|
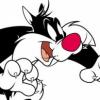
Stage Efficiency Vs Overhead Vapor Fraction
#1
Posted 10 August 2007 - 06:58 AM
1. As soon as I reduced top tray efficiency from 1.0 to 0.95, stripper overhead stream vapor fraction dropped from 1.0 to 0.56.
2. Further reduction of top tray efficiency specification resulted in even lower vapor fraction of stripper overhead stream.
3. The total number of stages in the model and their efficiencies have no influence on overhead stream vapor fraction. You can have efficencies as low as 0.1 and as high as 0.95, regardless of the number of stages - but if top tray efficiency is number smaller than 1.0, there is a liquid in the overhead stream as simulation output.
4. The same thing happens in the crude atmospheric distillation column model (also modeled as absorber-type).
Does anyone know why is this happening and how to overcome it?
P.S. Just to mention, this is not an issue in refluxed absorber and distillation column templates/models.
#2
Posted 10 August 2007 - 08:22 PM
I have noticed the same thing in ASPEN also. Perhaps this is related to the way stage efficiencies are modeled in these softwares.
abhishek
#3
Posted 11 August 2007 - 03:23 PM
this is typical of myrphee stage efficiney with hysys. the tray efficeiny you enter are not overall try efficeny you find in referance books.
hysys is a steady state simulator, it assumes equilibirum on every stage by defult. by putting numbers lower than one, you force hysys to deviate from the equilibrium. the vapour leaving the tray still have some liquid in it and the liquid has some vapour. in reality this should not be the case if the column is running steadly and you dont flood the top tray and have liquid carryover.
for the overhead vapour line getting some liquid is only depenant on the top tray murphee efficiney, changing other trays will not affect it.
for the column bottoms tray, an efficiney less than one will cause the liquid to have vapuor and if you are using a pump it will give errors.
try to avoid this practice and use overall tray efficiy= # theoritical/ actual trays, this sould solve this problem.
cheers,
#4
Posted 12 August 2007 - 05:43 AM
Since it happens only when using absorber template, I'm thinking of it as a software bug. Trying to change top tray efficiency in other templates/models (refluxed absorber, distillation column etc.), one can see that there are no changes in the overhead stream vapor fraction.
In case you are right, this should affect overhead stream quality in all column templates/models - that is the way I think about it.
#5
Posted 12 August 2007 - 02:03 PM
changing the murphee tray efficeny changes everything inculding the tray hydrolics as far as i know. i actually do it on purpous for alot of situations to know if the column top tray is flooding or not. try chaniging the number in hysys or aspen and see if it behaves deferently or not.
in hysys if i want to use murphee tray efficiceny i try to avoid it on top and bottom trays and drawoffs. this is colser to reliaty as you have good volume in these trays to prevent entraiment.
as far as i know the change happens to all models regardless. in a refluxed absorber the reflex comes from the tray below and this might change things, i did not investigate this. try deferent cases and see what comes out.
cheers,
#6
Posted 07 December 2007 - 10:38 AM
The explaination that Mr Smalawi has given is the same one that we find in AspenTech's knowledge base on their website. They have further explained it: the O/H stream gets a vapor fraction less than one because Hysys considers the condenser as the first stage (By default in Hysys, the Tray numbering starts at the top) or one of the stage, so there is not enough space above the top tray in the tower where the liquid droplets can settle down resulting in the vapor fraction of overhead stream ~ to 1.
Now we can do same thing here at the tower top by putting a separator (just to compensate for the vapor space required in Hysys - like what it is normal towers) and considering it as the first stage in Column Envirnment as we do in the case of thermosyphon reboiler installation instead of the kettle type of reboiler (Hysys default).
I hope this can help to tackle the problem. Any query, please let me know.
#7
Posted 07 December 2007 - 01:41 PM
What should be affected by changing overall tray efficiency in column simulations is: vapor and liquid compositions, and NOT vapor and liquid fractions of overhead and bottom streams. This simply does not reflect any case that could be encountered in real tower operation.
#8
Posted 11 December 2007 - 08:58 AM
Can't quite agree with you. In the other templates, you will have a condenser as the first stage (like smalawi said). Hysys will not let you set the efficiency of the condenser; it is always 1, and the "problem" is avoided.
Now, if at a certain pressure and temperature you change the composition of the vapor (because it is no longer in equilibrium with its liquid), and then you flash it again (as Hysys does with all streams), you will see a stream that is composed of vapor and liquid - because Hysys did an equilibrium flash to determine the vapor fraction. If you insist that the stream is all vapor, then you can ignore the calculated vapor fraction, since the reported number is just the equilibrium vapor fraction (now I've said it 3 times, I'll stop). Therefore, if your stripper operates such that the top is not in equilibrium, you may expect downstream condensation, since eventually equilibrium will occur. There is no way for Hysys to tell how long your pipe is, or when equilibrium will be achieved. I guess you just have to live with the fact that Hysys will not calculate/report a non-equilibrium vapor fraction for you.
