Chemical and Process Engineering Resources

Fume Control and Scrubbing on Hydrochloric Acid Pickle Lines
Nov 08 2010 01:20 PM | Chris Haslego
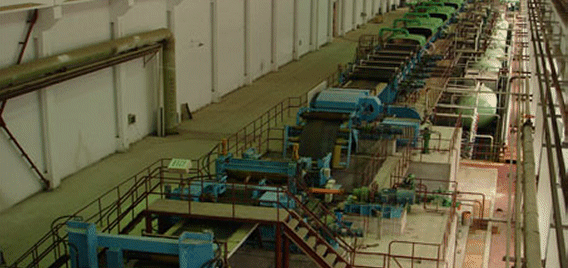
Scrubber Design
![]() |
Figure 2: Conditions in the Pickle Tank |
![]() |
Figure 3: Conditions in the Fume Scrubber |
When HCl dissolves in water, a substantial amount of heat is generated - in a scrubber, this heat is absorbed by evaporation of water into the air. The evaporation of water will also cool the incoming air to near the adiabatic saturation temperature, so that the air leaving a wet scrubber will have almost 100% humidity.
Although there are numerous scrubber designs, three types dominate the market - packed, plate and crossflow.
The packed scrubber is by far the most widely used type. Figure 4 shows the construction of a packed scrubber. The air enters the bottom of the scrubber, and flows upwards through a bed of packing. Scrubbing water is sprayed on top of the packing bed, and flows downwards by gravity - the purpose of the packing is to promote turbulence, and good mixing of the liquid and the gas, so that the HCl will be absorbed.
Figure 4 shows the components of a packed scrubber , which are the shell, the packing support, the packing, the liquid distribution system and the demister. The shell is usually plastic - PVC, polypropylene or FRP - and is most economically constructed as a cylinder. At the bottom is a grid which supports the packing, and which needs to have a large open area to allow passage of the air and gas in opposite directions, without creating excessive pressure drop.
The packing consists of plastic shapes, typically 2" to 4" in size. There are numerous proprietary packing designs - some common ones are: rings, which are short hollow cylinders; saddle shaped packing; donuts of small dia. rod wound in a spiral; and intersecting plates, usually with a spherical external profile. Each packing claims superiority, backed by lab and pilot testing - in fact, they all have about the same efficiency under industrial conditions.
![]() |
Figure 4: Components of a Packed Fume Scrubber |
![]() |
Figure 5: Components of a Plate Fume Scrubber |
![]() |
Figure 6: Components of a Cross-Flow Fume Scrubber |
Good liquid distribution on the top of the packing is essential - if more liquid is added in one area of the packing, it runs down that area, while the gas, taking the path of least resistance travels up areas where there is less liquid, and contacting is poor.
Finally, the droplets entrained in the air stream must be removed, in order to stop them being discharged from the stack as acid rain. This is done by passage through a device which changes flow direction, and provides a surface for the removed droplets to grow, in order to prevent re-entrainment. The two main types of entrainment eliminator are: chevron, consisting of parallel S-shaped blades; and mesh, which is a bed of knitted polypropylene fibers. They are both equally efficient, but the chevron is preferred, because it lasts longer, has large openings, a lower pressure drop, and less tendency to block with dust, crystals or deteriorated fibers.
The advantages of packed scrubbers are simplicity and cheapness (mainly due to traditional use of cheap materials and flimsy construction methods), plus the ability to accommodate variations in air flow. Disadvantages are the tendency of the packing to plug with dirt and the need for a large water flow over the packing (about 100 gal water/10,000 cu.ft. gas). Usually, to avoid high water consumption, and generation of large amounts of very weak acid effluent, this water flow is obtained by pumping water from the bottom of the scrubber back to the top of the packing. This requires a pump to be maintained, and also puts acidic water, instead of clean water, in contact with the clean air.
The components of a plate scrubber are shown in Figure 5. The shell and demister are the same as for a packed scrubber, but the gas/liquid contact is brought about by a number of perforated plates. The plates are plastic plates, perforated with numerous small holes, 1/8" to 3/8" in diameter. As the air passes through these holes at high velocity, it prevents the water from falling through the holes, and generates a highly turbulent water/air mixture on the plate. The water depth on the plate is controlled by weirs - as more water is added to the top plate of the scrubber, it displaces water over the weir, and this flows by gravity through a downcomer pipe to the plate below, eventually discharging from the base of the scrubber.
Plate scrubbers use relatively low amounts of water (1-2 gal water/10,000 cu.ft. gas) on a once-through basis, and require minimal maintenance. The low volume of relatively concentrated effluent makes for easier recovery. However, these scrubbers are not suitable for systems in which the air flow varies widely.
The features of cross-flow scrubbers are shown in Figure 6. These are packed scrubbers in which the gas flow is horizontal instead of vertical - the water still flows downwards by gravity. In these scrubbers, the shell is frequently rectangular in cross section, and the packing is held between two grids. The water from the sump is pumped back to the top of the packing.
These scrubbers have the same advantages and disadvantages as packed scrubbers, but are less efficient. Their main advantage is a low profile when headroom is limited, and the ability to locate the fan on ground level with minimum ducting.
0 Comments