|
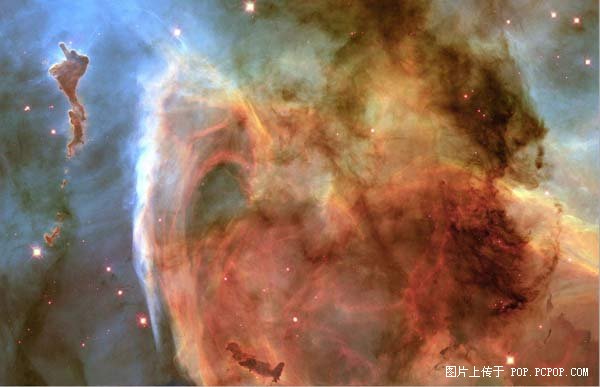
Natural Gas Saturator
#1
Posted 16 August 2006 - 03:51 AM
I need your advice here, any experience professional designer can share your experience design natural gas saturator? the incoming dry natural gas will make "saturated" with countered flow clean water. The "saturated" natural gas will feed to knock out pot before introduce to Desulfurization vessel.
Here the specifications of desulfurization vessel:
Nominal flow rate gas = 49,300 Nm3/hr
Op. Temp = 20C
Max Op Temp = 40C
Op. Pressure = 30 Bar(g)
Max. pressure drop = 1.0 Bar
Natural gas, % Vol
CO2 = 4.07%
CH4 = 91.10
N2 = 0.41
H20 = 0
Ethane, 2.85
Propane, 0.93
Butane, 0.45
Pentane, 0.13
Hexane, 0.04
Heptane, 0.02
H2S - 10ppmv
MW = 18.2
Thanks and regards
#2
Posted 16 August 2006 - 02:17 PM
It's always nice to hear from you because you bring good, interesting problems to the table. This time I'm having difficulty understanding your needs. That's OK, because I think we're on the same wave length. I believe you basically want to remove traces of H2S from a gas stream. And I've done this before from a process design to a mechanical design.
What I don't fully comprehend is why you state "natural gas saturator". What do you mean by "saturator"? If you merely want to saturate (humidify) natural gas with water moisture, then that is an easy chore. I don't think you need help there. I believe you want assistance in designing a Hot Zinc Oxide Treater vessel for removing traces of H2S. And that, I believe, is not easy when you haven't done it before. I have, (a long time ago) and the Excel Workbook attached should help you out. I found my old hand-written notes and calculations between the pages of my old Gas Purification text book by Kohl & Riesenfeld and thought it might be of interest to you and others.
I hope this helps you out.
Regards
Art Montemayor
Attached Files
#3
Posted 16 August 2006 - 09:24 PM
For the natural gas water saturator, i'm using HYSIS to model it. I try several water flow rate until i obtained saturation state which mean water is "produce" from bottom of knock out pot.
The clean water/utility water spec:
O.P. Barg = 32
O.Temp, C = 27
Flow rate = unknown
Once the dry gas is saturated with water, feed to knock out pot then residual water will discharge from the drum. The gas now is humidity with water and feed to desulfurization vessel.
I'm using shell standard for design knock out pot. Anyway how to design the saturator vessel? is this just a normal column?
Regards
DTan76
#4
Posted 16 August 2006 - 11:11 PM
For those new to hysis, here an example I used hysis for modelling dry natural gas saturated with water.
please give me your email and i will send to you.
Regards
#5
Posted 16 August 2006 - 11:22 PM
Some correction here, address to mys 1st post message. Correction here:
The inlet pressure of clean water from booster pump is 30 Bar(g) and temp at 236C. The amount of water calculated by Hysis - 130 kg/hr in order to saturated the gas.
The natural gas max flow rate = 63,000 NM3/hr which is equivalent to 53.4 MMSCFD. If you guy have problem getting gas standard m3/hr. just using P1V1/T = P2V2/T2. Normal condition is 32F amd standard is 60F.
Regards
#6
Posted 18 August 2006 - 03:03 PM
Thanks for HYSYS problem.
My email ID is
bhagat.arvind@yahoo.co.in
regards.
bhagat.
#7
Posted 20 August 2006 - 08:17 PM
Which correlations did you use to calculate it on hysis?
However, what I do not understand is the purpose of 'saturating' natural gas with water. Why do you need this before desulphurization?
Whatever gas processing I have come across, I never found 'desulphurization' of it. Because. Desulphurization is required to remove relatively high content of sulfur from gas oils (more than 10000 ppmw of to less than 50 ppmw).