#9
Posted 23 July 2010 - 08:13 AM
I hope you can guide me, thanks a lot.
Edited by Rick Hunter, 23 July 2010 - 08:51 AM.
#10
Posted 23 July 2010 - 09:29 AM
I think it would be much better if you start a separate thread on this subject. It will help you to receive quality answers on your particular questions.
Just as a quick hint - I'd recommend you to use theoretical plates in design stage, and then convert them into real trays by taking into account system efficiency. It works much easier that way, also because of the issues discussed in this thread.
In general I agree that it is not logical to have lower RVP at lower stage efficiencies (having all other things equal) - for a bottom product. Overhead product RVP may go down because - at lower separation efficiencies and therefore less number of theoretical plates in the column - you wil actually see more heavy components going with the overhead product, causing RVP to decrease. But, as said, it would be good to start a separate thread and use that opportunity to attach some process data as well.
Regards,
#11
Posted 23 July 2010 - 04:44 PM
Best wishes,
#12
Posted 18 December 2010 - 06:08 PM
#13
Posted 18 December 2010 - 11:34 PM
I concur with your observations as I have been encountering the same, more or less. There is no distinction - from process simulator perspective - between the liquid and the vapor temperature on the same tray, which is not the case in reality (for real trays, having efficiency less than 100%). On the other hand, working with actual/real tray efficiency can get you closer to the real performance of the tower, although simulators often experience convergence problems when tray efficiency is less than 1.
What I disagree with, is the explanation that using tray efficiencies less than 1 for the top tray leads to vapor fraction less than 1 in the overhead stream, due to entrainment. Entrainment is purely a hydraulic phenomenon and not dependent on mass transfer efficiency. Or, in simple words, we can have (as we do have) trays operating at quite low efficiencies but without entrainment and this, in my opinion, cannot be the cause of vapor fraction <1. I tend to agree with you that it is a consequence of incorrectly calculated heat balance, and it probably means that (by working the problem backwards) calculating the temperature at which the column stream has a vapor phase 1 (dew point) with given composition, could actually give you the real vapor temperature on the tray. But I haven't tried that so far.
#14
Posted 19 December 2010 - 04:52 AM
I think the real temperature of the vapour is somewhere between the bubble point of some theoretical mixture which is approximately between the liquid compositions on the top two trays, depending on what efficiency is specified. For narrow boiling mixtures it may be close to the dew point, for wideboiling it could be quite different.
Actually when you think about the heat balance on the tray, if all the trays have approximately the same efficiency, the error introduced is probably quite small, as the delta T between vapour and liquid on all the trays is likely to be similar. Also i would imagine the maths of dealing with this feature rigourously is actually very difficult in the column solving algorithms. (and lets remember most of the algorithms in use are using approximate updates to the jacobian matrix and not rigourous anyhow).
So probably using tray efficiencies, as long as draw/feed locations are specified as 1 tp, is probably ok in most cases.
#15
Posted 20 December 2010 - 09:48 AM
But as has been mentioned above, if you can live with the mixed phase product, efficiencies can be used to more accurately model actual conditions in a column.
The heat balance around the tray is still correct - the mixed phase products from these trays is purely a result of the way the efficiency is modelled by this bypass process.
#16
Posted 20 December 2010 - 10:10 AM
The heat balance around the tray is still correct - the mixed phase products from these trays is purely a result of the way the efficiency is modelled by this bypass process.
Heat balance is correct in the way it is modeled - but it doesn't represent something that actually happens in a real distillation column.
Thanks for the reply - it is an interesting explanation of efficiency algorithm within software. I haven't been aware of that before.
#17
Posted 20 December 2010 - 01:30 PM
The heat balance around the tray is still correct - the mixed phase products from these trays is purely a result of the way the efficiency is modelled by this bypass process.
It doesn't sound correct, the vapour has to be hotter than the liquid if the efficiency is less than 100%, then you wouldnt have mixed phases were you shouldnt.
Similar Topics
Ammonia Line Vapor GenerationStarted by Guest_simadri_* , 07 Apr 2025 |
|
![]() |
||
Minimum Vapor Disengagement Area For A Kettle BoilerStarted by Guest_Engib33r_* , 17 Oct 2024 |
|
![]() |
||
![]() Multiple Effect Evaporation 5 Stage CalculationStarted by Guest_pentakota.koti_* , 26 Jun 2018 |
|
![]() |
||
Chiller Efficiency Dependence On Cooling Water TemperatureStarted by Guest_Neha Vensiyani_* , 29 Apr 2024 |
|
![]() |
||
How To Right Size A Vapor Recovery Unit (Vru)?Started by Guest_MethanolPlant_* , 29 Apr 2024 |
|
![]() |