|
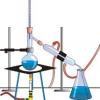
Control Valves On Reciprocating Compressors
#1
Posted 10 March 2011 - 05:11 AM
Can I have a pressure or flow control valve at the discharge of a reciprocating compressor. If not, why.. and if so - what are the limitations and risks?
Thanks in advance. From reading the forum I know that Art Montemayor has a lot of experience with recip compressors.. would appreciate his comment on this as well if he's available!
Cheers!
Temi
#2
Posted 10 March 2011 - 08:59 AM
Ogeds:
What are you trying to accomplish? If you tell us that, the correct advice and comments will go much quicker.
A reciprocating compressor is (I'm getting cramps in my fingers from repeating this) a POSITIVE DISPLACEMENT machine and, as such, is actually a metering device - if used properly. By installing a pressure control valve or flow control on its discharge you are not using the machine within its design constraints and in the best manner.
Just tell us ALL of the story so we can get to the bottom of what you are trying to do - or are worried about.
#3
Posted 10 March 2011 - 09:51 AM
In this instance this is actually a theoretical question, otherwise I would have provided details! I am working on a control assignment which requires me to set up a control scheme to regulate the discharge flowrate and pressure of a recip compressor. The question then goes on to say that "N.B. it is not possible to put a control valve in the suction or delivery line of any positive displacement device"
I found this statement quite difficult to believe..but since I have limited knowledge of recip compressors I decided to see if this is a general sentiment in the application of recip compressors..
Thanks
Ogeds
#4
Posted 10 March 2011 - 11:45 AM
Speaking theoretically, what do you imagine will happen if for a positive displacement machine, the discharge is throttled/constricted or even shut?
Read it along with the statement from Art that "it is actually a metering device".
Edited by pavanayi, 10 March 2011 - 11:50 AM.
#5
Posted 10 March 2011 - 12:00 PM
Ogeds:
When we receive a query, it is important to identify if the query is over an existing situation and/or equipment. If it is, we - as experienced consultants - have to be very careful about what we can or shouldnt - consult or comment because we could issue bad, erroneous - or worse, hazardous or unsafe advice. I cant take a chance on a member misinterpreting or misapplying engineering comments or advice and doing something unsafe. That is why I specifically require that OPs always identify what type of question or query we are given. If you dont provide details, that doesnt mean that you pose a theoretical question! Practically most of our OPs routinely omit details and basic data when asking advice over existing, operating pieces of equipment. I cant take that risk.
Whoever wrote the Nota Bene, it is not possible to put a control valve in the suction or delivery line of any positive displacement device, did not make the absolute correct statement. You can (and sometimes should) place a control valve on the discharge of a reciprocating compressor BUT ONLY FOR THE PURPOSE OF IMPOSING A BACK PRESSURE ON THE COMPRESSOR. YOU NEVER DO IT FOR FLOW CONTROL. There is NO flow to control, once the gas is discharged from the compressor. In some processes (the majority that Ive worked on in the past 51 years), the discharge pressure of the compressor is set by the process itself. The compressor pumps up the gas to suit the process pressure.
As I continue to stress: a reciprocating compressor is a positive displacement device. This, basically describes that it is a METERING DEVICE. Since it puts out a given and pre-set displacement, it is actually metering out a pre-set amount of gas with every revolution. When it is working correctly, you can set and calibrate your downstream meters by it.
If you want to (or have need for) varying the flow rate of the discharge gas from a reciprocating compressor, this can be done in a variety of ways. I have outlined the various ways in many other threads on our forums that relate to reciprocating compressors (which you can find if you use our SEARCH feature). You can:
- Vary the speed of the compressor. This is easy if you have a steam-driven unit or an electrical synchronous motor; I once had a steam turbine-driven Ingersoll-Rand that I could vary the speed on;
- Employ clearance pockets or plug suction valves;
- Employ finger unloaders on the suction valves;
- Employ a recycle capacity control valve on the discharge of the compressor.
