Dear All!
I have done lots of blast study on building in different projects, but yet, I am not sure about the best approach or methodology.
Frankly I confused today! after a deep review of Exxon Mobil & Total approach.
We have three different method to blast study as API 752 describes:
1- Using conventional tables
2- Consequence Analysis
3- Risk based
I am very happy with consequence analysis, because it is more realistic and provides direct result for Civil department for blast proofing.
I ask you some question to confer about the issue and having your valuable experiences. My questions are simplified here:
1- Which model TNO or BKS is preferred? Why?
2- What is your software? PHAST, FLACS, Shell Sheferd? or... which one is better and why?
3- If your model is TNO, what is strength factor?
4- What is your approach to select congested zone? All unit area? or just below piperack?
it is important to remember that TOTAL has some clues for building study, but no exact approach. First considering whole Fire Zone (Unit) as congested zone full of gas at stochiometry and then assuming strength factor of TNO method is 5.6 (equivalent to an explosion with 350 mbar at the edge of unit)
Exxon Mobil has sophisticated approach as described here:
Design Basis Vapor Cloud Scenario No. 1 (VCE #1)
Following a leak or uncontrolled release from process equipment, a vapor cloud develops resulting in a congested/confined
area of a process unit or operating area becoming enveloped in a flammable gas cloud. The volume of the flammable cloud is
assumed to be 140,000 ft3 (4000 m3) containing LPG type material in stoichiometric proportions. This is equivalent to a 165 ft
(50 m) diameter cloud 6 ft (2 m) high, or an overhead pipe rack, 300 ft (90 m) long, 25 ft (7.5 m) wide, filled with gas to a depth
of 20 ft (6 m). It is judged that this is close to the upper volume limit of the most highly congested/confined part of a typical
process unit or operating area.
Design Basis Vapor Cloud Scenario No. 2 (VCE #2)
The second scenario, VCE #2, involves a large vapor cloud engulfing an entire process unit area. Based upon previous
analyses of past VCE's, documented in EE.30E.91, it is assumed that the flammable portion of the cloud, occupying areas filled
with process equipment obstacles does not exceed a volume of 1,000,000 ft3 (30,000 m3) and contains LPG type material in
stoichiometric proportions. For a typically sized ExxonMobil process unit [70,000 - 100,000 ft2 (6,500 - 9,300 m2) plot area],
this is equivalent to the flammable cloud covering the whole block to a depth of 10 - 15 ft (3 - 5 m).
Design Basis Vapor Cloud Scenario No. 3 or “Maximum Credible Vapor Cloud Explosion" (VCE #3)
The third scenario, referred to as the “Maximum Credible Vapor Cloud Explosion" (VCE #3), is a large flammable cloud
engulfing a process unit area, which includes a central core of highly congested/confined equipment. Using the Multi-Energy
method to model this vapor cloud, it is assumed that two explosions will occur - one involving that part of the cloud occupying
the “highly congested/confined" area and the other involving the “partially congested/confined" area. Those parts of the cloud
which fall outside the “partially congested/confined" area, e.g., outside the plant battery limits, and which do not engulf any
process equipment or obstacles, are assumed to have a negligible contribution to the overall explosion.
HAMID
|
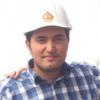
The Best Approach To Blast Study On Buildings In Onshore Facilities
Started by hamidkeng, Jan 20 2014 02:32 PM
blast study on building
No replies to this topic
Share this topic:
#1
Posted 20 January 2014 - 02:32 PM
Similar Topics
Water Hammer Study: Hysys Dynamics Vs PipenetStarted by Guest_powerox29_* , 07 Apr 2025 |
|
![]() |
||
Aspen Hysys Blowdown Philosophy ApproachStarted by Guest_Akshay.Gadekar_* , 29 Aug 2024 |
|
![]() |
||
Quantitative Risk Assessment Of Onshore Crude Oil PipelinesStarted by Guest_Mansi_* , 14 Feb 2024 |
|
![]() |
||
Calculation Of Approach To Equilibrium Of Primary Reformer CatalystStarted by Guest_muthukmaar_* , 05 Jul 2019 |
|
![]() |
||
Flare Study And Pump SealsStarted by Guest_Sue N_* , 21 Aug 2023 |
|
![]() |