|
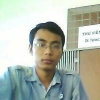
Distillation Column
#1
Posted 27 August 2012 - 08:32 AM
Could someone answer me this question? How do we add trays on distillation column and make sure it's not tilted?
Regards
Trungphu
#2
Posted 28 August 2012 - 10:07 AM
Trungphu:
Are you referring to a conceptual method of adding trays – as in a process design? Or are you addressing the need to physically add more trays to an existing column? I will assume the latter.
Trays are not normally “added” to an existing distillation column. Columns are normally fabricated for a specific duty and separation. If you find that you must add trays to an existing column, you have to confront the need to add height to the column to allow for the additional trays and spacings (and possibly manways). Adding height means essentially that you must do a “surgical” operation on the column: you must cut the column – normally at the top – and add the additional tray sections and shell. Then you have to weld the entire assembly. Of course, it isn’t that simple sometimes. If you add column height, you normally have to re-rate the column for MAWP, seismic and wind stresses, etc.
#3
Posted 05 September 2012 - 10:23 AM
Edited by trungphu, 05 September 2012 - 10:51 AM.
#4
Posted 06 September 2012 - 11:01 AM
#5
Posted 06 September 2012 - 12:33 PM
Trays are “added” conceptually at the design stage of the distillation column. This is done to compensate for the inefficiencies found in the type of tray and in the actual approach to equilibrium that is found in real life. In order to comply with the desired amount of purity sought in the overheads or bottoms product, the designer has to specify a quantity of trays in excess of that calculated theoretically. The additional amount is based on experience, historical data, and the risk involved in achieving the desired purities as related to contractual commitments.
I do not agree that the top diameter of a distillation column is often smaller than the rest of the vessel. I believe that most distillation columns are built as one continuous diameter – although many times this is due to economics and not in conformance to requirements. The internal vapour loadings in large part determine how big of a diameter you need. As a reference, look up the famous Souders-Brown equation or relationship in our Forums and you will find out that this relationship was developed by two famous men in order to design adequate distillation column diameters.
Those columns that you might have seen with the upper section smaller in diameter than the lower section are a product of engineering analysis and economic optimization. When the vapour loading above the feed point (the rectification section) is found to be smaller than the lower part (the stripping section), engineers arrive at a lower diameter for the rectification section. However, the fabrication costs of the finished column are the critical values to decide upon and sometimes – especially when the material of construction is very expensive (stainless steels, etc.) or the number of rectification trays are numerous, the optimum solution is to fabricate the column with two diameters instead of one (the larger, rectification one). Of course, a special transition section has to be fabricated (usually at the feed tray) in order to change diameters.
#6
Posted 10 September 2012 - 05:49 AM
#7
Posted 10 September 2012 - 06:10 AM
Question Not clear.
Please make sketch showing height you concerned
SRShah
#8
Posted 10 September 2012 - 06:24 AM
He might be interesting for you and other students to read these documents .
hope this helps
.
Breizh
#9
Posted 10 September 2012 - 12:33 PM
Your query is incomplete and non-specific. It cannot be addressed in a specific manner and can only lead to generalities – which are essentially useless as engineering tools.
What type of distillation column and vacuum system are you referring to? As SR Shah requests, it is far more accurate and specific for you to draw a detailed sketch complete with dimensions in order to fully understand your application.
I believe I can guess what you are referring to, but that would only be conjecture and we don’t have the time nor the availability to dwell on guesses. I don’t know if you have a total condenser or a partial condenser.
If you refer to Breizh’s submitted article, “Reliable Vacuum Condenser Performance”, on page 29 you will see a detailed sketch of what I believe is close to your application. There, you will find a full explanation on how to determine the necessary heights involved. In the meantime, please respond to SR Shah’s request.
#10
Posted 02 October 2012 - 10:07 PM
I have calculated the number of theoretical stages by using two methods. One is McCable - Thiele Diagram, the other is ProII, a simulation software. And I gained two different results from this two method. For the same reflux ratio, the number of theoretical stages from McCable -Thiele method is 26, while from ProII is 15. I wondered which one is more corrert?
Regards.
Edited by trungphu, 02 October 2012 - 10:07 PM.
Similar Topics
Refinery Lpg Deethanizer Column DesignStarted by Guest_Ilyes_* , 15 Feb 2025 |
|
![]() |
||
Considering Non-Condensable Gases In DistillationStarted by Guest_riwaldron1_* , 10 Apr 2025 |
|
![]() |
||
![]() Methanol Water Distillation ColumnStarted by Guest_Kakashi-01_* , 27 Jan 2025 |
|
![]() |
||
Basic Dynamic Simulation Of A Crude Distillation UnitStarted by Guest_tomr91_* , 12 Jan 2025 |
|
![]() |
||
Aspen V11 Help On Radfrac Distillation Column ErrorStarted by Guest_savinedanglokta_* , 13 Nov 2024 |
|
![]() |