Chemical and Process Engineering Resources

Fume Control and Scrubbing on Hydrochloric Acid Pickle Lines
Nov 08 2010 01:20 PM | Chris Haslego
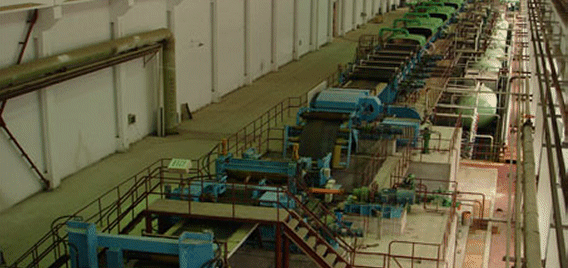
Scrubber Performance and Efficiency
This discussion relates to scrubbers which are operating with effluent acid concentrations of 5% or less, so that the HCl vapor pressure of the liquid can be considered negligible. Tower picklers, where recovered acid up to 15% can be generated, required more complex calculations.
The efficiency of removal of HCl in a packed scrubber depends on the air and liquid flow mass velocities, and the size of packing. Generally, the volume of packing needed for a given efficiency is approximately constant, so the same results can be obtained by a short, large diameter, scrubber, or a taller, small diameter scrubber. Large diameter requires a lot more water volume to irrigate the packing - small diameter gives high pressure drop, and the risk of flooding (when the water is held up in the packing due to the high gas velocity). A superficial air velocity of 5-8 fps is usually found to be the best compromise.
In packed scrubbers, the height of the packed bed is given by the equation
Z = Hog x Nog
where Hog is the height of a transfer unit (which is an experimentally determined property of the packing used), based on gas concentrations, and Nog is the number of transfer units, based on gas concentrations. The number of transfer units required, at low HCl concentrations, is:
Nog = ln [1/(1 - Eo)]
where Eo is the desired overall scrubbing efficiency (as a fraction).
The number of transfer units required for various overall efficiencies is given in Table 1.
Overall Efficiency, % | NOG |
90 | 2.3 |
95 | 3.0 |
98 | 3.9 |
99 | 4.6 |
99.5 | 5.3 |
This shows that, in order to increase the efficiency of a given scrubber from 90 to 99%, the depth of the packing has to be doubled (from 2.3 to 4.6 transfer units), and to get to 99.5%, has to increase 2.3 times (5.3/2.3 = 2.3). This increases the pressure drop through the scrubber proportionally, but does not increase the overall height in the same proportion - usually, the packing accounts for only about 1/2 to 1/3 of the overall scrubber height.
For plate scrubbers, the efficiency of a single plate varies in the range 60-80%, depending on air and water flow velocities, and plate spacing. Usually, it is desirable to minimize the diameter of plate scrubbers, without causing flooding or excessive entrainment, and they are typically designed with air velocities in the range 6-9 fps. The number of plates required for a given overall efficiency is:
n = ln(1 - Eo)/ln(1 - e)
where Eo is the overall efficiency, and e is the efficiency of a single plate, both expressed as fractions.
Table 2 gives the overall efficiency for various numbers of plates at three different plate efficiencies.
Number of Plates | Overall Efficiency for a Plate Efficiency of: | ||
1 | 65% | 70% | 75% |
2 | 88% | 91% | 94% |
3 | 96% | 97% | 98% |
4 | 98.5% | 99% | 99.6% |
5 | 99.5% | 99.75% | 99.9% |
Thus, present day plate scrubbers usually have 2 or 3 plates - to meet future efficiency requirements, 4 or 5 plates will be needed. For each additional plate, the height of the scrubber increases by 24-30", and the pressure drop by 1" to 1.5" of water.
0 Comments