|
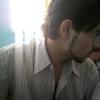
Pseudo Plastic Fluid Thermal Degradation
#1
Posted 13 March 2013 - 05:00 AM
#2
Posted 13 March 2013 - 05:46 AM
If your goal is to keep the polymers at a constant temperature, then shouldn't the fluid (HTF) in the pipe jacket be controlled to near that temperature? Any heat transfer from the environment would be absorbed by your heat transfer fluid rather than the polymer. Since this heat transfer would result in a decrease in the temperature of the HTF, you would have to pipe the hot HTF in parallel to relatively short sections of the pipe jacket. For example, if you are maintaining your polymer at 200C, the HTF might be supplied at 205C and withdrawn at a point where its temperature has decreased to 200C. The polymer would experience only slight heating at the pipe wall.
#3
Posted 13 March 2013 - 06:04 AM
Dear Steve Sir,
My problem is a bit different.
1. I am using electric heaters to maintain 220+ temp.( So HTF point does not applies here).
2. The heating is O.K w.r.t product movement but it is leading to some thermal degradation of polymer at walls which afterwards contaminates the material. So how to avoid this thermal degradation
Please guide.
#4
Posted 13 March 2013 - 07:03 AM
Still not clear. Are you overheating at the wall at all times, or just when the pumping is stopped? Can you decrease the energy supplied to the electric heaters? Are they thermostatically controlled and/or designed with self-limiting temperature?
Since the polymer is flowing in the laminar region, there is very little internal mixing and the velocity at the wall is extremely low. This means that a portion of the polymer has a very long residence time inside the pipe. There is no way to avoid the boundary layer from reaching a temperature very close to the temperature of your jacket. The amount of heat loss to the environment depends on insulation thickness, temperature in the environment, wind if outdoors, emittance from the insulation covering, and emittance of the surroundings. So it will continuously change, and you might have to control the heat tracing.
#5
Posted 13 March 2013 - 07:06 AM Best Answer
Utkarsh,
Some possible solutions:
1. Provide an inline static mixer(s) which would reduce wall deposits and act to homogenize the aged polymer (due to wall sticking) and the fresh polymer therby reducing non-uniform properties of the polymer. This can only be taken up during a shutdown.
2. Thermally shock the polymer transfer line by increasing the jacket temperature by 20-30°C for a short duration (2-3 hours). This thermal shocking will loosen the degraded wall material and it will enter the main polymer stream. Flush out this degraded material for a few hours as sub-standard polymer. Next, restore the jacket temperature to its normal temperature. After an hour or so of restoring the jacket temperture check the polymer colour to observe for degradation. If the polymer color indicates that the degradation is no longer there, then restore the polymer production as standard polymer production.
Hope this helps.
Regards,
Ankur.
#6
Posted 13 March 2013 - 07:21 AM
Dear Steve/ Ankur Sir,
Thanks for your valuable input. I got your point
Similar Topics
![]() Pipe Fluid Temperature Increase Due To Solar LoadingStarted by Guest_HeemeshJ126_* , 06 Apr 2016 |
|
![]()
|
||
![]() Recommended Fluid VelocityStarted by Guest_crn_* , 16 Apr 2025 |
|
![]() |
||
Thermal Oil Pump Motors Blew OffStarted by Guest_lizelle_* , 02 May 2025 |
|
![]() |
||
![]() Supercritical Fluid Flowrate - He Tube RuptureStarted by Guest_flarewolf_* , 07 Apr 2025 |
|
![]() |
||
![]() Thermal FuseStarted by Guest_Dr_bigfoot_* , 09 Apr 2024 |
|
![]() |