There all,
I need solution to the problem below:
A purge gas is connected to a flare header line into a flare scrubber to ensure that there is no ingress of oxygen into the flare through the tip. The vessel is expected to be maintain at a certain pressure. Also, the purge gas pressure is required to maintain the pressure in the vessel when there's no relief load through the vessel. The pressure maintained in the vessel should be capable to push the liquids out through the flare scrubber liquid control valve into the sump tank.
A study was performed to show that at a certain pressure in the vessel, liquid can flow through the liquid line without the aid of a liquid pump. From the study, it was obtained that at 3 psig, liquid can flow from the flare scrubber into the sump tank. The flare scrubber is located on a upper deck and the sump tank is located on lower deck at the oil platform.
Problem: I need to validate the purge gas flow rate required for the flare header/ flare system. Also, I need to determine the amount of purge gas required to maintain the estimated pressure expected to be maintained in the vessel.
Is there a relationship between pressure and gas flow rate in a vessel?
Your response is highly appreciated.
|
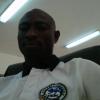
Purge Gas Flow Rate
Started by asade abiodun, Nov 07 2012 10:07 AM
4 replies to this topic
Share this topic:
#1
Posted 07 November 2012 - 10:07 AM
#2
Posted 07 November 2012 - 06:55 PM
I can't digest the vessel part yet, but I believe there's some correlation that tells you how much purge you need to flow to avoid O2 ingress in your flare stack.
#3
Posted 15 November 2012 - 06:17 AM
Dear Anonymous person,
Firstly you do not use purge gas to pressureise up a KO drum so you can force liquids out of the drain. Th e amount you would require on a continuous basis would be prohibitive due to waste of gas,
.
Each flaretip will have a recommended amount of gas required in order to prevent ingress of air into the system
This amount will either be specified by the vendor or can be calculated using various methods HUSA, API ( try googling it) or look at API 520
Also i do not understand if the KO drum is on the upper deck and the sump tank is on the lower deck whats wrong with Newton's dicovery of gravity to drain the KO drum
flarenuf
Firstly you do not use purge gas to pressureise up a KO drum so you can force liquids out of the drain. Th e amount you would require on a continuous basis would be prohibitive due to waste of gas,
.
Each flaretip will have a recommended amount of gas required in order to prevent ingress of air into the system
This amount will either be specified by the vendor or can be calculated using various methods HUSA, API ( try googling it) or look at API 520
Also i do not understand if the KO drum is on the upper deck and the sump tank is on the lower deck whats wrong with Newton's dicovery of gravity to drain the KO drum
flarenuf
#4
Posted 15 November 2012 - 07:55 AM
As per API guidelines purge gas flow rate would need to have a velocity of 0.3 m/sec.
#5
Posted 15 November 2012 - 10:49 AM
In addition to previous posts, following notes can be of interest.
1. For purge gas flow rate to eliminate possibility of air ingress, see http://www.cheresources.com/invision/topic/12530-flare and web references mentioned there. Also http://www.cheresources.com/invision/topic/13221-flares-pilots-and-purge-gas for general info.
2. For any purge gas flow, ΔP from atmosphere to the vessel could be estimated (including ΔPs related to exit, flare tip, riser, any seals, header, exit from vessel); and then find the purge gas flow to cause total ΔP=3psi (that is 3 psig in the vessel).
Resulting loss of purge gas is expected to render this option uneconomical (look at posts No 2 and 3).
Note: A sketch would also help clarify the picture.
1. For purge gas flow rate to eliminate possibility of air ingress, see http://www.cheresources.com/invision/topic/12530-flare and web references mentioned there. Also http://www.cheresources.com/invision/topic/13221-flares-pilots-and-purge-gas for general info.
2. For any purge gas flow, ΔP from atmosphere to the vessel could be estimated (including ΔPs related to exit, flare tip, riser, any seals, header, exit from vessel); and then find the purge gas flow to cause total ΔP=3psi (that is 3 psig in the vessel).
Resulting loss of purge gas is expected to render this option uneconomical (look at posts No 2 and 3).
Note: A sketch would also help clarify the picture.
Edited by kkala, 15 November 2012 - 10:53 AM.
Similar Topics
![]() Flare Header Reverse FlowStarted by Guest_Ahmadhamzahperta_* , 04 Apr 2025 |
|
![]() |
||
![]() Steam Flow And Heating Time In Batch ReactorStarted by Guest_seagal6_* , 16 Jul 2025 |
|
![]() |
||
Heat Exchanger Steam FlowStarted by Guest_aliebrahem17_* , 25 Nov 2024 |
|
![]() |
||
![]() Flow Through Normally No Flow LineStarted by Guest_iippure_* , 08 Apr 2025 |
|
![]() |
||
![]() Dynamic Simulation After Feed Flow ReductionStarted by Guest_Kakashi-01_* , 20 Mar 2025 |
|
![]() |