Chemical and Process Engineering Resources

Fume Control and Scrubbing on Hydrochloric Acid Pickle Lines
Nov 08 2010 01:20 PM | Chris Haslego
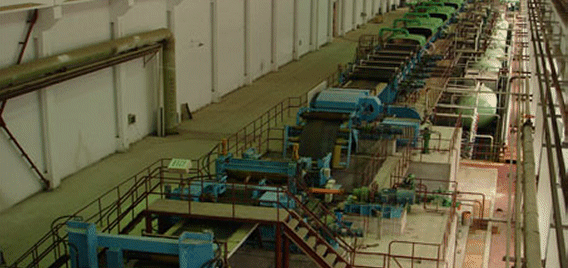
Scrubber Operations
The scrubber is only one component of a fume exhaust system, although there is a tendency to look upon it as being the only thing that matters. However, the function of the scrubber is to remove HCl from the air - collection of the fumes is determined by hood and duct design, and the amount of draft is determined by the fan performance.
Some areas where the scrubber design is important are:
- variable loads
- entrainment
- stack droplet emissions
The HCl concentration in the scrubber inlet gas can vary substantially, particularly in batch pickling operations, in which high HCl loads can occur as the steel is being removed from the tank - this is especially the case in modern systems that have crane-mounted hoods to control these fumes. Essentially, a fume scrubber is a constant-efficiency device, so, if the inlet concentration goes up 10 times, the outlet concentration also goes up 10 times. Usually, these high concentrations only occur for short periods, so that the average emissions remain low. However, such excursions increase the acidity of any droplets in the gas after the scrubber, and make entrainment control even more important.
In order to prevent acid rain from the stack, water droplets must be eliminated from the air stream. In the scrubber, this is done by having an efficient entrainment eliminator. However, all wet scrubbers discharge air saturated with water vapor, so that contact with cold equipment or stack walls can cause condensation after the scrubber - this condensation absorbs the residual HCl content of the gas, and becomes highly acidic. If the stack velocity is too high, or if the stack wall is very cold, or the scrubber exhaust air temperature high, the condensate may be discharged as droplets from the stack. In order to prevent this, an additional entrainment eliminator may be necessary at the top of the stack. This presents problems in compliance testing, because the rules require testing in the stack, at a point which does not represent the actual stack emission!
Another factor that needs consideration is what to do with the scrubber effluent. The scrubber only removes the HCl from the air, generating a dilute acid effluent stream in the process. This effluent requires treatment or re-use. With plate scrubbers, which use little water, it is possible to generate effluent acid up to 2-3% strength, which can often be returned to the pickle tanks to make up for evaporation - this is not generally possible with packed scrubbers, that generate effluent in the 0.1 to 0.5% concentration range. Recycle of the scrubber effluent makes economic sense - a continuous strip pickle line can discharge acid costing as much as $25,000/yr, and then spend as much again in neutralizing chemicals.
Controlling Costs
Costs for scrubbers are always of concern, and will become even more important as more efficient scrubbers are required. The initial cost of the scrubber can be minimized by designing the fume exhaust system to handle the smallest volume of air that will give satisfactory control of fumes. It is tempting to oversize exhaust systems, just to be safe, and to avoid having to pay too much attention to maintenance. However, oversizing results in higher capital costs, more fan hp, more effluent generation, and higher acid losses from the pickle tanks.
The ideal fume control system is a closed cover, with no exhaust, as in ‘fumeless picklers’ used for wire strands, but this is not technically practical for batch pickling or high speed strip lines. Techniques for minimizing exhaust rates include:
- tight, well-maintained covers
- locate exhaust ducts near openings in hoods and tanks
- minimize open area with local seals or closures
- use of double covers
- regular maintenance of fan, hoods and ducting.
- careful, well-balanced duct design
Conclusions
Future emission regulations are going to require larger, more efficient HCl fume scrubbers. The new limits are easily achievable using scrubbers that are 30-50% larger than those presently in use. The cost of upgrading fume scrubbers can be reduced by improving fume control practices to minimize exhaust rates.
References
- Perry, R.H., and Green, D.W., ‘Perry’s Chemical Engineers’ Handbook’, 6th ed., McGraw-Hill, New York, 1984, p 3-64
- Fritz, J.J., and Fuget, C.R., ‘Vapor pressure of aqueous hydrogen chloride solutions, 0 to 50°C’, Ind.Eng Chem., Chem. and Eng. Data, Vol1, #1, p 10, 1956
***This article was written by J. Neil Stone of Kingsville Ontario Canada and this work is entirely his. Any information gathered from this article must be so noted by appearing as a reference in future works.
0 Comments