|
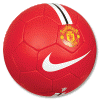
Centrifugal Pump
#1
Posted 13 April 2011 - 01:18 AM
One question relating to the centrifugal pump discharge pressure needs your help!
When do we need to set PSLL for discharge of a pump? What's the purpose? Some pump manuals stated that a minimum discharge pressure of 50 psig is required to insure proper capacity control. Our oil transfer pumps to FSO include: PSHH, PSLL(@50psig) >> Minimum FLOW >> Control Valve >> PSLL (it is to protect pipeline rupture @ 50 psig) >> Flowline to FSO. All pumps on our platform is set @ PSLL 50psig discharge.
Please help me to clarify this issue.
Regards,
vnpetroleum
#2
Posted 13 April 2011 - 02:05 AM
The trip / alarm settings for pressure / flow in centrifugal pumps cannot be generalized. Each case becomes a unique case for the given application and operating philosophy.
The discharge pressure developed by the centrifugal pump is a function of the pump system resistance to flow. For a given pump with a given flow destination and given piping system the system resistance does not change unless the following changes occur:
1. Change in pumped liquid properties
a. Increase in liquid density reduces the volume flow for a given mass flow thereby decreasing the system resistance and indicated as a decrease in
discharge pressure
b. Decrease in liquid density increases the volume flow for a given mass flow thereby increasing the system resistance and indicated as a increase in
discharge pressure
c. Increase in liquid viscosity increases the frictional loss in the piping system thus increasing the resistance to flow and indicated as a increase in the
discharge pressure
d. Decrease in liquid viscosity decreases the frictional loss in the piping system thus decreasing the resistance to flow and indicated as a decrease in
the discharge pressure
2. Damage / Wear and Tear to pump impeller : Damage can cause instantaneous loss in pressure whereas wear and tear over a long period of operation will reflect in efficiency loss and shifting of the rated or BEP (Best Efficiency Point) on the pump curve to give a lower flow and increase in system resistance.
3. As you mentioned in your post capacity control (minimum or maximum flow rate) could also govern the discharge pressure conditions and alarm / trip settings of the pump. Again this is required to be evaluated on a case-to-case basis.
In many cases there may be no requirement of any alarm or trip settings at the pump discharge. For example in a batch transfer from the source to the destination using a small capacity pump I would not go for any alarm / trip settings on the discharge side. In such a scenario the only alarm / trip I foresee is the loss of pressure in the suction side of the pump due to low level in the suction vessel and I would provide a pump trip on either low level in the suction vessel or a PSLL on the suction line.
Hope this explanation helps.
Regards,
Ankur.
#3
Posted 13 April 2011 - 02:15 AM
PSLL @ discharge can inform about pipe rupture. It could be a safety requirement
Breizh
#4
Posted 13 April 2011 - 02:39 AM
Thanks Ankur for your clarification.
Breizh, we had a PSLL @ 50psig to detect pipeline rupture (which is located dowstream of a Control Valve) but pump discharged pressure is still set at PSLL @ 50 psig.
Honestly, PSLLs are required for all critical pumps such as LP Flare, Oil Transfer Pump. What is the design basis for PSLL setting?
Thanks,
vnpetroleum
#5
Posted 13 April 2011 - 04:08 AM
What is the design basis for PSLL setting?
Hi vnpetroleum,
IMO,it would be set to prevent pump's motor damage due to operating beyond prespecified point as "end of curve".
Fallah
#6
Posted 13 April 2011 - 10:04 PM
I attached a pump curve for your reference.
Thanks all for your reply. It is very useful for me.
vnpetroleum
Attached Files
Edited by vnpetroleum, 13 April 2011 - 10:05 PM.
#7
Posted 14 April 2011 - 01:15 AM
For the LL pressure shutdown on the pumps the choice of set pressure is not exact and is to a large degree set based on operational considerations. We don't want it set too high because if so it will always be tripping out the pump due to normal changes in system pressure for changing operating conditions. 50 psig was originally set because it was sufficient below the margin of pipeline operation for flowing conditions. It is experienced number, isn't it?
Yes,it should be well below the pipeline operation point,and on the other hand in the accepted range of motor operation (power value),as well.
I attached a pump curve for your reference.
Thanks all for your reply. It is very useful for me.
vnpetroleum
Similar Topics
Turbine Driven PumpStarted by Guest_Rahimzadeh_* , Yesterday, 09:14 AM |
|
![]() |
||
Vacuum Pump Power EquationStarted by Guest_hysyshunter_* , 22 Apr 2024 |
|
![]() |
||
Heavy Crude PumpStarted by Guest_Rahimzadeh_* , 13 Apr 2024 |
|
![]() |
||
Pump Sizing ConsiderationsStarted by Guest_panagiotis_* , 07 Apr 2024 |
|
![]() |
||
![]() Fan Laws For Centrifugal Compressors And Varying Suction ConditionsStarted by Guest_SickPuppy0_* , 25 Jan 2023 |
|
![]() |