If you have a need to sustain a controlled back pressure on the reciprocating compressor, you must carefully analyze and design your controlling instrumentation with care and caution. Dont simply think that the instrumentation is needed for normal operation. Do not forget to take into account the important fact that all process reciprocating compressors require a startup and shutdown procedure that includes the basic need for 100% unloading. In other words, a recip should never be started or stopped while it is handling a full load of gas. It acts just like an automobile another positive displacement device in that you cant rev up a car from dead stop to full load speed immediately. You have to gear up. The same applies to stopping it.
#6
Posted 10 March 2011 - 01:29 PM
To answer your comment Pavanayi, if the discharge valves throttles or shuts, I would expect my compressor to have a spillback line which would return the flow to the suction.. not efficient, but also not "dangerous". Again the distinction between "would" not - and "cannot" or "not possible".
Thanks again for all your comments, much appreciated!
Ogeds
Ogeds:
When we receive a query, it is important to identify if the query is over an existing situation and/or equipment. If it is, we - as experienced consultants - have to be very careful about what we can – or shouldn’t - consult or comment because we could issue bad, erroneous - or worse, hazardous or unsafe advice. I can’t take a chance on a member misinterpreting or misapplying engineering comments or advice and doing something unsafe. That is why I specifically require that OPs always identify what type of question or query we are given. If you don’t provide details, that doesn’t mean that you pose a theoretical question! Practically most of our OPs routinely omit details and basic data when asking advice over existing, operating pieces of equipment. I can’t take that risk.
Whoever wrote the Nota Bene, “it is not possible to put a control valve in the suction or delivery line of any positive displacement device”, did not make the absolute correct statement. You can (and sometimes should) place a control valve on the discharge of a reciprocating compressor – BUT ONLY FOR THE PURPOSE OF IMPOSING A BACK PRESSURE ON THE COMPRESSOR. YOU NEVER DO IT FOR FLOW CONTROL. There is NO flow to control, once the gas is discharged from the compressor. In some processes (the majority that I’ve worked on in the past 51 years), the discharge pressure of the compressor is set by the process itself. The compressor pumps up the gas to suit the process pressure.
As I continue to stress: a reciprocating compressor is a positive displacement device. This, basically describes that it is a METERING DEVICE. Since it puts out a given and pre-set displacement, it is actually metering out a pre-set amount of gas with every revolution. When it is working correctly, you can set and calibrate your downstream meters by it.
If you want to (or have need for) varying the flow rate of the discharge gas from a reciprocating compressor, this can be done in a variety of ways. I have outlined the various ways in many other threads on our forums that relate to reciprocating compressors (which you can find if you use our SEARCH feature). You can:The amount of energy wasted increases as you go from option 1 to option 4.
- Vary the speed of the compressor. This is easy if you have a steam-driven unit or an electrical synchronous motor; I once had a steam turbine-driven Ingersoll-Rand that I could vary the speed on;
- Employ clearance pockets or plug suction valves;
- Employ finger unloaders on the suction valves;
- Employ a recycle capacity control valve on the discharge of the compressor.
If you have a need to sustain a controlled back pressure on the reciprocating compressor, you must carefully analyze and design your controlling instrumentation with care and caution. Don’t simply think that the instrumentation is needed for normal operation. Do not forget to take into account the important fact that all process reciprocating compressors require a startup and shutdown procedure that includes the basic need for 100% unloading. In other words, a recip should never be started or stopped while it is handling a full load of gas. It acts just like an automobile – another positive displacement device – in that you can’t rev up a car from dead stop to full load speed immediately. You have to gear up. The same applies to stopping it.
Similar Topics
Parallel Control Valves Downstream Relief ScenarioStarted by Guest_pklavinsJ_* , 18 Jun 2025 |
|
![]() |
||
![]() Level Control ValveStarted by Guest_Ilyes_* , 03 Jun 2025 |
|
![]() |
||
Pulsation Device In Reciprocating CompressorStarted by Guest_zaidanamir_* , 17 Feb 2025 |
|
![]() |
||
![]() Restricted Orifice (Ro) After The Reciprocating Compressor? Why?Started by Guest_VolereePotere_* , 24 May 2023 |
|
![]() |
||
![]() Breather Valves - Liquid Movement In Breathing ScenarioStarted by Guest_panoska_* , 14 Dec 2024 |
|
![]() |