be reduced to near 45,000 Nm3/h (26,485 scfm) in natural gas compressor. The differential pressure in the synthesis compressor is 175 kg/cm2a (from 25 kg/cm2g to 200 kg/cm2g), while the differential pressure is only 60 kg/cm2 a in natural gas compressor (from 40 kg/cm2g to 100 kg/cm2g). The power consumption is around 3.0 MW in the conventional recirculator. This will result in a total power consumption of 6.0 MW in raising the pressure of synthesis gas. Presently, the power consumption in the synthesis gas compressor is around 25.0 MW for a conventional ammonia plant at same load. This ,however, requires the process air compressor to be operated at a discharge pressure of 100 ata (1470 psia) compared with a pressure of 34-35 ata (510 psia) in the conventional plant. The net energy saving in the isobaric process can be near 0.5 Gcal/tonne (1.98 MBtu/tonne). Moreover, it will also save the energy in CO2 compressor of the urea plant because the CO2 from the ammonia plant will be available at a much higher pressure.
Shift Section Developments
The water-gas shift reaction is favorable for producing carbon dioxide which is used as a raw material for urea production. Presently, most plants use a combination of conventional High/Low Temperature Shift (HTS/LTS) or High/Medium/Low Temperature Shift (HTS/MTS/LTS) technology. Another option is a combination of HTS/LTS/Selectoxo technology. While not as common as the other combinations, this arrangment offers advantages that will be discussed later. The most important objectives for this section are a low pressure drop and efficient heat recovery from the process gas.
Selectoxo Unit
The Selectoxo unit offers several advantages for grass root designs as well as for revamps. Selectoxo (or selective catalytic oxidation) was developed by Engelhard for oxidizing carbon monoxide while not oxidizing hydrogen. The Selectoxo process provides good energy efficiency because it minimizes carbon moxide "slip" (only about 0.03%), improved process flexibility, and higher productivity in revamps when compared to other oxidation options. The Selectoxo unit is capable of increasing a plant's capacity by 1.5-2.0%.
The Selectoxo unit can also help in a grass root plant by maintaining carbon dioxide/ammonia production ratios which is favorable for full conversion of ammonia to urea. The economics of this option are to be considered against the extra cost of carbon dioxide production by other means (either from the flue gas of the primary reformer or through back burning of extra synthesis gas).
0 Comments