Chemical and Process Engineering Resources
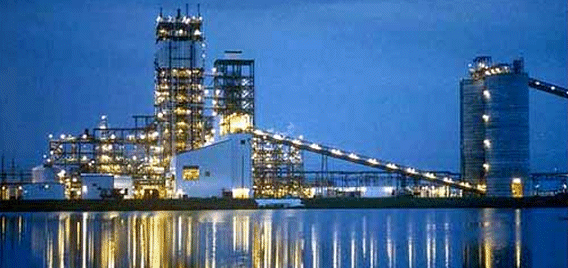
Ammonia Synthesis
Several developments in ammonia synthesis have been made in the past, these developments revolve around the basic principles of reactioin, heat recovery, cooling, production ammonia separation, and recycling of synthesis gas.
Synthesis Catalysts
After almost 90 years of a monopoly in the ammonia synthesis market, iron catalyst has not been replaced by a precious metal (ruthenium) based catalyst used in the KAAP developed by Kellogg. The KAAP catalyst is reported to be 40% more active than iron catalysts.
Research work on low temperature and low pressure catalysts to produce ammonia at 20-40 kg/cm2g and 100 °C is being performed at Project and Development India Ltd. (PDIL) according to their in-house magazine. The catalyst being studied is based on cobalt and ruthenium metals and has exhibited few encouraging results.
Ammonia Separation
The removal of product ammonia is accomplished via mechanical refrigeration or absorption/distillation. The choice is made by examining the fixed and operating costs. Typically, refrigeration is more economical at synthesis pressures of 100 ata or greater. At lower pressures, absorption/distillation is usually favored. A comparison of these two methods is presented in Table 3.
Condensation | Absorption |
High energy costs at lower loop pressures (below 100 ata) | Almost constant energy costs independent of pressure, and less than condensation separation below 100 ata |
Higher fixed costs below 100 ata | Almost constant fixed costs independent of pressure, and less than condensation separation below 100 ata |
Economical at higher operating pressures (above 100 ata) | Economical at lower synthesis pressures in comparison to condensing process |
Energy consumption in refrigeration cycles | Inefficient energy consumption in the distillation process |
Simple process with condensers and separators | More complex process with absorber, distillation column, pumps, reboilers, condensers, and reflux accumulators. Associated instrumentation is also complex |
No chance of catalyst poisoning | Chance of catalyst poisoning due to oxygen in the absorbents |
Minimizing the amount of ammonia in the recycle gas of an ammonia process presents an interesting scenario. Usually the ammonia concentration of the recycle is 3-4%, but reducing this amount to 1.5% can increase plant capacity by about 2.5%. However, the additional separation can often represent a significant addition to the capital cost of the plant and may not be economical for retrofitting (depending on operating pressure). However, reduced ammonia concentration in the recycle can be reviewed for a grass root project where capacity gains can be realized with an additional investment.
Decreasing the ammonia concentration in the recycle stream of existing plants is usually hampered by the high energy cost required for water absorption. Norsk Hydro (Norway) developed a method of reducing the recycle ammonia concentration to near 0.5% via absorption in glycol (DEG). This process can be installed in a high pressure loop (>100 ata) and in combination with a condensation unit. The installed cost is said to be lower than a comparable mechanical refrigeration system.
The separation of product ammonia within the converter using liquid or solid adsorbent can increase the system efficiency significantly. The regenerated adsorbent is fed to the converter and contacts the reaction mixture. Product ammonia is absorbed and removed from the converter. The product ammonia can be recovered either by changing the pressure or temperature depending on process economics. This method would eliminate the need for a synthesis loop and the recycling of synthesis gas. This concept is still being investigated in academic research.
Final Word
The developments discussed here such as isobaric manufacturing, the use of gas heat reformers, hydrogen separation, carbon dioxide removal technology, product ammonia separation, and high activity synthesis catalyst can result in a significant reduction in energy consumption when compared with traditional technology.
Global demand, increased competition, and ingenuity have fueled efforts to enhance existing ammonia technology. In an industry where change is often accepted reluctantly, these technological advancements will have to prove themselves worthy before receiving industry-wide attention.
By: Pawan Agarwal, Guest Author p_bihari"at"yahoo.com
0 Comments