From the composition you mentioned, it is clear that H2S is very very low (10 ppmv). To remove this small quantity, you need to have a treater as explained by ART which works on adsorption principles. This is the most common practice in 'gas processing' to remove sulfur. The sweet gas, before further processing, will then be send to dehydration unit to remove all of H2O to the lowest possible value.
So, I really do not understand the purpose of 'saturation' of natural gas with water.
Would you please elaborate more?
Regards,
#8
Posted 21 August 2006 - 05:14 AM
I used Peng-Robinson fluid package.
Address to your question why I using the Natural gas saturator treating is because this is not a well or crude oil production plant. Many peoples will misunderstood that I adopt this treatment in similar gas/crude oil production. In fact, this is natural gas further treatment process in a Metal Oxidation/metallurgy plant (End user)
The natural gas from the pipeline is dry basic. The catalysts using in the plant has particular needs, by means that it must react with humidity gas because H2O content in order to produce H2 and Metal sufide, further treatment/removal of sulfide component to less than 1 ppm also need for 2 stage catalysit reaction, whereby t he 2-stage catalysist could poison by H2S in natural gas.
Regards
#9
Posted 21 August 2006 - 07:50 AM
As I described in my workbook, Dtan is removing the last vestiges of H2S from his natural gas in order to be able to put it through a process reactor where the catalyst employed is very susceptible to H2S "poisoning". This is common practice when you have to Steam-Reform natural gas to form Hydrogen or Syn Gas - from which you produce Methanol or Ammonia. Dtan has a problem in sticking to the simple basics of communicating information. I asked him than in my reply, but he never responded. I also guessed and asked if he was merely "humidifying" the natural gas (which is exactly what he is now saying).
Please note that I'm not describing an Adsorption "treater" in my workbook. I'm describing a real, common chemical reaction. The ZnO is converted to ZnS and is, therefore, consumed. It must be replenished. That's quite common when you are removing a substance in the very low concentration levels we are dealing with.
Dtan:
If you desire, I can tell you how to specify and fabricate a natural gas "saturator" vessel as well. All you have to do is ask or tell me if that is what you need. HySys is a great simulator and assistance in designing heat and mass transfer applications. However, the application you have is so simple that I can design it with an old fashioned slide rule and some experience. With HySys you now should know the recommended number of theoretical mass transfer stages and the equivalvent height of the packed bed to be used. You should also know the recommended diameter of the bed. Is that right? If so, tell us and also tell us the type of packing recommended, the water flow rate at the top, the amount of water transfered, the superficial velocity, the pressure drop, and the temperatures.
I can send you a specification sheet of the vessel - added to the workbook I've already enclosed. Is that what you want?
By the way, why don't you just tell us what the process is that you are working on? Are you using Hot Zinc Oxide beds as I have guessed? If not, what are you using?
I'll await your reply.
Attached Files
#10
Posted 21 August 2006 - 10:30 PM
Thanks for valuable advise. Indeed I'm handling process design right now for Knock out pot, water-gas saturator column and Desufurization vessels. I do not have any info on Desufurization vessel at this moment, as our sister company - Johnson Mathew Catalyst will handling the catalysit portion. The Client will advise us the De-H2S vessel design philosophy and right now I do not have.
You can refer to attached Mass & Energy Balance results from Hysis 3.0. For Knock Out Pot, process sizing is listed as follow:
Design Gas flowrate = 52,000 Nm3/hr or 44 MMSCFD
nominal Op Pressure/Temp = 20 Bar(g) / 20 degC
Knock Out Pot
L/D = 3.0
Max Vap Velocity = 0.2653 m/sec
Liquid Resident Time = 600 sec/10 min
Sizing Result:
D = 2.743m
Total Length = 9.701 m
Sump to Inlet Nozzle = 0.3048m
Inlet Nozzle to Demister = 8.298m
You can refer to mass/energy result, the amount of water (minimum) injection is 50 kg/hr x 1.1
Also, I still don't understand how to design Saturator column? In Hysis, i modelled it as "mixing tank". I scrath my head find every literature but couldn't found. Any rule of thumd to size? My boss (he is mech eng. background) told me just use half of Knock out pot size... but I not statisfly with his opinion.
I'm looking at GPSA Eng. Databook/Chemical Process Equipment Sizing but not answer also.
Would appreciate if you could advise me
Thanks and regards
P/s: If you guy can't download the attachments(s), due to global space left 5K only, just give me your email address and i'll send it.
#11
Posted 22 August 2006 - 03:00 PM
It's very hard to follow what you are describing and/or doing. Now, I understand you to say that you need help on a Knock Out Pot. This, according to your process description, is a basic Vapor-Liquid separator. If you have done a decent HySys simulation, you should have no problem designing the appropriate separator. I've already furnished you a specification for the "Saturator".
Attached find more than you have probably seen on the subject of vapor-liquid separators. All you now need as data for the design is the liquid and vapor densities. Use a vertical configuration because your vapor/liquid ratio is going to be very high.
Attached Files
#12
Posted 24 August 2006 - 08:34 PM
Thanks for your prompt reply. I got this spreadsheet and really very helpful. Indeed, Hysis estimated result was very significantly deviated from the spreadsheet sizing. For instant
Q = 46MMSCFD
SGliquid = 1.0
SG.Gas=0.6280
P=20Bar(g)=304psig
T=20degC=68F
Z=0.9447
Result:
Internal dia,D = 42 inch = 1.043m
Let say L/D = 3 then vessel lenght L = 3.0 to 3.5 approximate
Hysis calculated
Diameter = 1.986m
Length = 6.987m
Some queries here:
a) How many demisters, let say 25mm thick to be install in the knock out pot? what is the recommended no?

thanks a lot
Regards
My queries here:
#13
Posted 31 October 2008 - 12:01 PM
Can you please send me the setup you have for doing water saturation with natural gas? Thanks a lot
My email is le.timmy@gmail.com
Regards,
#14
Posted 15 December 2008 - 09:00 PM
I went searching the net for a summary explanation. Take a look below but in essence the unit is a packed column that uses process condensate for its water source. The water contacts the feed gas and saturates it in the process.
Here is a patent application that offers a more in depth process description / background:
Feed gas saturator patent
Look at section 2, copied here for convenience:
The commercial application of steam reforming for the production of hydrogen, ammonia, methanol, and other products involves the catalytic reaction of a hydrocarbon feedstock with steam to form a mixture of hydrogen, carbon monoxide, carbon dioxide, water vapor, and residual hydrocarbons. Steam for this "reforming" reaction has typically been supplied from boilers utilizing treated boiler feedwater. The mixture of gases produce by the catalytic reaction are treated in various downstream processes which include cooling in which the water vapor condenses and is separated from the gas stream. This condensed water vapor is the "process condensate" which is typically contaminated with carbon dioxide and sometimes other compounds such as methanol and ammonia which are formed in the processes downstream of the catalytic reforming reaction. This condensate has typically been sent to a purifying system or "stripper" to remove the carbon dioxide and other contaminants, after which it is re-used as feed water to the plant boilers.
Recent technology has incorporated systems in which the process condensate is heated and sprayed into a packed tower or other vessel to saturate the hydrocarbon gas feedstock to the plant. This type of system can recover low level heat only to the extent allowed by liquid phase heating of the process condensate, and a temperature difference must exist both between the heat source and the condensate liquid and between the condensate liquid and the hydrocarbon gas feedstock.
In my travels found this post that offers a good blow-by-blow of where energy savings can be found:
Ammonia Counting Energy
This booklet's got some good general background on ammonia process technology as well:
EFMA Ammonia Booklet
#15
Posted 19 February 2012 - 02:14 PM
Regarding desulfurization of natural gas, from your excel, you use zinc oxide as the adsorbent, right? but zinc oxide are expensive, can't be generate n high cost of disposal. Actually i want to find alternative to reduce the cost in term of adsorbent. i want to studies the design and mechanism of the desulfurization vessel/column by using adsorbent other than zinc oxide,(maybe sulfatreat- cheap,envifriendly)....but i dont have enough info. all i found is just the general literature review. can you help me in this problem?
thank you...
#16
Posted 19 February 2012 - 03:36 PM
My experience is in the established and well-document hot Zinc Oxide process that is time-tested and field-proven. I have little or no interest in pursuing any other process because I frankly can't justify it.
By the way, I have to correct your erroneous statement that the Zinc Oxide is an adsorbent. Please look up a prior thread on our Forums where I prove that it is nothing more than a chemical reactant that produces zinc sulfide - a natural, normal occurring compound found in nature.
I hope you have success in your search for a substitute.
Similar Topics
![]() Hello, Design Of Natural Gas Liquefaction Processes.Started by Guest_guoyinyanliner_* , 18 Jun 2025 |
|
![]() |
||
![]() Maximum Natural Gas Flow Through OrificeStarted by Guest_ukrche_* , 10 May 2024 |
|
![]() |
||
Heating Of Natural GasStarted by Guest_kaidlut_* , 01 May 2024 |
|
![]() |
||
Tank Blanketing With Natural Gas/ Vapor Recovery SystemStarted by Guest_MethanolPlant_* , 26 Apr 2024 |
|
![]() |
||
Conversion Of M3 Of Natural Gas To M3 Of LngStarted by Guest_sachico28_* , 30 Sep 2023 |
|
![]() |